All scientific fields and industries require calibrated equipment to accurately measure a multitude of physical product characteristics. This article will provide an overview of why calibration is important in the field of metrology.
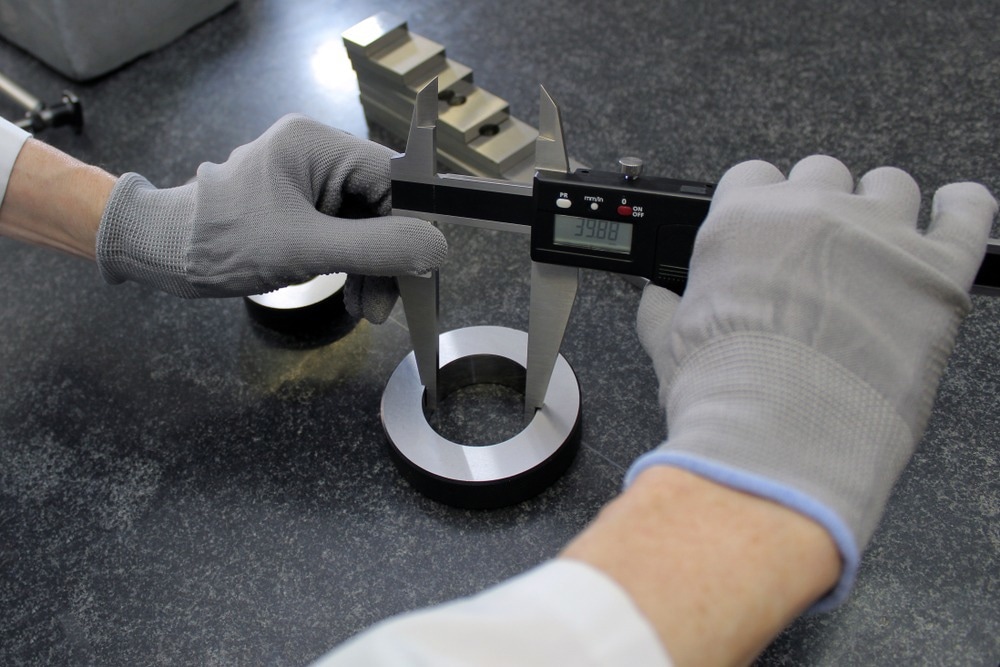
Image Credit: Zabolotskikh Sergey/Shutterstock.com
What is Metrology?
Metrology can be widely defined as the science of measurement, with roots in the 18th and 19th centuries. There was a growing desire by intellectuals, industry, and governments to standardize the standards for measurement and move away from more outdated and confusing methods that differ between locales.
The metric system was first developed in 1795 in France, and over the next century became adopted in many nations. International efforts throughout the 19th and mid-20th centuries eventually led to the International System of Units (SI,) the standard in industry today.
Scientific metrology is a subfield of metrology concerned with the accuracy of scientific measurements. This subfield covers measurements in acoustics, chemistry, ionizing radiation, magnetism, electricity, physical measurements and dimensions, and thermometry.
Due to its need to capture the highest degree of accuracy, scientific metrology is considered to be the “top” level of metrology. Several worldwide institutes set the standards and reference points for measurements in this subfield, which is widely used in nearly all industries.
Another related subfield of metrology is industrial metrology, also known as technical or applied metrology. This field is concerned with providing accurate measurements for the manufacturing industry, which is essential for ensuring optimal product quality. Calibration is key in metrology.
Calibration and Metrology
In order to provide accurate measurements, equipment must be properly calibrated. Calibration is typically conducted in specialized laboratories.
During calibration, internationally accepted standards of known accuracy are used to check the values of instruments to ensure their proper operation. Dimensional inspection is used to compare product dimensions with design specifications.
Calibration can also be performed on-site by trained engineers, providing a field service that can save companies time and money, negating the need to send equipment off to a lab and wait for it to be calibrated.
Examples of equipment that can be calibrated either in the lab or on-site include welders, hand tools, gauges, surface plates, compression and tension machines, hardness testers, furnaces, and optical comparators.
Calibration engineers will test measurement parameters such as pressure, torque, humidity, flow, temperature, and mass for all types of measuring instruments and masters. Performance output is evaluated against a measurement standard.
The Benefits of Calibration for Different Industries
Proper instrument calibration has a number of benefits for different industries. The main benefit is ensuring that measurements are accurate and products, therefore, meet international specification standards.
- The pharmaceutical industry: Proper equipment calibration is essential to ensure the correct dosage in drugs, as improper dosage can cause health issues in patients.
- The automotive industry: Vehicle parts must be produced to specific standards and sizes. Components such as brakes and the motor must be able to operate effectively under stress. Accurate measuring instruments are essential to ensure parts and vehicle safety.
- Gas stations: Knowing the accurate amount of diesel and gas pumped into a vehicle’s engine provides crucial economic and stock information. Meters must be able to accurately measure the amount of product consumed.
- The petrochemical industry: Accurately measuring parameters such as temperature mitigates safety risks in oil wells and processing plants.
- Manufacturing: Measuring product dimensions accurately ensures that they meet rigorous standards.
- The aerospace industry: Civilian and military aircraft components must be able to withstand extreme environmental stresses, making the accuracy of test equipment measurement vital in the industry.
These are just a few of the benefits of properly calibrated instruments for many different industries.
In Summary
Metrology is a scientific field concerned with measurement and requires the use of specialized equipment by trained operators. Measurement accuracy is essential to ensure optimal product quality and safety. The performance output of equipment is evaluated against international standards and requires proper calibration.
Proper instrument calibration provides key benefits for sectors including the pharmaceutical industry, manufacturing, aerospace, and the automotive industry. Calibration can be conducted either in a specialized laboratory or on-site by trained engineers.
Several international bodies and institutes provide guidance and calibration services for industry, underpinning the importance of accurate measurements and improving confidence in results and data. These include the National Metrology Institute in the UK and the National Institute of Standards and Technology in the US.
More from AZoM: Why is 3D Optical Metrology Important in the Automotive Industry?
References and Further Reading
National Metrology Institute [online] npl.co.uk. Available at:
https://www.npl.co.uk/about-us/national-metrology-institute
National Institute of Technology [online] Available at:
https://www.nist.gov/metrology
Laboratory Testing, Inc. (website) Metrology & Calibration Services
https://labtesting.com/metrology-calibration-services/
Disclaimer: The views expressed here are those of the author expressed in their private capacity and do not necessarily represent the views of AZoM.com Limited T/A AZoNetwork the owner and operator of this website. This disclaimer forms part of the Terms and conditions of use of this website.