Stainless high-grade steel is, in general, resistant to corrosion and insensitive to the majority of lyes and acids. Found in many industries, stainless high-grade steel is characterized by its high resistance and variety of processing methods.
The typical composition of stainless high-grade steel consists of a high chromium content of more than 10.5%. It also contains the alloying elements manganese, molybdenum, and niobium for better corrosion resistance and more favorable mechanical properties. Mechanical strength and durability are not solely dependent on these elements, however, but also on the carbon content.
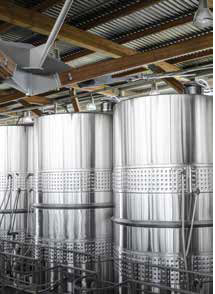
Image Credit: Elementar Americas Inc.
Steel of alloy 316 is a popular example, used for constructing petrochemical plants. This alloy is produced and marketed in two variants: the alloy 316 (also W-No. 1.4401), and alloy 316L (W-No. 1.4404). The carbon content is what separates these two materials, with "L" used as an indicator for "low carbon" (Table 1).
Table 1. Chemical composition of high-grade steel Type 316 and 316L. Source: Elementar Americas Inc.
Permissible Chemical Composition In % By Weight |
|
C |
Mn |
Si |
Cr |
Ni |
P |
Mo |
N |
AISI 316 |
0.07 |
2.0 |
1.0 |
16.5-18.5 |
8-13 |
0.04 |
2-2.5 |
0.11 |
AISI 316L |
0.03 |
2.0 |
1.0 |
16.5-18.5 |
8-13 |
0.04 |
2-2.5 |
0.11 |
Type 316 alloys are commonly used in the oil and gas industry as well as in the chemical industry, with many other areas of application, including:
- Non-corroding components in the automobile industry
- Watches, jewelry, functional components in electronic housings and accessories
- Foodstuffs and chemical plant sector as well as tank construction
- Aerospace, power plant and turbine industry
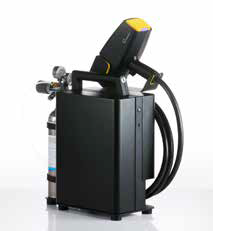
Image Credit: Elementar Americas Inc.
Influence of Carbon on Corrosion Resistance
Introduced as an alternative to AISI 316 alloy, the AISI 316L was created to mitigate the risk of intergranular corrosion (weld decomposition) that, in the early days of using the alloy, would often result in accidents and premature failures in petrochemical plants.
Intergranular corrosion may occur when steel is kept in a temperature range from 450 °C to 850 °C for several minutes, and subsequently exposed to aggressive, corrosive environments. Corrosion will then take place adjacent to the grain boundaries. This type of corrosion is eliminated if the carbon content is below 0.03%.
Analyzing the Carbon Content Using ferro.lyte
A dependable identification of the alloys is important due to the difference in behavior resulting from the change in carbon content. The method for differentiating between alloy 316 from 316L, and 304 from 304L, is to determine whether the material contains more or less than 0.03% carbon.
Table 2. Typical measurement data. Source: Elementar Americas Inc.
C [%] |
0.031 |
0.035 |
0.032 |
0.032 |
0.033 |
0.036 |
0.032 |
MEAN: 0.033%
SD: 0.0018%
RSD: 5.53% |
Using the mobile optical emission spectrometer ferro.lyte® directly on-site enables dependable identification of materials differing only in carbon content, using a few measurements.
ferro.lyte provides calibration over the vast majority of elements relevant in steel and has been optimized for analyzing carbon.
The calibration of ferro.lyte has been carefully performed with approximately 200 certified samples. More than 40 samples were used to calibrate carbon in the high-grade steel methods shown here (Table 3).
Table 3. Typical carbon performance data. Source: Elementar Americas Inc.
Parameter |
Value |
Detection limit* |
60 ppm |
precision at 0.02 % (absolute) |
±0.0015% |
precision at 0.06 % (absolute) |
±0.0015% |
Measuring time |
17 seconds |
*3 Sigma pure sample
Elementar – A Partner for Excellent Elemental Analysis
Elementar is a world leader in high-performance analysis of organic and inorganic elements.
Continuous innovation, creative solutions, and comprehensive support form the foundation of the Elementar brand, ensuring products continue to advance science across chemical, agricultural, environmental, energy, forensics, and materials markets in more than 80 countries.
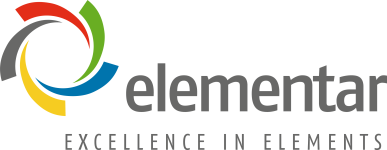
This information has been sourced, reviewed and adapted from materials provided by Elementar Americas Inc.
For more information on this source, please visit Elementar Americas Inc.