Flash chromatography is a well-established, efficient, and rapid isolation technique for the separation and purification of organic substances. This technique caters to the needs of both the organic bench chemist and those dealing with natural product extracts.
Amongst the Flash Chromatography Users community, a widely accepted standardized set of specifications is typically employed to utilize Flash Silica. Nevertheless, many chemists opt for a more conscious compromise, considering a cost-to-performance ratio. This entails the use of silica for Flash Chromatography that exhibits the following characteristics:
- Irregular particle sizes (often referred to as granular) – non-spherical.
- Relatively large particles, falling within the 43-63 um range.
- Wide particle distributions (20 microns).
- Moderately small pore sizes, measuring between 60-70 Angstroms (60-70 Å).
The motivation to deviate from the well-established standard, with its economical purchase price, to a seemingly more costly alternative in the form of spherical silica remains a question for users. The answer to considering this transition lies in the enhanced separation efficiency that using spherical silica provides.
Explanation
Depending on individual applications, efficiency can be measured through chromatographic performance, economical value of time to results and also purification effectiveness.
Illustration
Distinct chromatographic variances become evident when comparing standard flash grade granular/irregularly shaped particles to spherical particles of smaller particle sizes but similar porosity. This section of the article illustrates some of these differences.
These differences offer several valuable benefits, including providing higher loading capacities (allowing more material to be loaded per run, expediting the overall purification process) and resulting in faster flow rates (reducing total run length).
In addition, these differences can provide more uniform sample distribution, higher plate counts, significantly higher resolution, improved peak symmetry and reusability- allowing multiple, successive runs using the same column.
Comparison of Specifications
Table 1 provides a side-by-side comparison of Sorbtech’s spherical silica and a competitor’s granular materials. This comparison highlights the several chromatographic advantages of packing columns with spherical silica, as previously discussed in this article.
Table 1. Source: Sorbent Technologies, Inc.
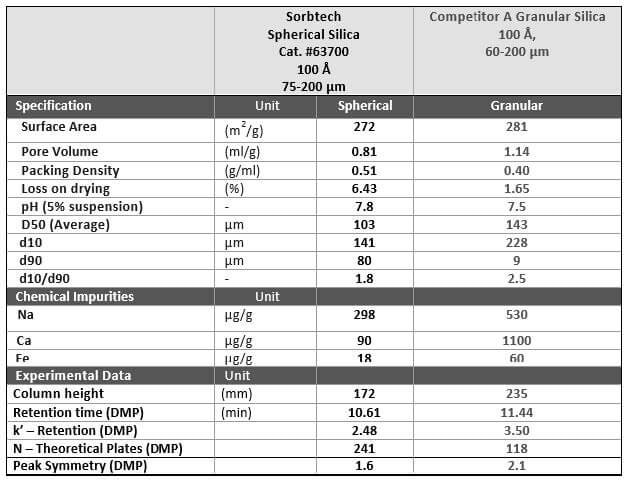
Using spherical-shaped silica improves peak symmetry and resolution thanks to increased theoretical plates (N). Figure 1 illustrates the significant advantage of more baseline resolution of the analyzed sample and a more symmetrical peak shape. These improvements result in purer fractions from a complex mixture that can be recovered during flash chromatography.
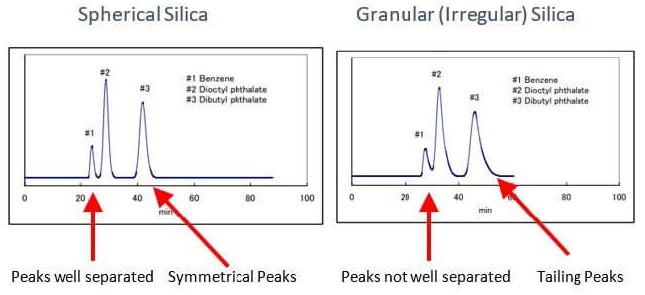
Figure 1. Image Credit: Sorbent Technologies, Inc.
Influence of Particle Shape
Particle shape profoundly influences the characteristics of the column bed, affecting the packing density and uniformity. Spherical silica boasts a higher packing density than irregular silica, leading to several advantages.
Firstly, more material in the column allows for higher material loading without compromising resolution. Secondly, there is reduced interstitial volume (volume between particles), which reduces liquid volume and minimizes molecule dispersion during separation. As the interstitial volume decreases, both separation efficiency and resolution increase.
Packing a column and obtaining a homogeneous bed (no channeling) with spherical silica is significantly easier, resulting in lower pressure drops and a more homogenous flow profile.
This particle shape difference also offers the advantage of chromatographic reproducibility if all other separation conditions are held constant. Spherical materials form more uniform and consistent column bed structures, improving the mechanical stability of the packed bed and prolonging column lifespan compared to granular silica columns.
An Increase of Fines with Granular Silica
Granular materials generate more fines (tiny particles) during silica manufacturing. Agglomeration of these fines, especially when accumulated on the column frits, can lead to higher back pressure, uniform flow resistance, and column outlet frit blockage.
Fines with small diameters may even pass through the frit and contaminate the collected fractions.
Particle shape, however, is only a single (morphology) parameter of influence on the separation of compounds.
Consideration of Other Factors
Optimizing separation involves considering several other important factors, including solvent choice, flow rate, temperature, stationary phase chemistry, loading capacity, and numerous other parameters. These factors, along with particle shape, collectively influence and affect the viability of a separation.
Choosing the Efficient Option
For those accepting a 90-95% purity, irregular silica will suffice. However, if consistently achieving around 99% purity with minimal effort is the goal, spherical silica is preferred.
With spherical silica gel, you can:
- Load more per run, reducing the number of runs required
- Attain a higher resolution
- Capture your products in a smaller volume, minimizing evaporation
- Depending on your compounds, use the same column for multiple runs
Recommendations
Sorbtech strongly recommends against allowing purchase cost, traditional methodology, or legacy methods to dictate the choice of flash silica specifications. Instead, Sorbtech believes that greater separation efficiency, improved mechanical strength/lifetime, higher flow rates, and better loading capacity should be prioritized. The higher purchase cost of spherical silica permits an efficient and economically responsible return on your investment of time and resources.
Acknowledgments
Produced from materials originally authored by Robert Cotta, Raymond Lombardi, and Robert R. Kerr, Ph.D.
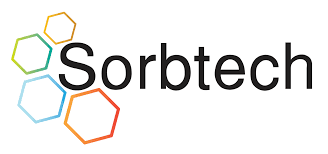
This information has been sourced, reviewed and adapted from materials provided by Sorbent Technologies, Inc.
For more information on this source, please visit Sorbent Technologies, Inc.