Maintaining a contaminant-free environment is crucial in high-throughput semiconductor manufacturing. Vigilant monitoring is necessary for every semiconductor fabrication plant (fab) section, including cleanrooms, plenums, and sub-fab areas.
Image Credit: TOFWERK
A manifold valve system, also called the manifold sampling system, plays a pivotal role in semiconductor manufacturing, particularly in monitoring airborne molecular contamination (AMC).
This system monitors the gases from different sources, ensuring that production processes occur optimally and safeguarding materials from contamination.
AMC monitoring holds paramount importance in semiconductor manufacturing. Even tiny traces of airborne contaminants can significantly impact product quality and performance. Hence, precise control over gas and chemical flow in the manufacturing process is imperative, and the manifold valve system serves this crucial purpose.
Manifold valve systems enhance sampling efficiency, enabling a single analyzer to monitor multiple sources. The speed of measuring each source or port inversely depends on the number of ports.
TOFWERK's multiport valve system, in conjunction with the AMC analyzer, offers rapid sampling within milliseconds. Each port is sampled in seconds, accommodating up to six chemical ionization methods across a broad spectrum of AMC classes.
TOFWERK's manifold system seamlessly attaches to AMC monitors, enabling customization of the number of sampling points by adding modules to the six available ports, as illustrated in Figure 1.
The ultra-swift instrument response permits sampling of each port in as little as 10 seconds, without any memory effects between ports, as depicted in Figure 2.1
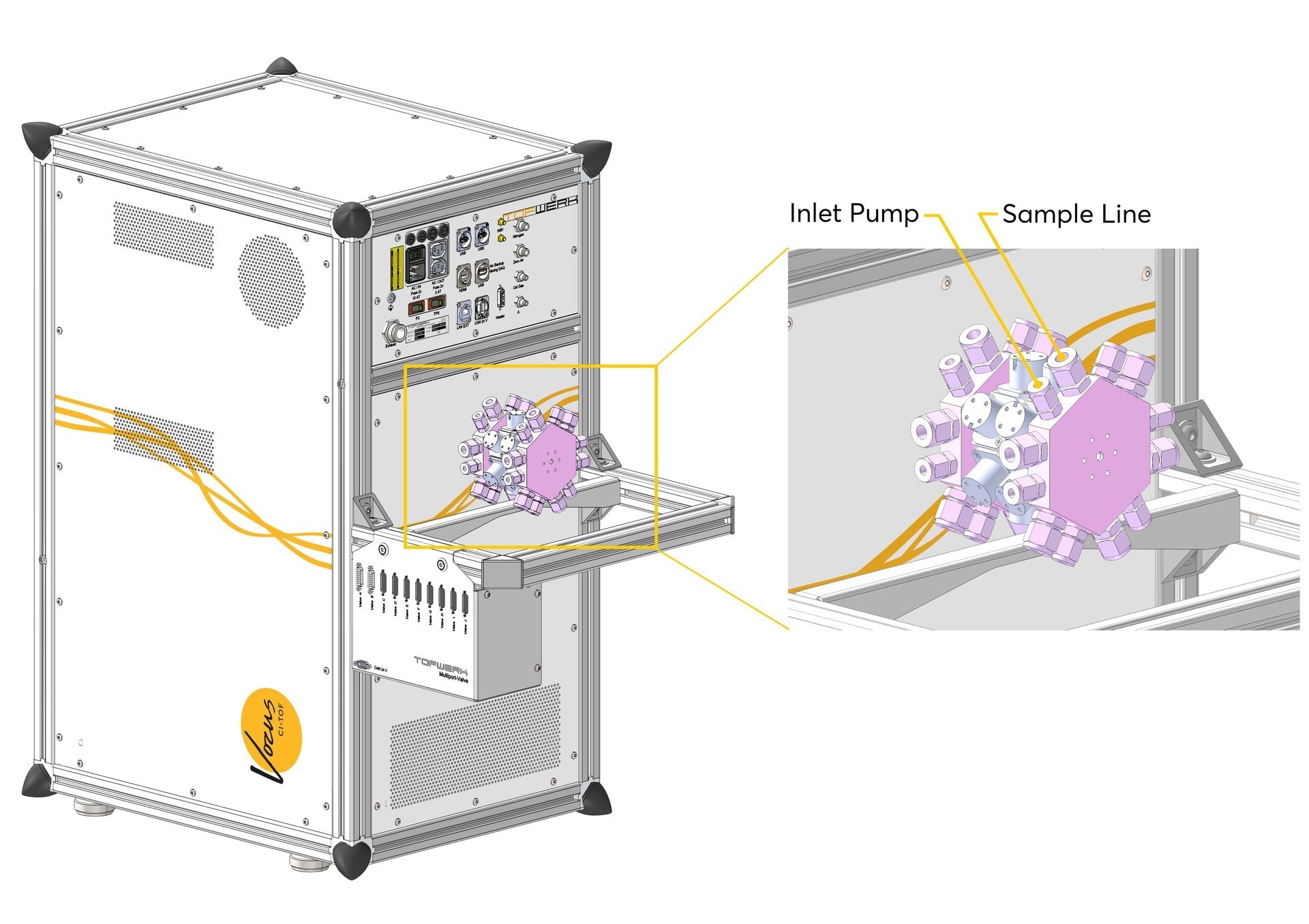
Figure 1. Schematic of TOFWERK’s multiport valve assembled with an AMC monitor. Image Credit: TOFWERK
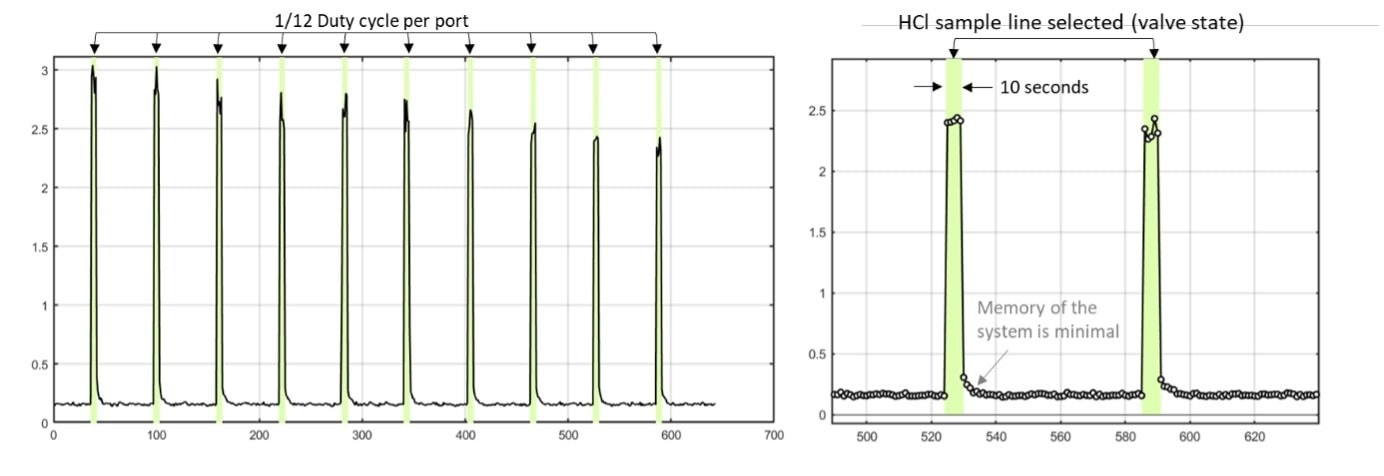
Figure 2. Duty cycle per port using twelve ports (left) and fast time response between ports (right). Image Credit: TOFWERK
TOFWERK's manifold system has undergone testing within fabs, effectively analyzing timed excursion events from diverse locations. During these tests, the system accurately identified the presence of AMCs, including acids, solvents, and bases. Examples of excursion events are showcased in Figures 3 and 4 for PGMEA and Cl2, respectively.
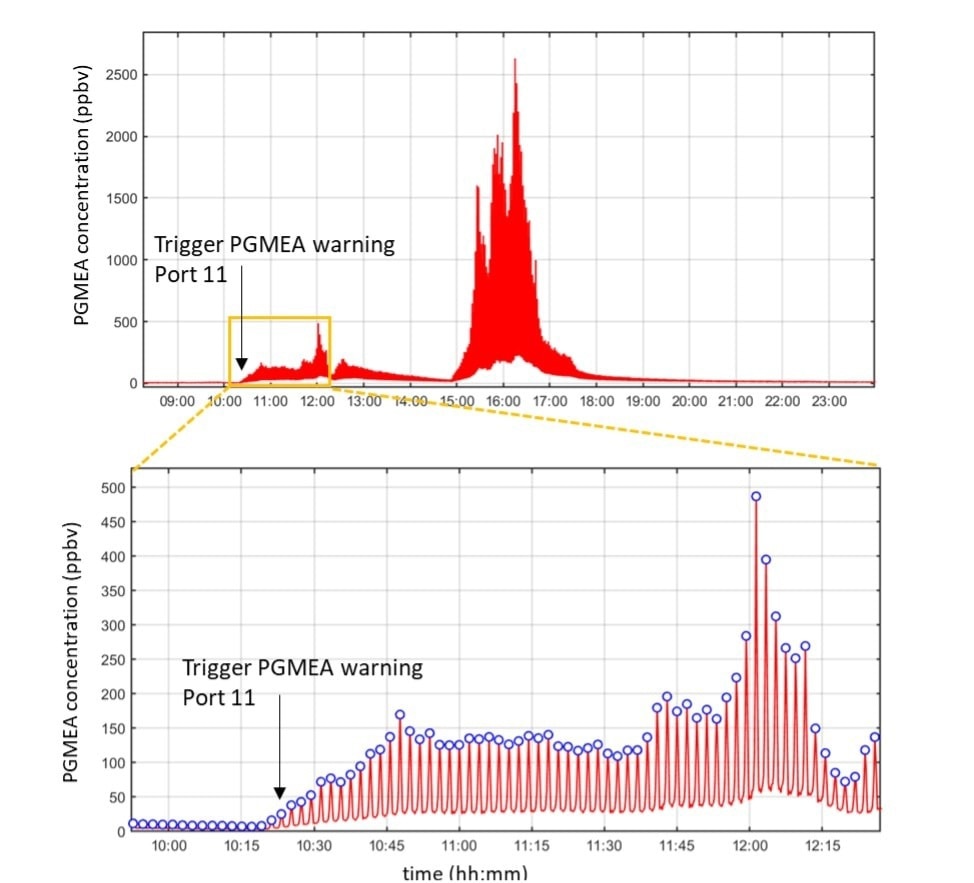
Figure 3. Top: Time series for PGMEA showing excursion events in one location (Port 11). Bottom: zoom-in in one of the excursion events where an alarm was triggered. Image Credit: TOFWERK
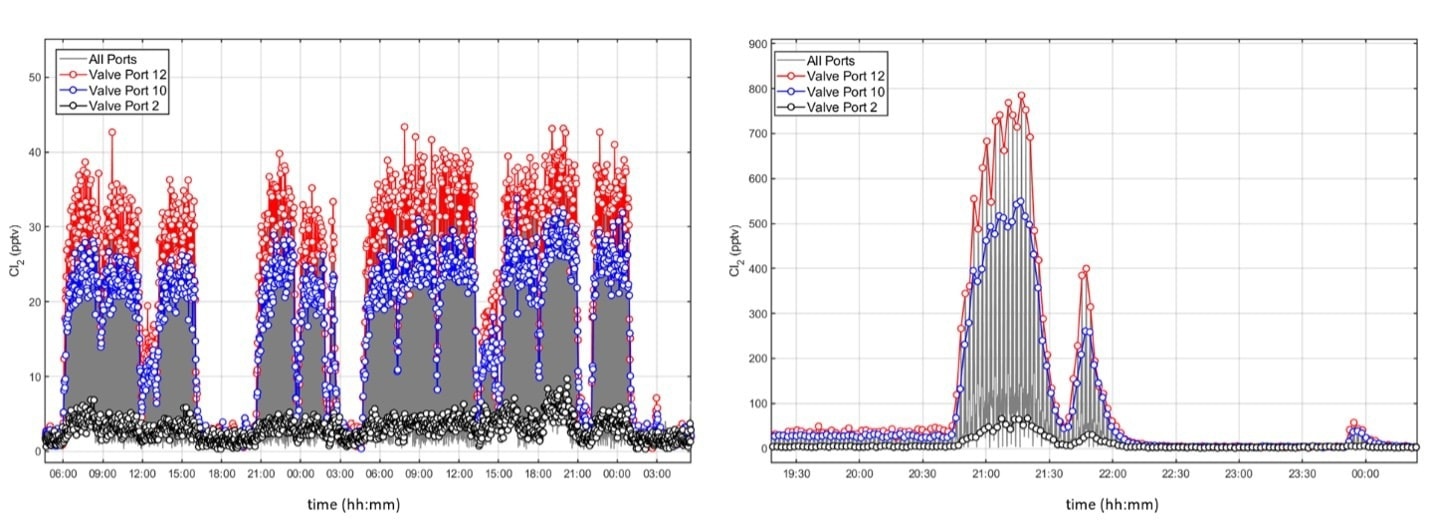
Figure 4. Chlorine ( Cl2) measurement in a fab. Left: recurring events with low concentrations ~50 pptv with measurement points at 3 different locations highlighted. Grey lines are the 12 port switching in a cycle of 2 minutes. Right: Excursion event reaching concentrations of almost 1 ppb in port 12 and 500 ppt in port 10, while other locations in the fab were minimally impacted. Image Credit: TOFWERK
This article demonstrates the utilization of a multiport valve system to enhance the efficiency of monitored locations and assists in identifying processes or events that reduce production yield.
1 Depending on the contaminant's physicochemical characteristics, its sampling might be delayed due to interactions with the sampling lines. This effect remains independent of the analyzer and primarily depends on the contaminant's volatility, absorption, and adsorption.

This information has been sourced, reviewed and adapted from materials provided by TOFWERK.
For more information on this source, please visit TOFWERK.