When searching for analytical equipment to support top-tier production, a trustworthy supplier becomes paramount. This includes not only offering dependable equipment but also housing experts who can address questions and ensure the appropriate techniques are employed for specific goals.
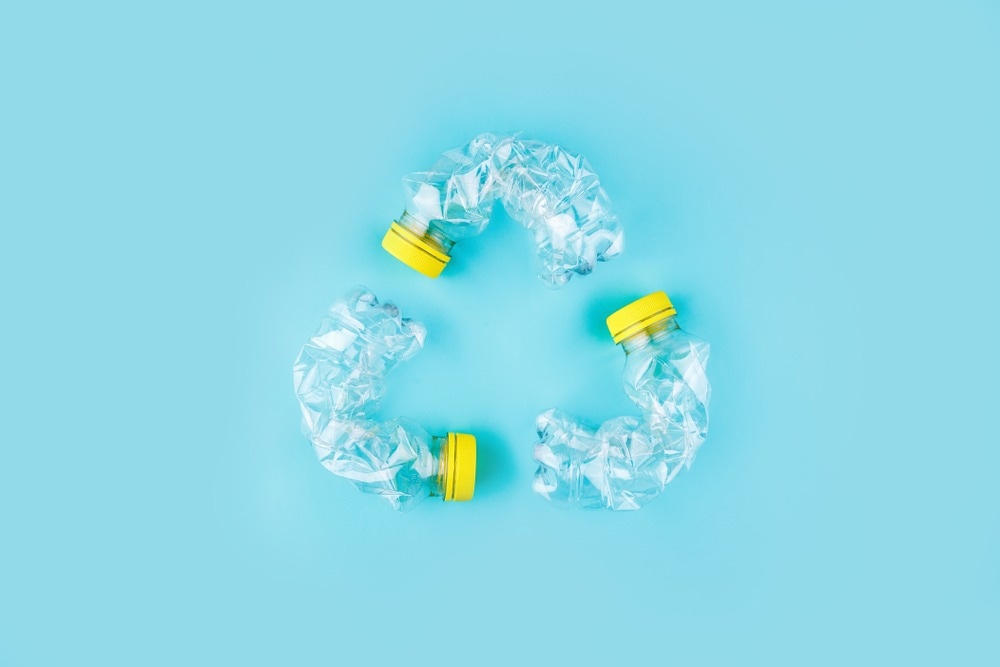
Image Credit: shutterstock.com/Mykolastock
For 50 years, Hitachi has collaborated closely with clients across various industries, crafting tailored testing methodologies for countless industrial applications. Hitachi’s applications and product specialists remain readily available to guide on addressing analysis challenges most effectively.
One of Hitachi’s most recent engagements involved a customer from the polymer industry inquiring about the incorporation of recycled plastic into production.
In response, Hitachi sought the expertise of the thermal analysis product manager, Olivier Savard, who enthusiastically shared insights into the most suitable techniques and instruments for working with recycled plastic while maintaining stringent quality standards.
Utilizing Differential Scanning Calorimetry (DSC) to Confirm Polymer Type
Differential scanning calorimetry (DSC) proves to be the ideal instrument for easily verifying the specific polymer type and the potential presence of other polymers, such as the combination of polyethylene (PE) and polypropylene (PP).
Like many materials, polymers exhibit distinct thermal properties during heating or cooling. Certain polymers exhibit a sole melting point, while others feature a glass transition and/or a re-crystallization point. These properties are intrinsic to each polymer and dependent on their category, synthesis, or the inclusion of additives during production.
Accurately determining the temperature and energy required for these thermal transitions represents a practical approach to confirming their identity, a task well-suited for a DSC.
By subjecting a known quantity of polymer to a specific heating rate (typically 10 °C per minute) and monitoring the sample’s temperature in comparison to an inert reference (typically an empty aluminum pan), the DSC precisely detects various thermal transitions within the polymer.
Once these transitions are detected, the results can be conveniently compared to expected values. For example, this facilitates the verification of whether the melting temperature of a fresh polymer batch corresponds to the reference.
A DSC not only confirms the polymer’s accuracy but also identifies potential contamination, such as the presence of PP within a PE sample.
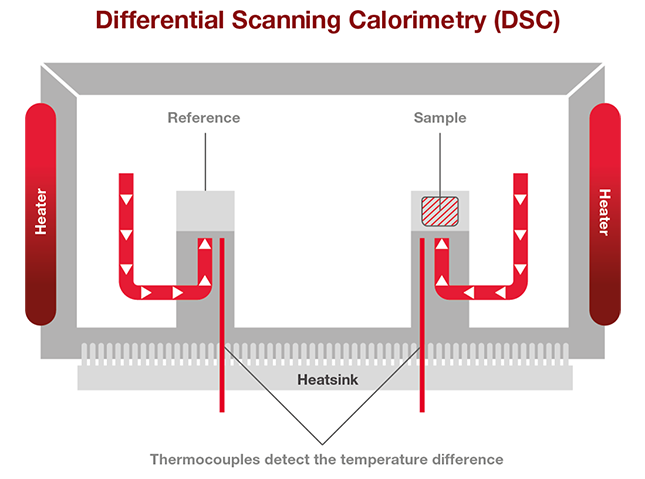
Image Credit: Hitachi High-Tech Analytical Science
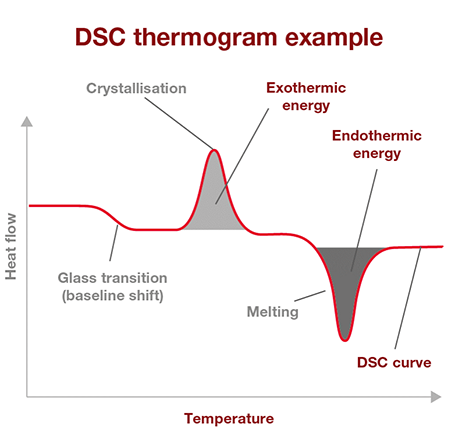
Image Credit: Hitachi High-Tech Analytical Science
Hitachi’s NEXTA DSC range is designed for precise material testing and characterization based on thermal attributes like melting points, crystallization, and glass transition.
For the development of new materials, the NEXTA DSC600 stands out as the instrument of choice, thanks to its high sensitivity and resolution, providing a comprehensive understanding of the material. In routine testing across a variety of applications, however, the NEXTA DSC200 represents the preferred instrument.
Both instruments seamlessly integrate with the Real View® camera system, facilitating real-time observation of polymer behavior and enhancing material comprehension.
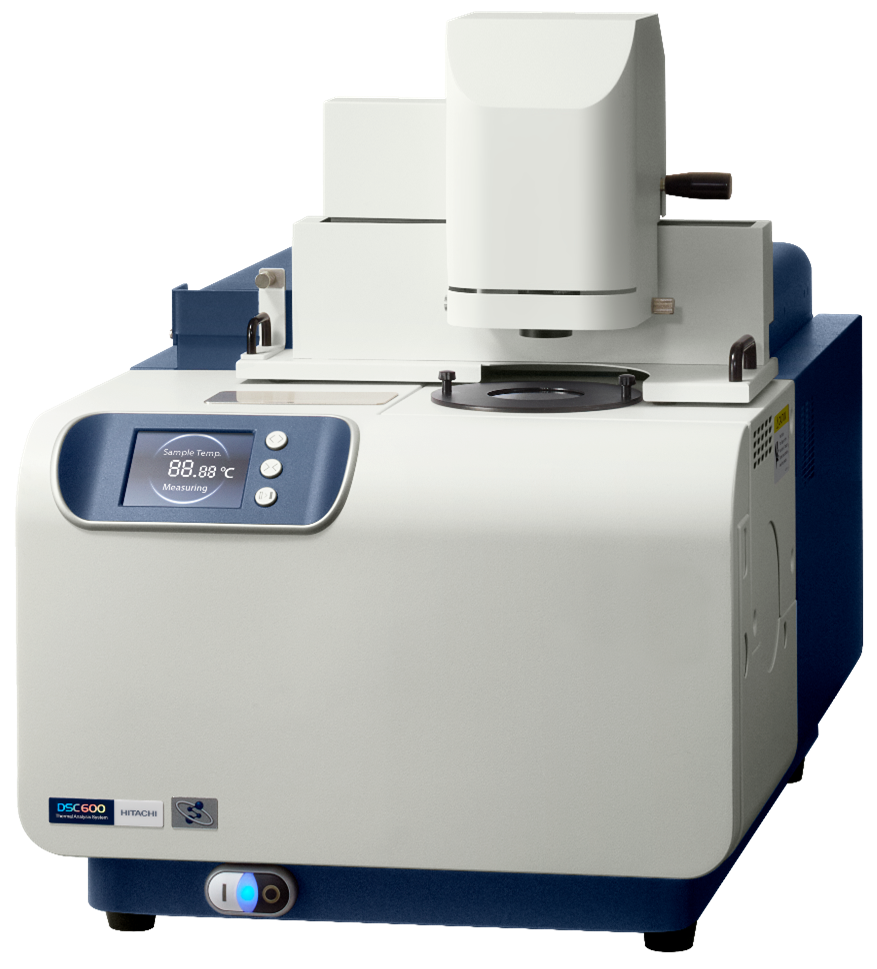
NEXTA DSC thermal analyzer. Image Credit: Hitachi High-Tech Analytical Science
To learn more about how the NEXTA DSC range works for polymer analysis, please see the following application notes:
- Application note: DSC measurement of polypropylene
- Application note: Thermal analysis of biodegradable plastic - polylactic acid (PLA)
- Application note: Thermal Analysis of Silicone Rubber
- Application note: DSC and DMA measurements of silicone rubber
- Application note: RV-DSC measurement of thermal expansion capsules
- Application note: Compatibility observation of LDPE and HDPE using RV-DSC
- Application note: RealView DSC measurement of foamed polystyrene
- Application note: Thermal analysis of polyvinyl chloride slip-proof sheet
- Application note: DSC measurements of epoxy resins
- Application note: Oxidation induction time (OIT) measurements
Leveraging Thermogravimetric Analysis (TGA) for Assessing Additive Levels in Polymers
Thermogravimetry (TGA) proves to be a valuable technique for ascertaining the composition of polymers.
It is widely used to determine polymer purity and the presence of additives, including plasticizers, pigments (e.g., carbon black or titanium dioxide (TiO2)), and inorganic constituents within materials. TGA also yields critical insights into the quantities of UV stabilizers and antioxidants.
Like most materials, various polymer types and their additives undergo evaporation or decomposition at distinct temperature intervals.
During these transitions, the polymer’s weight decreases proportionally to the content in the sample, enabling the quantification of each constituent. The process of quantifying these weight reductions, and thus measuring the amount of each component in a material, is achieved through TGA.
Through the application of a specific heating rate (typically 10 °C/minute) to a known quantity of polymer under controlled atmospheres (nitrogen or air), TGA precisely regulates temperature while measuring weight loss. Given that most materials exhibit unique degradation patterns, TGA facilitates the quantification of ingredients within the polymer.
For example, a rubber containing an oil extender and carbon black can have each component quantified using TGA. The oil is the first to evaporate, followed by the rubber in an inert atmosphere.
The inert atmosphere (nitrogen) is then exchanged for a combustive atmosphere (air), causing the carbon black to combust and enabling its quantification.
It is important to note that inorganic materials like calcium carbonate or titanium dioxide present challenges when measured by TGA, as they do not exhibit weight loss.
Non-combusting ingredients, however, can be quantified, constituting what is often referred to as “ash content.” Other techniques, such as X-Ray fluorescence (XRF), are employed to quantify each component within the ash content.
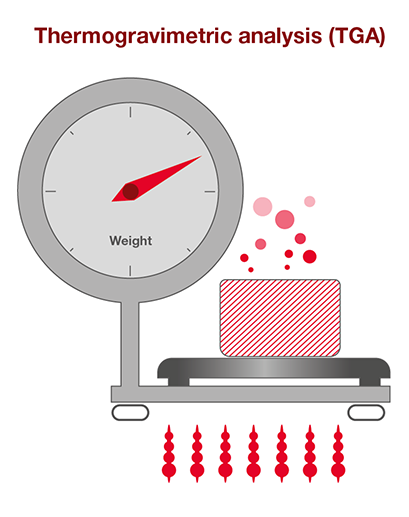
Image Credit: Hitachi High-Tech Analytical Science
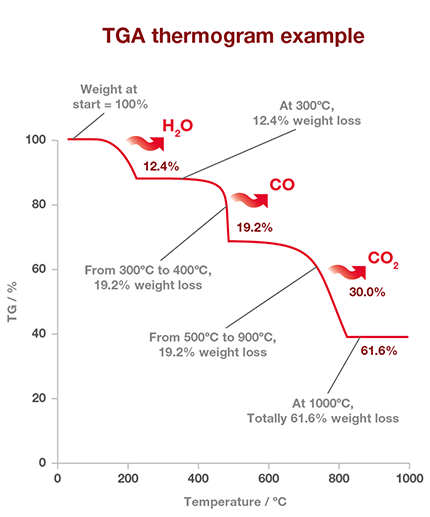
Image Credit: Hitachi High-Tech Analytical Science
The NEXTA STA instruments seamlessly combine DSC and TGA measurements within a single instrument, providing a comprehensive understanding of materials and any potential impurities they may contain.
Similar to the NEXTA DSC, the NEXTA STA instruments are compatible with the Real View® camera system, enabling the monitoring of polymers as they undergo heating and cooling. The accompanying images, coupled with the results, offer a more comprehensive view of the work.
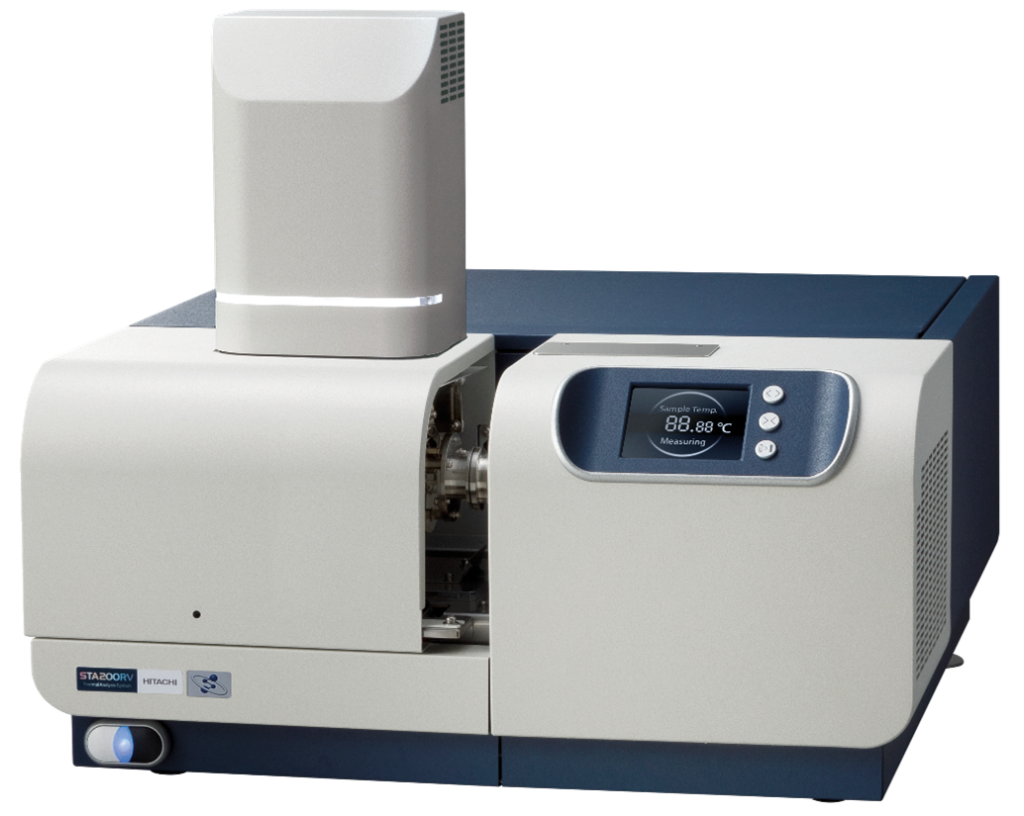
NEXTA STA200RV thermal analyzer. Image Credit: Hitachi High-Tech Analytical Science
For detailed explanations and test results utilizing these instruments, the application notes below provide further insights:
- Application note: Thermal analysis and SPM evaluation of carbon black in rubber
- Application note: Thermal Analysis of Silicone Rubber
- Application note: Observation of the decomposition behavior of PET by using RealView TGA
- Application note: TGA/DTA measurements of decomposition of adhesive
- Application note: Thermal analysis of polyvinyl chloride slip-proof sheet
- Application note: Thermal analysis of rubber
Identifying and Quantifying Inorganic Fillers and Other Additives in Recycled Polymers Using XRF Analysis
XRF analysis facilitates an understanding of various aspects of the materials being investigated. For example, it aids in determining the quantity of titanium dioxide within the material. This swift and precise method reveals the elemental composition of the materials within seconds, with results displayed on-screen.
This non-destructive method enables operators to track catalyst residue levels in virgin polymers during the polymerization process.
XRF can also quantify the amount of additional elements, including antioxidants, antistatic agents, flame retardants, lubricants, stabilizers, pigments, and additives.
XRF analyzers are versatile and capable of examining a wide array of materials, including solids, liquids, powders, pastes, films, and pellets, making them well-suited for polymer analysis. These instruments swiftly provide comprehensive information about the material’s composition.
The selection of XRF analyzers includes the portable X-MET8000, as well as the benchtop LAB-X5000 and X-Supreme8000 analyzers. These products are designed to deliver dependable and quick results, prioritizing ease of use and suitability for operational needs. They are built to withstand the most demanding production environments.
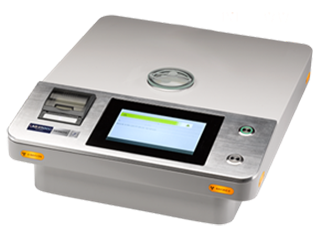
Image Credit: Hitachi High-Tech Analytical Science
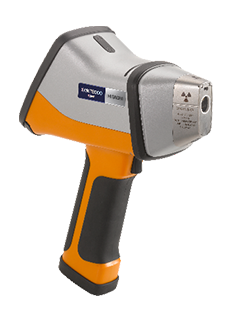
Image Credit: Hitachi High-Tech Analytical Science
For further details on the application of XRF analyzers in polymer analysis, please refer to the following application notes:
- Application note: LAB-X5000 for Zn stearate in polystyrene
- Application note: LAB-X5000 for catalyst residue and additives in PET
- Application note: X-Supreme8000, Determination of Co, Mn, and Br in PTA
- Application note: X-Supreme8000 for Mn in sealant
- Application note: X-MET8000, HBCD in waste polystyrene
- Application note: X-MET8000 determination of chlorine in plastic materials
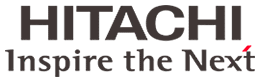
This information has been sourced, reviewed and adapted from materials provided by Hitachi High-Tech Analytical Science.
For more information on this source, please visit Hitachi High-Tech Analytical Science.