In today's ever-evolving manufacturing environment, efficiency and precision are pivotal when it comes to ensuring product quality and competitiveness.
Across diverse industries, the emphasis centers on harnessing advanced technology to optimize operational processes and address strategic requirements.
Within this context, this article will explore notable developments in quality control practices within the plating industry. These innovations are redefining quality assurance approaches, elevating operational efficiency, and enabling more informed decision-making.
Below, four approaches to enhance Industry 4.0 capabilities, particularly in the areas of data management and diagnostics, are discussed.
1. Seamless Plating Line Integration
Efficient integration into plating lines holds critical importance in contemporary manufacturing. It optimizes operations, reducing costs and enabling swift implementation of quality control measures. Real-time data analysis ensures product consistency while minimizing defects.
Seamless integration fosters connectivity and bolsters decision-making, providing a foundation for Industry 4.0 adoption and enhancing competitiveness in today's industrial landscape.
2. Faster Results Retrieval
Accelerating the retrieval of results is vital, especially for those who have not yet embraced automated QC testing. While XRF analysis is inherently quick, traditionally, significant time is spent on pre-analysis setups, such as selecting calibrations, spot sizes, measurement locations, and focusing procedures.
The FT230 significantly streamlines these setup tasks in a matter of seconds with its automated focus and Find My Part™ features. This efficiency not only reduces setup time but also streamlines the entire analysis process, enhancing productivity and decision-making capabilities.
3. Data Access for Informed Decisions
Data access is crucial, particularly for coatings XRF results. Swift access to this information is essential for timely decision-making.
Whether it involves generating customer reports or efficiently storing data in a networked folder for quality managers to review, the ability to quickly retrieve and utilize this data is crucial.
Additionally, for more integrated systems, such as quality management systems (QMS), supervisory control and data acquisition (SCADA) systems, or manufacturing execution systems (MES), fast data access ensures seamless operations.
This rapid access is essential because it enables organizations to respond promptly to deviations, optimize processes, and uphold the highest standards of product quality and efficiency.
4 . Proactive Instrument Health Monitoring
An essential aspect of a smart, integrated factory is the proactive monitoring of instrument health. This approach differs from traditional reactive methods by enabling manufacturers to anticipate potential equipment failures and strategically plan maintenance.
Proactive monitoring aligns maintenance activities with production schedules, reducing unexpected downtime and its disruptive impact.
Early issue detection helps mitigate risks, safeguard equipment, and maintain product quality. Ultimately, instrument health monitoring empowers factories to allocate resources efficiently, enhance operational effectiveness, and maintain a competitive edge in today's dynamic manufacturing landscape.
The plating industry's progress toward enhanced quality control mirrors the broader manufacturing landscape's pursuit of efficiency and precision. These innovations have not only enhanced quality assurance but also equipped manufacturers with the tools for better decision-making and increased operational efficiency.
The integration of plating lines, expedited results retrieval, rapid data access, and proactive instrument health monitoring represents a transformation that positions manufacturers for a competitive future.
These advancements are not solely about embracing smart industry practices; they serve as a testament to the industry's commitment to quality, efficiency, and resilience in an ever-evolving business ecosystem.
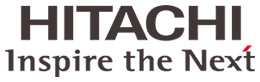
This information has been sourced, reviewed and adapted from materials provided by Hitachi High-Tech Analytical Science.
For more information on this source, please visit Hitachi High-Tech Analytical Science.