This article explores viscosity, covering definitions, measurement considerations, viscometer selection, and the symbiotic relationship between viscosity and rheology.
Viscosity Defined
1. What is the viscosity of my product?
- Kinematic viscosity n (nu), comes from flow time measures, considers gravity, and is for less viscous fluids like Newtonian fluids. It is in Stokes, cStokes, or cm2/s.
- Dynamic viscosity h (Eta) is for most formulated products, unaffected by density, often measured with rotary instruments. It considers the product's rheological behavior, having an absolute nature. Units are Pa. s, mPa. s (where 1 mPa.s = 20 °C water viscosity), or Poise, cPoise.
- In polymer fields, other viscosity values like specific, intrinsic, and relative viscosities help calculate the average viscous molar mass in solution.
2. Is the measurement of the specified viscosity significant? Answering this question prompts further inquiries:
- Why do I require the viscosity value? To adhere to a standard, assess product quality stability, validate an industrial process, innovate, or furnish a specification to a customer.
- Establishing the purpose of this measurement is the initial step.
- Does the temperature at the measurement time accurately represent the duration I aim to characterize? It is crucial to align with the conditions the product experiences throughout its life cycle.
- Do the quantified results of this measurement enable me to pinpoint disparities between two products? Precision alone in a measurement is insufficient to make it meaningful.
- What details should I convey regarding this viscosity value? Specifying the standard used and measurement conditions facilitates communication among different departments, customers, and suppliers.
- Why might I observe a discrepancy in viscosity values compared to my supplier? This necessitates a precise and transparent discussion about the measurement methods employed by each party. Including detailed information alongside the provided viscosity value simplifies conducting measurements under similar conditions.
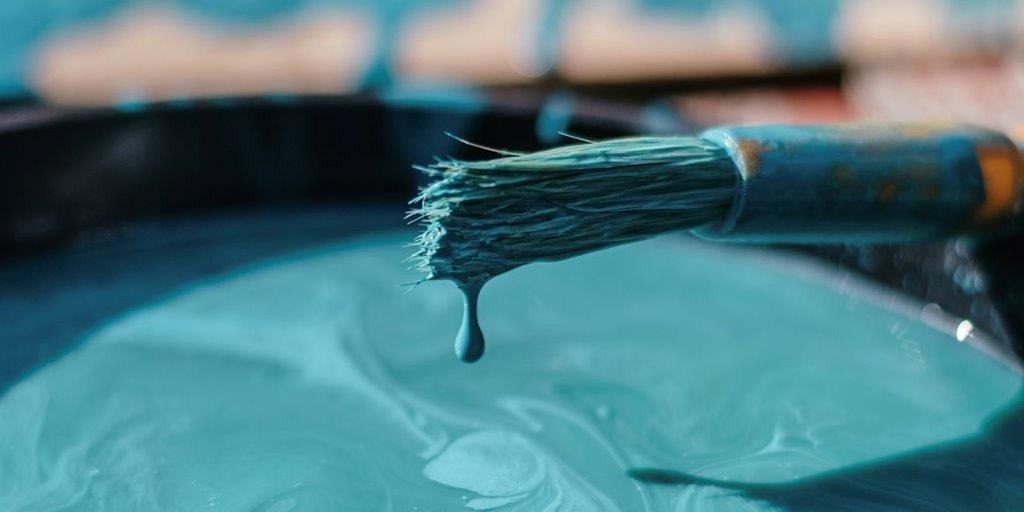
Image Credit: Paul N. Gardner Company, Inc.
Viscosity Measurement
1. Which factor holds importance in ensuring an accurate viscosity measurement?
The critical elements to understand or regulate include:
- Temperature: This factor holds significance due to its potential impact on viscosity based on the sample's chemical composition. Temperature variations can alter viscosity values. However, maintaining consistency allows for effective comparison or adherence to standard values.
- Speed or Shear Rate: A pivotal parameter influencing the viscosity of non-Newtonian formulated products. Using defined or standard geometries, such as cone-plate or coaxial cylinder systems, is essential to control this factor effectively.
- Time: It stands as the third variable requiring control for various products. Viscosity tends to decrease with prolonged shearing compared to shorter durations. Although this thixotropic effect is uncommon, it can significantly impact processes and accuracy in viscosity control.
2. Choosing a viscometer: Which technology suits you best?
- Falling Ball Höppler viscometer: Ideal for Newtonian clear syrups and lotions standardized in pharmacopeia viscosity controls. It utilizes different-sized balls to measure a range of viscosities and offers temperature control via an external water circulation connected to a bath.
- Standard flow cups: These are prevalent in coating and paint applications, equipped with defined volumes and calibrated hole diameters, ensuring simplicity in use and suitability for solvent paints.
- Rotational viscometer with standard spindle: Complies with ASTM/ISO standards, widely used to measure relative dynamic viscosity across various product types. Ensuring accuracy requires considering parameters like speed, spindle, sample volume, and time.
- Rotational viscometer with shear rate defined geometries (cone-plate, coaxial systems): Recommended for non-Newtonian products across different industries, compatible with DIN/ISO standards. These configurations yield the most defined and absolute viscosity values.
Rheology - How Fluids Behave
1. What is the connection/distinction between Rheology and Viscosity?
- Viscosity serves as the elemental unit employed in rheological investigations conducted on a product, playing a crucial and intrinsic role in shaping the behavior of product rheology.
- Rheology, the science of flow, enables the understanding of how a fluid will respond to various parameters during its manufacturing, packaging, storage, transportation, and overall utilization.
2. Which instrument should be chosen to analyze the rheology of my product?
Sophisticated, intricate, and costly solutions are often recommended, but practicality may not always be the best choice. Hence, a pragmatic approach is recommended based on the product being analyzed:
- What volume is involved?
- What is the viscosity range?
- What is the nature of the product?
- Is the product loaded or unloaded?
- What level of expertise is required (quality control, R&D, basic research)?
- What is the budget available?
Do in-house skills exist to proficiently operate the equipment and interpret data? Answers to these questions guide the selection of the most suitable equipment, accessories, and methods based on specific needs.
Accurate Measurements with a Rotational Viscometer
Verify the proper calibration of the viscometer using an ISO 17025-certified calibration oil.
- Prepare your sample following a standard test method, such as ASTM D2196-10 Standard Test Methods for Rheological Properties of Non-Newtonian Materials by Rotational Viscometer, or ISO 2555, ISO 1652 [1].
- Maintain consistency in viscometer, spindle, rotational speed(s), test time, container specifications, and sample size for repetitive and quality control testing. Always utilize the spindle guard leg.
- Control ambient temperature and sample temperature with a temperature bath or suitable accessories for accurate and repeatable results. Allow at least one hour for equilibration before measurement. Use a sample temperature probe during measurement to ensure constant sample temperature.
- Verify the cleanliness of the spindle, ensuring the shaft is unbent and free of dings or dents.
- Avoid introducing air bubbles during sample preparation.
- Exercise caution to prevent shearing of the sample during preparation, particularly with materials exhibiting shear-thinning or shear-thickening behavior.
- Ensure the sample container is residue-free from previous tests.
- Immerse the spindle in the sample up to the middle of the line on the shaft, avoiding overfilling or underfilling to prevent erroneous results.
- Minimize turbulence, especially with lower viscosity samples, which can distort results, particularly at higher speeds.
- Utilize the same test time, as many fluids undergo viscosity changes over time.
- In most cases, ensure the spindle rotates at least five times before recording a value, adjusting for non-Newtonian fluids as needed. Allow the displayed viscosity to stabilize before measurement.
- Prevent sample drying or evaporation, as this can lead to increased viscosity.
Choose the Correct Viscometer Range and Spindle
Rotational viscometers are available in three distinct viscosity ranges to accommodate various viscosity measurements.
Determine the viscosity range that closely aligns with the viscosity of the products under evaluation—whether it falls within the low, medium, or high viscosity category.
Source: Paul N. Gardner Company, Inc.
Low Viscosity |
Medium Viscosity |
High Viscosity |
Adhesives (solvent base) |
Adhesives (hot melt) |
Asphalt |
Biological Fluids |
Ceramic Slurries |
Caulking Compounds |
Chemicals |
Creams |
Chocolate |
Coatings, Water-Based |
Dairy Products |
Epoxies |
Edible Oils |
Detergents |
Gels |
Inks, Water-Based |
Dressings & Sauces |
Grease |
Juices |
Gums |
Inks (ballpoint, offset) |
Liquid Soap |
Inks (screen printing) |
Mayonnaise |
Liquid Wax |
Lotions & Cremes |
Molasses |
Mouthwash |
Paints |
Ointments |
Paints, Latex |
Paints & Coatings |
Pastes |
Photo Resist |
Paper Coatings and Pulp |
Peanut Butter |
Soda |
Plastisols |
Putty |
Solvents |
Shampoo & Conditioner |
Roofing Compounds |
Select Spindle and rotational speed. Selecting the Spindle and Rotational Speed involves considering various factors:
- For replication purposes, match the spindle, rotational speed, container, and sample size used in the method you intend to duplicate.
- To approximate a particular shear rate, such as the shear rate during product application, select a rotational speed that mirrors that shear rate.
- You know the sample's viscosity to be tested, input the appropriate spindle code and RPM setting into your viscometer. The instrument will display the viscosity range for that combination. Experiment with different combinations to identify the suitable spindle.
- If you do not know the fluid's viscosity to be tested, aim for a speed and spindle combination that yields a torque reading between 10% and 100%. Prioritize the highest torque reading below 100% for accuracy. Test the sample with the selected spindle at various speeds. If a reading between 10% and 100% is unattainable, try a different spindle. Opt for the next smallest spindle if the reading exceeds 100% at the slowest speed. If the reading falls below 10% at the highest speed, opt for the next largest spindle.
- If you need to test at multiple speeds, choose a spindle that provides readings between 10% and 100% for at least three-speed settings.
For the lowest viscosity range, use the largest spindle at maximum speed, while the highest viscosity range can be measured with the smallest spindle at the lowest speed.
Evaluation of Viscosity Flow Curves
- Newtonian: Both the differential viscosity and viscosity coefficient remain constant with the shear rate.
- Shear-thickening: Both the differential viscosity and coefficient of viscosity increase continuously with the shear rate.
- Shear-thinning (pseudoplastic): Both the differential viscosity and coefficient of viscosity decrease continuously with shear rate, with no yield value.
- Shear thinning (pseudoplastic) with yield response: The differential viscosity and coefficient of viscosity decrease continuously with the shear rate once the apparent yield stress has been surpassed.
- Bingham plastic (ideal): Adheres to the Bingham relation ideally, with the differential viscosity remaining constant above the Bingham yield stress, termed plastic viscosity, while the coefficient of viscosity decreases continuously to a limiting value at an infinite shear rate.
- Bingham plastic (non-ideal): Above the apparent yield stress, the coefficient of viscosity decreases continuously, and the differential viscosity approaches a constant value with increasing shear rate. Extrapolating the flow curve from the linear, high shear rate region to the stress axis reveals the apparent Bingham yield stress, with the differential viscosity in the linear region referred to as plastic viscosity.
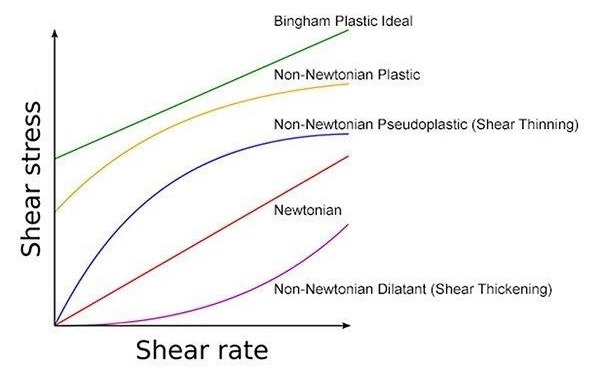
Image Credit: Paul N. Gardner Company, Inc.
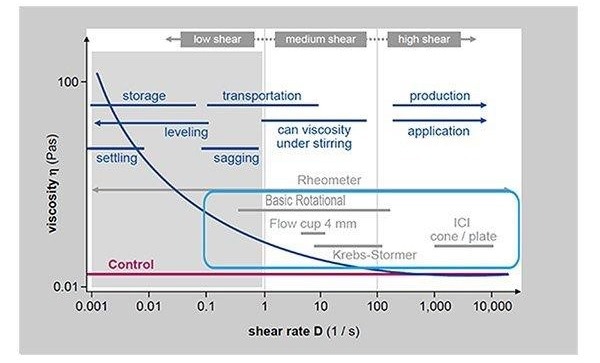
Image Credit: Paul N. Gardner Company, Inc.
Viscosity Methods and Influence of Shear Rate
Most paints' viscosity varies based on the applied shear rate, which measures how the paint is worked or sheared during flow. Many paints exhibit lower viscosity with higher shear rates.
Different viscosity measuring methods employ varying shear rates during measurement. Choosing a method that offers a consistent shear rate is crucial when assessing paint quality. The image provides an overview of shear rates applied in specific applications alongside measuring methods.
1. Rheometers are preferred instruments for studying comprehensive rheological behavior. Although they provide a holistic view, they are complex to use and interpret, require highly trained personnel, and are relatively expensive.
2. Rotational Viscometers are user-friendly and commonly used for Quality Control (QC) applications. Similar to rheometers, they yield repeatable and reliable results, functioning at shear rates most suitable for specific applications:
- Basic rotational viscometers are highly versatile, covering various shear rates and viscosities.
- Krebs or Stormer viscometers are best suited for paints applied with a brush or roller, operating at medium shear rates between 10 to 100 s-1.
- Cone and plate viscometers are often employed at high shear rates, allowing viscosity control during application, and capable of measuring at shear rates as low as 20 sec-1.
3. Flow Cups are cost-effective and offer a swift means to assess viscosity. Their primary output is the efflux time, convertible to kinematic viscosity. They should only be used for Newtonian liquids to ensure accuracy. Refer to the Insta Visc Viscosity Calculator app for assistance in converting measurements from flow cups into viscosity values.
Viscometers for Special Applications
- Cone and Plate Viscometer: Utilized for dynamic viscosity measurement as per DIN ISO 2884-1 and ASTM D4287. They are practical for QC or R&D labs, facilitating quick and straightforward material testing, suitable for both Newtonian and non-Newtonian materials with viscosities up to 15,000 poise and shear rates ranging from 25s-1 to 13000 s-1. They come with fixed or set speeds and incorporate heating and cooling functions for testing within temperatures from 5 °C to 235 °C.
- Krebs Stormer Viscometer: The prevalent method for gauging the viscosity of architectural paint involves the Krebs Stormer viscometer, detailed in ASTM D562. This viscometer employs a rotating paddle within a standardized container, rotating at 200 rpm through the paint. It measures the resistance offered by the paint, expressed in Krebs units (KUs). A higher KU number indicates higher paint viscosity. Modern Krebs Stormer viscometers, such as the BYK byko-visc DS, also concurrently display viscosity in centipoise (cP) and grams (gm). The BYK unit functions within the 40-141 KU range, equivalent to 27-5274 centipoise (cP) according to ASTM D562. These viscometers are user-friendly, delivering consistent results without the need for manual calculations.
- Measurement of Creams, Gels, and Ointments: Flow characteristics are important in the cosmetic industry. These products exhibit shear-thinning behavior, indicating a viscosity decrease with increased shear strain. Creams, ointments, and gels display plastic behavior, not flowing solely due to gravity. They might also possess viscoelastic properties, varying from solid-like to liquid-like products.
- Rotational Viscometer: Employing a defined rotation speed (ISO 2555) or a shear rate ramp (ISO 3219) aids formulators in understanding the force required to initiate flow, termed yield stress. Once flowing, creams or gels adopt a shear-thinning behavior, where the viscosity decreases under shear strain. Using the rotational viscometer based on defined shear rates (ISO 3219) provides insights into how the product will flow or apply to the skin.
Verification and Calibration of Viscometers with 17025 Certified Viscosity Standard
To ensure accurate testing of substances with varying viscosities, verifying and calibrating the viscometer within the viscosity range of the tested products is crucial.
Modern rotational viscometers like the BYK byko-visc RT series facilitate users to verify calibration and conduct on-site calibration using ISO 17025-certified standard oils.
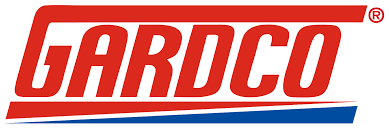
This information has been sourced, reviewed and adapted from materials provided by Paul N. Gardner Company, Inc.
For more information on this source, please visit Paul N. Gardner Company, Inc.