Can you please introduce yourself and tell us about your background in process safety testing?
My name is John Weaver. I earned a bachelor's degree in chemistry from Penn State University many years ago. I relocated to Sterling Drug in East Greenbush, New York, dedicating a decade to medicinal chemistry. After that, I transitioned to Pfizer, where I have been employed for over 29 years.
I initially worked in medicinal chemistry and later shifted to process chemistry. I spent three of my 19 years in process chemistry doing a secondment in the kilo laboratory manufacturing area processing batches. After that, I shifted to process safety, where I have been for the past ten years.
What is process safety testing, and how is it completed?
Process safety testing is crucial for preventing catastrophic accidents—such as explosions, fires, and other disasters—at processing facilities.
It involves various tests and screenings conducted at different stages of the pharmaceutical production process. The goal is to identify and mitigate potential hazards, including explosive or impact-sensitive properties of the materials involved.
In the early stages of the process, differential scanning calorimetry (DSC) is often employed as a screening tool for explosive properties. The DSC tests are sometimes complemented by other screening tools, such as thermal stability testing using the Thermal Screening Unit (TSU) offered by HEL, including ramp and isothermal testing.
For materials flagged as potentially impact explosive, an impact test is conducted using tools like the United Nations (UN) impact test.
The number of tests will increase as the chemistry moves into the early development area. This may include looking at explosivity, accelerating rate, gas flow measurements, and side stream and waste testing.
As the chemistry moves into the co-development or commercial route processes, the number of tests increases again. This includes dust testing and mal-operation testing.
Can you tell us more about DSC?
DSC is a critical screening tool that we use at Pfizer in our safety testing processes. When a new project or compound is introduced, the first step is to conduct DSC tests on all relevant materials.
DSC allows us to assess the thermal stability of materials quickly and efficiently, as it only requires a few milligrams of material. At Pfizer, we employ a gold-plated 40-microliter high-pressure pan for DSC tests, using a margin of safety adjustment (MOS) of a hundred degrees.
By employing DSC in the early stages of development, we can identify potential impact-sensitive compounds.
How is DSC used as a screening tool in assessing process safety?
During DSC analysis, we pay close attention to features such as the onset temperature and the presence of exothermic or endothermic reactions. Interpreting DSC data requires attention to specific conventions, such as the notation for exothermic reactions ("exo" in our case).
Additionally, we use Yida shock and explosivity curves to gain insights into the characteristics of the materials. If flagged as potentially explosive, we proceed to run an impact test, such as the UN impact test at Pfizer.
What is the MOS adjustment, and why is this necessary?
The MOS adjustment is a crucial aspect of our testing procedures, particularly in DSC and other safety tests. At Pfizer, we employ a MOS adjustment to enhance the safety margin in our data interpretation.
This adjustment involves subtracting a specific value, in our case, 100 degrees for DSC tests and 75 degrees for TSU tests, from the onset temperature recorded during these tests.
The MOS adjustment is a precautionary measure based on the sample size and the sensitivity of the instrument being used. This adjustment helps ensure that the recorded onset temperature provides a conservative estimate of the material's thermal properties.
Can you explain the role of impact tests in process safety methodology?
Impact tests play a crucial role in our process safety methodology, serving as a pivotal component in our safety assessments. When a compound is identified as potentially impact-sensitive during the DCS, the first step we take is to conduct an impact test.
At Pfizer, we utilize the UN impact test, which involves employing the OZM drop hammer with a 10-kilo weight dropped from a height of 60 centimeters.
The primary objective of impact tests is to evaluate whether a compound exhibits a flash or sound upon impact. These parameters are key indicators of the impact sensitivity of a material.
A compound is considered impact-sensitive only if it demonstrates a flash or a sound. We may also note discoloration during the test, however, this aspect is not a decisive factor in determining impact sensitivity.
In cases where full-scale UN tests for explosivity are required, the materials are sent out to a vendor for a screening assessment that involves three tests of explosivity: a time pressure test, a Conan test, and a gap test.
These tests use a substantial amount of material, are expensive, and require the use of explosives (which Pfizer does not have a permit for).
To avoid outsourcing, we have developed an explosivity test using the HS FinTech one.
Can you walk us through the steps involved in assessing and managing explosivity risks?
In our process safety methodology at Pfizer, assessing and managing explosivity risks involves a multi-step approach.
We initiate the process with a preliminary screening using DSC to identify potentially explosive compounds. Subsequently, we employ a customized explosivity screening test with the modified HS FinTech one, incorporating a fast-rate data capture card for efficient assessment.
By running this screening test with standards that mimic explosive behavior, we establish a threshold value specific to our equipment. Further evaluation is conducted using Accelerating Rate Calorimetry (ARC) to delve into detailed explosive properties.
The results are analyzed, and safety thresholds are set, incorporating MOS adjustments. Materials flagged as potentially explosive undergo remediation, and if needed, definitive determinations are made through UN tests.
This screening procedure helps us avoid sending materials out to be tested unnecessarily—most of the time, the compounds flagged as potentially explosive by the DSC are negative when tested further.
This systematic process, from initial screening to detailed assessments and remediation, ensures a comprehensive and cautious approach to explosivity risks in pharmaceutical development and manufacturing at Pfizer.
Can you walk us through the process of safety testing for an example generic process?
Consider a simple alkylation process involving phenol, thionyl chloride, cesium carbonate, and acetyl nitride for a generic example. The chemists provided the detailed process steps, and we requested a balanced chemical equation for comprehensive understanding. Starting with the charge of phenol, we conduct thermal stability testing using the TSU.
At each step of the process, including the addition of subsequent materials and the resulting solution, we perform TSU testing to assess thermal stability, endothermic or exothermic nature, and the potential release of gases.
If water is added, we conduct additional calorimetry for that step. Waste stream testing is then implemented, followed by thermal and isothermal stability testing and ARC testing at various stages.
This allows us to evaluate the safety implications associated with each step of the alkylation process, ensuring a comprehensive approach to process safety testing at Pfizer.
On average, how long does it take to complete process safety tests?
The duration of process safety tests can vary based on the specific characteristics of the materials being tested and the nature of the reactions involved. An ARC test can take a little over a thousand minutes, or approximately a day, for a specific compound.
Nevertheless, the time required for process safety tests can range widely. Factors such as the reaction's complexity, potential hazards, and the specific testing protocols being followed all contribute to the overall duration of the safety assessment.
At Pfizer, with two ARC instruments available, the capacity to run six tests per week ensures efficiency in the testing process, allowing for timely and thorough safety evaluations.
Click Here to Watch the Full Process Safety Testing Webinar
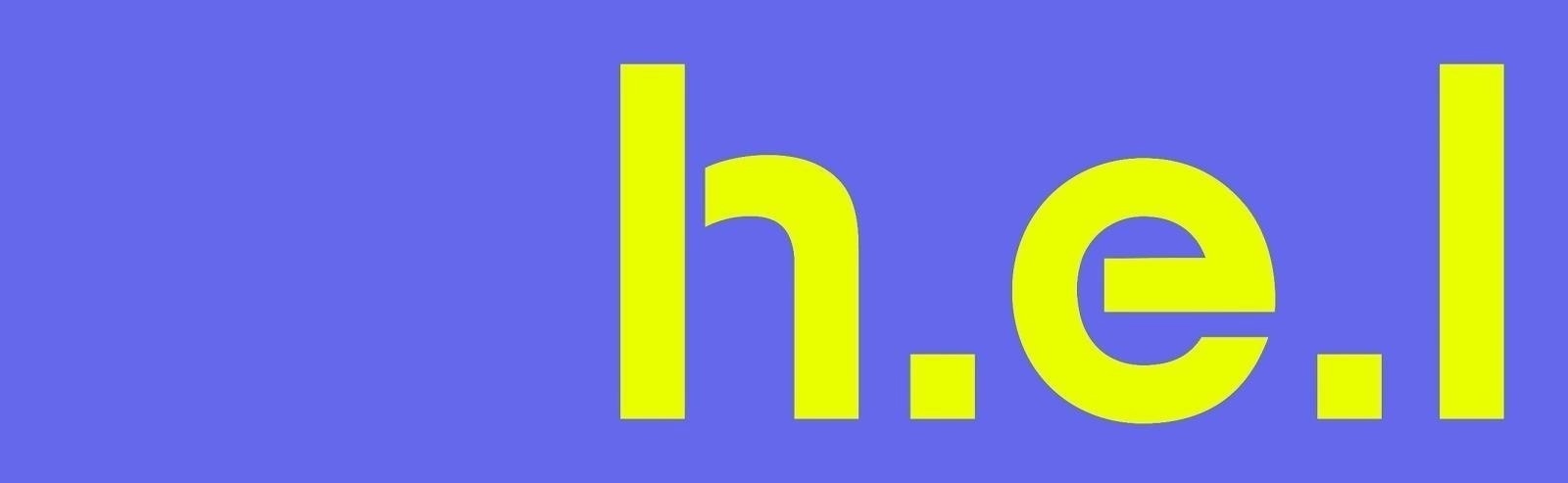
This information has been sourced, reviewed, and adapted from materials provided by H.E.L Group.
For more information on this source, please visit H.E.L Group.
Disclaimer: The views expressed here are those of the interviewee and do not necessarily represent the views of AZoM.com Limited (T/A) AZoNetwork, the owner and operator of this website. This disclaimer forms part of the Terms and Conditions of use of this website.