The electric vehicles (EVs) market has experienced remarkable growth in the past few years. In 2022, EVs constituted 14% of global car sales, with China taking the lead as over half of cars on its roads are already electric.1,2
The demand for EVs is surging and is projected to rise by 35% in 2023 as consumers respond to the climate-friendly and fuel-efficient features of these vehicles.3 Government policies are encouraging this seismic shift in the transportation industry, after the century-long dominance of the internal combustion engine.
This article explores a cutting-edge case study in electric vehicles (EVs), focusing on meticulously inspecting fuel cell separator layers in Fuel Cell Electric Vehicles (FCEVs).
Battery EVs and Fuel Cell EVs
Two major types of EV engines are utilized currently, and both provide the advantages of carbon-emission-free operation. Battery Electric Vehicles (BEVs) have "a battery pack that’s used to provide an electric current that powers your electric motor and thus propels the vehicle forward. The electric battery systems vary, but all of them have a basic anode, cathode, and electrolyte system that converts chemical energy (stored) into electrical energy."4
FCEVs utilize fuel cells to transform hydrogen into electricity to power the vehicle. "The chemical process that takes place involves an anode, cathode and electrolyte membrane system, similar to battery-powered EVs, but with a few additional steps in converting the energy from hydrogen into electrical energy" to power the vehicle."5
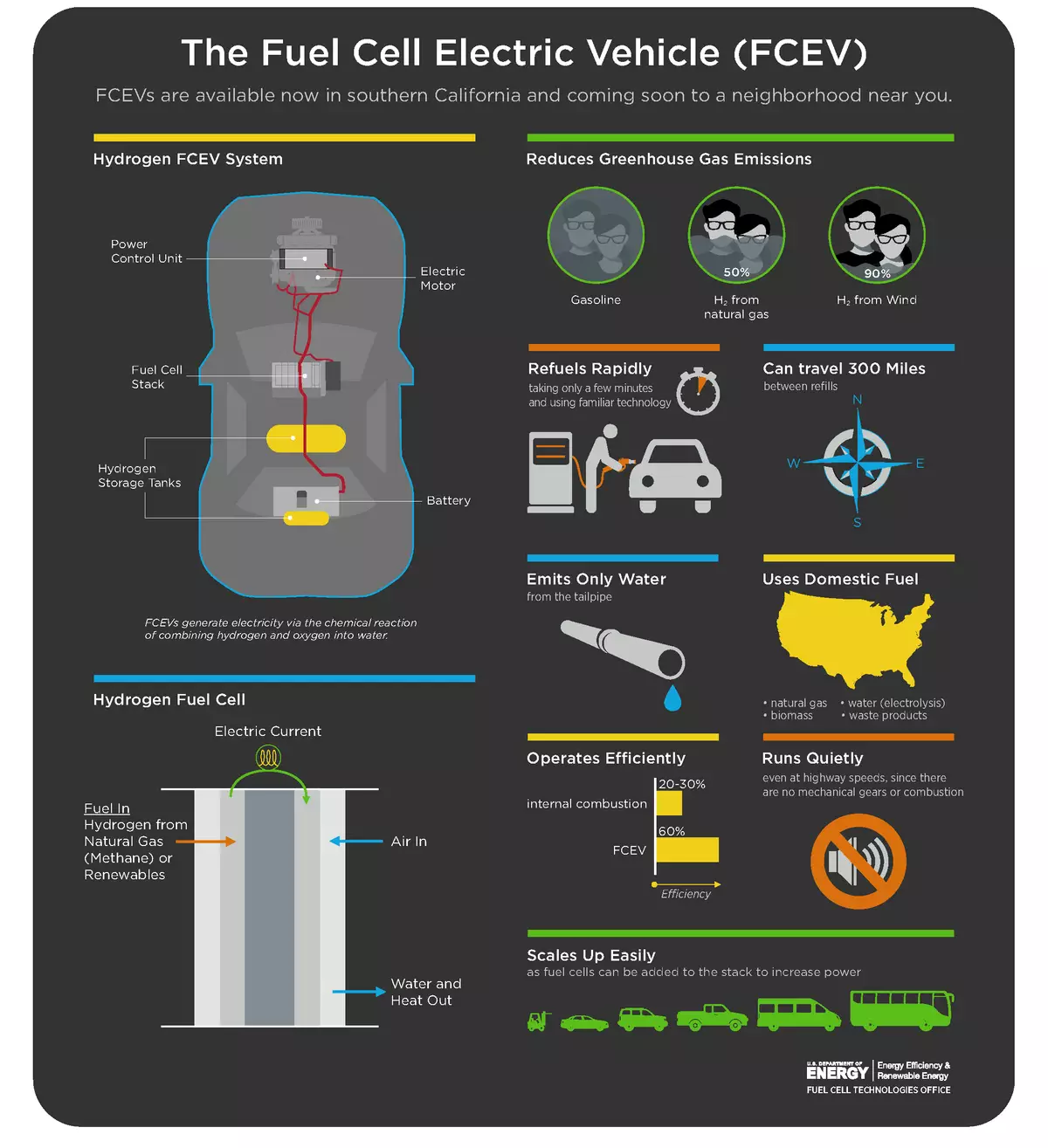
Image Credit: U.S. Department of Energy
An individual fuel cell created for vehicle applications produces "less than 1.16 volts of electricity—far from enough to power a vehicle. Therefore, multiple cells must be assembled into a fuel cell stack. The potential power generated by a fuel cell stack depends on the number and size of the individual fuel cells that comprise the stack and the surface area of the PEM [polymer electrolyte membrane]."6
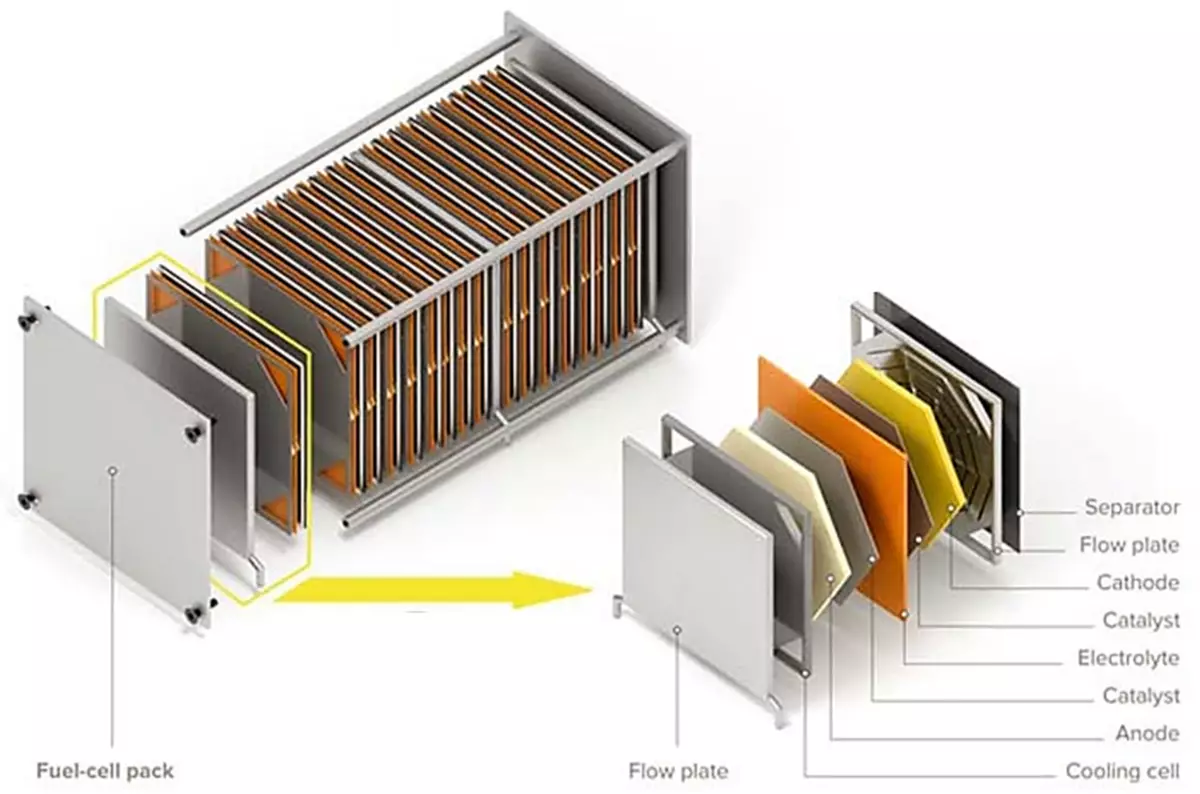
Diagram of a fuel cell stack and individual layers. Image Credit: Radiant Vision Systems
Fuel Cell Inspection Case Study
Toyota produced FCVs. The fuel cells must function perfectly as they are the central component in powering each vehicle. The fuel cells must, therefore, be free of defects and flaws. To achieve this, Toyota needed a method to assess both sides of the separator utilized in fuel cells for its FCVs. Traditional machine vision cameras did not produce clear images to identify fine dirt and small scratches.
The fuel cells utilize PEMs. Numerous PEMs are layered together and sandwiched between negative (anode) and positive (cathode) electrode layers. Separators (biopolar plates) are utilized to construct these layers into stacks and provide channels for gaseous air and fuel. Particles and scratches on the separators can hinder the performance of the fuel cell.
This case study describes how Toyota collaborated with Konica Minolta to employ a solution utilizing Radiant's ProMetric® Imaging Photometer, TrueTest™ Software, and a custom lighting configuration to conduct visual surface inspection of the fuel cell separators.
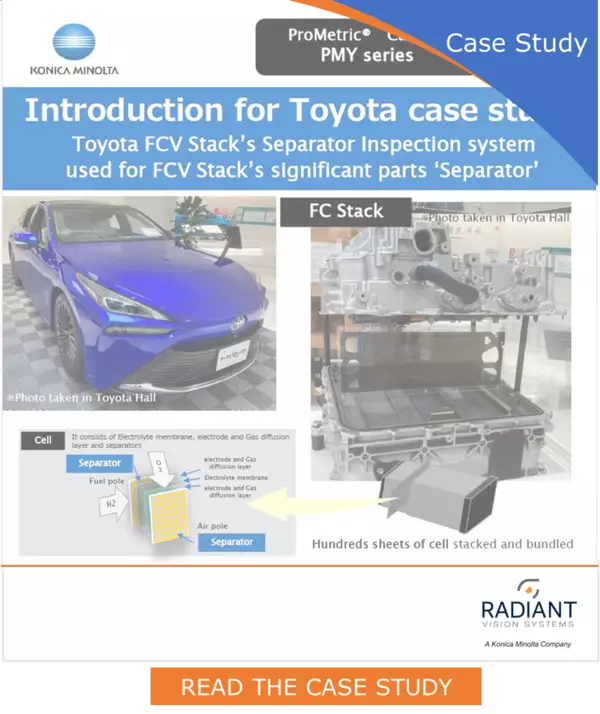
Image Credit: Radiant Vision Systems
References and Further Reading
- Global EV Outlook 2023, International Energy Agency (IEA), Paris , License: CC BY 4.0
- Ibid.
- "Demand for electric cars is booming, with sales expected to leap 35% this year after a record-breaking 2022", International Energy Agency (IEA), April 26, 2023.
- "Battery Electric Vehicles vs. Fuel Cell Electric Vehicles," Toyota of Downtown LA website,(Accessed August 15, 2023)
- Ibid.
- "How Fuel Cells Work," US Department of Energy (Retrieved August 15, 2023).
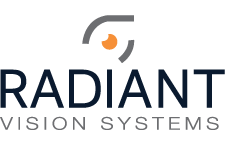
This information has been sourced, reviewed and adapted from materials provided by Radiant Vision Systems.
For more information on this source, please visit Radiant Vision Systems.