Aerospace applications require materials with distinctive qualities for extreme operating conditions.
Kyocera, a global leader in advanced technical ceramics, provides unique material solutions for aerospace applications. This article delves into some of these advanced materials and explores their pivotal role in driving innovations within the aerospace industry.
The aerospace sector depends on cutting-edge technology. Next- generation vehicles for atmospheric flight, low-earth orbit, or space exploration require the highest performance and reliability features.
Some of these features include, but are not limited to, being lightweight, compact, durable, and resistant to thermal shock.
Progress in this field hinges on pioneering approaches and innovative designs, which fundamentally rely on the evolution of new materials possessing vital physical qualities, such as high mechanical strength, low density, high fracture toughness, and high thermal shock resistance.
A material category that stands out with unique properties is advanced ceramics. Unlike polymers or metals, ceramics are distinguished by their ability to resist heat fluctuations and maintain dimensional stability at elevated temperatures.
While traditional ceramics encounter disadvantages relating to brittleness, advancing technology has led to the creation of ceramic composites that are characterized by enhanced reliability and improved properties.
So, what are these advanced ceramics, and how do they progress in a rapidly evolving and exceptionally demanding industry?
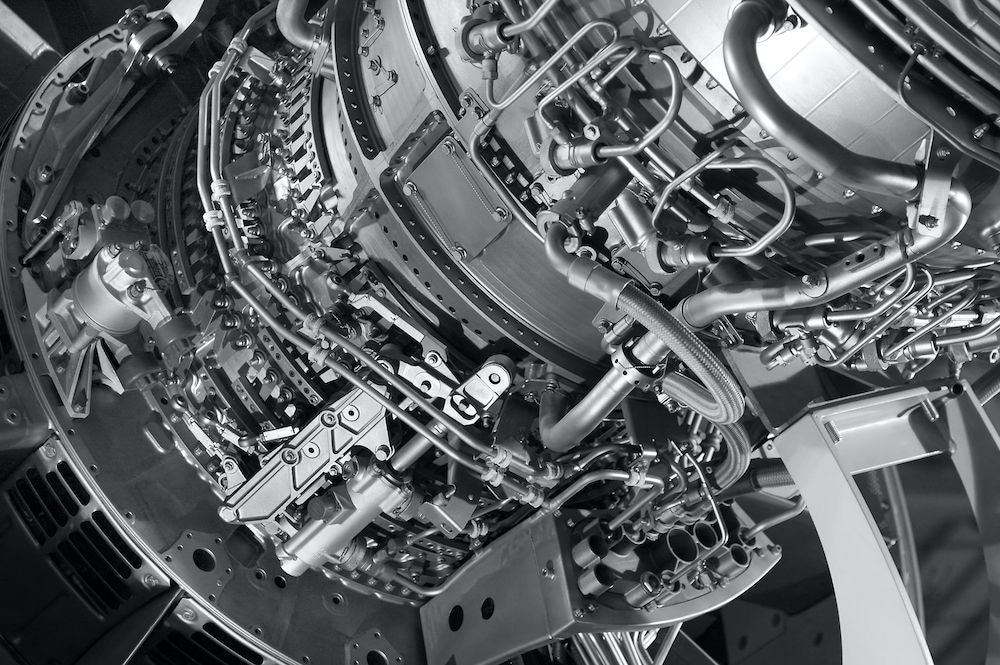
Figure 1. Fine ceramics are vital materials for aerospace propulsion system components due to their exquisite material properties. Image Credit: Kyocera International, Inc.
Exploring Advanced Ceramics
Aerospace requirements have created showcase applications for ceramics producers, particularly in Fine Ceramics. Non-oxides such as silicon carbide (SiC) and silicon nitride (Si3N4), and technical oxides like alumina (Al2O3), aluminum titanate (Al2TiO5), and zirconium oxide (ZrO2), headline the technical ceramics sector.
Offering an assortment of over 200 ceramic materials, Kyocera has also incorporated state- of-the-art ceramic composites, such as silicon-infiltrated silicon carbide (SiSiC), a material that possesses unparalleled mechanical and thermal properties.
An intriguing aspect of SiSiC is that it is electrically conductive, unlike most ceramics, which commonly have high electrical resistivity.
In creating such materials, Kyocera has developed a variety of advanced processing techniques in milling, turning, polishing, sintering, and coating ceramics. However, what makes the materials unique?
Table 1 illustrates a comparison between ceramics and metals utilized in the aerospace industry. Low density, high hardness, thermal conductivity, and modulus of elasticity are specific areas that differentiate Kyocera’s fine ceramics.
These ceramics also exhibit high thermal shock resistance, low coefficients of thermal expansion, high dimensional and chemical stability, and exceptional corrosion resistance, all of which solidify their standing in the aerospace industry.
In essence, enriched performance and long-term durability can be accomplished by employing advanced ceramics for application-specific conditions.
Table 1. A comparison between ceramic and metal properties. Source: Kyocera International, Inc.
Material Property |
Ceramics |
Metals |
SiSiC |
SSiC |
Si3N4 |
Al 6061 |
Ni 718 |
Density (g/cm3) at 20 °C |
3.05 |
3.1 |
3.22 |
2.7 |
8.22 |
Hardness, Vickers at 20 °C |
2040 |
2550 |
1530 |
111 |
380 |
Thermal Conductivity (W/m·K) at 20 °C |
175 |
125 |
20 |
166 |
14.2 |
Elastic Modulus (GPa) at 20 °C |
380 |
395 |
290 |
70 |
200 |
Applications of Advanced Ceramics
The captivating properties of advanced ceramics have rendered them valuable across a range of applications.
Propulsion systems, including the vital components of the rocket engine, demand high efficiency which is attained by reducing vehicle weight, minimizing fuel consumption, and enhancing material durability.
Silicon carbide (SiC), with its outstanding physical and high-temperature features (including low density, corrosion resistance, low thermal expansion, and high thermal conductivity), emerges as a suitable material that can maintain the propulsion system components’ conditions against harsh occurrences like deformation, creep, fatigue, heat transport, and corrosion.
Kyocera’s StarCeram® S sintered silicon carbide (SSiC) features excellent wear resistance, high strength, and high hardness, making it a significant candidate for such applications.
A reaction-bonded composite of silicon carbide particles in a surplus silicon matrix, known as StarCeram® Si silicon infiltrated silicon carbide (SiSiC), is another product of Kyocera’s fine ceramics that possesses exceptional performance parameters and finds uses in bearings, bushings, rotors, nozzles, seals, and wear protection parts.
Propulsion processes generate very high temperatures, which may adversely affect the propulsion components’ performance.
These include structural components, parts in engines and exhaust systems, and heat protection shields. SiSiC and SiC can easily guarantee high performance and long life, owing to their maximum service temperatures, as well as their high corrosion and wear resistance properties.
Technical ceramics also find use in the structural and frame parts for system integration. For instance, optical benches demand a certain degree of rigidity, light weight, mechanical vibration frequency, and thermal deformation resistance.
Ceramics’ damping ability, low density, shock resistance, and low thermal expansion render them superior materials for such applications.
Other applications for Kyocera’s silicon carbide-based materials and other fine ceramics, like StarCeram® N silicon nitride (Si3N4), span from electronics (like sensors, capacitors, and resistors), to mechanical and structural parts (like sliding rings, slide valves, cylinder linings, and welding rolls) that require thermal stability, high hardness, and rigidity.
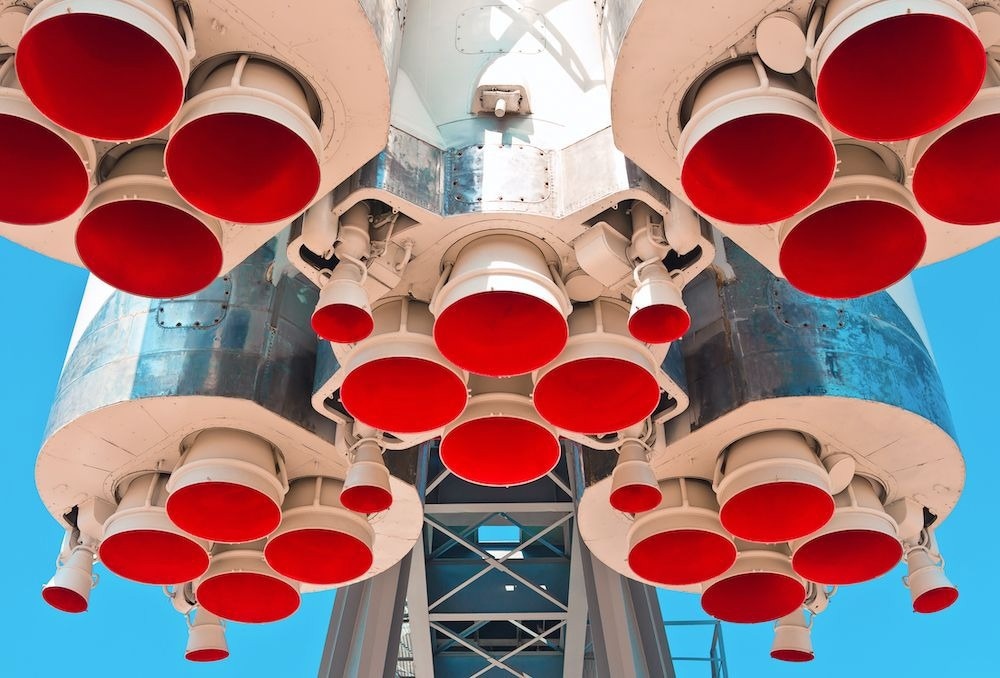
Figure 2. SSiC and SiSiC materials can be used in nozzles of space rockets, with their excellent high-temperature properties. Image Credit: Kyocera International, Inc.
What Does the Future Hold for Advanced Ceramics?
The realm of advanced ceramics continues to expand as ceramics and ceramic composites support new and diverse aerospace applications. Their outstanding properties serve as a solid foundation for their significance in the materials race.
As modern and future aerospace innovations require enhanced properties (like weight reduction, hardness, and thermal characteristics), technical ceramics and ceramic composites will likely replace metals and glass-based materials, and lead to increased customization and optimization.
With in-house powder preparation and unparalleled materials expertise, Kyocera can provide reliable, high-performance advanced ceramics in over 200 formulations.
As the aerospace industry embraces new materials and ventures, Kyocera’s advanced ceramics will gain prominence in improving air- and spaceflight.
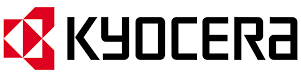
This information has been sourced, reviewed, and adapted from materials provided by Kyocera International, Inc.
For more information on this source, please visit Kyocera International, Inc.