In this interview, industry experts Stephan Botzki and Ian McEnteggart, senior applications engineer and composites market manager at Instron, provide key insights into mechanical testing for composites.
What are composite materials, and how do they compare to conventional materials such as metals and plastics?
Composite materials are engineered materials made from two or more components with significantly different physical or chemical properties. Usually, these components consist of reinforcing fibers and a matrix. When combined, these components can produce a material with properties that are more desirable than those of the individual components.
There are many different types of composite materials, but the most common type consists of continuous fibers embedded in a polymer matrix. The most common fibers are carbon or glass, embedded in a thermosetting or thermoplastic polymer matrix.
One of the most notable attributes of composite materials is their exceptional stiffness and strength-to-weight ratio (specific stiffness and strength). This makes composites particularly attractive to the aerospace industry, where weight reduction is crucial.
Unlike metals that are prone to corrosion, composites, particularly those with a polymer matrix - exhibit greater durability under harsh conditions. This resistance to corrosion broadens their use in chemical processing and marine applications. The anisotropic nature of composites is also a key feature. Anisotropy means that the material's properties vary with orientation. In composites, the arrangement of reinforcing fibers influences the material's behavior. These anisotropic properties allow engineers to tailor the material's characteristics to suit the specific requirements of an application.
Composites also excel in fatigue resistance. The combination of reinforcing fibers and matrix materials often results in materials that can withstand repeated loads without failure. This attribute is important in aerospace applications, where cyclic loading is common.
In the context of composite materials testing, can you elaborate on the various tests and challenges involved?
As mentioned above, composite materials are anisotropic (i.e. properties depend on direction) and they are also heterogeneous (i.e. they consist of fibers embedded in a matrix). Furthermore, the properties of polymer matrix composites may be affected by temperature and other environmental factors. This means that many more parameters are required to fully characterize the mechanical properties of a composite versus those of traditional materials such as metals.
The most basic mechanical test is a tensile test in which specimens are subjected to axial loading to measure properties such as modulus and strength. Test specimens, or coupons, are usually rectangular in shape with end “tabs” to prevent the surface of the specimen being damaged by the test machine grips. Common standards for composites tensile testing are ASTM D3039 and ISO 527-4/5. Tensile testing is straightforward in principal, but good specimen alignment is necessary in order to obtain accurate and consistent results.
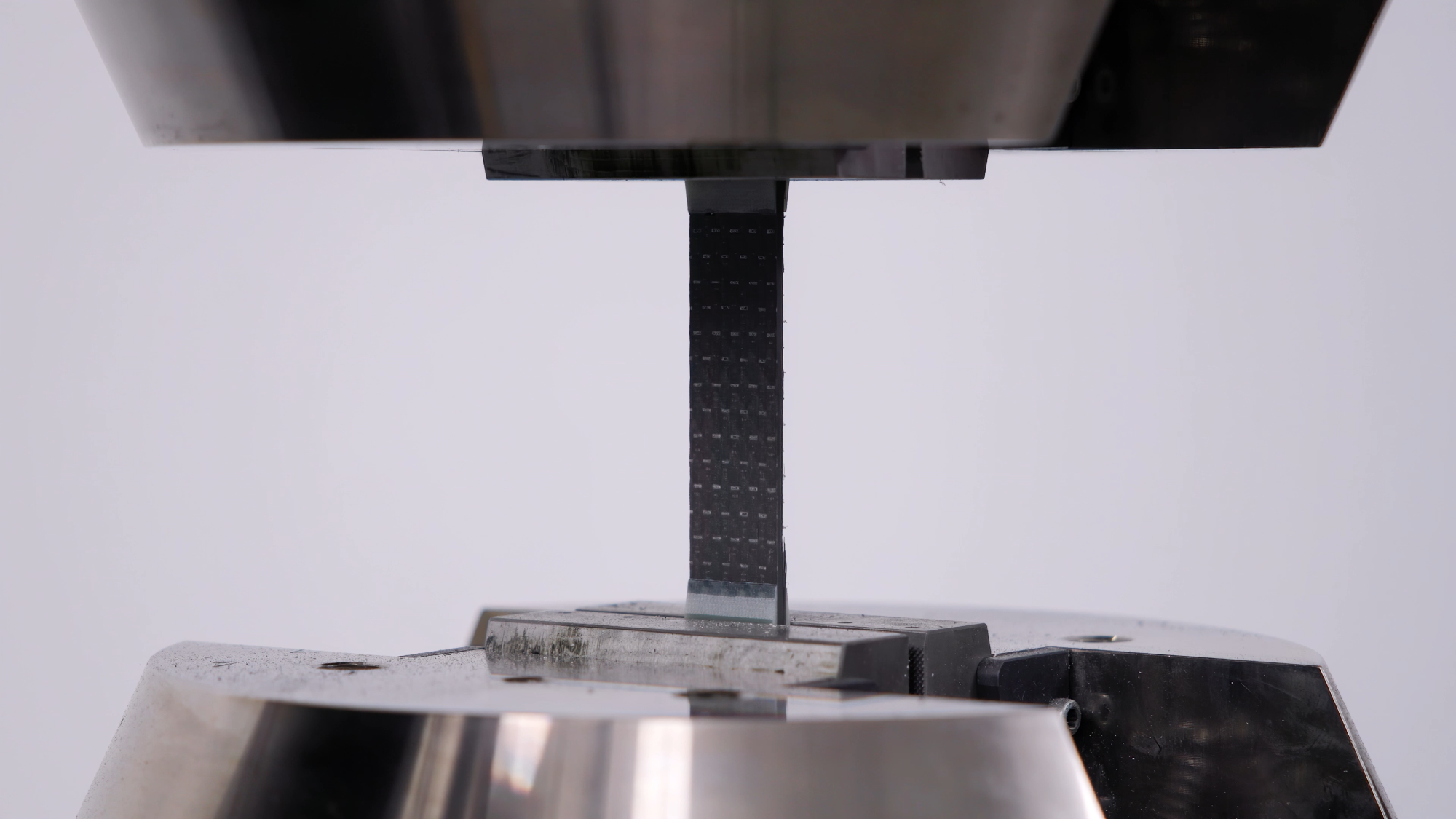
Figure 1 - Composites Tensile Test. Image Credit: Instron
Compression testing involves subjecting specimens to compressive forces. Composite materials are usually produced in the form of thin laminates, and although typically very stiff are prone to buckling under a compressive force. Specialized compression test fixtures are used to prevent buckling; these fixtures use either short unsupported gage lengths or supported gage lengths. The fixtures employ different methods of force introduction; either by end-loading, shear, or by a combination of both end-loading and shear. A commonly used compression test standard is ASTM D6641 Combined Loading Compression Test which employs a specimen with a short unsupported gage length along with a combination of end and shear loading.
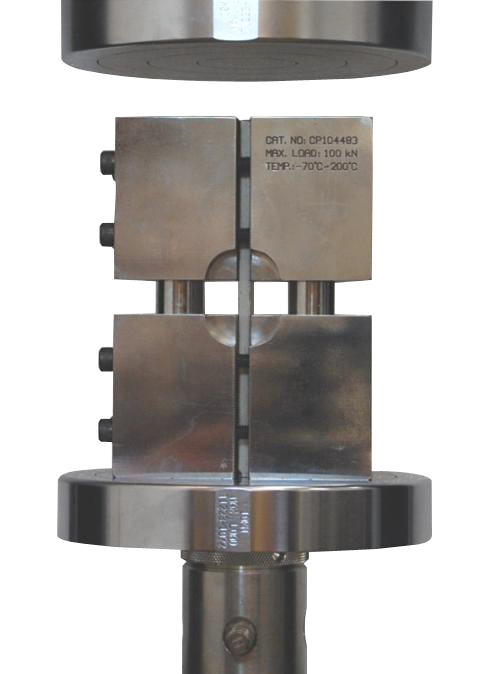
Figure 2 - ASTM D6641 Compression Test. Image Credit: Instron
Additionally, shear testing is crucial. Interlaminar shear strength (ILSS) tests, such as ASTM D2344 and ISO 14130, provide a measure of the bond strength between the fibers and the matrix. It is a simple and widely used quality control test. In-plane shear (IPS) testing, such as ASTM D3518 and ISO 14129, is also widely used in quality control, but V-notch shear methods, such as ASTM D5379 and D7078 can provide better data for design purposes.
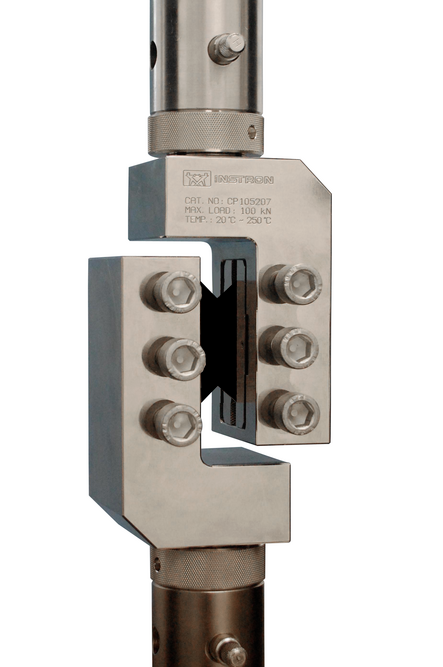
Figure 3 - ASTM D7078 V-Notch Shear Test. Image Credit: Instron
Flexure testing employing simple beam loading of a slender specimen (to minimize shear stresses), is another common test. Tests can employ either three-point or four-point loading. This method, governed by various standards such as ASTM D7264 and ISO 14125, provides modulus and strength data.
Can you elaborate on the significance of in-plane shear testing and interlaminar shear testing in evaluating composite materials? How are these tests conducted?
In-plane shear (IPS) testing and interlaminar shear testing (ILSS) are both employed to determine the shear strength of composite materials. In addition, the in-plane shear test provides shear modulus data.
In in-plane shear testing, a composite laminate specimen with fibers oriented at +/-45 degrees to the test axis is subjected to an axial force that generates a shear between the alternate layers of fibers. Along with force, both axial and transverse strain are measured during the test – shear strain is determined from these measurements which allows the shear stress/strain response to be recorded. It should be noted that the stress state in this test is not one of pure shear because the matrix is also subject to axial tension, hence the results do not accurately represent the true shear properties of the material.
Interlaminar shear testing (ILSS) sometime known as short beam shear (SBS) testing is usually performed by subjecting a short, relatively thick specimen to bending in a 3-point bend fixture. This geometry generates large shear stresses along the center of the specimen resulting in a shear failure in a successful test. Again, the test does not produce a pure shear stress due to the presence of bending stresses.
In-plane shear and interlaminar shear testing are mainly used for quality control testing. There are several other tests used to determine shear properties during the design process. V-notched shear tests (ASTM D5379 and D7078) require more complex specimens and test set ups, but they produce a region of pure shear. A recent development of the short beam shear test is the double beam shear test (ISO 19927) which produces a region of pure shear in a small bend specimen and can provide shear modulus data. Finally, ISO 20337 describes the use of a shear frame to determine the in-plane shear stress/strain response at large shear strains.
In your experience, what are some common challenges faced during composite material testing, especially when dealing with alignment issues?
One of the common challenges encountered during composite material testing revolves around alignment issues. Achieving precise alignment is crucial in ensuring accurate and reliable test results. Misalignment, whether concentric or angular, can lead to uneven stress distribution, affecting the material's behavior during testing.
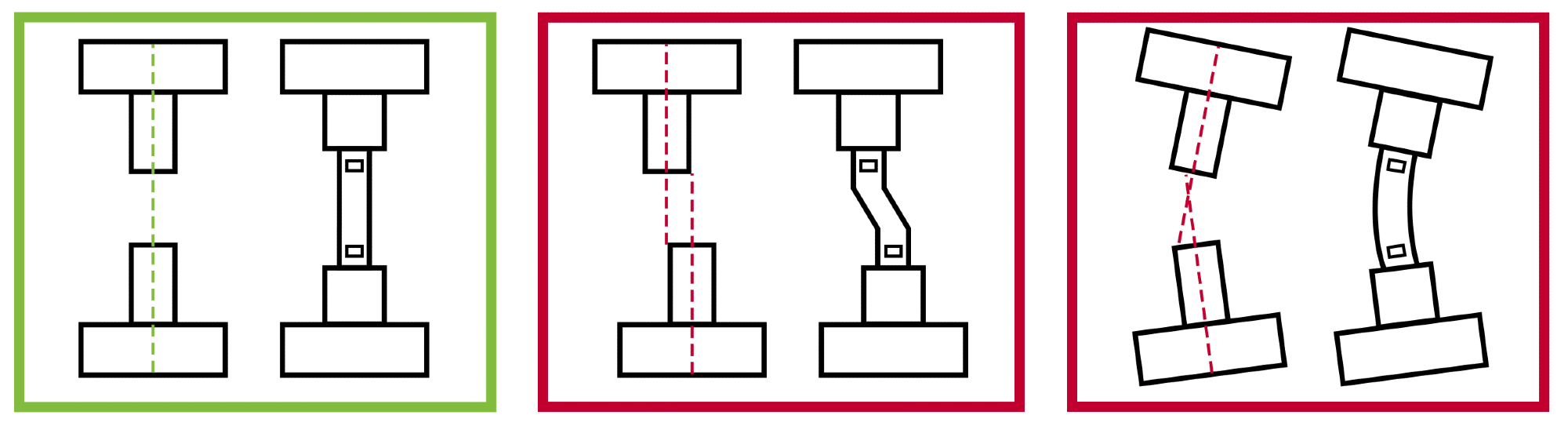
Figure 4 -Test Machine Alignment. Image Credit: Instron
The consequences of misalignment are more pronounced in composites compared to traditional materials such as metals. Metals, when misaligned, might yield in high stress regions, redistributing stress and still carrying a load. However, the limited strain capacity of composite fibers, especially in unidirectional materials, makes them more susceptible to rapid failure under misalignment, impacting the overall accuracy and reliability of the test data.
It is essential to utilize testing machines with high axial and lateral stiffness, guided fixtures with precision-machined guiding posts, and alignment fixtures to address alignment challenges.
How do explosive failures in composite materials impact the strain measurement techniques? What strategies can be employed to overcome these challenges?
Due to their sudden and dynamic nature, explosive failures in composite materials can significantly impact strain measurement techniques. Traditional strain measurement devices, such as extensometers, can also face challenges when dealing with explosive failures in composites.
To overcome these challenges, video extensometers have become the preferred solution. Non-contact video extensometers are isolated from the test specimens and immune from the effects of explosive failures. They can precisely measure strain without the limitations and potential damage that traditional devices may encounter in high-energy events.
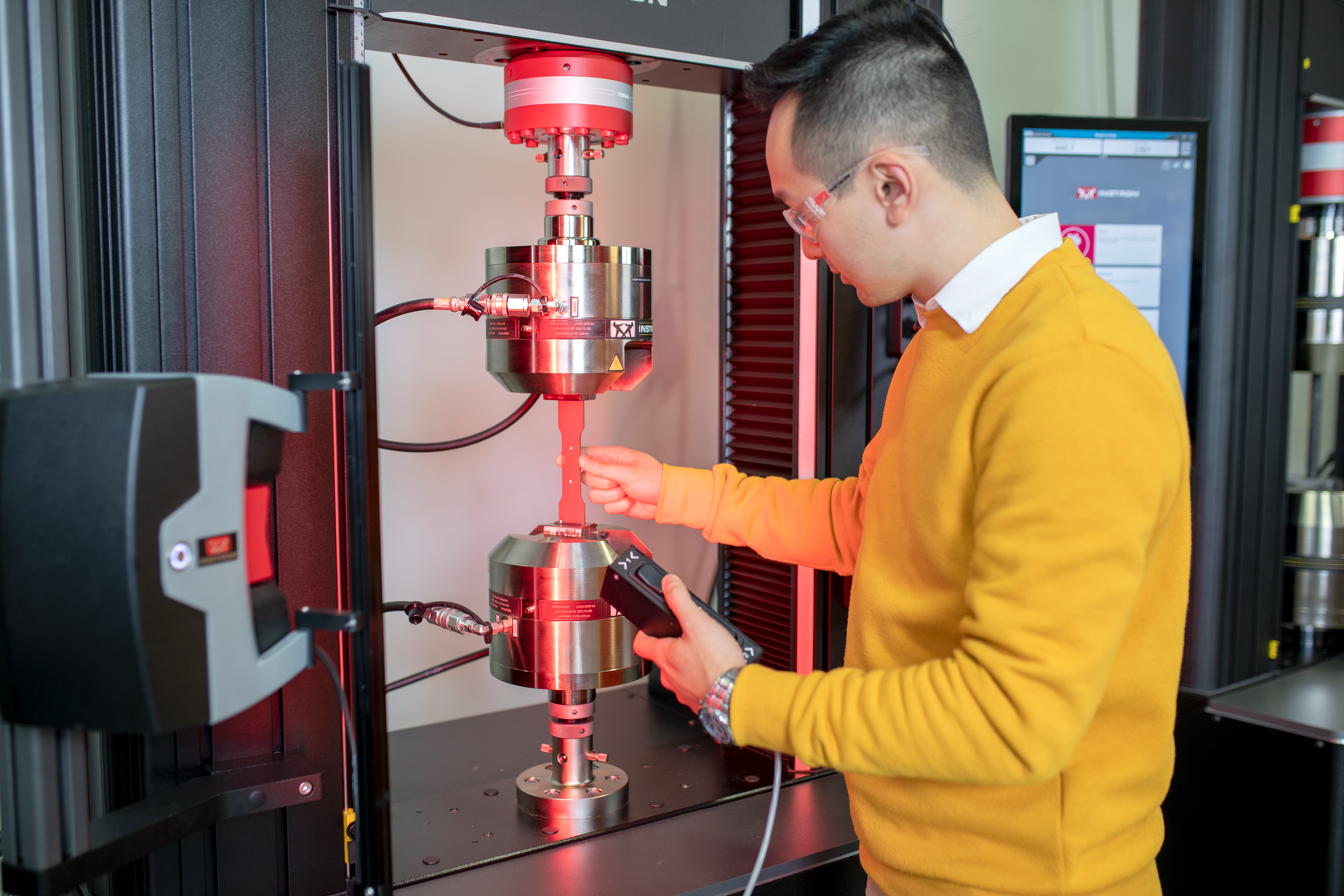
Image Credit: Instron
The advantage of video extensometers extends beyond their resilience to explosive failures. They also eliminate the need for manual attachment by operators, providing a more automated and consistent measurement process. Additionally, video extensometers can meet the accuracy requirements of relevant standards, making them a reliable choice for capturing strain data in composite material testing labs.
What is the role of the testing environment, including temperature and humidity control, and what are some challenges associated with maintaining these conditions during testing?
The testing environment plays a crucial role in composite material testing, particularly in terms of temperature and humidity control, as they can have a significant effect on the mechanical properties of composite materials. Thus, it is imperative to test under controlled conditions to ensure accurate and reliable results.
Maintaining controlled conditions during conditioning and testing presents various challenges. Specimens may need to be conditioned in the appropriate humidity environments, replicating the specific conditions they might face in actual service. This conditioning process must be carried out for an adequate duration of time to ensure that the specimens have reached equilibrium with their environment.
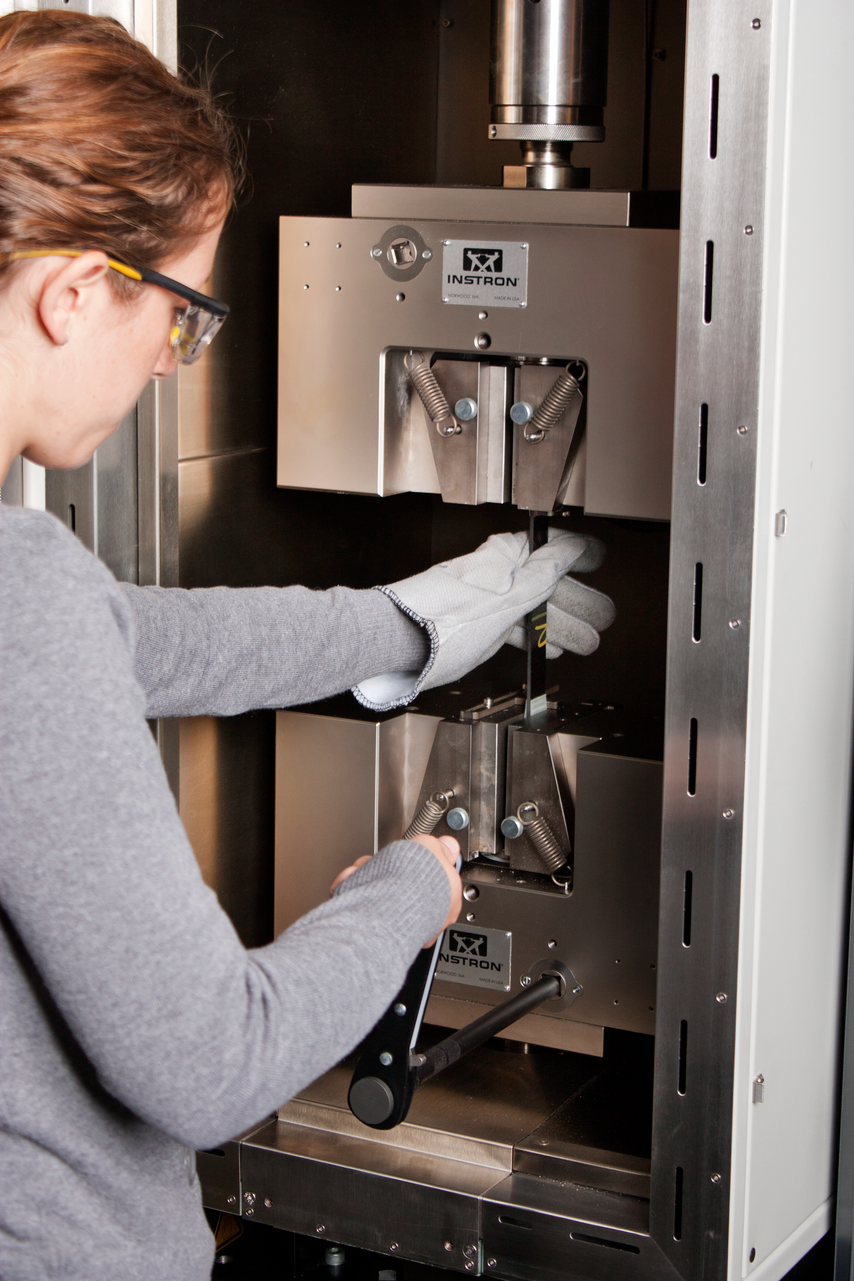
Image Credit: Instron
Temperature control during testing is equally important, and testing chambers equipped with electrical heating elements and/or cooling methods such as liquid nitrogen or CO2 are employed. However, achieving precise and uniform temperature distribution across the specimen can be challenging. Specialized chambers may be necessary for extremely low temperatures.
In the context of testing composite materials, what are the key features that should be prioritized in testing equipment, especially with respect to the precision of alignment and the capabilities of the load cell?
When choosing testing equipment for composite materials, selecting features that suit their unique characteristics is essential. A high level of axial and lateral stiffness in the testing machine is crucial for accurate and dependable results. The machine should also include an alignment fixture to ensure accurate alignment. Optimal grip design is also key, focusing on symmetry, a moving body design, and specimen stops to ensure consistent results. If a temperature chamber is required, then extended grips will be required. Accessories such as compression platens and various fixtures provide versatility in accommodating different testing standards for composite materials.
The choice of load cell is significant. It should offer a broad calibration range, allowing the machine to cover a wide range of test forces while maintaining high accuracy.
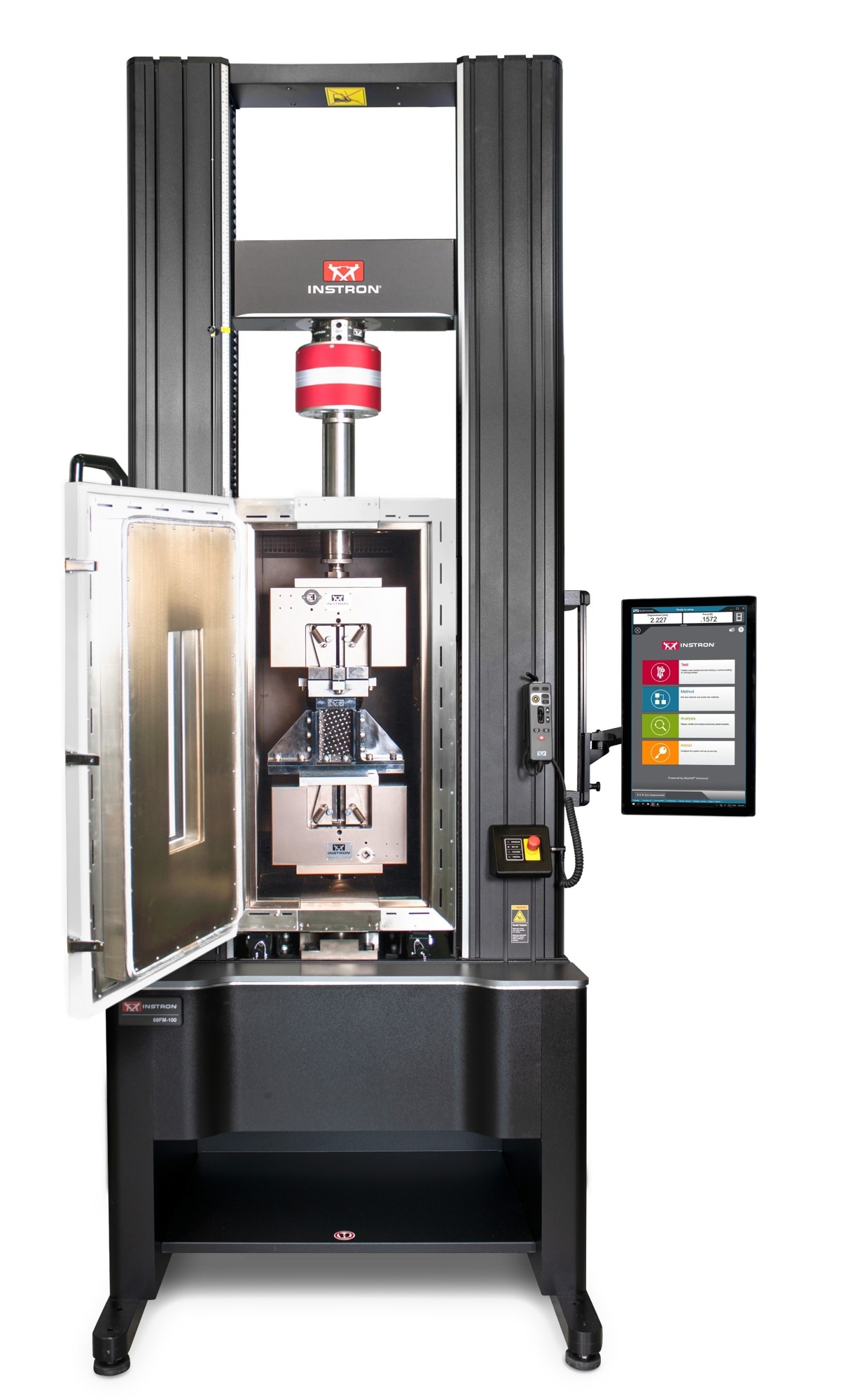
Image Credit: Instron
How does the choice of testing equipment impact productivity in a composite material testing lab? Can you provide examples of equipment configurations that enhance efficiency?
The choice of testing equipment plays a crucial role in determining the productivity of a composite material testing lab. The right equipment not only ensures accurate and reliable results but also contributes to the efficiency of the testing process by minimizing the time involved in switching over between different test types.
Equipment that allows for “piggybacking” additional components can significantly improve efficiency. For instance, compression platens and other test fixtures can be quickly mounted onto fixed grips, enabling a seamless transition between different test types without the need to disassemble the whole setup. This helps maintain alignment, saving time and resources.
The use of a powerful and flexible software system is paramount to enhance efficiency. Instron’s Bluehill® Universal software, for example, includes a composite module with pre-configured testing methods for various standards.
In summary, the choice of testing equipment impacts productivity by influencing factors such as alignment precision, flexibility, and the ability to integrate additional components. Configurations that prioritize these aspects contribute to a more efficient and reliable composite material testing process.
About Stephan Botzki 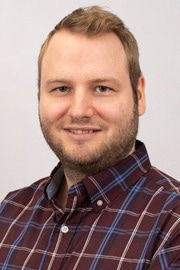
Stephan Botzki brings a strong background in mechanics and data analysis to his role as a Senior Applications Engineer at Instron, where he specializes in static high-force testing for composites and other high-strength materials. He is also an active voting member and serves as recording secretary for the ASTM D30 committee, which is dedicated to composite materials.
About Ian McEnteggart 
Ian McEnteggart is the Manager of the Composites Market at Instron, where he has led the composites division for over 45 years. His extensive experience involves advancing testing standards and supporting the mechanical performance needs of industries that rely on composite materials. Ian is also the Chair of the BSI Committee PRI/042 on fiber-reinforced thermosetting plastics, contributing to the development of national standards for these critical materials. Holding a diploma in Systems Engineering from City University, London, Ian is recognized for his extensive publications and thought leadership in the field of composites testing.
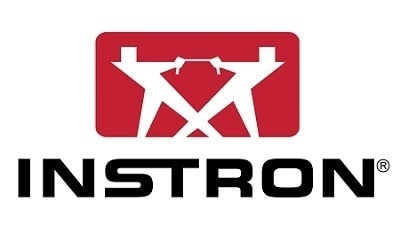
This information has been sourced, reviewed and adapted from materials provided by Instron - USA.
For more information on this source, please visit Instron - USA.
Disclaimer: The views expressed here are those of the interviewee and do not necessarily represent the views of AZoM.com Limited (T/A) AZoNetwork, the owner and operator of this website. This disclaimer forms part of the Terms and Conditions of use of this website.