Sponsored by Specac LtdReviewed by Maria OsipovaJul 2 2024
Specac has consistently pioneered innovative spectroscopic solutions to facilitate reliable quantitative measurements for its clients. The company's engagement with Process Analytical Technology (PAT) commenced in the 1990s and has since evolved into a steadfast commitment.
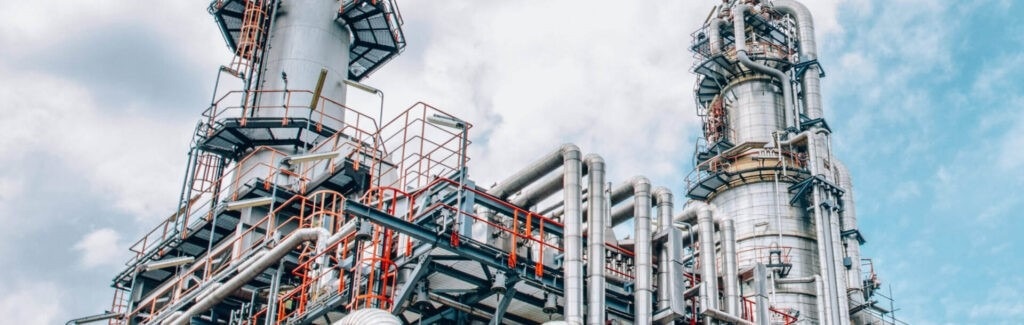
Image Credit: Specac Ltd
NIR Process Cells: A Primer
NIR process cells represent the critical interface between a chemical process stream and dedicated process measurement systems. The demands imposed on these cells are multifaceted, arising from the chemical dynamics within the process stream and the external environmental conditions. Given the potential hazards, the means for safe installation and servicing are deemed as crucial as the in-service requisites.
Concurrently, process cells are responsible for enabling the transmission of ultraviolet, visible, or near-infrared light to delve into the chemical composition of materials within the cell. This necessitates robust optics, precision fitment, and enduring physical stability throughout the cell's lifespan.
Advantages of On-line NIR Process Analysis
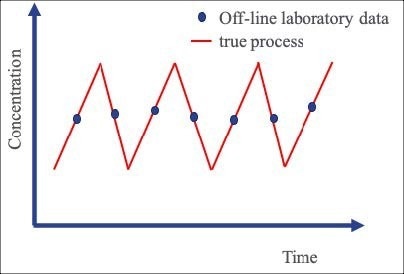
Image Credit: Specac Ltd
Online NIR process analysis, which entails the direct spectroscopic monitoring of chemical composition in fluids or vapors within a chemical process plant, has several merits:
Discovery of Process Instabilities: Identifies instabilities that may elude detection through offline methods.
Enhanced Process Precision: Facilitates running the process closer to specification limits for an extended duration.
Eliminating Hazardous Offline Sampling: Substitutes hazardous and time-consuming offline sampling with continuous in-line sampling.
Process flow cells emerge as pivotal components in realizing online process analytical systems, establishing direct contact with the chemical process itself.
Stages in Specifying On-line NIR Spectroscopy
The initiation of a new online NIR spectroscopy installation involves sequential stages:
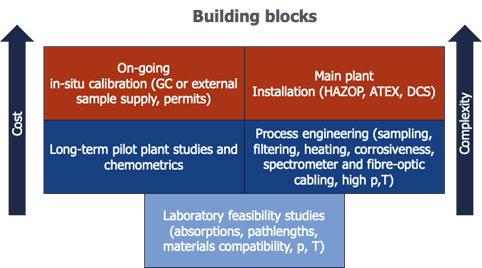
Image Credit: Specac Ltd
Feasibility Studies: Preliminary investigations determine the suitability of the chosen process for online NIR analysis.
Pilot Plant Construction: A pilot plant is constructed for isolated system testing, enabling performance data collection compared to the regular process.
Full-scale Implementation: If the tests prove successful, full-scale implementation within the main plant is greenlit.
The requisites for process cells vary at each stage of this delineated process. Early-stage studies would use cells with more adjustment in path length that also have a lower cost; in later stages, the means of integrating the cell with the final production-scale process streams need to be specified, and the designs can become more bespoke.
Functionality of Integrated Process Flow Cells
Integrated process flow cells operate through the transmission of light via an optical fiber cable from the spectrometer source to one port of the process flow cell. Collimation optics guide this light through a specified path length of the process stream to a second set of optics, refocusing the beam onto a return optical fiber cable attached to the second port of the process flow cell.
The return optical fiber cable facilitates the transmission of the light beam back to the spectrophotometer detector. Typically integrated into the process circuit, process flow cells can be directly in the process stream or within a 'by-pass loop,' allowing isolation for routine cleaning, servicing, or calibration when configured in the latter manner.
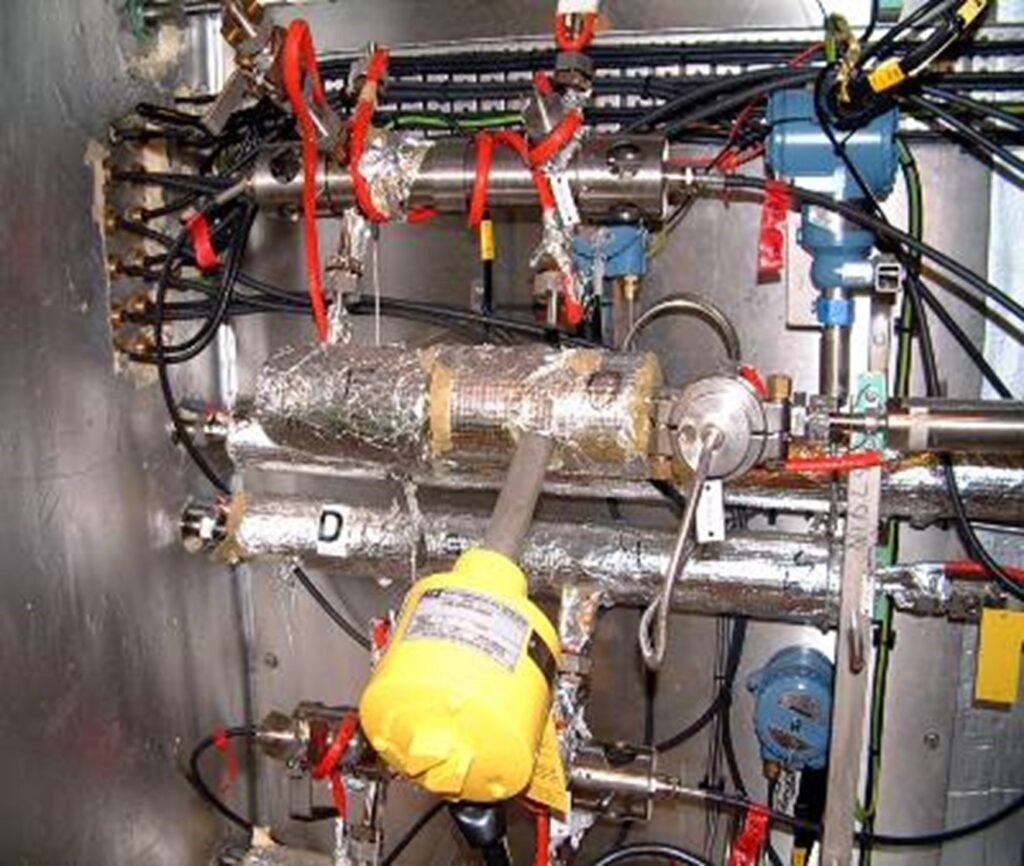
Installation configuration of a Specac Typhoon gas-phase process cell at the top of an image on a chemical plant. Image Credit: Specac Ltd
The flexibility of NIR systems lies in the ability to multiplex between different cells located at considerable distances from one another. These cells can analyze diverse process streams with varying compositions and physical states, including gas and liquid cells, within one spectrometer.
Design Considerations for Process Flow Cells
The design of a new process cell hinges upon crucial information about the chemical process it will encounter. Factors such as temperature, pressure, material properties (solid, liquid, powder, gas, particulate, etc.), and chemical compatibility with potential cell materials must be discerned before initiating the design process.
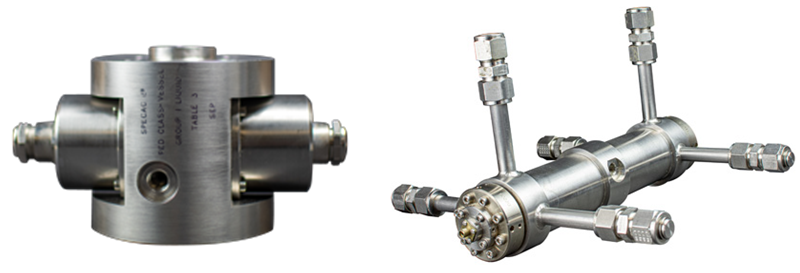
Image Credit: Specac Ltd
After specifying process parameters and selecting a suitable solution, the next consideration is the cell's installation. This can involve a direct in-line installation with the main process pipework or a "double block and bleed" arrangement on a bypass loop.
Fiber Optics for Process Flow Cell Integration
Specac process flow cells are compatible with a range of optical fiber cables, featuring core sizes of up to 600 microns in diameter. Users should select cables appropriate for the application, such as water-free optical fibers for NIR applications or UV-grade optical fibers for enhanced UV transmission.
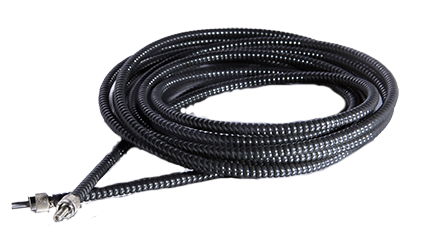
Image Credit: Specac Ltd
Optical fibers must be appropriately coated for the temperature at the connection point to the process flow cell. Polymide-coated or metal-coated fibers are recommended for higher-temperature applications. Specac adheres to industry standards, utilizing the widely available SMA 905 style of fiber connector for interfacing optical fibers with the process flow cell.
For inquiries and further information, interested parties are encouraged to engage with Specac, leveraging their state-of-the-art design tools and over 25 years of process application experience. Specac's range of process flow cells boasts a proven reliability and robustness track record, ensuring prolonged operation in demanding industrial environments.
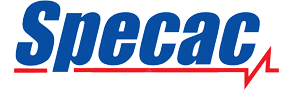
This information has been sourced, reviewed and adapted from materials provided by Specac Ltd.
For more information on this source, please visit Specac Ltd.