There are two primary application techniques for applying reactive adhesives: bead/dot application and slot or roller coating. The application technique is typically chosen according to the shape and size of the bonded areas as well as the geometry of the part.
When selecting an adhesive application method, several criteria should be considered:
- Type of adhesive
- Size of the parts to be bonded
- Time required for adhesive application
- Cycle time: the number of parts to be bonded per hour/day
- Indoor/outdoor application requirements
- Viscosity of the adhesive to be applied
- Level of investment required
Source: Huntsman Advanced Materials
|
Bead / Dot Coating |
Slot / Roller Coating |
Targeted application |
✓ |
✘ |
Large surface application |
✘ |
✓ |
Complex part geometry |
✓ |
✘ |
Manual application |
✓ |
✘ |
Robotic application |
✓ |
✘ |
Continuous line application |
✓ |
✓ |
Control of bond line thickness |
✘ |
✓ |
Visible bond lines / deformation |
✘ |
✓ |
Fast-cure adhesives |
✓ |
✘ |
Use of gap-filling adhesive for uneven parts |
✓ |
✘ |
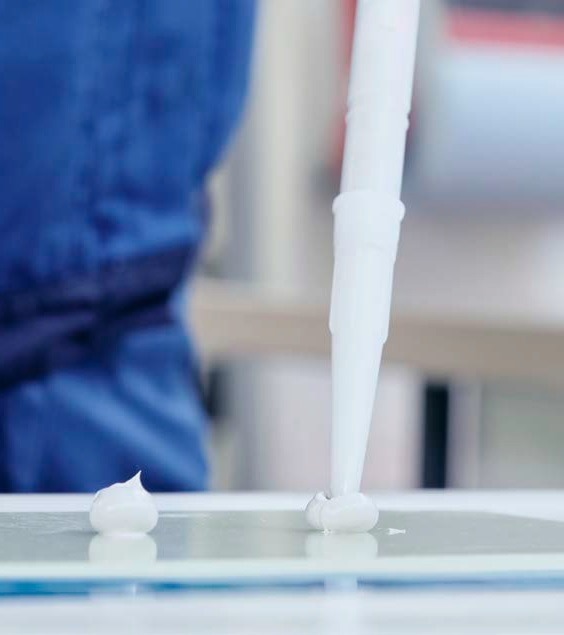
Image Credit: Huntsman Advanced Materials
Beads and Dots for Targeted Applications
Learning Lab: Choose the Right Adhesive Application Method
How to achieve a good beads and dots application. Video Credit: Huntsman Advanced Materials
Beads and dots of adhesive can be applied as single or multiple rows, either manually from a cartridge or using automated dispensing equipment. This method is highly versatile and suitable for a wide range of adhesive types, from low viscosity products to highly viscous or thixotropic pastes.
This method is ideal for applying adhesives to specific areas of parts and for three-dimensional forms. Robotic applications can be integrated with automated mixing/dispensing equipment to ensure consistent application, even on complex forms.
For most applications, the adhesive can be dispensed directly from a disposable static mixer, eliminating the need for equipment cleaning between applications. Only the disposable mixer needs to be changed. This method enables the use of fast-cure adhesives.
Clamping pressure is typically applied to the bonded parts during assembly to distribute the adhesive evenly across the bonded area. However, this process can result in unevenness in the bond line or the entrapment of air. For thin or flexible bonded substrates, this can lead to an uneven surface or the formation of "witness lines," which may be visible on the exterior of the bonded parts.
Advantages
- Targeted application on complex forms possible
- Minimal waste
- Simple and quick cleaning of application equipment
- No need for solvent flushing
- Equipment can be very mobile
- Suited to robotic application
Disadvantages
- Achieving precise control of adhesive thickness can be challenging
- The bead application pattern may be visible through thin substrates
- It relies on even pressure to effectively spread the adhesive
- It can be a slow application method, particularly for large, flat surfaces
Roller Coating for Larger Surfaces
Typically used with low- to medium-viscosity products, a film of adhesive is applied to a substrate using either a slot applicator or a roller coater. While small manual roller coaters are available, this method often employs automated lines with an integrated coater. Such applicators may also be connected to automated mixing-dispensing equipment. The installation is generally stationary (not portable) and requires regular flushing and cleaning with solvents, typically at the end of a shift.
Adhesives with relatively long working times (slow-cure) are typically suitable for this type of equipment. It enables very even adhesive application with precise control of bond line thickness on flat substrates. This makes it particularly suitable for bonding large, flat panels.
Advantages
- Accurate control of adhesive thickness
- Quick application on large, flat surfaces
- Even bond line
Disadvantages
- Suitable only for slow-cure adhesive systems
- Cleaning equipment is crucial - generally, solvent flushing/cleaning is required
- Equipment is usually not mobile
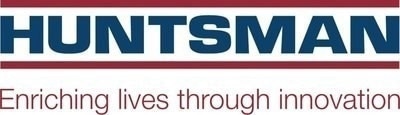
This information has been sourced, reviewed and adapted from materials provided by Huntsman Advanced Materials.
For more information on this source, please visit Huntsman Advanced Materials.