VIBRAPLANE Airmount Isolation
Traditional isolators are fabricated using metal springs or rubber blocks. They have low internal damping and only tend to be effective at frequencies in the region of 10 Hz. They also fail to isolate at frequencies above 30 Hz due to the “harmonic standing waves” at sonic velocities in the metal or rubber.
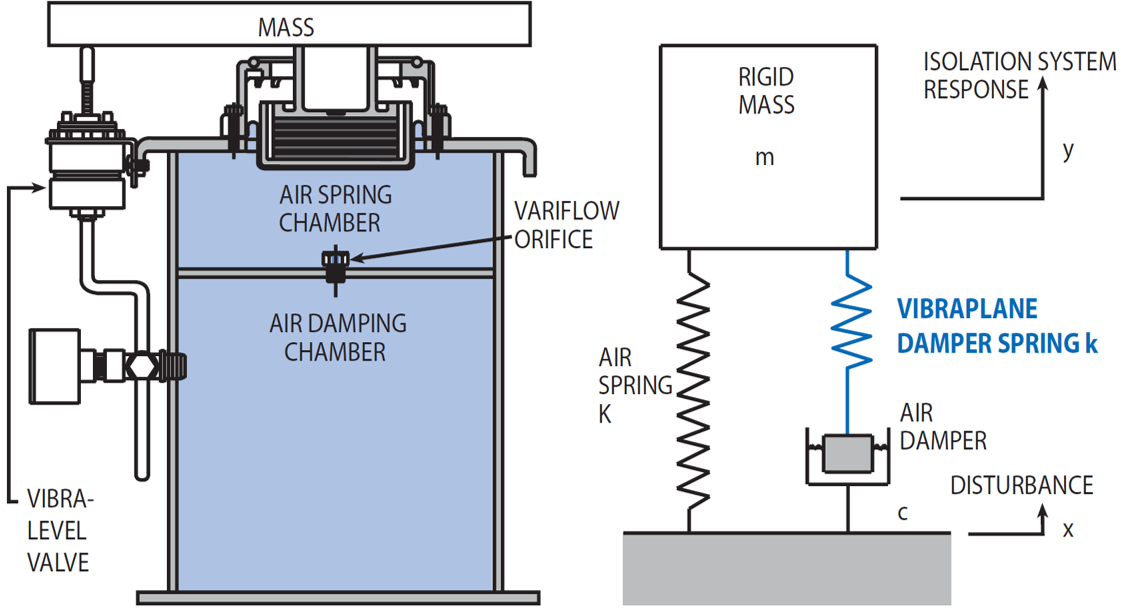
Figure 43.1. VIBRAPLANE Airmount. Image Credit: Kinetic Systems, Inc
The VIBRAPLANE design concept in Figure 43.1 eliminates the metal springs or rubber blocks used in traditional isolator designs. The VIBRAPLANE supports a load-carrying piston using a frictionless rolling diaphragm air seal in combination with dual air chambers, all of which form the spring and damping medium.
The combined air volume of the dual chambers is what gives the air spring its stiffness. This ensures the extremely low stiffness necessary to achieve the desired extremely low natural frequency needed for high-efficiency isolation. The VIBRAPLANE System prevents “Harmonic standing waves” due to its internal damping dual air chamber design.
VIBRAPLANE Systems are Mobile
Since current and prospective building vibration requirements are subject to change, the safest, most cost-effective method of vibration control in facilities utilizing sensitive technologies is making sure the equipment is isolated from vibrations at the point of installation.
For OEM and end-user installations, high-performance VIBRAPLANE systems offer vibration control that is not contingent on the building’s construction.
VIBRAPLANE isolation systems are comparatively compact and mobile, as opposed to fixed support piers or concrete inertia blocks, and can be switched out as future needs dictate. The alternative, modifying buildings and internal structures, is expensive and usually permanent with little or no leeway for future needs.
KSI has conducted vibration surveys which indicate that the majority of buildings have complex vibration control systems and may be determined using a broadband random vibration spectrum with a number of superimposed strong discrete “tonal” frequencies.
The broadband random vibration spectrum runs from 8 to 200 Hz. The multiple discrete tonal frequencies can typically be seen between 8 to 80 Hz and are attributable to motors, generators, pulleys, blowers, gears, etc.
The vibrations observed tend to be vertical, with horizontal vibrations averaging at about 25% to 30%. The frequency spectrum is, in effect, invariant. However, discrete frequency amplitudes can fluctuate vastly depending on the location and distance from where the disturbance originates.
Irrespective of location, an 8 to 200 Hz frequency spectrum of concern is determined from the generalizations to select appropriate vibration control to mitigate any damaging environmental frequencies which may have an impact on the equipments natural frequencies. KSI’s standard VIBRAPLANE vibration isolation systems have been deveoped with a low 1 to 2 Hz natural frequency that will reduce all potentially damaging vibration amplitudes in the 8 to 200 Hz frequency spectrum.
Better Damping
The VIBRAPLANE leverages KSI’s innovative proprietary VARIFLO™ orifice design to control the flow between air chambers. Therefore, improved damping control is achieved at both high and low amplitudes and frequencies. This concept ensures an evenly distributed air flow across all amplitudes without choking, preserving the efficiency of both (airspring) chamber volumes.
As shown in the schematic representation displayed in Figure 43.1, VARIFLO damping incorporates a “filtering” spring. This differs from vibrations from the standard isolator model of Figure 42.1, where the damper is directly paired with the mass and leads to a loss of isolation at high frequencies as demonstrated in Figure 42.2.
The VARIFLO damping (air) spring in effect decouples the damper at high frequencies, meaning there is no loss of isolating properties where high damping forces would typically reduce efficiency in a traditional isolator assembly.
Zero Friction
The VIBRAPLANE concept leverages a frictionless thin wall rolling diaphragm to support the (airspring) piston. This novel design stops friction locking from occuring, which is a primary cause of loss of isolation for low frequency, micro-inch disturbances in conventional isolators.
VIBRAPLANE Transmissibility
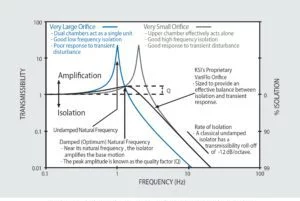
Figure 45.1. VIBRAPLANE Transmissibility. Image Credit: Kinetic Systems, Inc
The VIBRAPLANE’s dual chamber design enables optimization of the vibration Transmissibility performance as shown in Figure 45.1. The air volume performs effectively at low frequencies in both air chambers, this results in a large air volume and a soft low natural frequency system.
This is determined by the “left” branch of the Transmissibility curve in the diagram. At high frequencies, the orifice progressively chokes the air flow, which means, in time, only the small chamber is able to effectively stiffen the system.
This action is shown in the “right” branch of the Transmissibility curve. KSI’s proprietary orifice design is amplitude sensitive and modeled to produce the “optimum” transmissibility between the left and right branches.
VIBRAPLANE facilitates optimal conditions when it comes to damping at resonance as well as enabling minimum damping at high frequencies for improved isolation that outperforms conventional isolation systems.
Active-Air Leveling
VIBRAPLANE Active-Air leveling delivers leveling compensation and an extensive load range. By leveraging a compressed air source and KSI’s proprietary VIBRALEVEL Air Servo Valves, users are able to feed into the airsprings as well as being able to also bleed the air out. This maintains a preset “zero deflection” level and compensates for any changes in the load.
Horizontal Vibration Control
While vertical vibrations are the most prominent, horizontal vibrations in buildings still average 25% to 30%. The VIBRAPLANE System has the Kinematic Horizontal Isolation Piston built-in, which ensures isolation in any vibration environment irrespective of direction.
The piston part of the inner-framework includes inbuilt rubber-in-shear elements that translate and rock simultaneously in a low-frequency coupled response action to respond to horizontal vibration. KSI BaseMate Platforms utilizes an omni-directional low-frequency pendulum system to cancel out any horizontal vibrations.
Early on, KSI was able to determine that precise system leveling is vital when trying to achieve sufficient horizontal vibration isolation, and it was the first company to introduce mechanical leveling feet on all of its workstations. This supports the maximum efficiencies of the systems zero friction design concept as the leveling feet are able to equalize piston extension and mitigate any rubbing friction due to frame tilt.
Structural Damping
Kinetic Systems structural damping system eliminates the “ringing” generated by resonances in frame, table, and platform structures external to the VIBRAPLANE airspring suspension system. All structures are subjected to resonance regardless of how stiff or massive.
Damping modifications are the most effective means to dissipate vibration energy. KSI’s engineering staff is engaged in the ongoing research and development of new, advanced damping technologies which can be incorporated during the production of all VIBRAPLANE systems.
KSI uses viscoelastic damping laminations and “tuned absorbers” on all composite, solid, and honeycomb tables and platforms. Additionally, frame structures are bolted through the viscoelastic laminations.
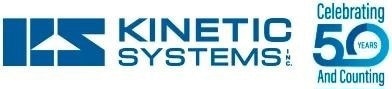
This information has been sourced, reviewed and adapted from materials provided by Kinetic Systems, Inc.
For more information on this source, please visit Kinetic Systems, Inc.