Kinetic Systems' active-air vibration isolation platforms ensure optimal performance of sensitive equipment in real-world conditions, effectively mitigating over 99% of the most common floor vibration problems.
When is Vibration Control Necessary?
- KSI recommends and can offer onsite vibration surveys to determine the environmental information in buildings or facilities. If results indicate vibration amplitudes at frequencies above the equipment specification criteria, isolation is required.
- If new equipment is installed in an active facility where other equipment performs well with vibration isolation, isolation should be maintained and applied to the latest equipment. Sticking with a known practice that performs well rather than experimenting with a new, unknown situation is considered more cost- and time-effective.
- No isolation can be continued if new equipment is installed in an active facility where existing equipment is not isolated. However, new equipment designs may be more sensitive if they have been developed with precision in mind. Therefore, it is advised that isolation offers a suitable safeguarding solution, especially if time and precision is a key factor for going online.
How Much Vibration is Acceptable?
Look at the Application
Due to the diverse nature of instrument components, designs, and applications, equipment sensitivity to vibration will depend on the specific device, the operating environment, and the needs of the individual researcher. “How much vibration is acceptable” cannot be easily determined.
When developing equipment, manufacturers are usually focused on achieving specified performance limits in a benign or non-critical development laboratory environment. This means the end user’s responsible for ensuring a “safe operating vibration environment” at the point of installation.
The data on the capabilities of various equipment classes to withstand vibration is relatively limited. The data that has been compiled comes from various surveys, as displayed in Figure 6.1, and represents suggested safe operational vibration levels for a range of sensitive instruments.
Each equipment line constitutes an envelope of rms vibration amplitude vs frequency within acceptable limits which may not be exceeded. The “allowable” vibration envelopes displayed in Figure 6.1 have been drawn up by several engineering committees for standardization by the International Standards Organizations (ISO) to complement their existing standards.
Kinetic Systems Takes the Guesswork Out of Vibration Control
Kinetic Systems, Inc. is a global innovator in the development and application of state-of-the-art vibration control systems that help create vibration-free work environments for sensitive equipment.
An overview of KSI’s expertise and practical vibration control methods are presented here to assist the selection decisions and outline cost-effective vibration isolation solutions for different applications.
Vibration Control at “Point of Installation”
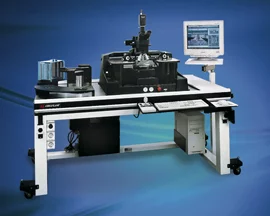
Image Credit: Kinetic Systems, Inc
For end-user applications, KSI produces extensive lines of active-air and passive-air mounts, platforms and tables, with load capacities ranging from 200 lb to 20,000 lb per unit isolator.
Available as standard or customized solutions, design table and platform configurations are at hand for research applications involving complex assemblies of elements that are by nature sensitive to vibration, such as microscopes, mask aligners, probers, etc.
Vibration Control at “Point of Design”
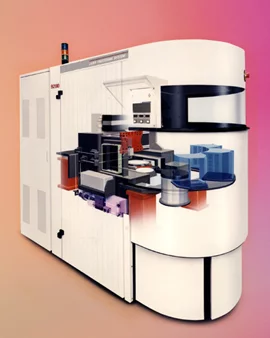
Image Credit: Kinetic Systems, Inc
For OEM applications, KSI produces unit active-air vibration isolators that can be easily incorporated into existing equipment assemblies to safeguard platforms and trays supporting vibration-sensitive elements.
This cost-efficient and space-saving approach allows process equipment manufacturers to achieve sufficient vibration control. KSI can offer a customized external isolation table or platform to provide the desired vibration environment protection when installing an integrated internal isolation system due to the fixed equipment design.
With over 30 years of applied vibration control experience, KSI has carried out all the necessary calculations to offer the end-user point of installation pre-engineered, low-frequency, all-purpose, vibration-free tables, and platforms for tabletop and freestanding equipment.
For the OEM, KSI supplies unit active air mounts in dimensions compatible with custom integration with internal system components and structures.
Crucially, unless the work environment is particularly vulnerable to dramatic vibration fluctuations, KSI Vibration Isolation Systems and Optical Tables will offer near-flawless performance. Full details of the systems are available via the technical section of the KSI website.
However, if an application is time-sensitive and demands high-performance vibration isolation equipment or optical tables, go directly to the product section, choose a workstation, and contact KSI directly. After just a few very simple questions, KSI can offer a hassle-free solution that will work for your application.
All Buildings Vibrate
All buildings are prone to vibration from the movement of people to the activities of machinery, heating, and ventilation systems, as well as nearby truck or rail traffic. These vibrations may be of little concern to the occupants, however, certain pieces of research equipment cannot tolerate even minor vibrational disturbances especially when precision manufacturing, inspection, and quality control are key factors.
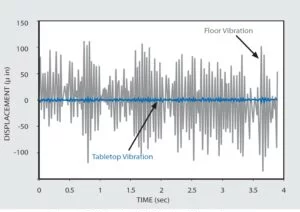
Figure 5.1. Typical Building Vibration and VIBRAPLANE Performance. Image Credit: Kinetic Systems, Inc
Ambient vibration levels in buildings, laboratories, and cleanrooms can vary considerably. Figure 5.1 displays a standard time sample of a building subject to a heavy vibration environment.
The vibration is displayed as a random amplitude and random frequency disturbance. In such an environment, sensitive electromechanical equipment will experience several issues, such as excessive signal noise and potential structural damage.
Optical equipment will be subjected to low-frequency jitter and high-frequency image blur and line thickening. In the short term, this leads to inconsistent and unreliable performance. However, the long-term effects include excessive wear which means increased maintenance and possible fatigue failures.
To ensure sensitive instruments and equipment are protected from faults and operational failure, exposure to vibration must be reduced significantly. This can be easily achieved by using a KSI VIBRAPLANE ISOLATION system, which can be fitted by the end user at the point of installation or incorporated earlier by OEM designers when the vibration-sensitive components are installed.
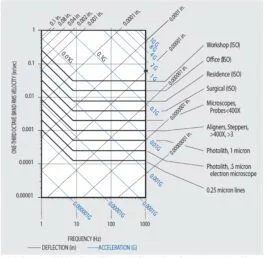
Figure 6.1. Safe Operating Environments for Various Classes of Equipment. Image Credit: Kinetic Systems, Inc
As shown in Figure 6.1, a four-coordinate vibration nomograph has been superimposed. The nomograph’s inclined coordinates facilitate convenient direct reading of rms vibration amplitude as a function of frequency in units deflection, in., velocity, in./sec, or acceleration, G in multiples of gravity, g.
The data should be cautiously approached as they represent subjective opinions related to the onset of operational problems, including signal noise or optical blurring. The data is not representative of structural damage or failure. Furthermore, adjustment is necessary when comparing data with different measurement bandwidths as the data are rms 1/3 octave band width (23%) filter analyses.
It should be noted, that for “Point of Design” vibration control, equipment designers should pay attention to mass, stiffness, and damping. For optimal results, KSI recommends that moving components should be lightweight, rigid, and damped. By the same token, stationary parts should be heavy, rigid, and damped.
It is recommended that sensitive elements are placed together on a rigid platform within the equipment console for grouped isolation. KSI can provide customized vibration protection for all the sensitive components whatever your design needs.
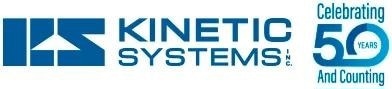
This information has been sourced, reviewed and adapted from materials provided by Kinetic Systems, Inc.
For more information on this source, please visit Kinetic Systems, Inc.