Public knowledge of ocean pollution has become a driving force in ensuring a greener approach to transporting goods by sea.
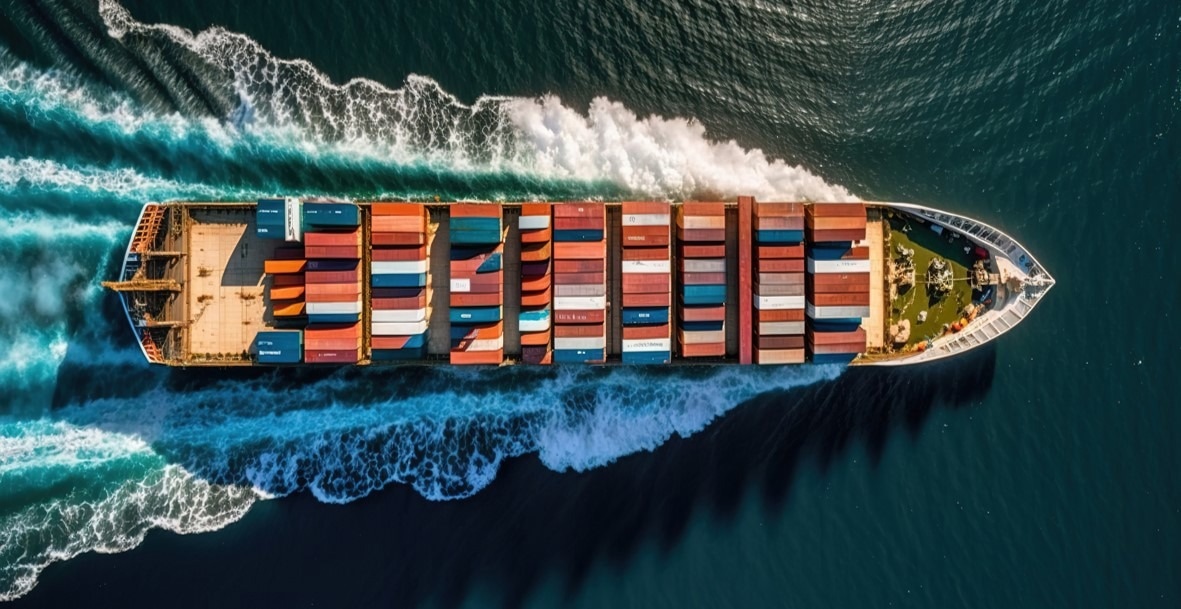
Image Credit: ABB Measurement & Analytics
Approximately 80 percent of world trade is transported by shipping. Although air cargo moves more than US $6 trillion in products every year (Source: IATA), shipping provides the most efficient method to transport bulk goods, including cereals, mineral ores, fuels, cereals, and an extensive selection of products for consumers and manufacturers.
The International Maritime Organization (IMO) has initiated strict emission levels for Sulphur Oxide (SOx) and Nitrogen Oxide (NOx) to address the issue of shipping pollution. The Tier III standard for vessels with keels laid starting January 1, 2016, requires pollutant levels for marine engines to be less than 3.4 g/kW-hr.
The levels are currently applied to the North American Emission Controlled Area (ECA) and were established in the North and Baltic Seas for ships with keels laid starting January 1, 2021. Companies that sell marine two-stroke are responding to the customer’s need to simply and effectively meet these standards.
Finding Improvements Through Measurement
Ensuring its engines meet the required emissions standards, the world’s largest manufacturer of marine diesel engines has chosen the precise ABB AZ10 Zirconia combustion oxygen analyzer.
The strict emissions limitations require the engine manufacturer to confirm the efficiency of the Exhaust Gas Reduction (EGR) system utilized in its two-stroke engines. A percentage of the exhaust is mixed with carbon dioxide (CO2) and fed back to the air inlet. Having an increased temperature capacity than oxygen (O2), CO2 decreases the peak engine temperature, reducing the formation of NOx.
Experiments were completed by the marine diesel engine manufacturer revealing that when the exhaust air was mixed with the inlet air it reduced the oxygen inlet amount by 3-6% percent, instead of natural air’s 21 percent, reducing NOx production by 85 percent.
Reducing emissions by the maximum amount requires the oxygen intake to be accurately measured. In addition, the equipment requires a low response time; and the company needed a solution that reduced the use of expensive gases for calibration.
Comparing devices provided by the major vendors, the ABB AZ10 achieved an accuracy greater than ±0.05 percent of the actual O2 level.
The ABB AZ10 utilization of low-drift sensor technology produces a drift of only 1.0 percent O2 per month. In comparison, other vendors produced a drift of 2 percent O2 per month.
Savings on Cost and Calibration
An additional advantage is the calibration of the AZ10 uses air instead of costly calibration gases. ABB supplies a calibration certificate for every cell eliminating the need for the user to complete the calibrations. The optional auto-calibration unit can perform manual or automatic calibrations.
Another important feature is the on-board “Fuel Gauge.” This lifetime monitor provides an early warning of the unit’s operational effectiveness that allows the user to schedule repairs or replace the cell.
The AZ10 is simple and quick to repair on-site with basic tools. It has an easy cell release and site-serviceable probe that replaces the ABB sensor in a few minutes.
The ABB AZ10 has marine certification IACS E10 Rev. 5.0 2006 Test Specification for type approval and ABS certificate 15-LD1262098-PDA.
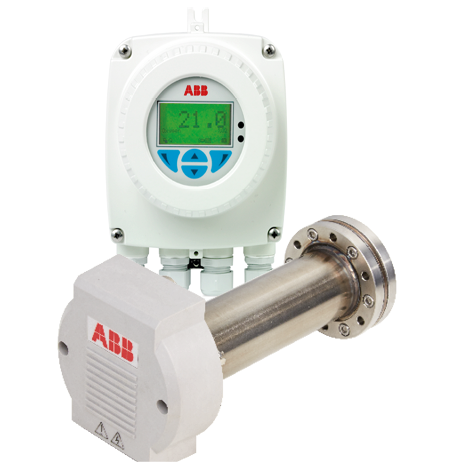
Image Credit: ABB Measurement & Analytics
Making the Seas Greener Through Measurement
To find out how ABB’s measuring equipment can assist the marine industry in reducing pollution and maximizing efficiency, visit ABB’s dedicated portal page.
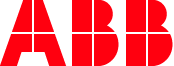
This information has been sourced, reviewed and adapted from materials provided by ABB Measurement & Analytics.
For more information on this source, please visit ABB Measurement & Analytics.