Driven by the growth in the electric vehicle market, battery manufacturing has seen an unprecedented surge in recent years, and it is likely to continue over the next decade.
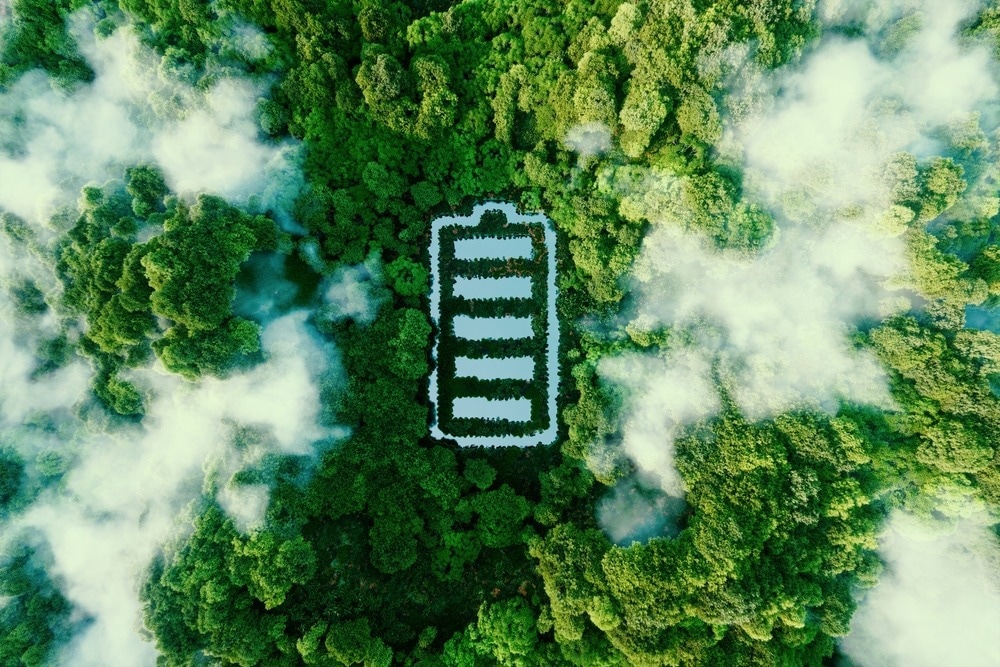
Image Credit: petrmalinak/Shutterstock.com
As the price of battery packs continues to fall, manufacturers are forced to innovate during the production process to minimize waste and maintain consistent quality.
The same can be said of battery recycling, which must remain profitable despite the volatile and fluctuating prices of key minerals, such as lithium (Li) and nickel (Ni). Automation of certain processes and analytical solutions that enable Industry 4.0 smart factory process flow can significantly contribute.
Malvern Panalytical can provide a range of online solutions that cover the entire battery manufacturing value chain, including:
- Elemental composition analysis of black mass for recycling
- Elemental composition analysis of electrode coatings
- Elemental composition analysis of liquid precursor materials during production and recycling
- Orientation index of graphite-coated electrodes
- Particle size analysis in precursor and electrode materials production
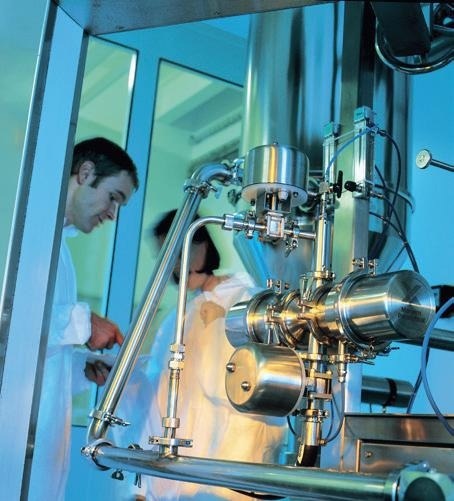
Image Credit: Malvern Panalytical Ltd
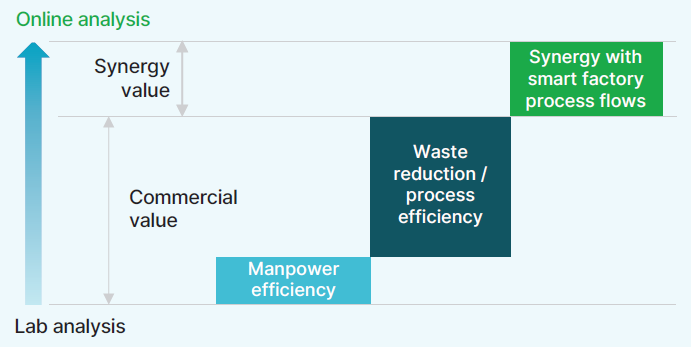
Potential gains with online monitoring in the process control. Image Credit: Malvern Panalytical Ltd
Insitec
Online Particle Size Analyzer for Battery Precursors and Electrode Materials
Insitec Wet: Designed to endure harsh chemical environments, Insitec Wet particle size analyzers leverage laser diffraction technology to measure particles in the 0.1 to 1000 µm size range in emulsions, suspensions, and slurries. The Insitec Wet can be configured for almost any wet particulate process, such as battery recycling. It also delivers automated, real-time results 24/7.
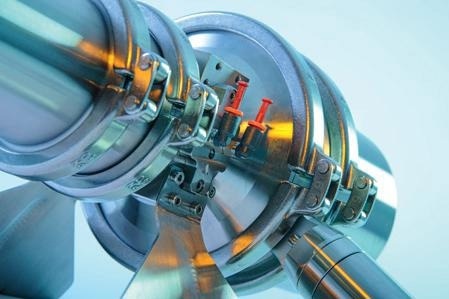
Image Credit: Malvern Panalytical Ltd
Insitec Dry: Designed to endure the rigors of the process environment, Insitec Dry particle size analyzers leverage laser diffraction technology to measure particles in the 0.5 to 2500 µm size range. Insitec Dry can be configured for almost any dry particulate process, providing users with real-time monitoring and control of process optimization and Industry 4.0.
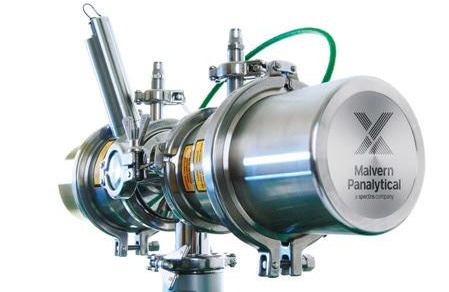
Image Credit: Malvern Panalytical Ltd
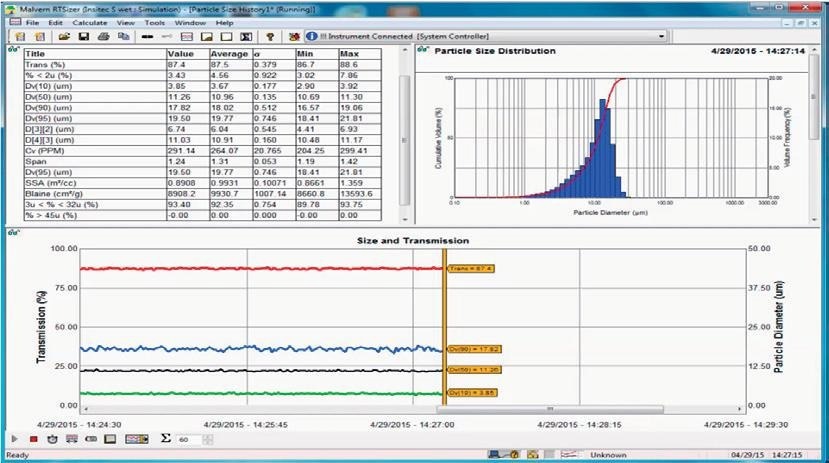
Monitoring trends in particle size with Insitec Wet. Image Credit: Malvern Panalytical Ltd
Online Particle Size Control to Minimize Process Waste
Insitec’s online particle size analysis enables monitoring and ensures control over the following process stages of a standard manufacturing process for NCM cathode material:
- Nucleation and particle growth in the reactor tank to generate NCM hydroxide precursor
- Sieving/grinding of Li precursors (LiOH, LiCO3)
- Control of the classifier mill to ensure the correct particle size distribution of cathode and anode materials is achieved
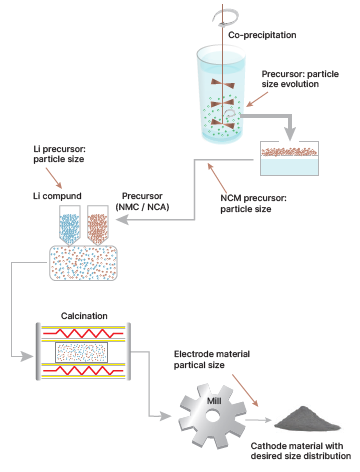
Image Credit: Malvern Panalytical Ltd
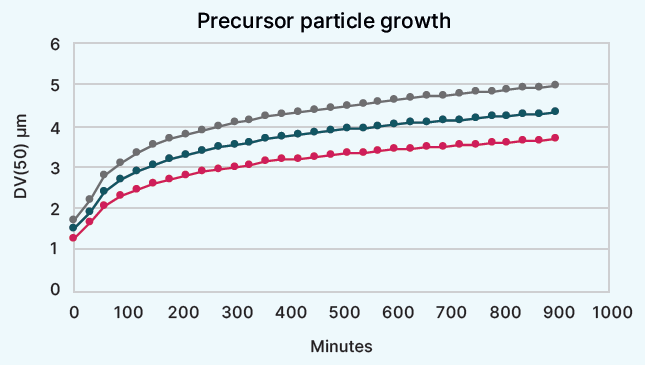
Growth of cathode precursor particles in the reactor tank under different growth conditions, as measured with online laser diffraction over time. Image Credit: Malvern Panalytical Ltd
Epsilon Xflow
Online Elemental Composition Analysis of Liquid Precursors
Cathode active materials are typically manufactured via the co-precipitation method using a solution containing metal sulfates (Ni, Co, and Mn sulfate for NCM-based active material).
The ability to perform online analysis of the elemental composition of the liquid precursor with the Epsilon Xflow facilitates rapid yet accurate control of the chemical composition of starting materials.
More stringent regulations and strict quality specifications are calling for improvements in continuous process flow monitoring throughout the battery industry.
The Epsilon Xflow offers real-time data insights, enabling users to efficiently manage production processes while reducing operational costs.
- Simultaneous multi-element liquid precursor analysis in battery CAM manufacturing and battery recycling
- Real-time results
- Leading EDXRF technology for rapid measurement with high repeatability and accuracy
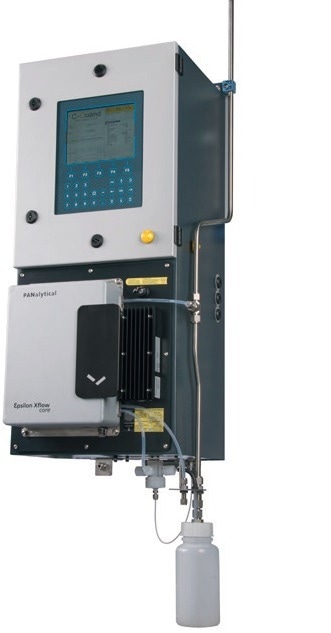
Image Credit: Malvern Panalytical Ltd
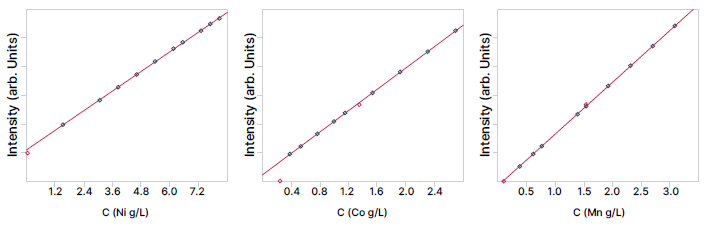
Ni, Co, and Mn calibration on liquid precursor samples using EDXRF. Image Credit: Malvern Panalytical Ltd
Epsilon Xline
In-Line Elemental Composition Analysis of Electrode Coatings
Malvern Panalytical has combined its state-of-the-art Epsilon 4 technology with in-line functionality in a tool that offers real-time material monitoring and process control for both ultrasonic spray coating and roll-to-roll (R2R) coating processes:
- Continuous monitoring of R2R coating processes: Disruptions to the coating process are limited as sampling is eliminated via real-time analyses.
- Precise measurement: A patented robotic arm with a high-speed Silicon Drift Detector offer optimal distance control over the production line for precision measurements at ultra-fast coating speeds.
- Seamless integration into production processes: Epsilon Xline supports conventional communication protocols, streamlining adoption and integration into existing production assemblies.
- Detailed element analysis: The instrument can measure all elements of interest, such as impurities and dopants, down to the parts per million (ppm) level.
- Precision measurement of thin layers: The system utilizes proven software for single and multi-layer webs.
- Versatile use: Well-suited for patch, continuous, or multi-lane coating processes, the Epsilon Xline offers several scanning options to optimize coating homogeneity for a consistent-quality product.
- Wide roll width compatibility: Epsilon Xline can accommodate a diverse range of roll widths, enabling greater flexibility throughout the manufacturing process to meet the increasing product differentiation across the fuel cell industry.
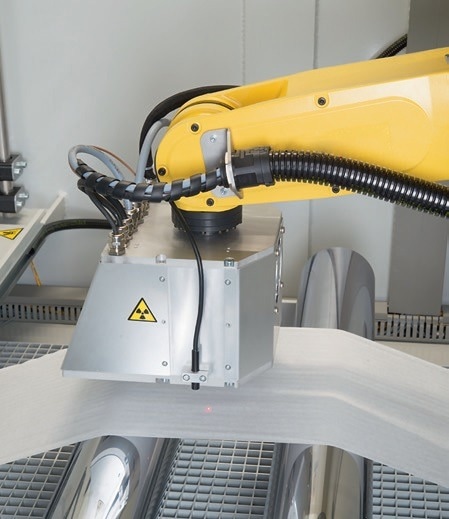
Image Credit: Malvern Panalytical Ltd
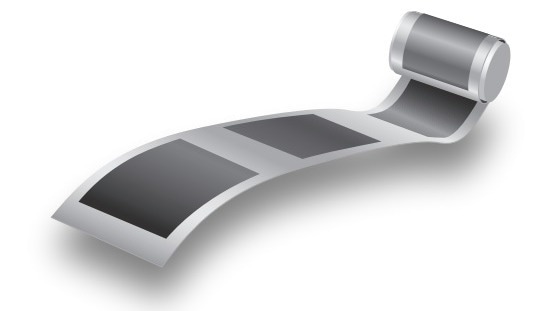
Image Credit: Malvern Panalytical Ltd
Online XRD
Controlling the Orientation Index in Graphite Electrode Coatings
The orientation index is a key parameter in coated graphite layers. The orientation of graphite particles can vary depending on which coating process is applied.
Orientations such as 110 and 100, where the c-axis of the graphite aligns with the plane of the current collector, have a sizable impact on the electronic and ionic conductivity in contrast to the 001 orientation, where the c-axis is out-of-plane to the current collector.
Online XRD makes real-time monitoring of the orientation index possible.
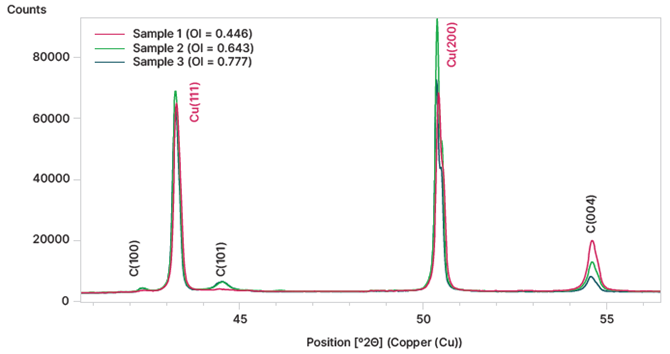
Typical orientation index measurement using XRD. Image Credit: Malvern Panalytical Ltd
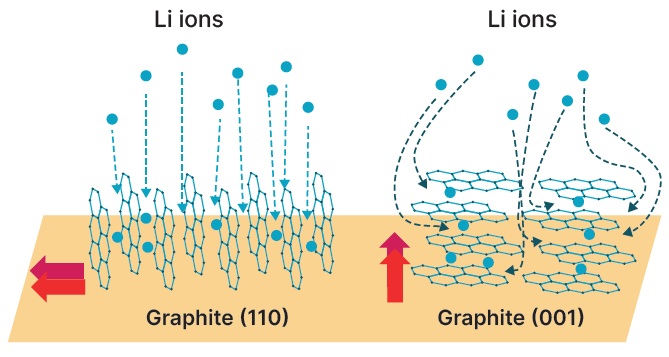
Schematics of Li intercalation pathways for graphite 110 and 001 orientations. Red arrows show the direction of the c-axis. Graphite has poor ionic and electronic conductivity along the c-axis. Image Credit: Malvern Panalytical Ltd
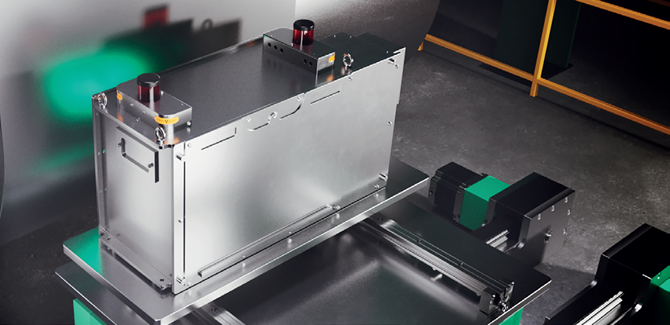
Image Credit: Malvern Panalytical Ltd
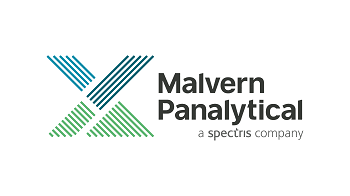
This information has been sourced, reviewed and adapted from materials provided by Malvern Panalytical Ltd.
For more information on this source, please visit Malvern Panalytical Ltd.