In the field of naval aviation, safeguarding the integrity of aircraft is paramount to ensuring the operational safety and capability of a fleet. A perpetual concern in this regard is corrosion, which demands vigilant preventative measures and timely intervention.
A recent audit by the Department of Defense Inspector General revealed that, between 1989 and 2020, corrosion-related issues led to at least 14 technical directives within the Navy’s F/A-18C-G community. While this number may sound small, corrosion damage to naval aircraft is a primary financial burden in maintaining the operational readiness of their carrier air wing. Moreover, between 2017 and 2020, corrosion remediation efforts by squadron maintainers on F/A-18C-G aircraft single-handedly exceeded $2 billion.1,2
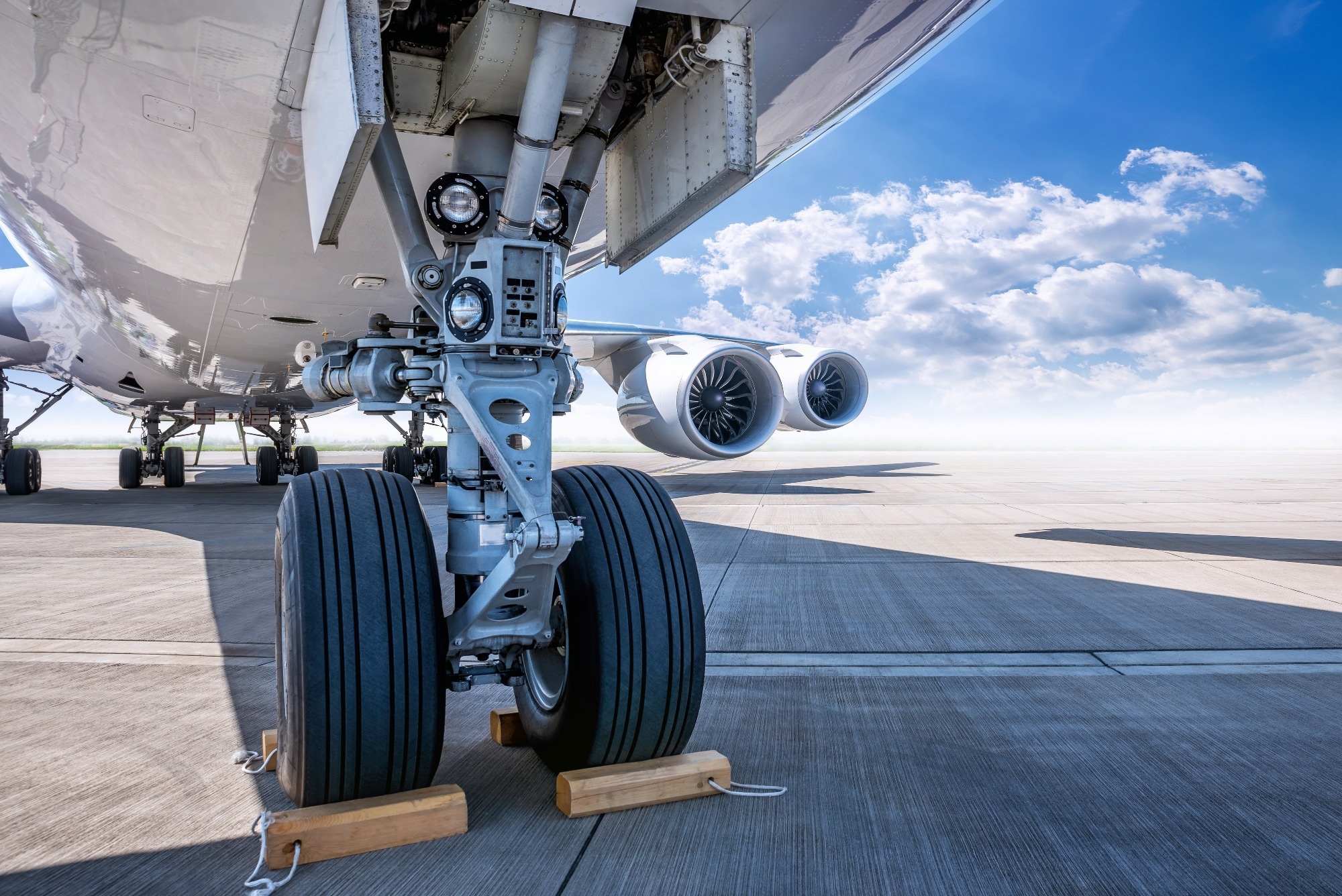
Image Credit: frank_peters/Shutterstock.com
Problem: The Menace of Landing Gear Corrosion
Due to their increased environmental exposure, aircraft landing gears are particularly vulnerable to corrosion. When left unchecked, even minor corrosion can proliferate, endangering the functionality and airworthiness of vital components. This can result in costly repairs and/or complete removal of the affected part.
Within the playbook of corrosion mitigation techniques in aerospace applications, cadmium plating has emerged as an invaluable process. This technique involves the deposition of a fine layer of cadmium onto the component surface, which serves as a durable barrier against physical assaults as well as a sacrificial anode that protects the underlying metal against corrosion. Cadmium plating is superior to other coatings and is praised for its remarkable adhesion, resilience against contaminants, and capacity to diminish friction between components.3 Ultimately, these attributes mitigate wear and tear, prolonging the lifespan of the product.
Challenge: Confronting the Issue of Deteriorating Parts
Microscopic examination of aerospace parts, such as landing gear, is vital for detecting corrosion-related flaws otherwise invisible to the naked eye. Advanced imaging techniques, such as scanning electron microscopy (SEM), are widely employed for precise analysis, defect identification, understanding a materials nature, identifying areas for proactive maintenance, and ensuring quality during manufacturing.
However, a persistent challenge arises when dealing with components that exceed the confines of conventional microscopy chambers. While these larger samples can be carefully deconstructed to fit within the chamber, this method has its drawbacks. For instance, there are situations where refraining from dismantling a sample is advantageous and scenarios, such as forensic analysis or the examination of antiquities, where cutting a sample is simply impractical.
In the following section we'll walk through a real-world analysis of a defective landing gear clamp using the Thermo Scientific Axia ChemiSEM—a concise solution to the vexing dilemma of accommodating oversized specimens.
Solution: Introducing the Thermo Scientific Axia ChemiSEM
Following the final visual inspection of a cadmium-plated steel aircraft landing gear clamp, anomalies in the form of pinholes and blemishes were discovered. While superficial in appearance, these defects could induce catastrophic failure if left unaddressed.
The Thermo Scientific Axia ChemiSEM was employed to non-destructively evaluate the integrity of the clamp at high-resolution. With over 70 mm of clearance to the analytical working distance and a 5-axis motorized stage capable of supporting 500 g, this system offers a solid approach to acquiring, processing, and showcasing physical as well as compositional data.
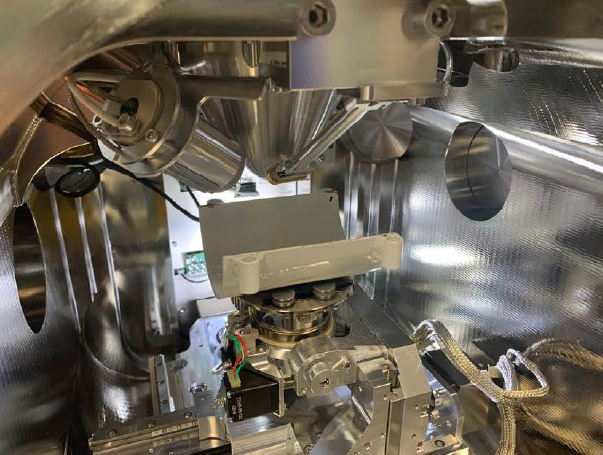
Plated steel landing gear clamp inside the Axia ChemiSEM vacuum chamber and on top of 5 axis motorized stage. Image Credit: John Yorston, Thermo Fisher Scientific, Inc.
Standing apart from conventional EDS analyses, the system harnesses simultaneous x-ray and electron signals to expedite sample analysis, yielding quicker data and results with reduced noise.4
Primary advantages of the system include:4
- Real-time Compositional Insights: Conduct EDS analysis by simultaneously capturing multiple signals, enabling live assessment of sample morphology and elemental composition.
- Continuously Primed for Imaging: Ensure seamless data collection without interruptions.
- Enhanced Speed of Data Acquisition: Employ various imaging and scanning techniques to optimize image capture in addition to enhancing throughput.
- Versatile Stage Design: Accommodate large samples effortlessly with a spacious chamber accessible via a door, coupled with a stage capable of supporting up to 10 kg through axis modulation.
- Superior Imaging Capabilities: Features optional low-vacuum mode and beam deceleration mode for effective charge mitigation, resulting in exceptional imaging performance.
By leveraging this cutting-edge imaging + EDS approach, the Axia ChemiSEM efficiently exposed the intricacies of the affected landing gear clamp, laying bare the underlying corrosion issue. Live quantitative elemental mapping allowed for the detection of cadmium chloride crystals, as well as iron oxychloride and the titanium dioxide found in white paint.
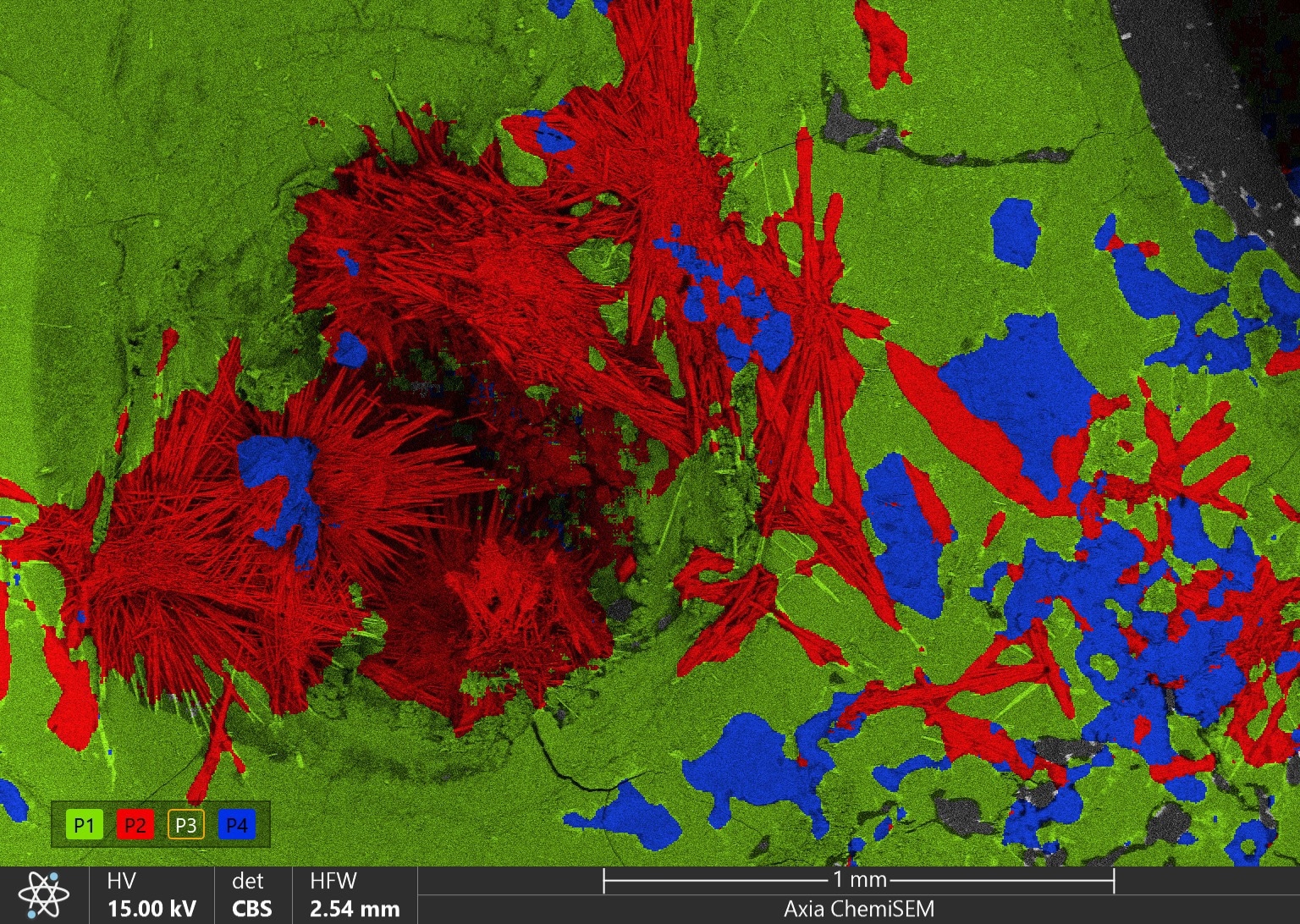
ChemiPhase image of the sample surface showing P1) oxidized base metal with chlorine (iron oxychloride), P2) potassium cadmium chloride needles, P3) carbon and titanium dioxide (white paint), and P4) sodium cadmium chloride needles. Image Credit: John Yorston, Thermo Fisher Scientific, Inc.
Through meticulous analysis, the origins of the pinholes were traced back to the welding process, where voids at the root of the weld fillet served as breeding grounds for corrosion initiation. In addition, the ChemiPhase mapping capabilities of the Axia ChemiSEM offered invaluable insights into the detailed composition of cadmium plating salts, shedding light on the intricate interplay between material properties and environmental factors.
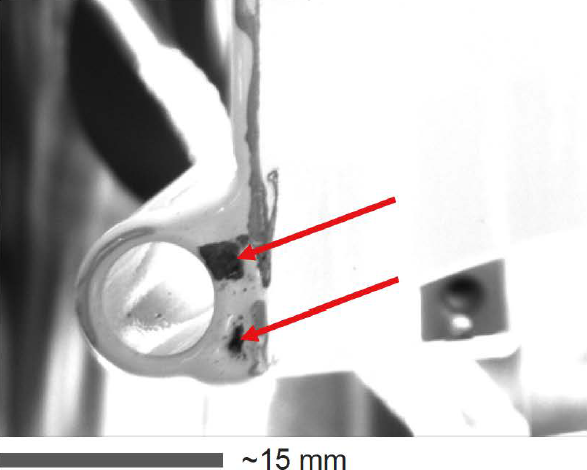
One of four bolt tabs on plated steel landing gear clamp. Image Credit: John Yorston, Thermo Fisher Scientific, Inc.
Equipped with a deeper understanding of the corrosion dynamics at play, corrective measures were drawn up to forestall the recurrence of defects. A re-evaluation of welding processes to eliminate pinholes was also suggested. Not only would this preemptively tackle the advance of corrosion on landing gear clamps, but it could safeguard all components affected by the welding process.
Conclusion: Forging Ahead in the Fight Against Corrosion
As the navy navigates the treacherous terrain of corrosion management, technological innovations such as the Thermo Scientific Axia ChemiSEM herald a new dawn for defect detection and mitigation. By marrying precision imaging with advanced analytical capabilities and speeding up time to results, engineers are empowered to confront corrosion challenges head-on, ensuring the unwavering resilience of naval aviation machinery.
References and Further Reading
- Spadafora, S.J. (2000). NAVAIR Perspective on Corrosion Prevention and Control. DTIC. Available at: https://apps.dtic.mil/sti/citations/ADA375736
- Lagasse, P. (2022). How Naval Aviation is Solving Its Billion-dollar Corrosion Problem. [Online] America’s Navy. Available at: https://www.navy.mil/Press-Office/News-Stories/Article/3025210/how-naval-aviation-is-solving-its-billion-dollar-corrosion-problem/ (Accessed on 15 April 2024).
- Sims, J. (2023). The Shining Benefits Of Cadmium Plating In The Aerospace Industry. [Online] Valence. Available at: https://www.valencesurfacetech.com/the-news/cadmium-plating/ (Accessed on 15 April 2024)
- ThermoFisher Scientific. Axia ChemiSEM Scanning Electron Microscope Instant fusion of chemistry and imaging. Available at: https://www.thermofisher.com/document-connect/document-connect.html?url=https://assets.thermofisher.com/TFS-Assets%2FMSD%2FDatasheets%2Faxia-chemisem-datasheet-ds0354.pdf
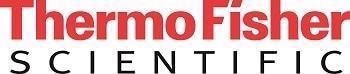
This information has been sourced, reviewed and adapted from materials provided by Thermo Fisher Scientific – Electron Microscopy Solutions.
For more information on this source, please visit Thermo Fisher Scientific – Electron Microscopy Solutions.