High-performance bonding materials like OEM-specified polyurethane and acrylic tapes are the ideal method when it comes to automotive attachment applications. Selecting the right tape for your automotive application means comparing the tapes in regard to their characteristics and performance under many conditions.
This article explores two Saint-Gobain® automotive tapes, Norbond E500 and Norbond Z3100, and their performance under a variety of test conditions, as well as their ideal applications.
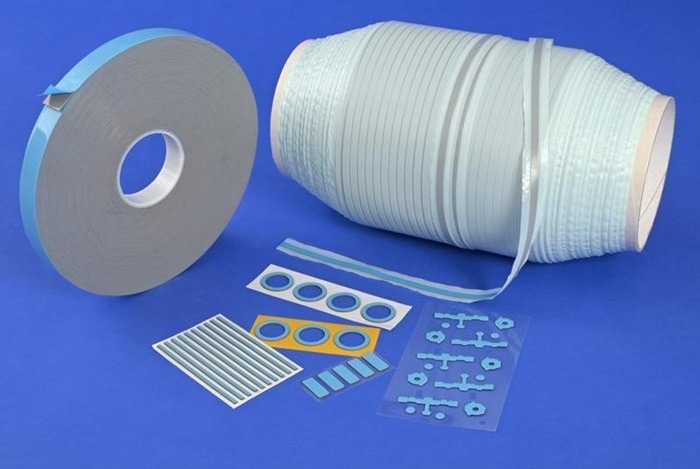
Image Credit: Saint-Gobain Tape Solutions
A Closer Look: E500 And Z3100
These two tapes are part of the Norbond® brand and offer unique benefits. The E500 Series is a black polyurethane foam tape featuring a high-performance acrylic adhesive system on either side.
The Z3100 Series is a dark gray acrylic foam tape with exceptional viscoelastic and adhesion properties and high-performance adhesive systems on both sides. There are many test methods and values that can be used to evaluate the general performance of these acrylic and polyurethane tapes.
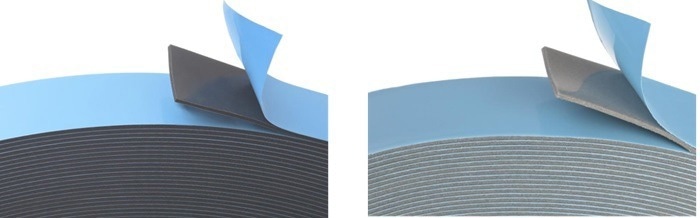
Image Credit: Saint-Gobain Tape Solutions
Tensile and Elongation Test
The tensile and elongation test is a characterization test used to rate the strength and elasticity of the foam core. A tensile testing machine pulls a cut sample section at a consistent speed, typically 20 inches (508 mm) per minute. The extension continues until the tape breaks, which is called tape failure.
The stress value and elongation percentage are measured and then plotted over the test duration to create the stress-strain curve. Using this test, the Z3100 acrylic foam tape demonstrates high elongation and moderate tensile strength at the breaking point. In contrast, the E500 polyurethane foam exhibits moderate elongation with relatively high tensile strength at the breaking point.
Adhesion Tests
Adhesion typically refers to the bond strength between an adhesive and its substrate. When conducting adhesion tests, it is important that the tapes compared are of similar gauges. Understanding the significance of dwell time—the period from when the tape is applied to when it is tested—is crucial.
Additionally, the test speed must be considered to determine if the samples have aged or been exposed to environmental conditions. Variations in any of these factors can yield different results for the same type of tape. Below are four typical adhesion tests:
- Peel Test
Commonly based on ASTM-D3330, this test is useful in comparing the adhesion of the same tape on a variety of substrate panels, like different paints.
A strip of tape, usually 1 inch wide × 6 inches long, is backed with an aluminum film (to limit stretching and simulate a semi-rigid surface) and adhered to a substrate panel. The tape is subsequently pulled at 90° or 180° to the panel’s surface at a consistent rate, typically 12 in (305 mm) per minute. Measurements of the peak force and average continuous peel force are then taken.
When comparing the 90° peel adhesion between polyurethane and acrylic tapes, the Z3100 acrylic tape exhibits greater peel strength from a painted panel than the E500 polyurethane tape. This superior performance is attributed to the highly viscoelastic core of acrylic tapes, which allows for more elongation during the peel process. Consequently, this involves a larger surface area and requires greater force to separate.
- Dynamic Tensile Adhesion (Pluck Adhesion)
Here, the tapes are commonly cut to 1 inch × 1 inch (25 mm × 25 mm) squares, then bonded between two substrates (often aluminum T-blocks) and then stressed perpendicular to the bond area.
The substrates are then separated at a test speed of 2 inches (51 mm) per minute while the peak force is measured, typically in pounds per square inch. In tensile and elongation tests of this type, polyurethane cores have less elongation and higher internal strength. When compared to Z3100 acrylic tape, E500 shows greater tensile adhesion strength.
- Dynamic Shear Adhesion
This test is typically designed after the ASTM D1002 test methodology, which decides adhesive strength, surface preparation guides and adhesive environmental durability. The tape is bonded between two overlapped panels and stressed parallel to the bond area. The peak force to separate the two panels is measured, with values reported in pounds per square inch.
When drawing comparisons of dynamic shear adhesion on painted panels after 72 hours, the E500 polyurethane tape has marginally higher resistance to dynamic stress versus the Z3100 acrylic tape.
- Static Loading (Creep)
This test is commonly based on ASTM D3654, which assesses the ability of pressure-sensitive tapes to remain adhered under a continuous load applied parallel to the surface of both the substrate and tape.
Unique to this test, the tape’s ability to withstand static loads is significantly influenced by not only its own properties but also by the part's geometric design and the loads applied.
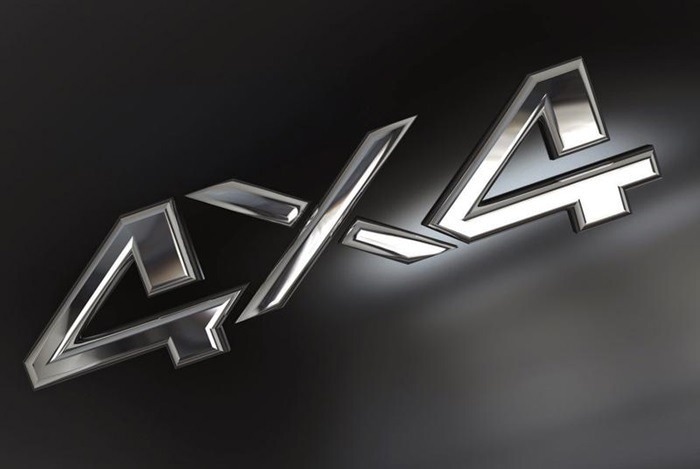
Image Credit: Saint-Gobain Tape Solutions
Making the Selection
If we were to examine two common automotive bonding applications, the tape configurations and adhesion comparisons previously discussed can help determine which tapes are best suited for those needs.
- Nameplates and emblems, typically small and intricate, are bonded to the bumper or hood of a vehicle. In this scenario, the design engineer requires a material that is easy to die-cut to align with the shape of the part, conforms well, and offers shear and tensile adhesion for stress resistance. Aesthetics are also crucial here, so a black color is preferred to lighter colors which are more visible. Using these selection criteria, a polyurethane foam such as E500 is the best match.
- Body side molding applications require materials that are somewhat flexible with excellent peel resistance. As these parts are often long and subject to varying thermal expansion rates, the chosen tapes must exhibit good stress relaxation properties. An acrylic tape like the Z3100 is particularly suitable for this application, thanks to its superior peel adhesion to automotive paint systems and its robust performance under high-stress conditions.
While acrylic tapes have exceptional viscoelasticity, good stress relaxation, and high elongation peel adhesion, tapes with polyurethane cores offer ease of die-cutting, good compressibility, high tensile adhesion, and good shear resistance.
By making an assessment of the properties, characteristics and performance under a variety of testing conditions, you can select the correct product designed to offer durable, long-lasting holding power for your automotive bonding requirements.
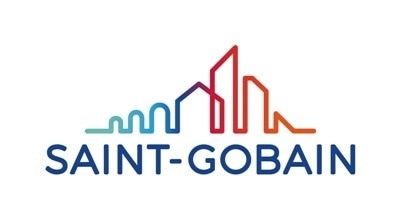
This information has been sourced, reviewed and adapted from materials provided by Saint-Gobain Tape Solutions.
For more information on this source, please visit Saint-Gobain Tape Solutions.