Introduction
Polyimide resins are known for their thermal stability, durability, and resistance to a range of solvents and chemicals. Combined with their excellent dielectric properties, these polymers possess characteristics which make them the favored materials for the fabrication of microelectronic devices for numerous electronic applications. Dianhydrides such as BTDA® (benzophenone tetracarboxylic dianhydride) are key comonomers required to produce polyimide resins.
Polyimide is widely used in electronics as film substrates for flexible copper-clad laminates (FCCL), which are used to manufacture flexible printed circuits (FPCs). PI-based FPCs provide many benefits over rigid printed circuit boards (PCBs), usually based on glass fiber-reinforced epoxy.
Epoxy-based rigid PCBs, advanced computer technology, and polyimide-based flexible PCBs are revolutionizing the technology of handheld and wearable electronic devices. The rest of this article is focused on the utilization of PI-based flexible PCBs, known as PI-based FPCs.
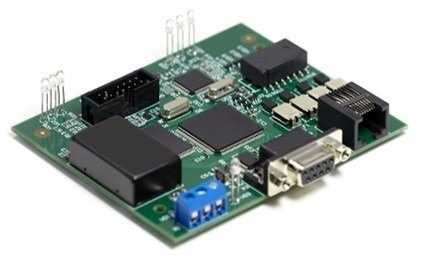
Rigid PCBs. Image Credit: Brun Bjorn/Shutterstock.com
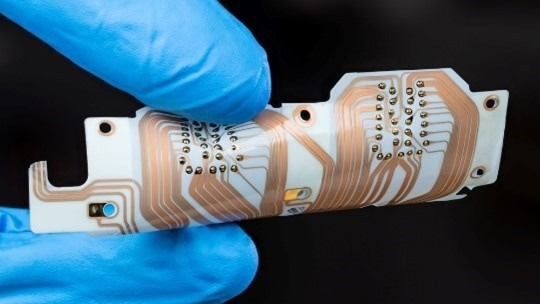
Flexible PCBs. Image Credit: KPixMining/Shutterstock.com
Flexible Printed Circuits (FPCs)
FPCs are a flexible alternative to rigid printed circuit boards (PCBs), which are usually manufactured with glass-reinforced epoxy. They are created starting with a flexible copper-clad laminate (FCCL). The basic FCCLs consist of a thin polyimide film base layer with a thin copper layer laminated on top. A predesigned circuit is created by carefully removing the excess copper from the top layer.
The PI substrate provides the electrically insulating foundation for the circuit. Its thinness (as little as 10 microns) makes the FPC bendable, foldable, or windable, miniaturizing the electronic device. It increases the circuitry density of an electronic device, benefiting the end-user with an increase in functions and features despite the smaller device size.
The FPC’s thin design facilitates excellent heat dissipation, improving the device's overall performance and life. An additional PI film is often installed on top (coverlay) to protect the fragile circuitry.
This system is a single-sided FCCL that produces a single-sided FPC. Double-sided FCCLs and FPCs are extensively used for printing circuits on both sides of the PI film substrate doubling the circuitry on a single FPC.
A sizeable percentage of commercial FCCL is manufactured with polyimide produced from pyromellitic dianhydride (PMDA). These 3-layer FCCLs usually apply an adhesive layer between the copper and the polyimide.
Specialized polyimides can be produced using benzophenone tetracarboxylic dianhydride (BTDA) achieving a secure and direct adhesion to copper. In addition to reducing the FPC thickness, 2-layer FCCLs eliminate potential failures in the FPC, including failure of the adhesive layer or its bond with the copper or the PI substrate.
Polymers other than polyimides are used in FPCs. Polyethylene terephthalate (PET) is often used in non-demanding applications because PET loses dimensional stability above 60-80 °C. Depending on the formulation chosen, polyimides can perform well above 250 °C.
The summary of the benefits of polyimide-based FPCs include:
- Thin and foldable
- Higher-temperature rating
- Superior dimensional stability
- Strong dielectric performance across a range of temperatures
- Withstands vibration
- Improved heat-dissipation
Polyimides' benefits can be utilized in devices like smartphones, smart watches, hearing aids, and other wearables. These devices can all be packed with more features in handheld, pocket-sized, or smaller designs and still be lightweight.
Which Properties of Polyimides Favor Their Use in Electronics?
The following explores the benefits of polyimides highlighting why they are the chosen dielectric polymers in electronics.
Resistance to high temperatures is critical for semiconductors and FPCs. The dielectric performance of the polymer is reduced at high temperatures, especially as it nears its glass-transition temperature (Tg). Polymer’s dimensional stability weakens above the Tg. It is vital that the dielectric material withstands numerous semiconductor production methods using high temperatures, including the solder reflow process that occurs at 288 °C.3
Polyimides can be formulated with Tgs from 350 °C to over 400 °C.1,2 In comparison, even specialized epoxy formulations have trouble reaching over 250 °C in Tg, without a severe compromise to their mechanical properties. Polyimide is a superior choice when evaluating based on the temperature criterion.
Coefficient of thermal expansion (CTE) for the dielectric base in an FPC should match that of copper’s CTE. A major mismatch increases the chance of the copper circuit delaminating from the base substrate when heat increases in the device during use, especially under climate extremes.
A partial delamination can result in a malfunction or total failure of the device. Epoxy can offer CTEs of 45-65 ppm/°C.4 In comparison, polyimide CTEs offer a range of 15-20 ppm/°C,5 which matches the 15-17 ppm/°C range for copper.4
PI-based FPCs perform excellently over a wide range of temperatures and withstand heat buildup when the device is being used. Commercial epoxy formulations can come close to copper’s CTE. However, the use of elevated levels of inorganic fillers makes them problematic as thin-film dielectric substrates for FPCs.
FPC’s thin polymer substrate must provide a low dielectric constant (Dk, high electrical insulation), across a broad range of frequencies. A low dissipation factor (Df), dielectric loss, or loss factor must be maintained.
High-frequency devices like 5G increase the burden because the dissipation factor can increase at higher signal frequencies. Although polyimides already provide good performance, newer PIs based on 6FDA dianhydride maintain a low dissipation factor even with increasingly higher frequencies like 5G.6
Growth Markets
The usage of polyimide-based FPC and, more broadly, in semiconductors is projected to increase with the expansion of electric vehicles and the installation of electronics in all vehicles.
New uses for PI include colorless polyimide films for foldable and shatterproof display systems for smartphones, tablets, and smartwatches. Related display applications being explored include OLED displays, pixel divided layer (PDL), and planarization layer (PNL).3,7
In this field, 2,2'-Bis-(3,4-dicarboxyphenyl) hexafluoropropane dianhydride (6FDA) produces colorless PI films with an outstanding performance at elevated temperatures and frequencies.
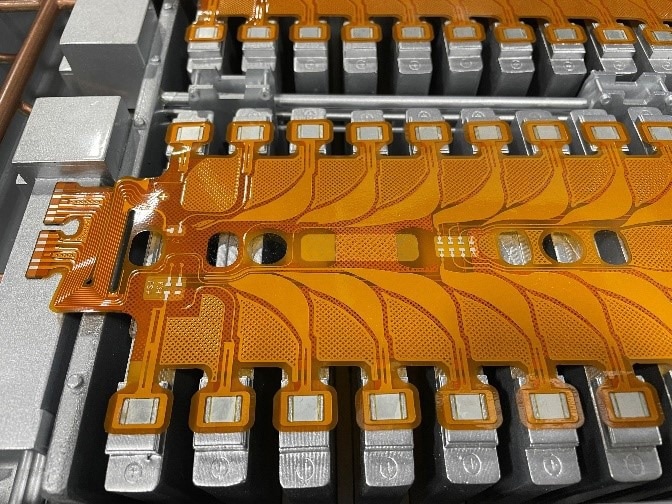
Prototype of a polyimide-based FPC designed to communicate with the battery management system within an electric vehicle. Image Credit: Doosan
Summary
Polyimides are a superior class of resins manufactured from dianhydrides and diamines. They provide increased glass transition temperatures, improved chemical resistance, high-dielectric performance, strong dimensional stability, and low CTE. They are a superior choice for manufacturing FCCLs, flexible printed circuits, and for semiconductor production.
As a result, polyimides have a significant place in the expansion of smart devices and personal electronics. Though polyimides can be classified as thermoplastics, they act and are utilized like thermosets. Historically, diamines have been more available in the industry than dianhydrides.
Innovations in the electronics industry are benefitting from the newer dianhydrides that are easily attainable on a commercial scale.
References and Further Reading
- Ch. 7 in Polyimides, Wilson, Stezenberger, Hergenrother, eds, Springer, 1990.
- Ch. 8 in ibid.
- M. Tomikawa, Polyimides for Micro-electronics Applications, in Polyimides, Nandeshwarappa and Chandrashekharappa Eds, InTechOpen, 2021.
- https://www.engineeringtoolbox.com/linear-expansion-coefficients-d_95.html
- DuPont™ Kapton® Summary of Properties, Technical Data, 2021.
- He, Yang, Zheng, Yang, Dielectric Properties of Fluorinated Aromatic Polyimide Films with Rigid Polymer Backbones. Polymers, 2022, 14, 649.
- Okuda, Miyoshi, Arai, Tomikawa, Polyimide Coatings for OLED Applications, J. Photopolymer S&T, 17, 207-214 (2004)
Notes:
BTDA is a registered trademark of Jayhawk Fine Chemicals Corporation (Jayhawk Fine Chemicals Corporation).
KAPTON is a registered trademark of DuPont Electronic Solutions.

This information has been sourced, reviewed and adapted from materials provided by Jayhawk Fine Chemicals Corporation.
For more information on this source, please visit Jayhawk Fine Chemicals Corporation.