In this interview, Adam Merah, the Business Development Manager at Nel Hydrogen, discusses the current landscape and challenges of scaling electrolyzer technology.
Can you provide an overview of the current landscape for electrolyzer technology scaling and the primary challenges faced in this area?
Despite volatile forecasts, the industry is experiencing significant growth driven by increasing demand for clean hydrogen production. Across geographies, industries, and applications, green hydrogen is the molecule crucial for achieving net-zero emissions. Government interest in promoting and encouraging the adoption of green energy has been instrumental in encouraging this demand, from the US to the EU and Japan.
Some of the primary challenges to scaling this technology are manufacturing costs, production capacity, and renewable energy availability. Nel is actively engaging with our partners to execute strategic initiatives to reduce our Platinum Group Metals (PGM) consumption, increase throughput, and expand our operations.
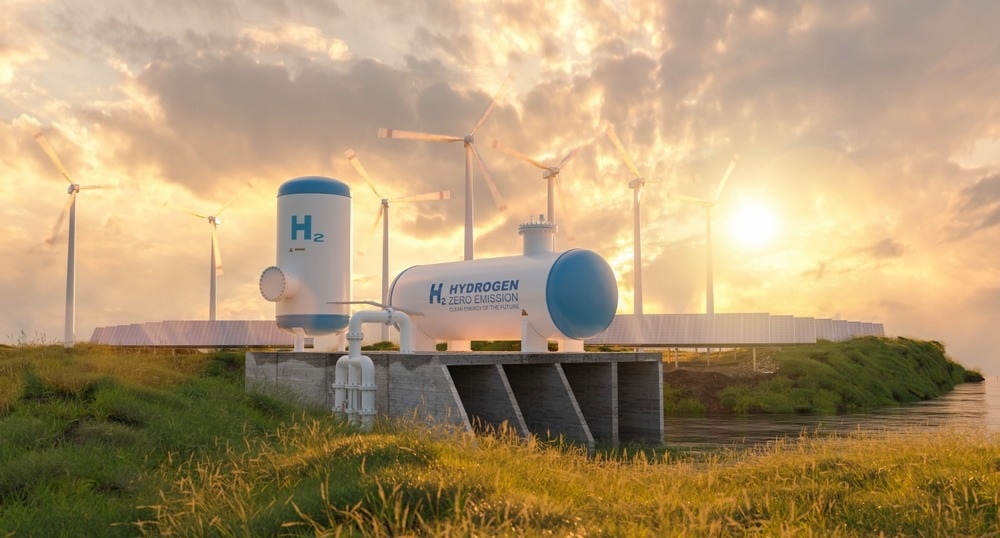
Image Credit: r.classen/Shutterstock.com
Given the global shortage of critical raw materials like Iridium, Platinum, Nickel, and Steel, what innovative strategies are electrolyzer OEMs adopting to ensure sustainability and scalability?
With Proton Exchange Membrane (PEM) Electrolysis, our goals are to reduce PGM loading and increase efficiency. This means fewer PGMs are used in the production of our electrolyzers, and we can produce higher volumes of hydrogen per unit of energy. We are currently implementing a sputtering process to decrease PGM loading by 66% and, as a result, reduce our Membrane Electrone Assembly (MEA) cost by up to 40%. Similarly, we are bringing online an automated Roll-to-Roll manufacturing process for our membranes to increase throughput by more than x100.
With AWE, we have numerous design initiatives to optimize our system design in order to minimize Nickel and Steel (primary inputs).
How are investments in R&D, such as Nel's significant allocation of revenues towards this area, driving advancements in alternative catalyst materials and improving electrolyzer efficiency?
Nel invests more than 20% of its revenues in R&D, in addition to government funding and grants we use to develop our technology. This is significant and underscores the importance of continuing to invest in ourselves and pushing the industry forward. Chemicals, materials, systems, and electronic engineering all play a part in the efficacy of our products.
Research and development to find alternative materials, specifically catalysts with equal or similar performance, is an ongoing effort. For instance, we focus on developing and evaluating less expensive catalysts made from more sustainable materials in greater abundance.
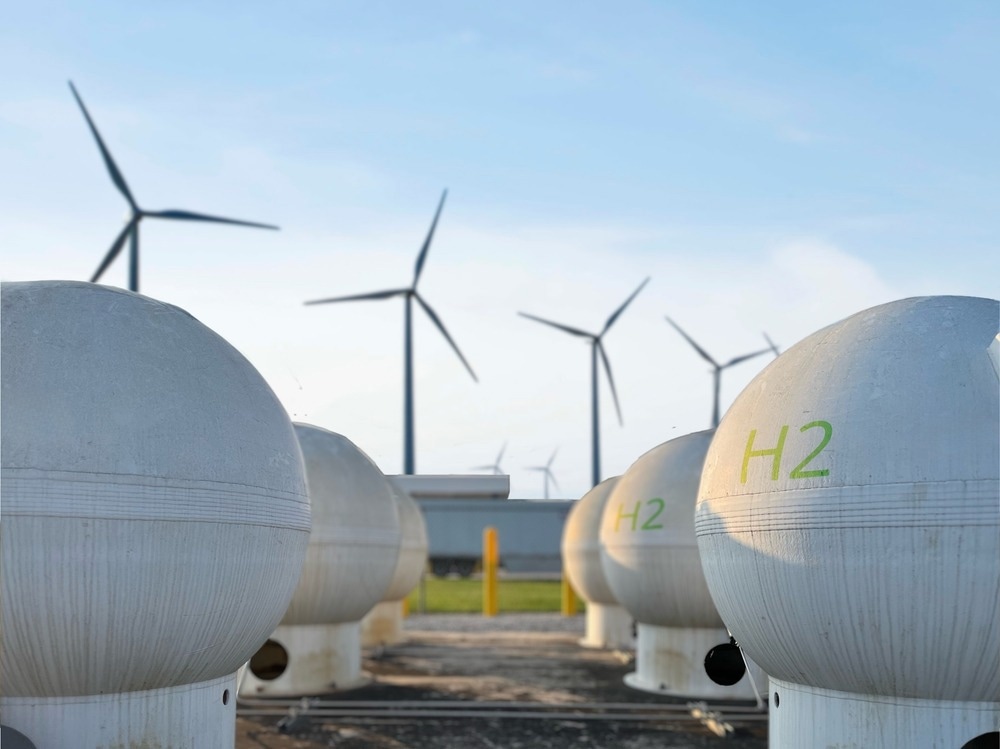
Image Credit: Industrial Donut Picks/Shutterstock.com
How does the standardization of components and materials contribute to the scalability of electrolyzer technology, and what challenges does this pose for innovation and customization?
This is one of our key strategies for driving down costs. Offering standard equipment helps reduce lead times and increases production, sourcing, and engineering efficiencies.
Standardizing components and materials used within electrolyzers reduces reliance on a wider variety of raw materials and simplifies the supply chain. When scaling up, this helps drive down costs.
From a customer perspective, designing larger systems using modular components allows for easier maintenance, repair, and replacement of individual units during their lifetime operation.
Could you elaborate on the role of advanced manufacturing processes, such as roll-to-roll and Sputtering, in reducing the dependency on precious metals like PGMs and their impact on cost and sustainability?
Industrializing and scaling the design and manufacture is critical to reducing equipment costs and accelerating electrolyzer adoption and integration into hard-to-abate sectors.
Moving to high-throughput processes can increase throughput AND lower the barrier to developing new materials. Delicate handling allows for fewer materials, and high–throughput standardization processes can also create higher uniformity, which improves performance.
Developing new production techniques, such as sputter coating, immediately reduces the consumption of PGMs in our PEM electrolyzers and directly reduces raw material costs. This also makes the production of this equipment more sustainable by reducing the demand for these resources.
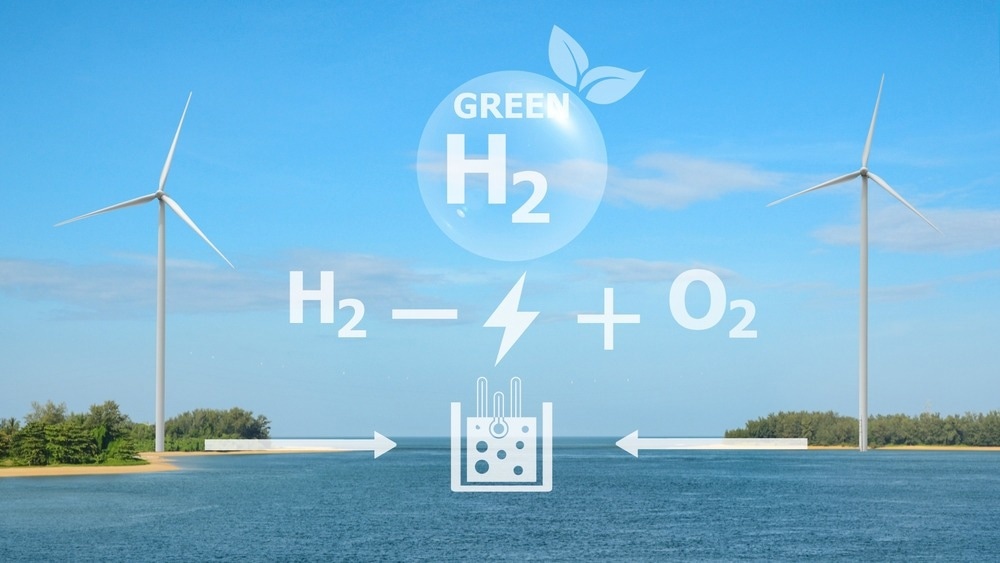
Image Credit: wasanajai/Shutterstock.com
How do recycling programs for PEM stacks contribute to a sustainable lifecycle for electrolyzer components, and what challenges are associated with these programs?
We implemented a recycling program for our PEM stacks to recover and reuse PGMs, thus creating a complete material lifecycle. The difficulty in implementing a program like this is how to incentivize customers to return the cell stacks. What we developed is a credit that can be applied to the replacement of that cell stack, thus creating an economic incentive for the customer, Nel, and the recycling partner. It’s a win for all parties.
In what ways are strategies like supplier diversification and advocacy with industry associations shaping the future of raw material sourcing for electrolyzer manufacturing?
Diversifying the supply chain for critical materials helps reduce dependence on any single source. This helps mitigate risk in case of supply disruptions. We also hedge and secure long-term supply agreements with suppliers to help further reduce the risk of supply constraints.
We are active participants in industry associations and lobby governments to prioritize responsible sourcing of critical materials. We want to ensure that the sourced materials are ethical and that all suppliers abide by the same rules.
From an R&D perspective, we are continually forming partnerships with research institutions (private and public) to develop new solutions, materials, designs, etc. This collaboration allows for shared resources and expertise to find solutions faster.
How important is local and community development in the scaling-up process, particularly in establishing local value chains and centers of excellence for the renewable hydrogen industry?
Developing local value chains and centers of excellence is mutually beneficial to electrolyzer OEMs and local and national governments. Local support, along with industry and academic partnerships close to the factories, helps contribute to lower Levelized Cost of Hydrogen (LCOH) in the scale-up phase. This transition from a traditional Oil & Gas to a renewable hydrogen industry further contributes to new jobs and skills development.
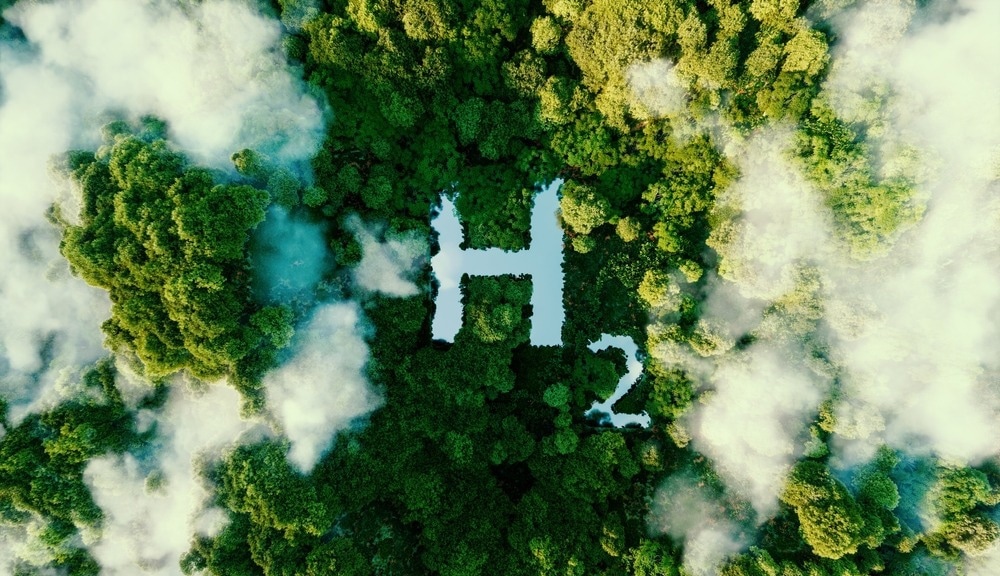
Image Credit: petrmalinak/Shutterstock.com
In your view, what role should government policies and international collaborations play in overcoming the challenges of scaling up electrolyzer operations, especially regarding raw material shortages and infrastructure development?
Government policies and incentives can encourage investment in grid upgrades, hydrogen infrastructure development, and research into electrolyzer technology, which are critical factors in the early adoption of green hydrogen. Many of the elements that inhibit the production of green hydrogen are within the control of government bodies and are crucial to unlocking this potential.
One of the most significant impacts is the development of new infrastructure to support these projects that still need to be created, i.e., pipelines, storage, grid capacity, etc. This emphasizes the importance of derivative liquid molecules in using existing infrastructure to transport green energy. We want to develop green drop-in solutions without needing new infrastructure to solve many of these challenges. This infrastructure expansion requires significant investment, coordination, and regulatory approvals.
On the price side, integrating larger electrolyzers may disrupt existing energy markets, particularly in regions dominated by traditional fossil fuels. Regulatory frameworks and market mechanisms must evolve to accommodate the growing role of hydrogen and incentivize investments in electrolyzer deployment and hydrogen infrastructure.
Addressing these challenges requires a coordinated effort involving policymakers, energy stakeholders, technology developers, and infrastructure providers. Strategic planning, investment in research and development, and collaboration across sectors are essential to successfully integrate larger electrolyzers into the existing energy system and transition towards a more sustainable and resilient energy future.
Where can readers find more information?
www.nelhydrogen.com
About Adam Merah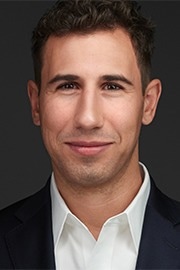
Adam is the Business Development Manager at Nel Hydrogen, with more than 13 years of technical and business development experience in industrial equipment and service solutions. In this role, he manages all business development efforts with PEM and Alkaline technologies for large-scale hydrogen projects in North America for Nel’s Electrolyser Division. His previous experience includes management roles in the centrifugal pump industry at ITT, where he focused on market development in the USA and Internationally for Oil & Gas, Chemical, and Power applications.
He has a Bachelor of Science in Mechanical Engineering from Rochester Institute of Technology and a Master of Business Administration from Heinrich Heine Universität, Düsseldorf.
About Nel Hydrogen
Nel has a history tracing back to 1927 and is today a leading pure play hydrogen technology company with a global presence. The company specializes in electrolyser technology for production of renewable hydrogen. Nel's product offerings are key enablers for a green hydrogen economy, making it possible to decarbonize various industries such as transportation, refining, steel, and ammonia.
Disclaimer: The views expressed here are those of the interviewee and do not necessarily represent the views of AZoM.com Limited (T/A) AZoNetwork, the owner and operator of this website. This disclaimer forms part of the Terms and Conditions of use of this website.