In this Interview, Mark Staub and Sandeep Pole delve into the intricacies of electrode manufacturing, focusing on the pivotal role of rheological characterization.
Can you tell us a bit about yourselves and your current roles at TA Instruments?
Mark Staub:
My name is Mark Staub. I am an application specialist in the Global Applications Group at TA Instruments. I received my Bachelor of Science in chemistry at Gettysburg College and subsequently earned my PhD in material science and engineering at Drexel University. I have published seven first-author, peer-reviewed articles, various co-authored articles, and several application notes. At TA Instruments, I lead theory and application courses on rheology and mechanical analysis.
Sandeep Pole:
I am Sandeep Pole, an application scientist in the Regional Applications Group at TA Instruments. I received my Bachelor of Science in chemical engineering at Virginia Tech and my PhD in polymer engineering from the University of Akron. I specialize in rheology, polymer processing, composite materials, process development, and R&D. I have co-authored five peer-reviewed journal articles on rheology. In my role at TA Instruments, I consult with customers and lead training sessions on rheology and dynamic mechanical analysis.
How does rheological characterization help in understanding the properties of electrode slurries?
Sandeep Pole:
Rheological characterization is crucial in electrode slurry development by providing detailed insights into how these complex fluids behave under various processing conditions. For instance, rheological tests allow researchers to measure shear viscosity across different shear rates, revealing whether the slurry is shear-thinning or shear-thickening.
Understanding thixotropy, which is how quickly the slurry structure recovers after shearing, helps optimize coating processes for uniform electrode deposition. Moreover, assessing yield stress ensures the slurry's stability, preventing settling and improving pumpability during manufacturing.
These rheological insights are indispensable for fine-tuning formulations and processing parameters to achieve consistent, high-quality electrode materials.
How is an electrode manufactured and what are the main challenges faced in this process?
Mark Staub:
Manufacturing an electrode begins by mixing an active anode or cathode material with a binder and conductive additive in an appropriate solvent. The resulting slurry is then coated onto a metallic current collector. After coating, the slurry is dried and calendared to produce an electrode with the desired density and porosity.
The primary objectives in electrode production include achieving high uniformity, ensuring good adhesion to the current collector, and minimizing costs. Challenges in slurry production include the need for early-stage characterization of the slurry formulation and addressing the time and cost associated with solvent removal processes.
What are yield stress and thixotropy, and why are they significant in producing battery electrodes?
Sandeep Pole:
Yield stress in battery electrode production refers to the minimum stress required for the slurry to begin flowing, crucial for preventing settling and ensuring uniformity during processing.
Conversely, Thixotropy denotes the time-dependent recovery of the slurry's structure after shearing, impacting the quality of coating applications. These properties are vital as they influence electrode slurries' stability, processability, and performance consistency throughout manufacturing.
What are some advanced tools and methods used in rheological testing for electrode slurries?
Sandeep Pole:
Rheometers and their accessories are advanced tools and methods in rheological testing for electrode slurries. They apply controlled forces to measure parameters such as shear stress, strain, and rate, which are essential for calculating viscosity and modulus.
These instruments operate in flow and oscillation modes, enabling detailed viscosity characterization as a function of shear rate or stress and the viscoelastic properties, including storage and loss moduli. Accessories like the rheo-IS allow simultaneous impedance and rheological testing, offering insights into the conductive network structure at high shear rates encountered in processing.

Image Credit: Kittyfly/Shutterstock.com
How do powder and slurry testing differ, and why are both important in electrode manufacturing?
Mark Staub:
Powder testing focuses on understanding the physical properties of individual solids before they are dispersed in a solvent to form a slurry. This includes characteristics like particle size distribution, surface area, and morphology.
Slurry testing, on the other hand, involves evaluating the rheological properties of the dispersed mixture in a solvent, such as viscosity, thixotropy, and stability.
Both types of testing are crucial in electrode manufacturing: powder testing ensures the quality and uniformity of raw materials, while slurry testing assesses the processability and performance of the final electrode slurries.
Can you share some examples of how rheological data has been used to improve electrode manufacturing?
Mark Staub:
Rheological data is instrumental in advancing electrode manufacturing processes, particularly in lithium-ion battery production.
For instance, yield locus analysis transforms shear experiment data into actionable insights in graphite anode manufacturing, revealing crucial parameters like cohesion and yield strength across different graphite samples from commercial and industrial suppliers.
This analysis aids in selecting materials with superior performance characteristics. It correlates bulk powder properties with microstructural features, such as particle size and morphology, significantly influencing storage stability and processing efficiency.
Similarly, in NMC-based cathode powder analysis, rheological studies demonstrate that adjusting the PVDF binder ratio impacts powder cohesion and yield strength while also affecting flow function during processing. By optimizing these parameters, manufacturers can achieve enhanced electrode performance and streamline production processes, aiming to reduce solvent use and improve overall battery quality and reliability.
How can reducing the use of solvents in electrode manufacturing benefit the environment?
Sandeep Pole:
Reducing solvent content in electrode manufacturing significantly reduces environmental impact and costs. Although a high solvent content aids in the slurry mixing process, it leads to a significantly longer and more energy-intensive drying process.
Solvents can often be toxic, further contributing to environmental concerns. By minimizing solvent usage, manufacturers can enhance the sustainability of their processes, lowering energy consumption and costs associated with solvent handling and disposal.
How can rheological characterization aid in developing more sustainable and efficient battery production processes?
Sandeep Pole:
Rheological characterization can significantly contribute to developing more sustainable and efficient battery production processes. By accurately measuring the viscosity, thixotropy, and stability of electrode slurries, rheology helps optimize solvent usage.
Higher solvent content reduces viscosity for easier processing but increases energy consumption during drying, which is time-consuming and environmentally taxing. Therefore, by reducing solvent content, rheological analysis supports environmentally sustainable practices in battery manufacturing.
In addition, rheological tools like rheometers provide critical data for formulating optimal slurry compositions and guiding processing conditions, ultimately enhancing efficiency and reducing waste in battery production.
About Mark Staub
Mark Staub, PhD is currently an Application Scientist in the Global Applications group at TA Instruments –Waters LLC. Dr. Staub received his Bachelor of Science degree in Chemistry at Gettysburg College and subsequently earned his PhD in Materials Science and Engineering (Polymer Science focus) at Drexel University.
He has published seven first-author peer-reviewed articles, various co-authored articles, and several application notes. In his role at TA Instruments, he leads the Theory and Application courses on rheology and mechanical analysis.
About Sandeep Pole
Sandeep Pole, PhD is an Applications Scientist under the Regional Applications group at TA Instruments – Waters LLC. Dr. Pole received his Bachelor of Science degree in Chemical Engineering at Virginia Tech and his PhD in Polymer Engineering from the University of Akron.
He specializes in rheology, polymer processing, composite materials, process development, and R&D. He has co-authored five peer-reviewed journal articles on the topic of rheology. In his role at TA Instruments, he consults with customers and leads training sessions on rheology and dynamic mechanical analysis.
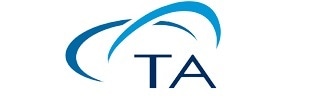
This information has been sourced, reviewed and adapted from materials provided by TA Instruments.
For more information on this source, please visit TA Instruments.
Disclaimer: The views expressed here are those of the interviewee and do not necessarily represent the views of AZoM.com Limited (T/A) AZoNetwork, the owner and operator of this website. This disclaimer forms part of the Terms and Conditions of use of this website.