Moving stages are essential but challenging components in semiconductor and nanotechnology manufacturing. These stages, used in wafer inspection, lithography, metrology ,and other applications can cause significant vibration that can affect tool performance and throughput if it is not mitigated properly.
In this interview, Elias Brassitos, Senior Control Systems Engineer at AMETEK, talks to AZoMaterials about these challenges and solutions. TMC works with clients to identify and mitigate tool-induced vibration, offering tailored solutions like the STACIS® and Electro-Damp® systems. This interview explores the importance of settling time, the impact of different isolators, and TMC's innovative techniques that enhance manufacturing efficiency.
What kinds of instruments use moving stages?
Many instruments involved in today’s semiconductor and nanotechnology manufacturing processes, such as wafer inspection, lithography, and metrology, suffer from payload-generated vibration caused by the onboard moving stages running on the tool itself.
These moving stages often operate at high accelerations to increase tool throughput. This can lead to large forces being applied to the tool’s vibration isolation suspension, which can deteriorate performance and compromise the target throughput.
TMC works closely with clients to understand the source and nature of every tool-induced vibration before recommending and tailoring a custom OEM vibration cancellation solution.
Why is settling time so important, and how is it defined?
Settling time determines how quickly the stage or inspection gantry reaches and stabilizes at a target position. It is typically defined as the time it takes for a stage, or sometimes the entire gantry, to settle and remain within a specified window after the motion stops or the travel limit is reached. It affects the semiconductor production operation in several ways, such as:
- Throughput: Semiconductor production has numerous steps involving the movement of stages during wafer transport and alignment, lithography, exposure, inspection, and more. Shorter settling times in every step will quickly increase the overall throughput of the manufacturing process and reduce dead time in the tool between the various manufacturing steps.
- Reducing Vibration and Oscillation: With every stage of acceleration or deceleration, the natural frequencies and mode shapes of the tool, its frame, and suspension are excited. The stage must settle without creating excessive vibration or oscillation, as these can affect the precision of subsequent steps.
- Temperature Control: The semiconductor manufacturing environment often needs to maintain tight temperature control. Long settling times can contribute to temperature variations, affecting the properties of materials and processes. Quick settling times help maintain a stable thermal environment, ensuring consistent process conditions in every run.
Settling time is largely affected by the floor isolation solution selected. The stiffer the isolator’s spring, the faster it settles, but at the cost of less floor vibration cancellation. Alternatively, the softer the isolator’s spring, the larger the vibration cancellation bandwidth, and the longer the settling times and payload displacements will be due to stage movements.
TMC’s STACIS® products provide the best of both worlds by combining a fast-settling hard-mount (stiff) isolator with a piezo-based actuation element to compensate for the isolation losses in floor vibration. For more settling-time critical applications, TMC’s ElectroDamp® combines soft-mount isolators with high-force voice coil motors to directly counteract payload moving stage forces.
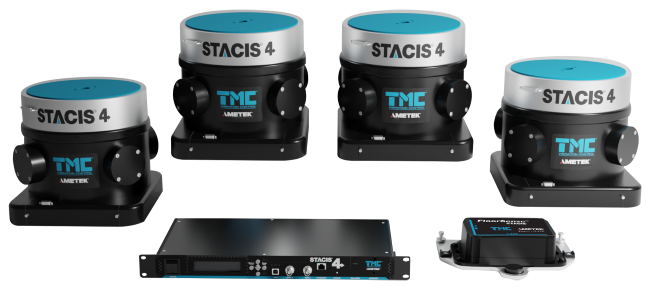
Image Credit: AMETEK, Inc.
What challenges does this create for vibration control?
The recoil forces generated by the stages’ acceleration and deceleration can cause the tool to bounce and oscillate on the isolators. The frequency and amplitude of these oscillations depend on the natural frequency of the floor isolators, which is roughly around 2-3 Hz for air isolators and roughly 15-25 Hz for piezo-based isolators. These disturbances can excite the vibration mode shapes of the tool subassemblies and degrade their performance or functionality altogether.
TMC manufactures and sells two main types of passive isolators: soft-mount and hard-mount isolators. Soft-mount isolators, such as air springs or low-frequency dye springs, result in large payload motion and long settling times. However, hard-mount isolators, such as STACIS®, which uses a stiff rubber spring, are more resistant to stage forces and typically result in 40 times less payload displacement. The settling time of hard isolators is also around nine times shorter than air isolators.
Below is the position response comparison for stage movement involving both hard and soft mount isolators. Hard-mount isolators result in significantly less tool displacement upon a stage movement than soft-mount isolators.
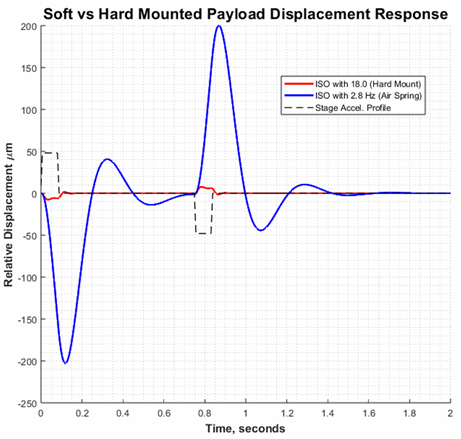
Image Credit: AMETEK, Inc.
Are there certain kinds of vibration control techniques that work better than others for this application?
Yes, certain types of vibration control solutions work better than others in applications involving moving stages. For applications requiring extremely minimal payload recoil, TMC recommends its novel stage cancellation system Electro-Damp®. This system directly operates on the payload using electric Lorentz motors and can suppress the stage recoil forces as they occur.
Electro-Damp® receives feedforward signals directly from the stage controller and applies an equal and opposite force to keep the payload balanced during the stage acceleration and deceleration periods.
Electro-Damp® also has advanced features for motorized positioning stage applications such as payload docking, where the payload is slowly lowered to grounded mounts. The payload can also be held horizontally during certain wafer transfer applications by engaging the Electro-Damp® motors.
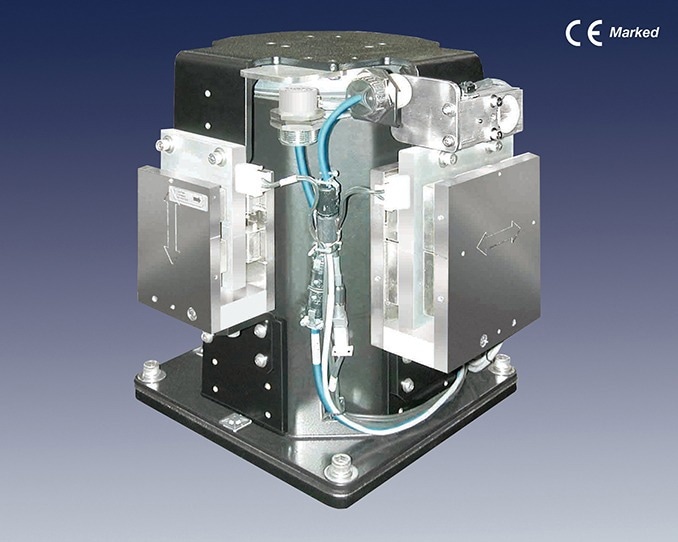
Image Credit: AMETEK, Inc.
How can you be sure? Can you model the behavior of various vibration control methodologies?
Exactly. We can model the behavior of dynamic payloads on springs and test potential solutions while drawing on many years and a myriad of real-world applications.
While most of our simulation work is computer-generated, the inputs used in these simulations, such as isolator frequency response, damping factor, and gain, are experimentally measured using the TMC shaker platforms.
By using these measured values rather than estimating them, we can produce precise, physics-driven vibration control analysis with high confidence and accuracy for our customers.
These capabilities, combined with years of isolator construction know-how, allow TMC to model, design, build, and test isolators that meet our customers’ floor vibration requirements with great precision and minimal trial and error.
Below, a simple 3D animation illustrates a customer payload response with 4 tri-axial 18 Hz springs. Using these dynamic models, TMC engineers can effectively communicate and architect advanced vibration control solutions for clients to meet their most intricate and sophisticated floor vibration problems, particularly when high acceleration/high force moving stages are in play.
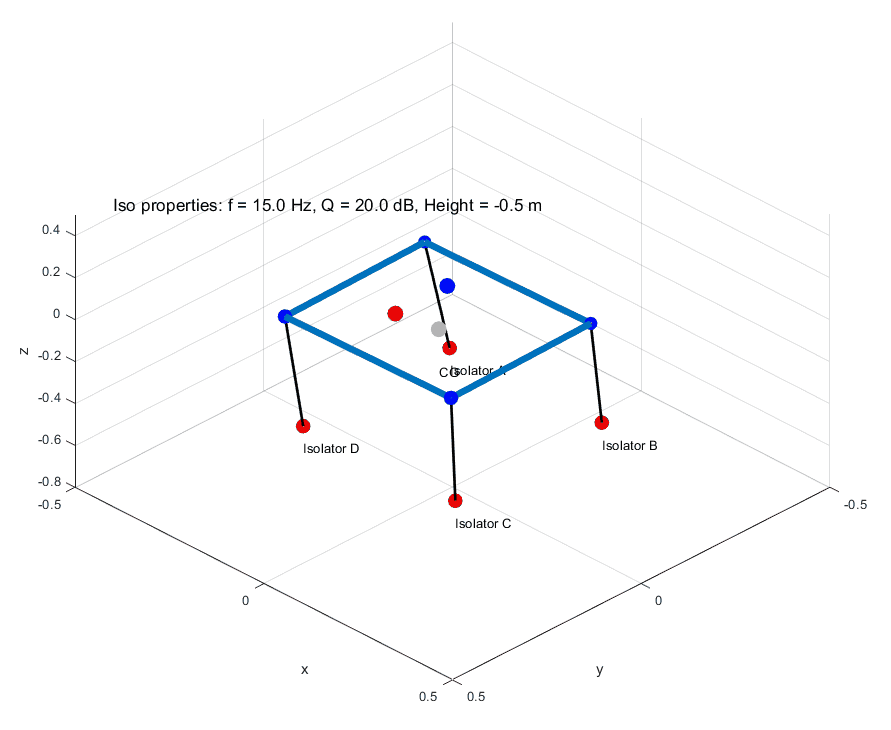
Image Credit: AMETEK, Inc.
About Dr. Elias Brassitos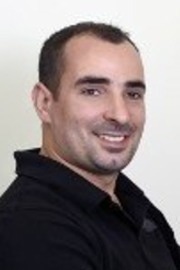
Elias Brassitos is currently a Senior Control Systems Engineer at AMETEK. He has previously served as a Space Technology Fellow at NASA's Jet Propulsion Laboratory, where he developed novel actuation hardware for extreme space robotics, focusing on planetary rovers and space manipulators. Dr. Brassitos holds several patent applications and has authored numerous technical papers in the areas of design, optimization, and dynamic modeling of complex mechanical systems and robotic actuators.
Dr. Brassitos received his B.S. degree from the University of Massachusetts, and his M.S. and Ph.D. degrees from Northeastern University, all in mechanical engineering.
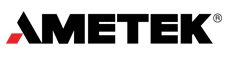
This information has been sourced, reviewed and adapted from materials provided by AMETEK, Inc.
For more information on this source, please visit AMETEK, Inc.
Disclaimer: The views expressed here are those of the interviewee and do not necessarily represent the views of AZoM.com Limited (T/A) AZoNetwork, the owner and operator of this website. This disclaimer forms part of the Terms and Conditions of use of this website.