Synthetic polymers are frequently used to replace conventional materials, however, the majority are flammable. The presence of strong heat and oxygen can result in combustion.
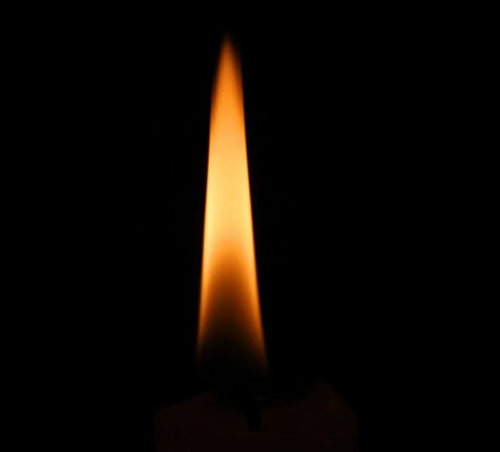
Image Credit: AIMPLAS
With this in mind, it has become crucial to investigate flame retardants for plastics. The goal is to improve the material's resistance to fire and reduce the heat release and flame spreading speed. Without these flame retardants, many plastics would be banned from use.
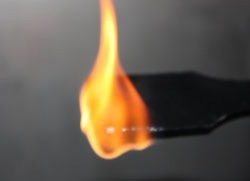
Image Credit: AIMPLAS
Traditional Flame Retardants
The demand for flame retardants has varied. Beyond being effective in the event of fire, flame retardant systems are required to comply with other demands, such as not being toxic, not migratory, and maintaining plastic mechanical properties.
In the world of flame retardants, halogenated additives (based on bromine and chlorine organic compounds) have historically been at a disadvantage because of environmental regulations. Many applications require non-halogenated additives, like magnesium hydroxides and aluminum trioxides. However, these require a high concentration to achieve a cooling degree that can inhibit ignition.
In the event of a fire, water, incorporated initially as a hydrate, is released, and the plastic is once again flammable. These additives are also incorporated in very high percentages, affecting processability and the material's physical and thermal properties.
In addition to the flame retardants previously mentioned, antimony trioxide is often used due to its synergic effect with halogenated compounds and other retardants, like boric acid and phospho-halogenated organic products.
Flame-retardant systems that are built on phosphorus inhibit the combustion process and cause carbonization on the surface. This protects the material from heat effects and interrupts the oxygen supply, limiting the spread of flames. This mechanism is significantly more effective than the physical mechanism of releasing water.
Flame Nanoretardants
The newest generation of flame retardants is called nanomaterials. Most polymeric nanocomposites contain particles with a high aspect ratio and a surface that assists in the interaction between particle and polymer. Small quantities (0.5-5 %) of these properties, such as rigidity and thermal resistance, might increase, while others, like water absorption and gas permeability, might decrease.
Several studies have recently explored the influence of specific nanoparticles in regards to fire performance of plastic materials, both isolated and when combined with other flame retardant systems, with encouraging results. The current focus in nanocomposites is to decrease the ignition timing and eliminate drips. This is because a carbon layer or three-dimensional net is formed during a fire's progress, which protects the rest of the material and propagates the fire.
Three distinct types of nanocomposites depend on how many dimensions the dispersed particles have of the nanometer order. Nano-1D are flat laminated structures, such as nano clays; Nano-2D are longitudinal structures, such as nanotubes or carbon nanofibers; and Nano-3D are dimensional, silica spherical nanoparticles.
The current challenge in nanotechnology is developing methodologies that allow obtaining nanocomposites with a uniform dispersion degree and a strong matrix-particle bond. The results of this will strongly influence the final properties of nanocomposites.
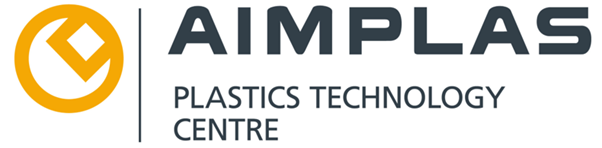
This information has been sourced, reviewed and adapted from materials provided by AIMPLAS.
For more information on this source, please visit AIMPLAS.