Historically, the evolution of plastics has gravitated towards reinforced plastics, a strategic enhancement aimed at boosting their strength, stiffness, thermal resistance, and durability, while preserving the intrinsic benefits of thermoplastics.

Image Credit: Ahmed Hamdy Hassan/Shutterstock.com
This article delves into the fundamentals, advantages, and uses of fiber-reinforced thermoplastics during a period of heightened interest in reinforcement agents.
The reinforcement of plastics is closely associated with the type and geometry of the fibers used, which influence the mechanical performance, weight, sustainability, rheology, cost, and other critical factors of the final product. These elements are key in determining the appropriate fiber for a specific material or application.
Common Reinforcing Fibers Include:
- Glass Fibers: Widely utilized for their high strength, stiffness, and cost-effectiveness, glass fibers come in various forms, such as chopped strands and continuous rovings. This variety allows for extensive customization in compound designs.
- Carbon Fibers: Known for their superior strength-to-weight ratio, high stiffness, and excellent fatigue resistance, carbon fiber-reinforced thermoplastics are prevalent in aerospace, automotive, and sporting goods industries. Their primary advantage over glass fibers is their lightweight nature.
- Aramid Fibers: Materials like Kevlar® are notable for their exceptional strength and impact resistance, as well as excellent abrasion resistance. Though used less frequently than glass and carbon fibers, aramid fibers are integral in ballistic composites, aerospace components, and high-performance sports equipment.
- Natural Fibers: Fibers such as hemp, flax, and jute are increasingly popular due to their renewable and eco-friendly properties. While not as strong as synthetic fibers, they provide commendable specific strength and low density, with biodegradability that makes them attractive for automotive interiors, construction materials, and consumer goods. Their primary attribute is their minimal carbon footprint.
- Basalt Fibers: Extracted from natural volcanic rock, basalt fibers excel in heat resistance and durability, making them excellent for incorporation into thermoplastics. These fibers demonstrate strong mechanical properties, including high tensile strength and stiffness, with exceptional thermal stability standing out as a key feature.
Importance of Fiber Length
Fiber length is pivotal in achieving optimal performance in reinforced plastics. Generally, longer fibers in both the compound and the final product correlate with better performance. This characteristic is influenced by the original length of the selected fiber and the processing conditions, which may shorten the fibers, diminishing their mechanical effectiveness. A fiber's physical attributes can be evaluated through calcination and measuring fiber length in compounds and final products.
Short (chopped) fiber reinforcement involves the use of fibers, ranging from 3 to 8 mm in length, randomly oriented within the polymer matrix. This style of reinforcement is often used in compression and injection molding processes for applications requiring complex shapes and geometries, for example, consumer goods and automotive interior components.
This method offers affordable solutions for improving mechanical properties and dimensional stability and is the most common technique for general-purpose applications.
Long fiber reinforcement uses fibers of several centimeters (final pellets from 1.25 to 2.5 cm in length), which are typically aligned in a specific direction within a polymer matrix.
Such a technique is appropriate for structural components in the construction, automotive, and aerospace industries because it provides excellent mechanical properties such as superior tensile strength, stiffness, fatigue resistance, and impact strength.
Continuous fiber reinforcement includes the utilization of unbroken fibers aligned in a single direction throughout a composite part. This technique offers exceptional mechanical properties, making it perfect for high-performance applications in the defence, aerospace and automotive industries, and use in advanced manufacturing methods such as pultrusion and filament winding.
Continuous fibers allow for the design of lightweight but structurally efficient components, providing flexibility for intricate shapes and structures and excellent strength-to-weight ratios. Fiber length is not an issue here because the fiber is usually embedded in a UD tape shape, which covers the entire length of a bobbin.
Milled fibers, unlike chopped fibers, are finely ground strands of reinforcing materials that have been processed to uniform lengths (0.1 to 0.3 mm). These have specific advantages in composite material applications in an array of industries.
Milled fiber reinforcement improves the performance of thermoplastics in the construction, manufacturing, marine, aerospace and automotive industries by improving stiffness, resistance to impact and dimensional stability.
Milled fibers can also be used in compounding processes where mixing capacity is inferior, such as in single-screw extrusion.
Conclusion
Fiber-reinforced thermoplastics offer significant enhancements in stiffness, strength, and thermal resistance, making them indispensable across a range of industries. The choice of fiber type, along with length, plays a crucial role in determining a material's final properties.
Each type provides unique advantages that can be customized to specific applications, driving innovation in and beyond the automotive, construction, and aerospace industries.
As the need for environmentally sustainable and high-performance materials increases, fiber-reinforced thermoplastics continue to evolve and meet the diverse needs of industry.
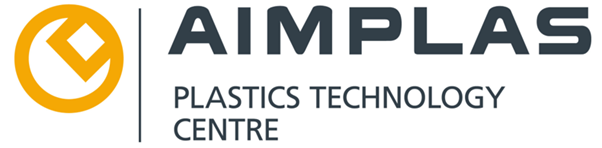
This information has been sourced, reviewed and adapted from materials provided by AIMPLAS.
For more information on this source, please visit AIMPLAS.