Reinforced plastics exhibit greater strength, stiffness, thermal resistance, and durability compared with conventional plastics while maintaining the benefits of thermoplastic materials, significantly enhancing their performance and applicability.
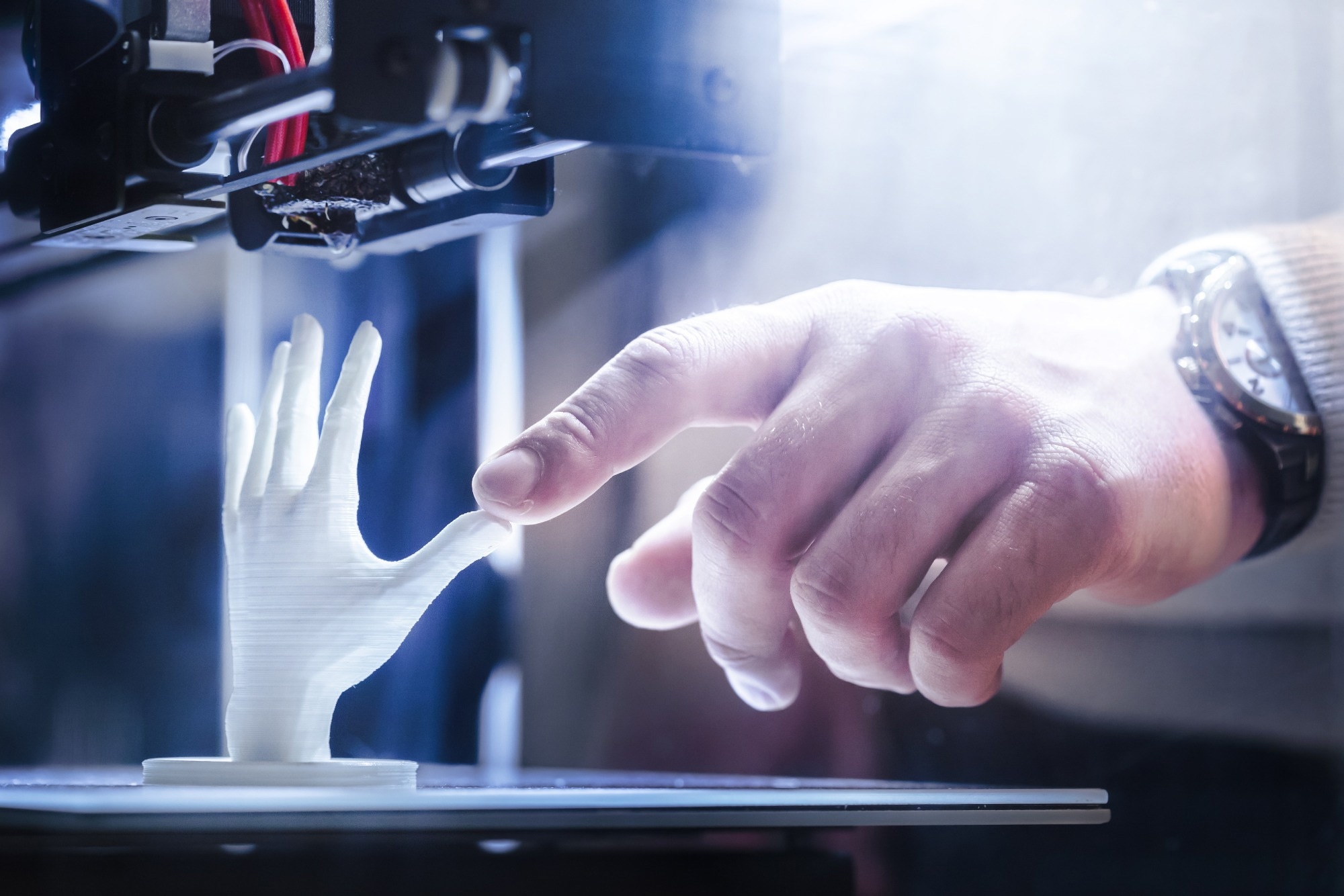
Image Credit: FabrikaSimf/Shutterstock.com
In this article, amid the increasing interest in reinforcing agents, the applications of fiber-reinforced thermoplastics are discussed.
Fibers can improve a variety of plastic properties, including mechanical characteristics, temperature of service, impact resistance, toughness, weight reduction, dimensional stability, and corrosion resistance, benefiting various high added-value industries, namely:
- Automotive Industry: Lightweight and high-strength composite components are incorporated into vehicle body panels, structural reinforcements, and interior trims to enhance fuel efficiency and crashworthiness
- Aerospace: Carbon fiber-reinforced thermoplastics are used in aircraft components to reduce weight, as well as maintain structural integrity and fatigue resistance
- Construction: Fiber-reinforced thermoplastics are used in building materials, including structural profiles, panels, and reinforcements, providing durability, corrosion resistance, and easier installation.
- Sports and Recreation: Fiber-reinforced thermoplastics provide high-performance, lightweight solutions for sporting goods manufacturers, with applications in equipment such as bicycle frames and tennis rackets
- Electronics: electrically conductive composites reinforced with metal particles or carbon fibers are employed in electronic enclosures, connectors, and housings to provide structural stability and electromagnetic shielding
In addition to applications in these sectors, reinforced thermoplastics continue to be a dynamic area of materials innovation, with several significant trends shaping their development and adoption across industries.
Increased Use of Carbon Fiber Reinforcements
Carbon fiber-reinforced thermoplastics (CFRTP) are gaining popularity due to their excellent strength-to-weight ratio, fatigue resistance, and stiffness. The automotive, aerospace, and sporting goods industries are increasingly adopting CFRTP for lightweight structural components, resulting in improvements to processing techniques and cost-reduction efforts.
Development of Hybrid Reinforcement Systems
Research into hybrid reinforcement systems, most of which combine carbon and glass, is ongoing, with the goal to achieve synergistic effects and customize mechanical properties for specific applications. Balanced price, weight and performance are crucial factors for combining glass and carbon fibers, as well as minimizing the electrical conductivity of carbon fibers.
Drive for High-Performance Polymers
High-performance polymers can exhibit exceptional properties and the lower prices of glass/carbon fibers make these compounds very attractive for such applications, particularly PEEK and other similar polymers.
Integration of Additive Manufacturing (3D Printing) and Fiber Reinforcement
By combining additive manufacturing technologies, including continuous fiber reinforcement (CFR) and fused deposition modeling (FDM), complex, fiber-reinforced thermoplastic parts with improved mechanical properties can be produced.
Sustainability and Recyclable Materials
The development of sustainable reinforced thermoplastics using recycled and bio-based materials has expanded rapidly in recent years.
As renewable materials, natural fibers are attractive materials for automotive and construction markets due to their availability, low weight and low cost. Their main application is as a replacement for mineral fillers. Natural fibers can also be used in the bioplastics market, which is expected to grow in the next few years.
Recycled fibers from thermoset resins are also generating interest due to the possibility of lowering prices and reducing the environmental impact of end products while maintaining a high level of reinforcement.
Continuous Fiber Reinforcement
Continuous fiber is being used increasingly to replace structures made of thermoset-reinforced resins. The key advantage of these thermoplastic composites is the versatility of matrices and recyclability.
Advances in Processing Technologies
Advances in processing technologies, including automated fiber placement (AFP), automated tape laying (ATL) and in situ consolidation methods, are constantly increasing the efficiency of complex fiber-reinforced thermoplastic structure manufacture.
These technologies provide greater throughput, precision and scalability, facilitating mass production of high-performance components for automotive, aerospace and industrial applications.
Fiber-reinforced plastics are experiencing a resurgence thanks to advances in technologies, environmental trends, and the development of new polymers and fiber formats. These materials are now being applied in diverse and non-traditional sectors such as aerospace, automotive, consumer electronics, medical devices, and renewable energy industries.
The versatility, durability, and potential for customization make reinforced thermoplastics increasingly popular in sectors looking for lightweight, durable, and high-performance materials.
AIMPLAS is actively involved across these industries, collaborating with companies to enhance the performance of their fiber-reinforced products and managing the entire value chain from compounding and converting to recycling.

This information has been sourced, reviewed and adapted from materials provided by AIMPLAS.
For more information on this source, please visit AIMPLAS.