Batteries have rapidly become a crucial factor in the global energy storage ecosystem and it is expected that batteries will continue to be central to ensuring a safe, affordable, and clean energy transition.
Batteries represent an essential enabler for the increasing number of electric vehicles (EVs) being sold every year, throughout the transport sector. Batteries are increasingly important in energy storage, with them seeing widespread use in utility-scale and behind-the-meter applications as their cost reduces and there is increased deployment of solar and wind power.
As their centrality to these applications continues to grow, sustainability in battery materials and the battery supply chain will be essential for integrating renewable energy sources, optimizing storage capacities, and accelerating the global transition to electric mobility.
The entire battery lifecycle must be considered in order to realize this goal, including the material supply chain, battery chemistries, and ongoing environmental impacts.
Current developments in battery technology have the potential to further improve the sustainability of lithium-ion batteries and alternative battery chemistries by enhancing the battery cathode and anode materials’ availability and safety. Essential raw materials will also be eliminated from future battery chemistries.
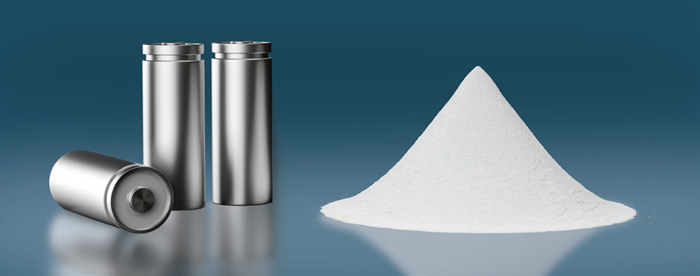
Image Credit: Thermo Fisher Scientific – Production Process & Analytics
For example, promising cases include the growing adoption of lithium-iron-phosphate (LFP) batteries in the market, the rapid development of next-generation battery technologies like the solid-state battery or lithium-sulfate battery chemistry; and the ongoing commercialization of sodium-ion batteries.
Conventional lithium-ion batteries continue to be a key component of modern economies, however, and these have very much reshaped electronic devices and electric mobility. Their use is also increasing in power systems.
The development of new battery chemistries may challenge traditional lithium battery dominance in the coming years, however.
Growing Demand for Battery Storage Capacity
The use of batteries continues to expand throughout the energy storage sector, with record electric vehicle sales and use of battery storage in the power sector.
One in five cars sold in the global market is now electric, while in China, approximately 50 % of car sales are electric. An increasing number of wind and solar power projects are also leveraging stationary battery storage capacity.
These factors have contributed to the announcement numerous new battery cell manufacturing facilities worldwide, with political support in various regions supporting these developments.
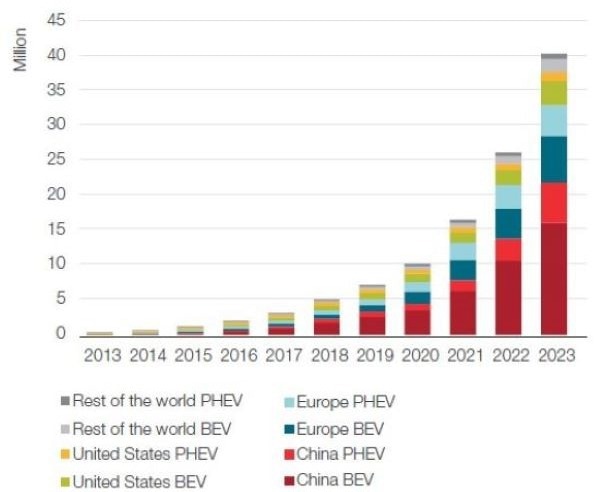
Figure 1. EV battery storage capacity. Image Credit: IEA, Global EV Outlook 2024, trends in electric cars
There has been rapid growth throughout the lithium-ion battery industry over the past five years. Between 2018 and 2023, the installed capacity of LIBs for energy storage applications increased by over 2000 GWh – a noteworthy fourfold increase that increased the total volume to over 2400 GWh by the end of 2023.
Lithium batteries have outperformed other energy storage technologies over the past ten years due to their superior cycle life and energy density. Ongoing advances in manufacturing processes and battery chemistry and have lowered the average costs of batteries by a total of 90 % from 2010 levels.
Battery Material and Supply Chain Risks
The current international rechargeable battery supply chain is extremely complex and involves a large number of stages. China moved into this sector early and, as a result, now occupies a dominant position at almost every point in the downstream battery supply chain.
China accounts for over 50 % of the global raw material processing for essential battery minerals including cobalt, lithium, and natural graphite.
China essentially controls the whole graphite anode supply chain, with the country possessing a 90 % share of the world’s graphite mining operations. It is home to 85 % of global battery cell manufacturing capacity, and the country’s industrial base is responsible for 90 % of global cathode active material production.
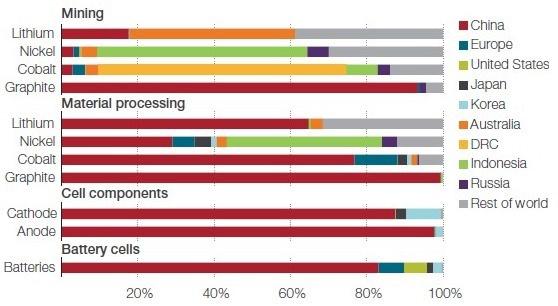
Figure 2. Geographical distribution ofthe globalbattery supply chain. Image Credit: IEA, Batteries and secure energy transitions
China’s dominant role in the battery supply chain ranges from the processing of raw materials to the finishing of components and cells. Its role is undeniably substantial and difficult for other nations to match at the present time, with just Korea (9 %) and Japan (3 %) currently housing noteworthy cathode active material manufacturing capacity outside of China.
Different battery chemistries require different supply chains, however, meaning that it may be possible to find opportunities to reduce supply chain dependencies while developing more sustainable means of advancing the electric mobility and energy storage sectors.
Evolution of Lithium-Ion Battery Material and Chemistries
The cathode material - the positive electrode, where lithium ions are stored during the charge and discharge cycle – is impacted by its elemental composition, which in turn influences battery performance. Batteries are, therefore, named and classified according to the applied cathode active material.
The most commonly employed lithium-ion battery chemistries are:
- lithium nickel manganese cobalt oxide (NMC)
- lithium nickel cobalt aluminum oxide (NCA)
- lithium iron phosphate (LFP)
- and lithium cobalt oxide (LCO)
Different combinations and proportions of each battery chemistry’s electrode material result in distinctive battery characteristics. For example, LCO is currently one of the most recognized chemistries with its high-energy density and technological maturity resulting in widespread use in portable electronics .
NMC, NCA, and LFP chemicals are currently the most prominent battery types used in electric vehicles (EVs), but alternative technologies and materials for lithium-ion batteries or entirely other chemistries have recently garnered attention as potential successors; for example, solid-state and sodium-ion batteries.
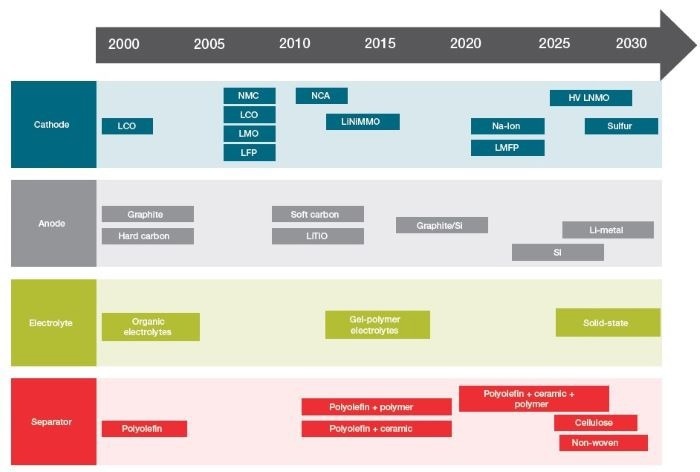
Figure 3. Timeline of battery cell chemistry development. Image Credit: Volta Foundation, Annual Battery Report 2023
Download the white paper
References and Further Reading
- IEA Report: Global EV Outlook 2024
- IEA Report: Batteries and Secure Energy Transitions
- Fraunhofer-Gesellschaft: Alternative Battery Technologies Roadmap 2030+
- Fraunhofer-Gesellschaft: Solid-State Battery Roadmap 2035+
- Nature Communications: Electric vehicle battery chemistry affects supply chain disruption vulnerabilities
- Volta Foundation, Annual Battery Report 2023
Acknowledgements
Produced from materials originally authored by Julian Renpenning, PhD. from Thermo Scientific.
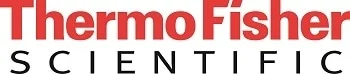
This information has been sourced, reviewed and adapted from materials provided by Thermo Fisher Scientific – Production Process & Analytics.
For more information on this source, please visit Thermo Fisher Scientific – Production Process & Analytics.