By Taha KhanReviewed by Lexie CornerAug 21 2024
An alloy is a mixture of two or more elements, at least one of which is a metal. The goal of creating an alloy is to combine the desirable properties of different elements to produce a material superior to its individual components. This article discusses the process of alloy creation, the various types of alloys, their applications, and their significance in modern industries.
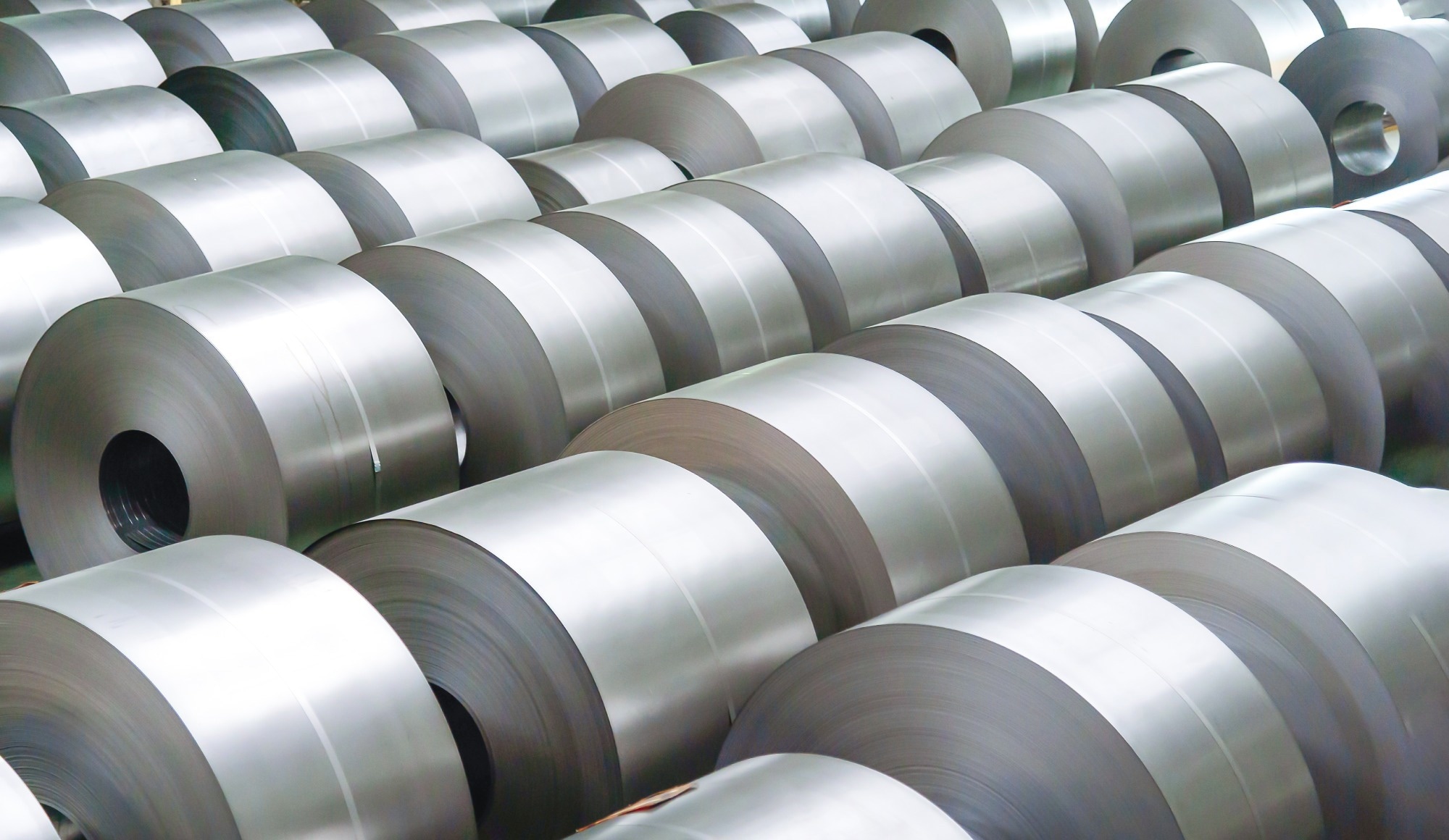
Image Credit: Nuttawut Uttamaharad/Shutterstock.com
Alloy Design and Properties
Alloys are not just random combinations of elements; they are precisely engineered to enhance specific properties, such as strength, corrosion resistance, ductility, and conductivity.1, 2 For example, stainless steel in kitchen appliances, bronze in sculptures, and aluminum alloys in airplanes are all meticulously designed to fulfill their specific purposes.
The alloying process generally involves melting and mixing the constituent elements in exact proportions, followed by cooling to form a solid material. The combination of these elements, along with the cooling process, significantly influences the properties of the alloy.
There are different methods of alloying, each impacting the final properties. In substitutional alloying, atoms of the added elements replace some of the atoms in the base metal's crystal lattice. In interstitial alloying, smaller atoms fit into the spaces between the base metal's atoms.2, 3
Additionally, the composition of the materials used in the alloying process plays a crucial role. For instance, varying the amount of carbon along with elements like chromium, nickel, or manganese can produce different types of steel, such as stainless steel or tool steel, each with distinct characteristics.2, 3
Common Alloy Types and Their Applications
Steel Alloys
Steel alloys are composed of iron combined with elements such as carbon, chromium, nickel, manganese, molybdenum, and vanadium. These elements enhance the alloy's properties, including strength, hardness, corrosion resistance, and toughness, making steel alloys versatile for a wide range of applications.3, 4
Carbon is the primary alloying element in steel, and its content directly influences the material's hardness and strength. For example, low-carbon steels are more ductile and easier to weld, while high-carbon steels are harder but more brittle. Stainless steels, which include chromium, are particularly resistant to corrosion, making them ideal for use in environments exposed to moisture or chemicals.3, 4
Steel alloys are used in a variety of industries, including construction, automotive, aerospace, and manufacturing.
Aluminum Alloys
Aluminum alloys are known for their lightweight, high strength-to-weight ratio, and corrosion resistance. They are also easy to machine, weld, and form, making them versatile for various applications. Common alloying elements for aluminum include copper, magnesium, manganese, silicon, and zinc, each imparting unique properties to the alloy.
For example, copper increases strength and hardness, making aluminum-copper alloys ideal for aerospace and automotive applications.3, 5 Magnesium enhances strength without adding significant weight, making it perfect for transportation and structural uses. Additionally, aluminum-silicon alloys, known for their exceptional casting properties, are frequently used in the automotive industry for engine components.3, 5
Brass Alloy
Brass alloys are primarily composed of copper and zinc, with varying proportions tailored to achieve specific properties. Brass is valued for its malleability, corrosion resistance, and attractive appearance, making it ideal for both decorative and functional applications.3, 6
In addition to copper and zinc, brass alloys can include small amounts of other elements such as lead, tin, aluminum, iron, and nickel to enhance particular characteristics. For example, lead is often added to improve machinability, making brass easier to cut and shape, which is essential for manufacturing precision components like gears, valves, and fittings.
Similarly, aluminum-brass alloys offer increased strength and corrosion resistance, especially in seawater, making them suitable for marine hardware and heat exchangers. 3, 6
Advantages of Alloys Over Pure Metals
Alloys offer numerous advantages over pure metals, including enhanced mechanical, thermal, electrical, and resistive properties. For example, pure iron is relatively soft and prone to rusting, but alloying it with carbon to create steel makes it much harder and more corrosion-resistant.
Similarly, while pure aluminum is valued for being lightweight, its softness and malleability can limit its use in structural applications. Alloying creates a stronger material that is more suitable for these purposes.
Alloys can also be engineered for specific electrical or thermal properties. For instance, adding small amounts of certain elements to copper can greatly improve its electrical conductivity, making it ideal for electrical wiring.7, 8
Another significant advantage of alloys is their improved resistance to environmental factors. Many alloys are specifically designed to withstand extreme temperatures, resist oxidation, or endure harsh chemical environments, expanding their use in industries like aerospace, where materials must perform reliably under challenging conditions.7, 8
Future Innovations
Researchers are continually exploring advanced materials and manufacturing techniques to develop alloys with even more extraordinary properties. These innovations have the potential to revolutionize various industries, including transportation, energy, healthcare, and electronics.
For instance, in a 2024 study, researchers developed a novel brass alloy, CuZn30X, to address corrosion issues common in traditional brass used in musical instruments.9 This new alloy incorporates 0.1 % each of phosphorus, tin, and nickel to enhance corrosion resistance.
Thermodynamic simulations guided the selection of these microalloying elements, which were then used to produce the CuZn30X alloy. Testing revealed that CuZn30X significantly improved resistance to dezincification compared to the standard CuZn30, largely due to the formation of a protective surface layer.
CuZn30X also demonstrated favorable properties for both cold and hot rolling. This development will mitigate corrosion problems in brass instruments, preserving their structural integrity and extending lifespan.9
Ongoing research and innovations in alloy development will not only advance the alloy industry but will also positively impact related industries such as transportation, healthcare, automotive, electronics, and aerospace.
More from AZoM: Properties and Applications of Bronze Alloys
References and Further Reading
- Ma, E. (2005). Alloys created between immiscible elements. Progress in materials science. doi.org/10.1016/j.pmatsci.2004.07.001
- Weinhandl, D. (2021) What is an Alloy? [Online] Mead Metal.inc. Available at: https://www.meadmetals.com/blog/what-is-an-alloy (Accessed on 09 August 2024)
- Lichtig, A., Schadegg, J. (2024) All About Alloys: A Xometry Guide. [Online] Xometry. Available at: https://www.xometry.com/resources/materials/what-is-an-alloy/ (Accessed on 09 August 2024)
- Sankara Papavinasam, (2024) Corrosion Control in the Oil and Gas Industry, Chapter 3 Materials. Elsevier. https://doi.org/10.1016/B978-0-12-397022-0.00003-0
- Stojanovic, B., Bukvic, М., Epler, I. (2018). Application of aluminum and aluminum alloys in engineering. Applied Engineering Letters: Journal of Engineering and Applied Sciences. doi.org/10.18485/aeletters.2018.3.2.2
- Nobel, C., Klocke, F., Lung, D., Wolf, S. (2014). Machinability enhancement of lead-free brass alloys. Procedia Cirp. doi.org/10.1016/j.procir.2014.03.018
- Warner Brothers Foundry Company. (n.d.) Advantages of Alloys Over Pure Metals. [Online] Warner Brothers Foundry Company. Available at: https://www.wbcastings.com/blog/advantages-of-alloys/ (Accessed on 09 August 2024)
- Wieland Diversified. (2020). Advantages of Using Alloys. [Online] Wieland Diversified. Available at: https://www.wieland-diversified.com/blog/the-advantages-of-using-metal-alloys-over-pure-metals/(Accessed on 09 August 2024)
- Berndorf, S., Markelov, A., Guk, S., Mandel, M., Krüger, L., Prahl, U. (2024). Development of a Dezincification-Free Alloy System for the Manufacturing of Brass Instruments. Metals. doi.org/10.3390/met14070800
Disclaimer: The views expressed here are those of the author expressed in their private capacity and do not necessarily represent the views of AZoM.com Limited T/A AZoNetwork the owner and operator of this website. This disclaimer forms part of the Terms and conditions of use of this website.