↵
Surfx's Dr. Robert Hicks takes us on a journey of discovery around atmospheric plasma and its potential to revolutionize semiconductor packaging.
Could you provide an overview of Surfx Technologies as a company? What is Surfx, and what do you specialize in?
Surfx sells atmospheric plasma equipment primarily to the semiconductor industry. Most of our equipment's applications are in advanced packaging. We create an ionized gas plasma to clean and activate surfaces for improved bonding. In particular, our hydrogen plasma removes the oxidation from tin micro-bumps on flip chips prior to thermocompression bonding. This enables the 3D stacking of chips with exceptionally high interconnect densities.
Many people think of plasma as exotic, but it is ubiquitous in the semiconductor industry, because it allows you to use electricity and the components of air to create a safe way to clean a surface. It is low-temperature, involves no hazardous chemicals, is fast, and can be automated for mass production.
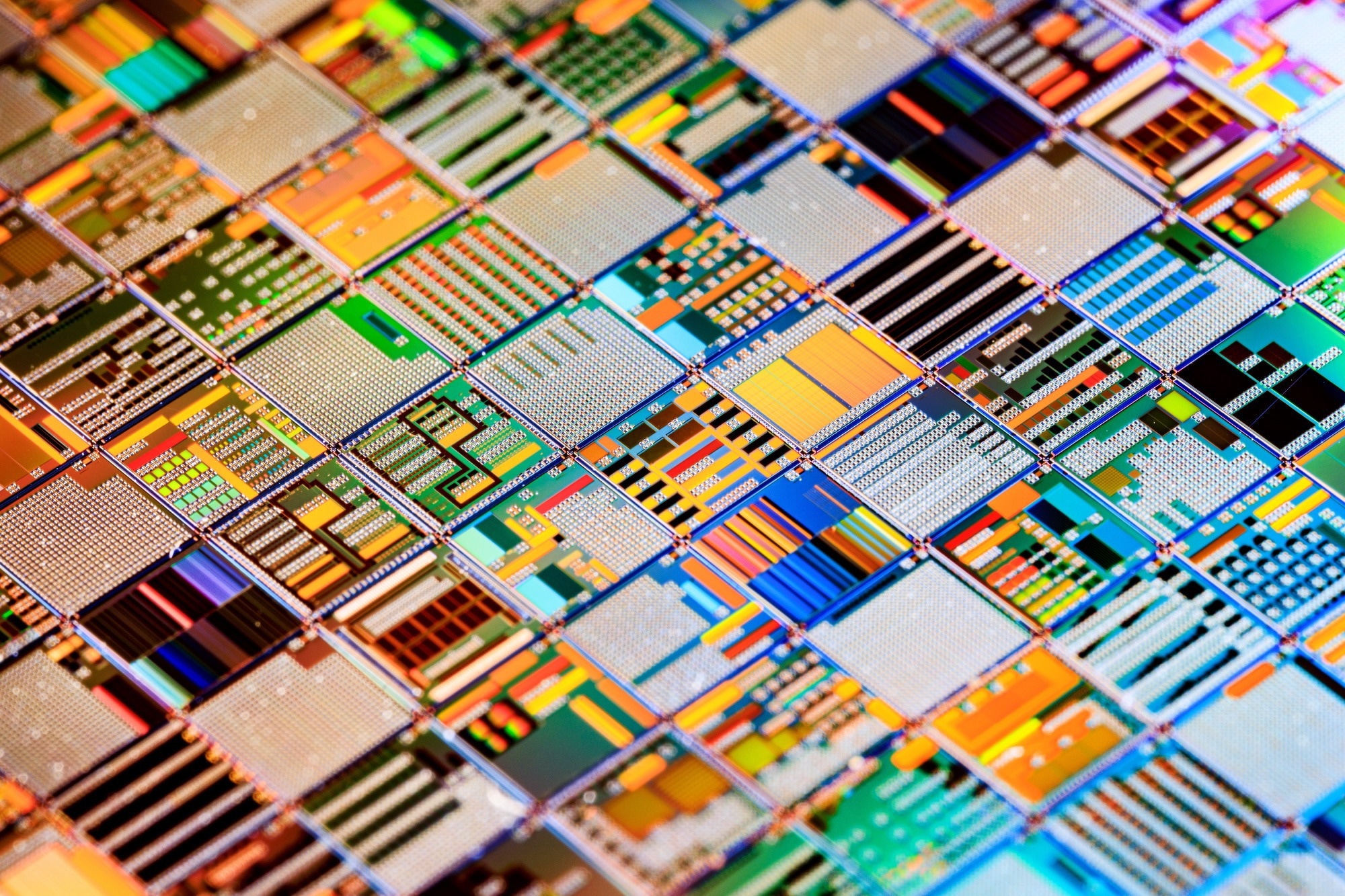
Image Credit: Andrei Armagiov/Shutterstock.com
Dr. Hicks, could you share a bit about your career and the expertise you bring to the semiconductor equipment industry?
I am a chemical engineer. I have a PhD in catalysis and surface science from the University of California at Berkeley. After I graduated, my next job was as a professor at UCLA, where I worked for 32 years. My research focused on plasma, surface science, materials modification, and the design of chemical processes for semiconductor processing. I retired from the university in 2017.
I founded Surfx in 1999 and helped lead the company through its early years. I became fully involved after retiring from the UCLA and have been guiding the company ever since.
In the highly competitive field of chip manufacturing, what unique advantages do Surfx’s products offer, and how does it stand out from other surface treatment solutions in the market?
A very specific type of plasma is needed in semiconductor manufacturing. It has to be a low-energy plasma with very little ionization. This keeps the temperature low so that the delicate integrated circuits are not damaged. Furthermore, the ionized gas must be generated over a large enough volume to uniformly treat the surface of the substrate, which in many cases is a 300-mm-wide silicon wafer. The plasma must not produce any particles in the micron or submicron range that could potentially settle on the wafer. Also, you cannot create an electrostatic discharge (ESD) that might short out the micro circuits.
All of these characteristics, weak ionization, low temperature, uniform, particle-free and ESD-free, are difficult to achieve. Originally, these plasmas could only be made inside vacuum chambers.
At Surfx, we figured out how to make this special type of plasma at atmospheric pressure. By doing so, we take the process out of an expensive vacuum chamber and integrate it into the next step in semiconductor manufacturing. In advanced packaging, this next step is the thermocompression bonder for flip chips. Combining the cleaning and deoxidation step with bonding is a tremendous advantage for stacking chips together with millions of interconnects.
Surfx is one of the fastest-growing plasma equipment companies. What strategic initiatives are you focusing on to maintain and accelerate this growth?
A major effort is underway at our factory in Taiwan, where we have been doubling the size of our footprint and hiring people as quickly as possible to meet demand. We are focusing on expanding production capacity while maintaining exceptional product quality. Another critical focus is building our service team.
We sell hundreds of plasma machines for a single application. They all have to run the same process at the same speed, and have no defects.These machines must operate 24 hours per day, 7 days a week for years, and require maintenance only once per year.
We need to keep our machines up and running 99% of the time. Excellent service and support is crucial to our success. If anything goes wrong with the equipment, we immediately bring it back online and support the customer’s production.
So, three things are key for us: growing production, focusing on quality, and expanding service and support.
Process cleanliness is crucial in semiconductor manufacturing. How does your atmospheric plasma technology meet client expectations while adhering to the stringent standards required in this field?
This has been a tough challenge, and we have spent many years improving this product. It was quite difficult to meet all the required properties, bring it to atmospheric pressure, and develop a tool that could meet the demands of this industry, which are by far the most stringent in the world.
Over the years, we have probably spent $50 million on R&D, developing and perfecting our product. We practice continuous improvement, so we are always making the plasma machine better. I believe it is about 99% there, but improvements can always be made.
One aspect that distinguishes our plasma from any other used in the semiconductor industry is our powerful hydrogen and argon plasma, which remove oxidation from tin or indium solder bumps. This is unique and cannot be done in by vacuum plasma.
In flip-chip and advanced packaging, where there are high densities of interconnects across a 2D pattern, our hydrogen plasma cleans and prepares the surface for thermocompression bonding in a way that no other technology can, completely free of residues. This is a game changer for the industry, especially for advanced computing applications.
Could you highlight some of the high-profile applications where your technology has had a significant impact?
Medical diagnostics is another important area for us, and we have many systems in production there. In these applications, such as testing for infectious diseases using a very small drop of blood, specific proteins need to be bound to a surface in a way that allows the detection of a signal when the microorganism binds to that protein.
Our plasma can clean and activate a surface to absorb protein in exactly the right way. This is a very precise and fine surface process, and our plasma performs better than anything else on the market. As a result, a Fortune 500 drug company uses our plasma in production to make these advanced diagnostics.
Are there particular markets that you see as key to your future success?
Our primary focus is the semiconductor industry, but we support other emerging markets.
One particularly interesting market is autonomous vehicles, such as ride-hailing services and flying air taxis. Flying air taxis are made of lightweight composites and powered by either batteries or hydrogen. Someday, there will be thousands of air taxis shuttling people around our cities. The makers of autonomous vehicles use our plasma to improve bonding during the assembly of the components and structures. It is a nascent industry right now, but in 10 years, it could be huge.
Where do you see Surfx in the coming decade? What do you see as the next milestone for Surfx as a company?
We are just getting started in semiconductor packaging applications. I anticipate this market will explode over the next few years, and Surfx wants to be a key equipment supplier.
The total market for our machines in this area is estimated to be between 2,000 and 5,000 machines. We are laser-focused on making this happen over the next five years and beyond.
About the Speaker
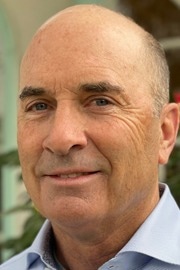
Dr. Robert Hicks received his B.S. in chemical engineering in 1977 from the University of Delaware, and his Ph.D. in 1984 from the University of California, Berkeley. In 1985, he joined the faculty of Chemical Engineering at UCLA and served there for 32 years. While a professor, Dr. Hicks founded Surfx Technologies in 1999. In 2017, he retired from UCLA to work full time as President and CEO of Surfx.
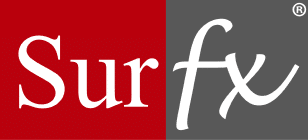
This information has been sourced, reviewed and adapted from materials provided by Surfx Technologies, LLC.
For more information on this source, please visit Surfx Technologies, LLC.
Disclaimer: The views expressed here are those of the interviewee and do not necessarily represent the views of AZoM.com Limited (T/A) AZoNetwork, the owner and operator of this website. This disclaimer forms part of the Terms and Conditions of use of this website.