Hydrogen energy is a renewable and clean energy source that is becoming central to the global energy transformation. The International Energy Agency report anticipates that the global hydrogen energy market will reach US$200 billion by 2030.
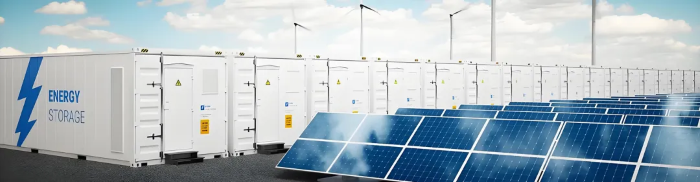
Image Credit: MICRO SENSOR CO., LTD
Hydrogen energy applications are employed in many fields, including industrial manufacturing, transportation, and energy storage. Hydrogen energy also has excellent potential for use in renewable energy storage and fuel cell vehicles.
The application of hydrogen energy faces numerous technical challenges. Its extremely high explosiveness and diffusivity mean that its production, storage, and transportation require highly specialized equipment. Hydrogen’s safe and reliable measurement has become a central requirement for the hydrogen energy industry.
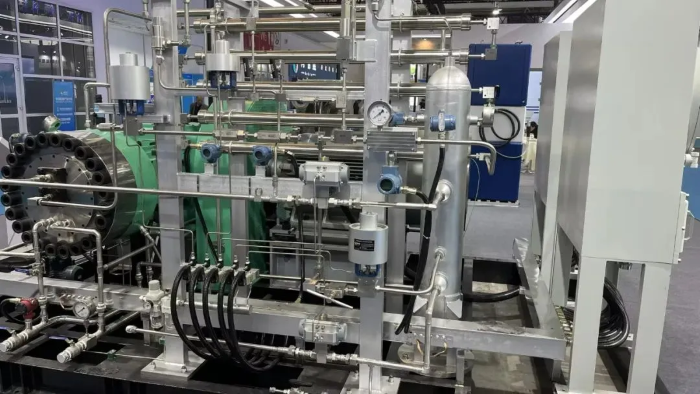
Application Site of a Hydrogen Energy Customer. Image Credit: MICRO SENSOR CO., LTD
Hydrogen Production via Water Electrolysis
In the electrolyzer, pressure transmitters monitor the hydrogen and oxygen levels to maintain stability and ensure the safety of the electrolysis process.
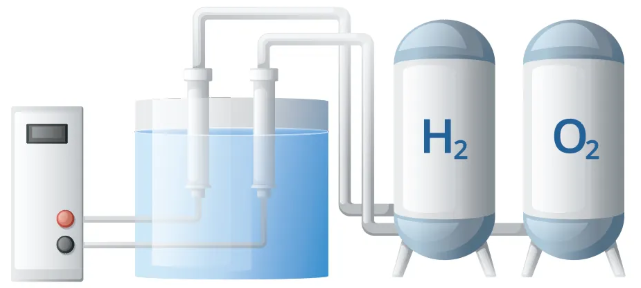
Image Credit: MICRO SENSOR CO., LTD
Challenges
There are several distinct challenges associated with this method of hydrogen production:
- Pressure in the electrolyzer increases during electrolysis, meaning the transmitter should operate normally under high-pressure conditions.
- As the electrolyte is corrosive, the transmitter must be manufactured from robust material and be fully sealed.
- The transmitter must offer stable performance, even when temperature changes occur.
- Highly accurate pressure measurement ensures a water electrolysis hydrogen production system operates safely and efficiently.
- The transmitter must function adequately over long periods to minimize maintenance costs.
Solutions
Micro Sensor’s transmitters represent the ideal solution to these challenges:
- The company’s instruments employ overpressure technology and are manufactured from highly durable materials, making them ideal for accurate measurement under high-pressure conditions.
- The transmitter is manufactured from corrosion-resistant materials, including stainless steel, special alloys, and a specialized gold-plated coating. These materials improve corrosion resistance and extend the transmitter’s working life.
- The transmitter’s wide temperature range and temperature compensation functionality assure stable and reliable measurement data.
- The transmitter leverages advanced sensing technology and high-precision calibration to ensure consistently accurate data.
- The transmitter’s high-quality components and optimized structural design ensure a low failure rate and reduced maintenance costs.
Products
- Smart pressure transmitters
- Temperature transmitters
Hydrogen Production from Natural Gas Reforming
When producing hydrogen via natural gas reforming, pressure transmitters are employed in the reactor and separation equipment. Their role is to monitor pressure changes and optimize reaction conditions to improve the efficiency of the hydrogen production process.
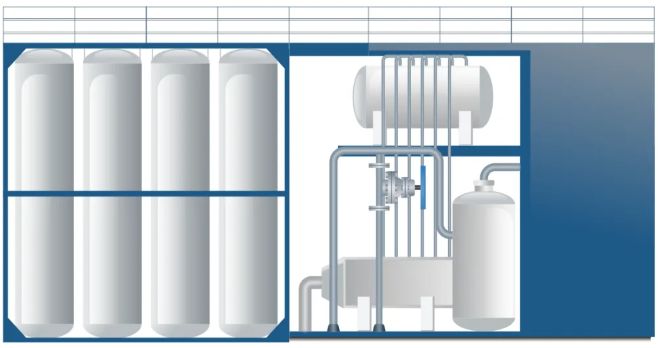
Image Credit: MICRO SENSOR CO., LTD
Challenges
Challenges associated with this method of hydrogen production include:
- The measuring instrument must operate normally in the high-temperature environment found in the natural gas reforming reactor.
- Because the natural gas reforming process operates at high pressure, the measuring instrument must provide accurate data even in this high-pressure environment.
- Corrosive gases and liquids are common in reforming, so the measurement instrument must offer good corrosion resistance.
- Hydrogen production requires responsive, highly accurate data to optimize process parameters.
- The transmitter should guarantee long-term, stable operation to minimize maintenance costs.
Solutions
Micro Sensor’s transmitters offer a robust solution to these challenges:
- Micro Sensor instrumentation features temperature-resistant materials and advanced high-temperature compensation technology, allowing the transmitter to offer consistent performance even in high-temperature environments.
- The measurement tool boasts a robust construction and a reliable design, ensuring accurate measurements even when operating in high-pressure environments.
- Corrosion-resistant materials and special coatings extend service life by allowing the instrument to withstand the effects of harsh media.
- High-accuracy, rapid-response sensing technology offers users accurate real-time pressure data designed to help optimize production processes.
- Micro Sensors’ measurement instruments offer long-term stability with minimal maintenance costs, thanks to their optimized design and high-quality components.
Products
- Pressure transmitters
- Mass flowmeters
High-Pressure Hydrogen Storage
Pressure transmitters monitor the pressure within hydrogen storage tanks to ensure it stays within safe limits, preventing overpressure incidents during storage.
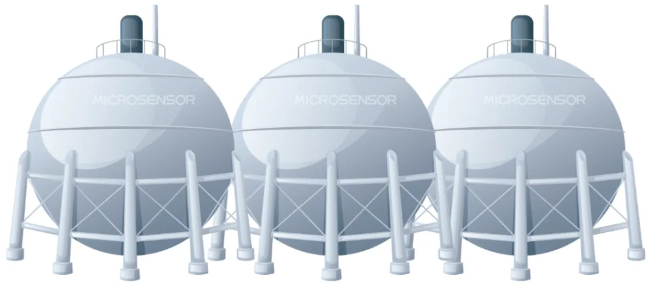
Image Credit: MICRO SENSOR CO., LTD
Challenges
Challenges associated with high-pressure hydrogen storage include:
- Oxygen tanks in hydrogen storage operate at high pressure, meaning the pressure transmitter must withstand high-pressure conditions while providing accurate measurement data.
- Hydrogen gas can diffuse through various materials. To avoid sensor failure, sensor housings must be as impermeable as possible.
- Temperature fluctuations may occur during the hydrogenation and dehydration processes. The pressure transmitter must accommodate these changes.
- High-pressure hydrogen storage tanks represent a potential explosion risk, meaning any pressure transmitter must feature sufficiently high safety standards and an explosion-proof design.
- Pressure transmitters in high-pressure hydrogen storage tank systems must reliably operate for a long time and have minimal maintenance requirements and costs.
Solutions
Micro Sensor’s transmitters offer an appropriate solution to these challenges:
- Micro Sensor’s pressure transmitters can withstand overpressure thanks to their robust construction and advanced sensing technology. These features are central to their accurate measurement capabilities and infallibility.
- The sensor's long-term stability is assured due to its use of low-permeability gold-plated materials, stainless steel, specialized alloys, and advanced sealing technology.
- Wide-range temperature compensation functionality ensures accurate measurement data, even during temperature fluctuations.
- The transmitter features numerous stringent safety protocols and robust explosion-proofing, guaranteeing safe operation under high pressure. The instrument adheres to strict safety and explosion-proof standards.
- The instrument’s use of high-quality components and optimized design ensures a reduced failure rate and minimal ongoing costs.
Products
Smart pressure transmitters
Liquid Hydrogen Storage
Pressure transmitters are used in cryogenic liquid hydrogen storage tanks to monitor the pressure inside the tanks and ensure that liquid hydrogen is stored as safely as possible.
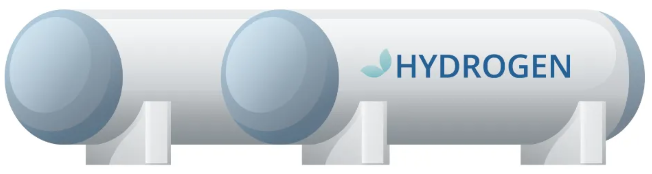
Image Credit: MICRO SENSOR CO., LTD
Challenges
Challenges associated with liquid hydrogen storage include:
- Liquid hydrogen is stored at extremely low temperatures, meaning the pressure transmitter must function under these conditions.
- Liquid hydrogen storage systems may operate in high-pressure environments. The pressure transmitter must tolerate these environments while maintaining measurement accuracy.
- Hydrogen's ability to permeate various materials may lead to deterioration and leakage risks. The pressure transmitter must be housed in materials that withstand these conditions.
- Pressure readings for liquid hydrogen storage systems should be rapid and accurate, allowing staff to respond to any changes as quickly as possible.
- Pressure transmitters in liquid hydrogen storage systems must run continuously with minimal maintenance requirements and related expenses.
Solutions
Micro Sensor’s transmitter offers an appropriate solution to these challenges:
- The Micro Sensor pressure transmitter maintains steady performance even at extremely low temperatures, thanks to its use of low-temperature sensing technologies and temperature-resistant materials.
- The transmitter leverages a combination of high-strength materials and cutting-edge pressure-sensing technology to ensure accurate measurements even in high-pressure environments.
- The transmitter uses advanced sealing technology and gold-plated materials with low hydrogen permeability to prevent hydrogen from damaging its internal components.
- Rapid reaction times and accurate sensor technology facilitates the delivery of precise pressure data in real-time, supporting ongoing optimization of transit and storage procedures.
- The transmitter’s low failure rates and minimal maintenance expenses assure reliable long-term performance. Premium components and an optimal design make these features possible.
Products
- Smart pressure transmitters
- Temperature transmitters
Hydrogen Pipeline Transportation
Pressure transmitters installed along the hydrogen pipeline enable continuous pressure monitoring. This is key to promptly detecting leaks or anomalies and safely transporting hydrogen throughout the pipeline.
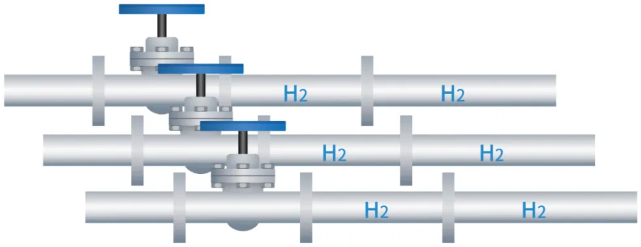
Image Credit: MICRO SENSOR CO., LTD
Challenges
Challenges associated with hydrogen pipeline transportation include:
- “Hydrogen embrittlement” and “hydrogen permeation” are common issues along the hydrogen transportation pipeline.
- Hydrogen has incendiary and explosive properties, meaning extra care must be taken.
- There are strict safety and regulatory guidelines around pipeline sealing and measurement accuracy.
Solutions
Micro Sensor’s transmitters address these challenges by:
- Employing a diaphragm with gold plating designed to help avoid hydrogen embrittlement.
- Offering outstanding precision and robust sealing performance.
- Leveraging an explosion-proof circuit specifically designed for use in dangerous environments.
Products
- Smart pressure transmitters
- Mass flowmeters
Hydrogen Transport Vehicles
Pressure transmitters are used in hydrogen transport vehicles’ hydrogen storage tanks to monitor pressure inside the tanks and ensure safety during transportation.
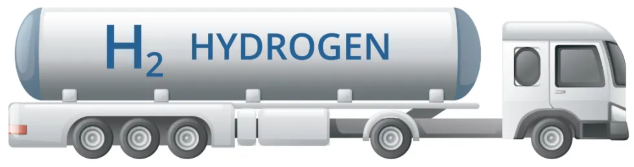
Image Credit: MICRO SENSOR CO., LTD
Challenges
Several challenges are associated with hydrogen transport vehicles:
- The pressure transmitter is required to function under high-pressure and high-temperature conditions.
- Vibrations and movement during transportation may present measurement challenges. Despite these, the pressure transmitter must provide accurate data.
- High-pressure hydrogen storage requires any pressure transmitter in this setting to adhere to strict safety standards.
Solutions
Micro Sensor’s transmitters address these challenges by:
- Leveraging high-strength materials and advanced pressure-sensing technology to ensure accurate measurement, even in high-pressure and high-temperature environments.
- An anti-vibration design ensures stable performance when the vehicle is in motion, ensuring reliable pressure measurement in dynamic environments.
- The transmitter complies with relevant industry standards and certification requirements, and it has multiple safety protections to ensure normal operation under challenging conditions.
Products
- Pressure transmitters
- Temperature transmitters
Stationary Hydrogen Fuel Cell System
Pressure transmitters are employed in fixed hydrogen fuel cell power systems to monitor pressures during hydrogen storage and supply, ensuring safe operation.
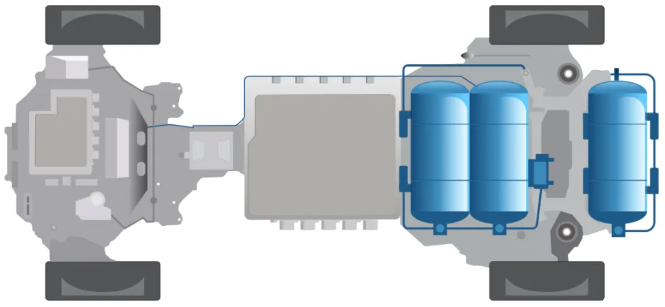
Image Credit: MICRO SENSOR CO., LTD
Challenges
A range of challenges are associated with stationary or fixed hydrogen fuel cell systems:
- Fixed hydrogen fuel cell systems rely on high-pressure hydrogen storage, which requires infallible pressure-sensing instrumentation.
- These fuel cell systems require measurement systems that offer long-term stability.
- Precise pressure control is essential in fixed hydrogen fuel cell systems.
- Strict safety requirements and stringent measurement standards are in place for pressure-monitoring systems used in stationary hydrogen fuel cell systems.
Solutions
Micro Sensor’s transmitters address these challenges by:
- Leveraging robust materials and powerful pressure-sensing technology to ensure accurate, reliable measurements under high-pressure conditions.
- Employing an advanced anti-vibration design to enable stable performance and accurate pressure measurement, even in dynamic working environments.
- Leveraging rapid response capabilities and high-accuracy sensing technology to monitor changes in pressure and optimize system operation.
- Ensuring strict safety standards are met, with relevant certification and a range of safety protocols.
- Using high-quality components and a highly optimized design for reliable, long-term, stable operation while minimizing maintenance costs.
Products
- Pressure transmitters
- Temperature transmitters
Hydrogen Fuel Cell Vehicles
Pressure transmitters are used in hydrogen fuel cell vehicles to monitor hydrogen pressure within the fuel cell stack, ensure stable hydrogen supply, and help optimize fuel cell operation.
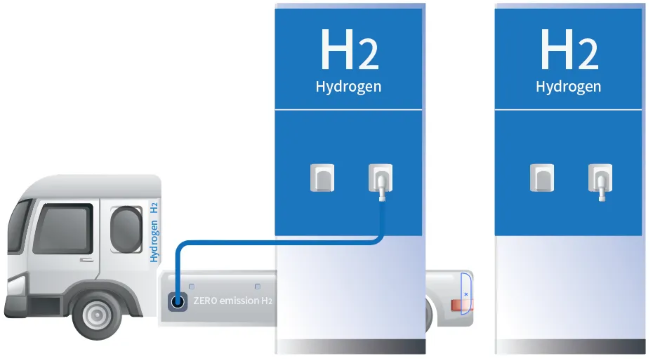
Image Credit: MICRO SENSOR CO., LTD
Challenges
A range of challenges are commonly found in hydrogen fuel cell vehicles:
- Fuel cell vehicles' high-pressure hydrogen storage requirements demand error-free, overpressure transmitters.
- The dynamic operating conditions associated with this application require pressure transmitters that are highly stable and vibration-resistant.
- Flammable hydrogen requires that strict safety standards be adhered to and reliable pressure monitoring is in place.
- Rapid response and accurate pressure data ensure a stable and efficient fuel supply.
- Long-term transmitter stability is necessary to minimize maintenance requirements and associated costs.
Solutions
Micro Sensor’s transmitters address these challenges by:
- Leveraging advanced pressure-sensing technology and durable materials to ensure infallible, accurate measurements even in high-pressure environments.
- Providing reliable pressure measurement under dynamic operating conditions, thanks to a highly stable, anti-vibration design.
- Adhering to establishing industry standards and complying with certification requirements, with a range of safety protections in place to ensure consistent operation.
- Employing rapid-response, highly accurate sensing technology to accurately monitor pressure changes in real-time.
- Leveraging an optimized design and high-quality components ensures stable operation in the long term and reduces maintenance costs.
Products
- Pressure transmitters
- Temperature transmitters
Hydrogen Filling Devices
Pressure transmitters are used within hydrogen filling devices to monitor hydrogen pressure during the filling process, enabling accurate pressure control while improving safety and efficiency.
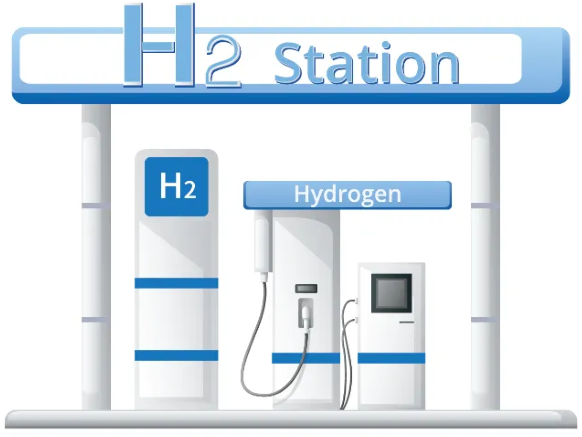
Image Credit: MICRO SENSOR CO., LTD
Challenges
A range of challenges are commonly found in hydrogen-filling devices:
- Hydrogen filling equipment requires accurate, reliable pressure transmitters to ensure safe, high-pressure filling.
- Rapid response and efficient measurement are key to meeting user demands for fast, efficient hydrogen filling.
- The strict safety standards associated with flammable hydrogen necessitate a dependable pressure-monitoring system.
- Stable filling pressure is necessary to ensure full charging of a hydrogen storage system.
Solutions
Micro Sensor’s transmitters address these challenges by:
- Combining high-accuracy sensing technology and a comprehensive pressure control algorithm ensures safe hydrogen filling, even when working under high-pressure conditions.
- Rapid response and high-sensitivity monitoring of pressure changes are key to efficient filling processes.
- Adherence to strict safety standards, complete with a range of safety protections and compliance with relevant certification.
Products
- Pressure transmitters
- Temperature transmitters
- Mass flowmeters
Hydrogen Refueling Station Safety Monitoring System
Hydrogen storage tanks and refueling equipment pressure must be continuously monitored with appropriate pressure transmitters to prevent accidents caused by pressure anomalies.
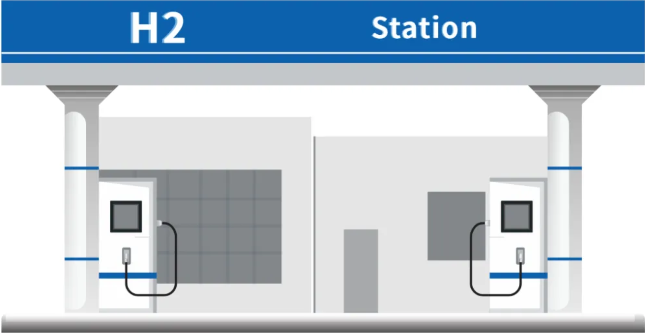
Image Credit: MICRO SENSOR CO., LTD
Challenges
A range of challenges are commonly associated with hydrogen refueling stations:
- High-pressure hydrogen refueling stations require precise, dependable pressure transmitters.
- Sensitive, responsive leak detection is essential in maintaining station and environmental safety.
- The real-time monitoring assures stable, safe operation of station equipment and piping.
- Data acquisition, storage, and analysis are central considerations when optimizing performance and improving safety.
Solutions
Micro Sensor’s transmitters address these challenges by:
- Leveraging advanced, accurate sensing technology and pressure control algorithms to ensure safe hydrogen filling under even high-pressure conditions.
- The ability to rapidly trigger alarms and safety measures once the instrument detects an abnormal pressure drop.
- The capacity to help detect abnormalities in real time, prompting staff to take corresponding measures.
Products
- Pressure transmitters
- Temperature transmitters
- Mass flowmeters
Summary
Micro Sensor's pressure transmitters are used in various applications throughout the hydrogen energy chain. The company’s sensors are key to ensuring the stability of hydrogen fuel cells, storage, transportation, and production.
All the company’s instruments offer strict explosion-proof certifications and have been subjected to robust corrosion resistance testing. This ensures safe operation in hazardous situations and mitigates the risk of accidents related to excessive pressure.
Materials used in constructing Micro Sensor's pressure transmitters are high-quality and high-strength, affording them exceptional wear and impact resistance and the ability to function reliably in the face of harsh impact and high-frequency vibration.
About Us
Since its founding in 1971, Micro Sensor Co., Ltd. has focused on researching and manufacturing piezo-resistive pressure sensors. With over 50 years of experience in design, development, and production, the company has become a leading player in China’s semiconductor piezo-resistive pressure sensor industry.
Micro Sensor offers a wide range of products, including pressure sensors, pressure transmitters, level transmitters, temperature transmitters, and flow meters. Serving more than 20,000 customers across over 100 countries and regions, the company specializes in providing customized solutions for various industries.
With its strong technical expertise and extensive industry experience, Micro Sensor delivers high-quality sensor solutions for the hydrogen energy sector. Its measuring instruments are critical to hydrogen production, storage, transportation, and application. Through continuous innovation and R&D, Micro Sensor is committed to driving global energy transformation and promoting sustainable development.
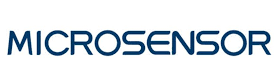
This information has been sourced, reviewed and adapted from materials provided by MICRO SENSOR CO., LTD.
For more information on this source, please visit MICRO SENSOR CO., LTD.