Battery material scientists focus on developing new materials and improving existing ones to address the challenges associated with cell performance, such as capacity fade, thermal stability, and cycle life. This work requires researchers to investigate the behavior of lithium when the batteries age and the consequent formation of dendrites.
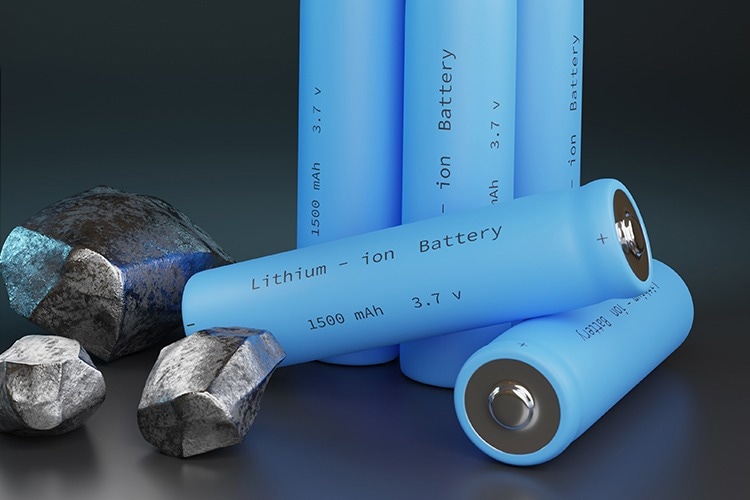
Image Credit: Juan Roballo/Shutterstock.com
The Importance of Lithium Metal in Battery Functionality
Many consider lithium metal to be the most crucial material for negative electrodes in lithium-based batteries. This is because it has an extremely high capacity to store energy—3,860 mAh g−1—which is much higher than the graphite currently used in batteries. Additionally, lithium is the most electropositive metal.
When lithium metal is paired with high-capacity cathodes—whether they use lithium insertion materials or conversion chemistries or are applied in a solid-state design—it can significantly boost the battery’s energy density.1,2,3,4,5
Microstructure Formation During Battery Cell Cycling
One of the challenges in using lithium metal directly as an anode lies in the formation of mossy and dendritic structures during battery cycling. This leads to low efficiency, continuous consumption of the electrolyte due to unwanted side reactions, growth of a solid electrolyte interphase (SEI), and irreversible capacity loss.6,7,8 These problems occur during both charging (when lithium is plated) and discharging (when lithium is stripped), resulting in an unstable electrode structure.
When the battery charges, lithium deposits unevenly, creating sparse and dendritic structures. The rapid growth of these lithium structures can cause internal short circuits or even lead to the battery overheating.9,10
During discharge, the unstable structures formed during plating can collapse, creating isolated lithium areas encapsulated by the SEI. These isolated areas, known as "dead lithium," are disconnected from the main electrode and no longer participate in the battery's electrochemical processes.11 For that reason, understanding how lithium microstructures form and evolve during charging and discharging is essential for guiding the use of lithium metal anodes in next-generation batteries.
Various strategies have been developed to control the microstructure of lithium during cycling and reduce the formation of inactive lithium. However, the formation of an ideal microstructure of lithium able to achieve over 99.9 % coulombic efficiency, which is a key standard for the long-term cycling of lithium metal batteries, has not yet been accomplished.
3D Reconstruction Showcases Evolution of Lithium Microstructures
Researchers from the Chalmers University of Technology in Sweden used X-ray tomographic microscopy (XTM) technology to capture lithium microstructures.12 They then used Thermo Scientific™ Avizo™ Software to analyze all of the collected tomograms. Segmentation of lithium phases in the reconstructed tomograms allowed the researchers to monitor the changes in individual microstructures during plating and stripping.
These advantages helped the researchers identify lithium, quantitatively track the spatial distribution of deposited lithium over time, and observe the formation of dead lithium during the plating and stripping processes.
3D renderings of the segmented lithium provided insights into structural connectivity and growth mechanisms of lithium microstructures (Fig.1). After plating, the tomograms showed that several separated regions formed at low current density.
At high current density, the lithium was almost entirely connected, except for a few residual inactive structures. This indicates improved connectivity at higher current density. Inactive lithium structures persisted after two cycles. The segmented lithium volume shows the evolution of microstructures, with an initial increase in surface area during plating due to rapid growth of surface followed by a decrease of surface, probably due to the integration of lithium microstructures.
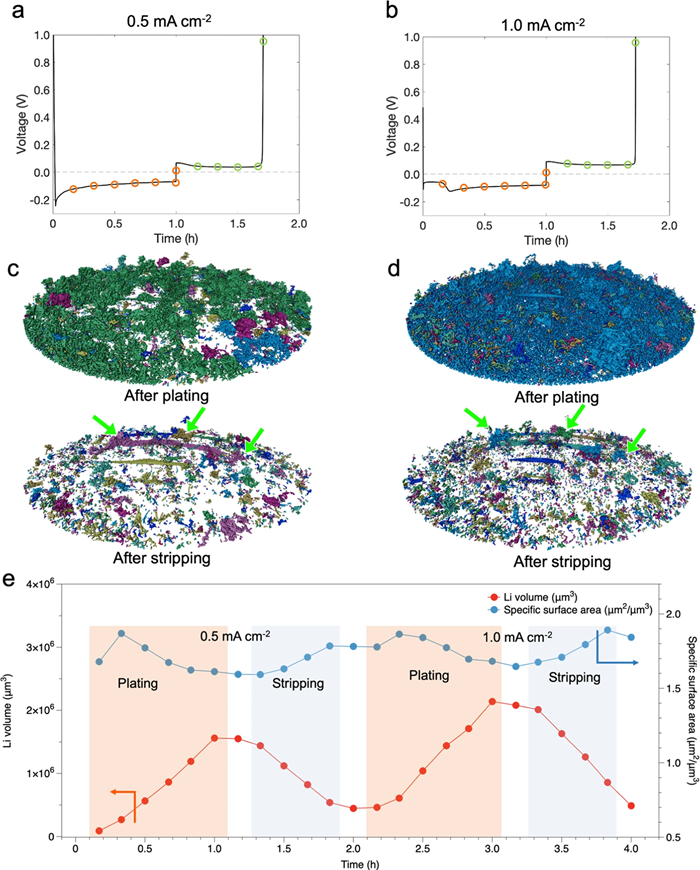
Fig.1: 3D renderings of segmented lithium. a, b Voltage profiles for galvanostatic plating and stripping during operando XTM are shown at 0.5 mA/cm-2 for the first cycle (a) and 1.0 mA/cm-2 for the second cycle (b). Circles mark the points where X-ray tomograms were captured. Orange denotes the plating process, while green indicates the stripping process. c, d 3D renderings display segmented lithium and identify isolated regions in distinct colors. Green arrows highlight regions of inactive lithium. Different colors, such as dark blue, light blue, dark green, light green, and purple, represent various separated lithium regions. e The volume and surface area of deposited lithium during plating and stripping cycles are shown. The white spaces between colored areas indicate the points at which tomograms were taken after the plating or stripping process. Image Credit: Nature Communications (Nat Commun) ISSN 2041-1723 (online)
Reconstructed 3D tomograms were also used to study the integration of mossy and needle-like structures (Fig.2).
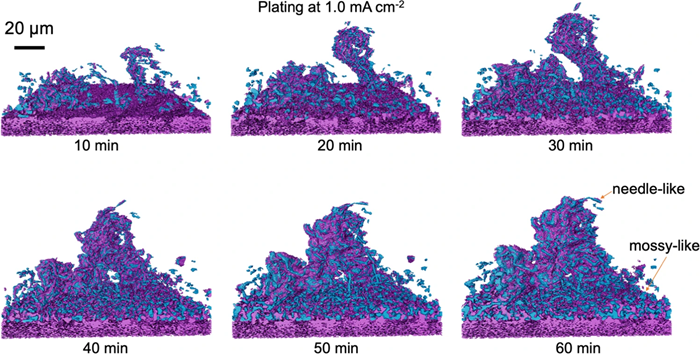
Fig.2: Formation of lithium dendrite and mossy structures. Renderings are derived from tomograms captured during plating at 1.0 mA/cm-2 for 10, 20, 30, 40, 50, and 60 minutes. Lithium is depicted in blue, with purple representing SEI or high-atomic-number components covering the lithium and purple at the bottom indicating the copper substrate. Image Credit: Nature Communications (Nat Commun) ISSN 2041-1723 (online)
Specifically, during lithium plating at a current density of 1.0 mA/cm-2, a single lithium cluster grew quickly but became more likely to collapse as it got longer. At the same time, mossy-like lithium spread across the surface and thickened. After 40 minutes, the isolated lithium cluster connected with the mossy layer, creating a stronger and more stable structure.
This work enabled the researchers to monitor the real-time evolution of internal lithium structures. This breakthrough is pivotal—it underscores the necessity of avoiding mossy and needle-like lithium formations in batteries due to their significant safety hazards.
Looking ahead, this innovative workflow has the potential to revolutionize the study of microstructure formation and progression in other metal anodes, including sodium (Na), zinc (Zn), and magnesium (Mg) batteries. By analyzing the geometry, connectivity, and electrochemical activity of lithium structures under various conditions, we are paving the way for the development of safer, high-performance lithium metal batteries.
Advanced Imaging and Analysis with Thermo Fisher Scientific's Avizo Software
Advanced XTM technology generates substantial amounts of diverse data. Image processing software is essential for effectively interpreting and understanding this information. It offers a more comprehensive perspective and numerical quantification of the features being studied.
Avizo Software13 offers a range of visualization and imaging data analysis tools to generate a comprehensive picture of the analyzed material. Avizo Software is engineered to streamline and automate numerous intricate steps in image processing and analysis.
In the work discussed here, the researchers used Avizo Software’s segmentation tools to generate 3D volume renderings and its quantitative tools to calculate the surface and volume of the lithium microstructures.
Video Credit: Thermo Fisher Scientific - Software
Watch on-demand: How to automate battery quality inspection with image interpretation
References and Further Reading
- Tarascon, J. M. & Armand, M. Issues and challenges facing rechargeable lithium batteries. Nature 414, 359–367 (2001).
- Xue, W. et al. Ultra-high-voltage Ni-rich layered cathodes in practical Li metal batteries enabled by a sulfonamide-based electrolyte. Nat. Energy 6, 495–505 (2021).
- Lee, Y.-G. et al. High-energy long-cycling all-solid-state lithium metal batteries enabled by silver–carbon composite anodes. Nat. Energy 5, 299–308 (2020).
- Varzi, A., Raccichini, R., Passerini, S. & Scrosati, B. Challenges and prospects of the role of solid electrolytes in the revitalization of lithium metal batteries. J. Mater. Chem. A 4, 17251–17259 (2016).
- Xu, X. et al. Electro–chemo–mechanical failure of solid electrolytes induced by growth of internal lithium filaments. Adv. Mater. 34, 2207232 (2022).
- Yoshimatsu, I., Hirai, T. & Yamaki, J. I. Lithium electrode morphology during cycling in lithium cells. J. Electrochem. Soc. 135, 2422–2427 (1988).
- Liu, J. et al. Pathways for practical high-energy long-cycling lithium metal batteries. Nat. Energy 4, 180–186 (2019).
- Wood, K. N., Noked, M. & Dasgupta, N. P. Lithium metal anodes: toward an improved understanding of coupled morphological, electrochemical, and mechanical behavior. ACS Energy Lett. 2, 664–672 (2017).
- Cheng, X. B., Zhang, R., Zhao, C. Z. & Zhang, Q. Toward safe lithium metal anode in rechargeable batteries: a review. Chem. Rev. 117, 10403–10473 (2017).
- Xu, W. et al. Lithium metal anodes for rechargeable batteries. Energy Environ. Sci. 7, 513–537 (2014).
- Fang, C. C. et al. Quantifying inactive lithium in lithium metal batteries. Nature 572, 511–515
- Sadd et al. Investigating microstructure evolution of lithium metal during plating and stripping via operando X-ray tomographic microscopy. Nature Communications 14, 854 (2023)
- Avizo Software for battery and energy materials characterization
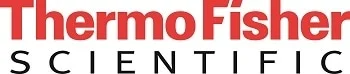
This information has been sourced, reviewed and adapted from materials provided by Thermo Fisher Scientific - Software.
For more information on this source, please visit Thermo Fisher Scientific - Software.