If you want to test the vibration behavior of an object that does not vibrate on its own, you must excite it externally. For modal tests, an electromagnetic shaker and a modal hammer are standard broadband excitation equipment that has been used for many years.
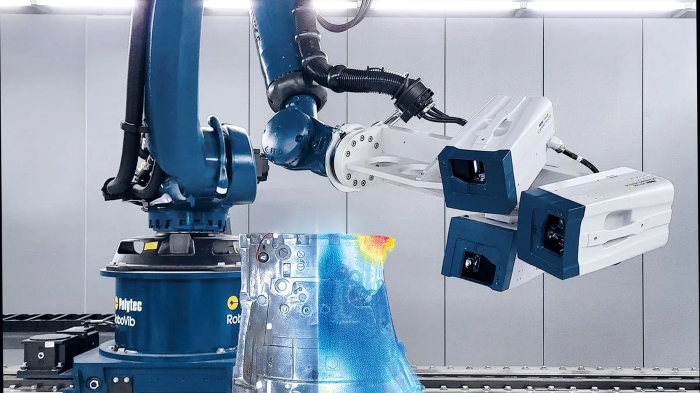
Image Credit: Courtesy of the authors
A hammer impact must be repeated for each scan point to measure points consecutively with a Polytec Scanning Laser Vibrometer. As a result, automated modal hammers such as the SAM, developed by NV-Tech, have gained popularity in recent years.
Both existing excitation methods have advantages and disadvantages. An electrodynamic shaker allows for speedier measurements at multiple spots and reliable test results. However, a shaker equipped with a force sensor might have a significant impact on the structure being tested.
Setting up and aligning the shaker, as well as maintaining alignment, is time-consuming, particularly on test setups where the sample is supported by soft rubber strings or soft foam to simulate free-flowing circumstances.
An (automatic) hammer, on the other hand, does not affect the part's intrinsic dynamic qualities, making it an excellent choice for relatively lightweight and weakly damped structures.
Because of the decay time after each impact, measurements take much longer, and for lightweight samples held by soft rubber strings, significant swaying may occur in the entire sample.
Combining Strengths
Recently, a third excitation method has emerged, addressing the shortcomings of the methods above: Qsources provides inertial shakers with integrated force transducers. These shakers offer unique qualities, including a self-aligning internal suspension, a low mass, and simple handling and alignment.
Because they are affixed to the structure, their location is set, and they do not have to wait like with automated hammers. On the downside, they only perform well over a particular cutoff frequency and load the structure like an accelerometer with a cable does.
In this article, the Qlws inertial shaker was tested and compared to a traditional shaker and an automated modal hammer.
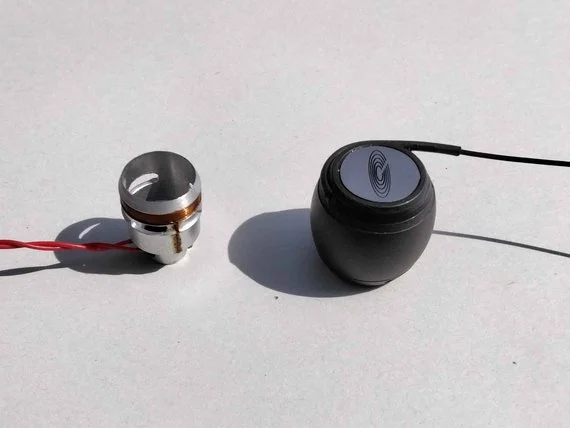
Figure 1. The Qlws components. Image Credit: Courtesy of the authors
Use of the Qlws Lightweight Inertial Shaker
The Qlws itself consists of two small pieces, plus an amplifier:
- A "force cup" houses the voice coil. It is affixed to the object being tested.
- The shaker body contains an inertial mass and a force sensor. It is simply pushed over the force cup.
A small layer of grease is employed for dynamic decoupling, resulting in a dynamically active mass of less than 2 g above 200 Hz.
Attaching the Qlws is simple: clean the sample with alcohol, glue the force cup with fast glue, apply a small layer of grease, slip the shaker body over the force cup, and connect the cables to the amplifier box and a data-gathering device with an IEPE power supply.
The gadget self-aligns in any inclination, eliminating the need for stinger alignment.
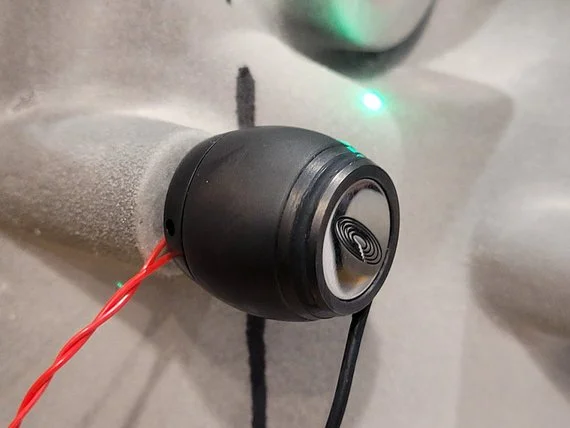
Figure 2. The Qlws inertial shaker mounted to the DUT. Image Credit: Courtesy of the authors
Comparison Test
The comparison was performed on a 1.5 mm thick aluminum plate hung by elastic bands. This plate is powered by a traditional modal shaker, an automated hammer "SAM 1," and the Qsources Qlws. A Polytec non-contact PSV Laser Scanning Vibrometer detects vibration behavior without affecting the test object.
The images below depict the electrodynamic shaker (LDS shaker), the automatic hammer (NV-Tech SAM), and the inertial shaker (Qsources Qlws):
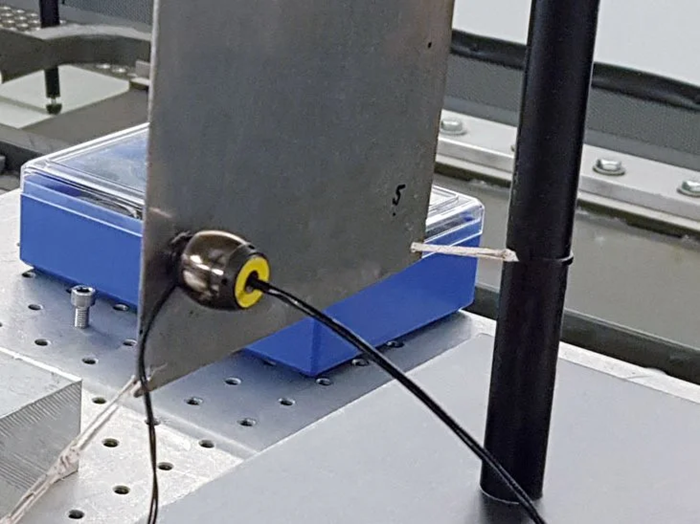
Intertial Shaker (Qsources Q/ws). Image Credit: Courtesy of the authors
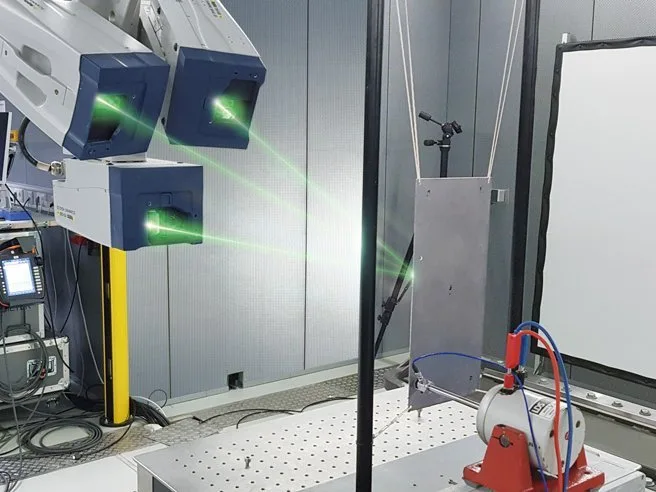
Electrodynamic Shaker (LDS shaker). Image Credit: Courtesy of the authors
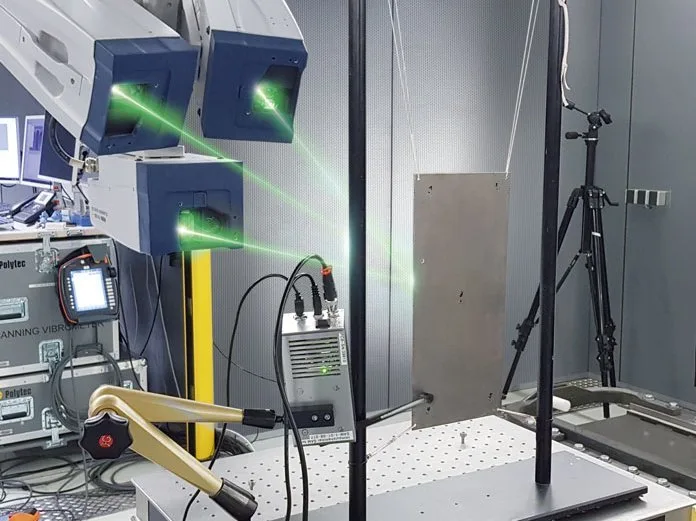
Automatic hammer (NV-Tech SAM). Image Credit: Courtesy of the authors
The LDS shaker immediately appears to have too much influence on the light test object: resonance frequencies shift, and the force spectrum drops dramatically, resulting in a poor signal-to-noise ratio at the response-excitation transfer function.
The standard modal shaker is, therefore, unsuitable for this arrangement and should only be used for heavier samples where it excels.
The NV-Tech SAM automated hammer is the standard for mass loading the test object because nothing is permanently attached to the structure. As a result, it is the optimal excitation source for objects with low damping. Its frequency range is likewise expanding to lower values.
There is, however, a disadvantage to the very light suspended test sample: It causes swinging of the suspended sample. This, combined with the use of a scanning vibrometer, produces needless noise in the data.
The vibrometer's inclusion of the latest Polytec QTec® technology can help limit this effect, but macroscopic swaying will still decrease the signal-to-noise ratio.
Swaying also extends the test time because the user must wait before the next automated hit can be applied. If swaying is avoided (for example, if sample support on soft foam is appropriate), the hammer remains an excellent choice for objects with little damping and a wide range of frequencies.
Because of its low dynamic mass, the Qsources Qlws has just a minor impact on the sample's natural behavior. When properly situated, coupling the shaker to the test-object eigenfrequencies has very little effect, comparable to suspending the test object, for frequencies below 2 kHz, which covers the first 15 - 20 resonances.
There is no waiting time between excitation sequences, allowing the test to run much faster. The sole negative discovered throughout the test was a low-frequency constraint below 250 Hz.
It does not imply that the shaker is ineffective at lower frequencies; rather, because of the higher effective dynamic mass, it has a somewhat greater influence on the sample's natural behavior at lower frequencies.
Figure 3 depicts typical SAM hammer (left) and Qlws (right) results in this arrangement.
The Main Results Are:
- Resonance frequencies and deflection geometries are nearly comparable between 200 and 2000 Hz.
- The inertial shaker has limited influence below 200 Hz and above 2 kHz.
- The deflection curve clearly shows the increase in loudness induced by hammer impact and swaying.
- The automated hammer measurement took around 2.5 hours compared to 0.5 hours with the Qlws.
- Even a modest traditional electrodynamic shaker with a stinger and force sensor is ineffective for this type of material.
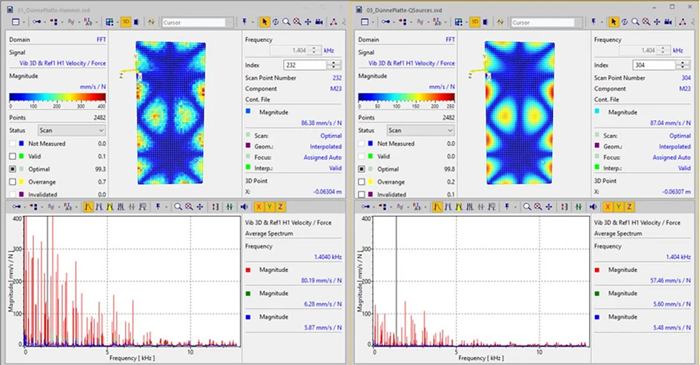
Figure 3. Deflection shapes and FRF (left: modal hammer, right: Qlws). Image Credit: Courtesy of the authors
Resume
To summarize, the Qsources Qlws shaker is a highly intriguing alternative to an automated modal hammer since it causes no swaying of the test item, which reduces the signal-to-noise ratio for single-channel vibration meters without Polytec QTec® technology.
Because this additional noise may be corrected using multi-channel QTec® Scanning Vibrometers, both the inertial shaker and the automated hammer produce test data at the same level. Limitations may include the lower frequency limit of the Qlws and the increased mass for exceptionally lightweight or low-damped samples.
The Qlws arrangement is incredibly convenient; it is as simple as an automated hammer, has good repeatability, and is faster and easier to use than a traditional shaker with a stinger. Because there is no waiting period between hits, measurement times for suspended samples can be significantly reduced.
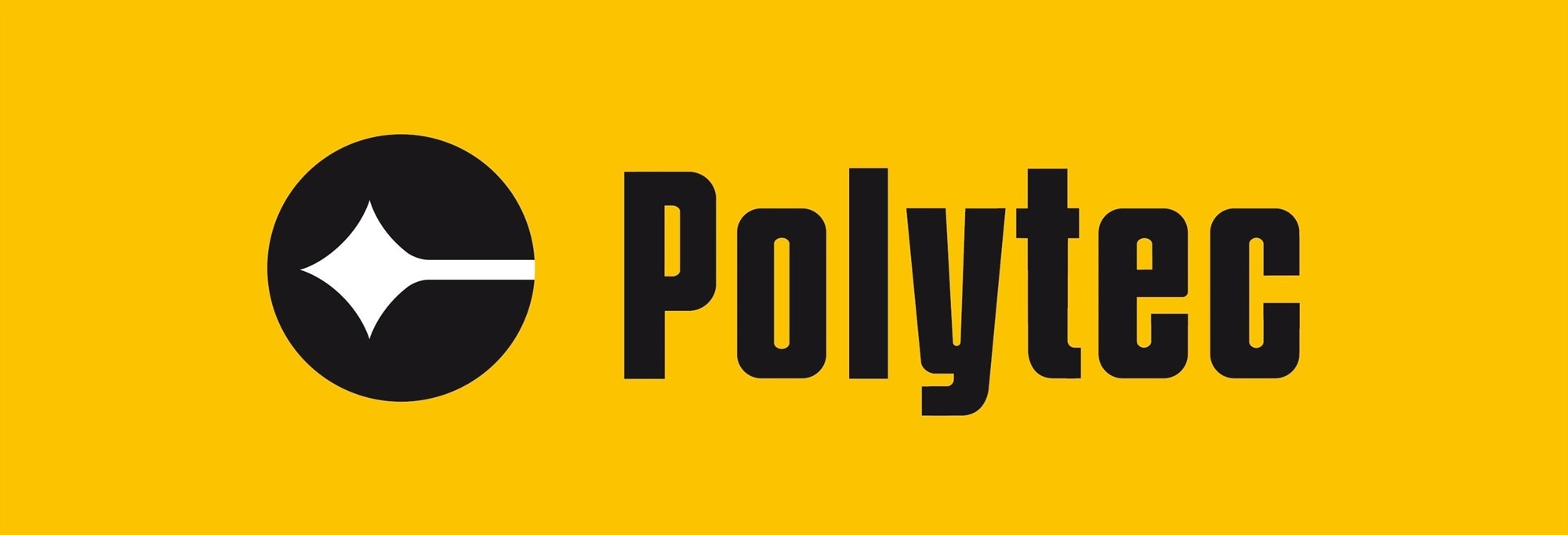
This information has been sourced, reviewed and adapted from materials provided by Polytec.
For more information on this source, please visit Polytec.