Clean room maintenance requires absolute control over contamination risks. Differential pressure monitoring is fundamental to this control, managing airflow to actively keep airborne particles in check.
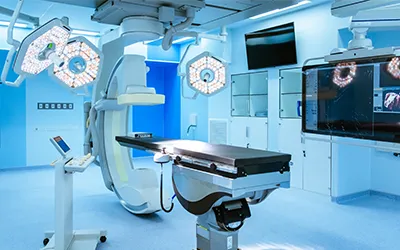
Image Credit: Superior Sensor Technology
This technology helps block contaminants from entering or leaking out of clean rooms in biotechnology, pharmaceutical, and semiconductor manufacturing settings, preserving the sterile conditions these industries rely on.
Principles of Clean Room Pressure Control
Clean rooms employ differential pressure to generate controlled environments that prevent contamination by regulating air movement. Two key types of pressure control systems are employed in air quality management.
Positive Pressure
Clean rooms utilizing positive pressure maintain higher air pressure inside than the surrounding areas. Should a leak or opening occur, this approach ensures air flows outwards, preventing any external contaminants from entering the clean room.
Positive pressure is vital in pharmaceutical production or semiconductor manufacturing industries, where even microscopic contamination could compromise product quality.
Negative Pressure
Negative-pressure clean rooms maintain lower pressure inside than outside, preventing potentially dangerous contaminants from escaping into the surrounding environment.
These clean rooms are often seen in healthcare settings, such as isolation rooms or laboratories working with dangerous pathogens, where ensuring hazardous substances remain contained is necessary.
The Role of Differential Pressure Sensors
Differential pressure sensors are central to maintaining these pressure differentials. They have been specifically designed to precisely measure pressure differences between the clean room and adjacent areas.
Modern sensors detect fluctuations in pressure as low as 0.5 Pa, facilitating real-time monitoring and implementing automated control systems that can adjust airflow as required.
Differential pressure sensors offer numerous vital functions, including:
- Detecting minute pressure changes, typically in the 0.5 to 15-Pa range.
- Continuously maintaining ideal pressure levels via ongoing pressure monitoring.
- Alarm triggering to notify personnel of equipment failures or system breaches.
- Automatically adjusting HVAC systems to correct any pressure imbalances rapidly.
These advanced sensors ensure clean rooms function optimally, mitigating potential hazards before they become significant safety risks.
Safety Enhancements Through Pressure Monitoring
Contamination Prevention
The core function of differential pressure monitoring in clean rooms is maintaining a robust barrier against contaminants.
Positive pressure environments must prevent the ingress of dust, microorganisms, and other airborne particles from less clean areas. This is key in industries like pharmaceuticals and biotechnology, where even trace contaminants could lead to product recalls due to compromised sensitive processes.
Semiconductor manufacturing requires extremely strict contamination control. The presence of microscopic particles could damage microchips or impact the performance of precision electronic components, so continuous monitoring of pressure levels is essential to ensure that these environments remain uncontaminated and product integrity is assured.
Hazard Containment
Pressure sensors help protect the external environment from dangerous materials in negative pressure rooms.
Facilities like biosafety labs that handle dangerous pathogens rely on negative pressure to ensure that if a breach occurs, any contaminants are drawn inward, away from the surrounding environment or any personnel.
This is essential to maintaining a safe working environment for laboratory staff and averting the spread of infectious agents.
Early Detection of Problems
The early detection of pressure imbalances can help prevent an array of serious issues, including:
- Clean room structural leaks
- HVAC system malfunctions
- Improper door sealing
- Air filter degradation
Differential pressure monitoring helps to detect and identify these issues early, enabling prompt corrective action and reducing the risk of equipment failure, contamination, or exposure to hazardous materials.
Regulatory Compliance
Stringent regulations regarding clean room standards are commonplace in many industries. Pharmaceutical companies must comply with the European Union and U.S. Food and Drug Administration’s good manufacturing practices, which outline strict guidelines around contamination control, air quality, and pressure differentials.
Accurate pressure monitoring is key to ensuring ongoing compliance with these regulations, avoiding the risk of penalties, and safeguarding product quality. Facilities can demonstrate adherence to these standards during audits or inspections.
Advanced Sensor Technology
Advances in differential pressure sensor technology have led to significant improvements in the efficiency and safety of clean room monitoring, including:
High Accuracy
Advances in sensor technology have led to more precise control of air pressure levels, facilitated by the detection of variances as small as 0.05% of the expected pressure.
Noise Reduction
Ground-breaking digital filtering technology can eliminate interference from vibration, temperature fluctuations, and other environmental factors, ensuring readings remain accurate, irrespective of changes in an HVAC system or surrounding area.
Rapid Response Times
More advanced sensors respond to changes in pressure within milliseconds. This enables the provision of real-time data, allows corrective actions to be taken immediately, and significantly reduces the risk of contaminant exposure.
These advances make pressure monitoring systems more efficient and reliable, improving the safety of clean room environments.
Selecting Clean Room Pressure Sensors
Differential pressure monitoring is essential in maintaining the safety and integrity of clean rooms and other controlled environments. Sensors that contain hazardous materials prevent contamination and enable the early detection of potential issues, ensuring clean rooms are safe and remain compliant with industry standards.
Sensor technology is constantly evolving, and these vital systems are anticipated to continue to become more precise. Applications across various industries can leverage sensor technology to maintain increased safety levels, protect workers and the surrounding environment from potential harm, and optimize processes to make them more efficient.
Superior Sensor Technology offers a comprehensive portfolio of advanced differential pressure sensors. The company’s sensors provide unparalleled accuracy and reliability for controlling and maintaining clean room safety levels.
Acknowledgments
Produced from materials originally authored by Superior Sensor Technology.
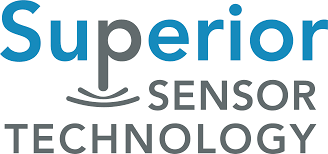
This information has been sourced, reviewed, and adapted from materials provided by Superior Sensor Technology.
For more information on this source, please visit Superior Sensor Technology.