Gelcoats provide a durable and reliable finish when handled appropriately, but faults may occur for several reasons. This article summarizes some common causes of gelcoat faults and their reasons.
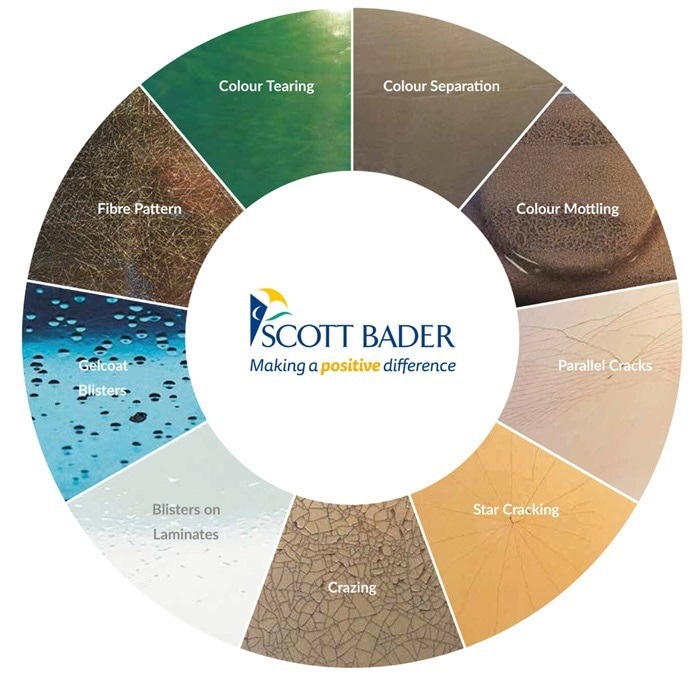
Image Credit: Scott Bader Company Ltd.
Color tearing:
- Long geltime or sagging
- The use of improper spray techniques
- Pigment becoming separated from resin
Color separation:
- Poor application of the gelcoat
- Drainage or sagging
- Insufficient mixing
Color mottling:
- The gelcoat being low in thixotropy
- Low viscosity
- Poor pigment compatibility
Parallel cracks:
- The laminate being too thin or flexible
- A thick gelcoat
- Flex cracking
Star cracking:
- The transfer of crack pattern from mold to surface
- The gelcoat being too thick
- Reverse impact
Crazing:
- Contamination
- Chemical attack
- Excess heat
Blisters on laminates:
- The presence of air voids
- Water ingress
- Damp reinforcement
Gelcoat blisters:
- Solvent contamination
- Unreacted catalyst
- Air voids on release
A fiber pattern:
- The gelcoat being too thin
- High exotherm in the laminate
- Insufficient cure, or the cure being released too soon
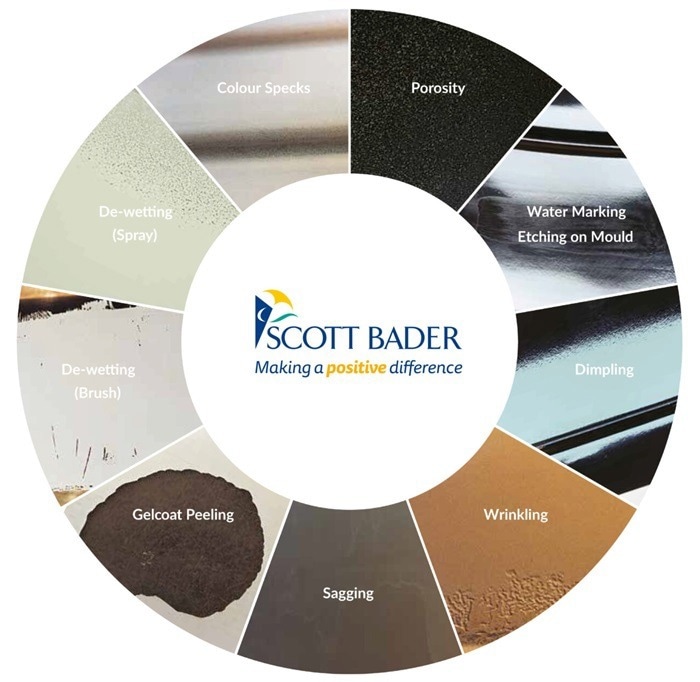
Image Credit: Scott Bader Company Ltd.
Color specks:
- Pigments being mixed or ground poorly
- Contamination
- Equipment being improperly maintained
Sagging:
- The gelcoat being too thick
- The geltime being too long
- Low viscosity or thixotropy
De-wetting (brush):
- The brush gelcoat being applied too thinly
- Use of an incompatible release system
- Contamination
De-wetting (spray):
- The spray gelcoat being applied too thinly
- Use of an incompatible release system
- Contamination
Wrinkling:
- The gelcoat being too thin
- The backup being too early
- Insufficient cure
Gelcoat peeling:
- The gelcoat being too fully cured
- Contamination
- The geltime being too long, resulting in the wax being dissolved
Watermarking or etching:
- Solvent attack
- Two colors being gelcoated on the mold
- Areas of thin, double gelcoating on the mold
Dimpling:
- Contamination
- Insufficient consolidation
- Too heavy wet-on-wet spray application
Porosity:
- The gelcoat being too viscous to adequately release air
- Gelling occurring too quickly, trapping air
- A cold gelcoat and/or mold
- The application of spray gelcoat with too high pressure or too low catalyst levels
Proper gelcoat application is key to minimizing these risks.
Acknowledgments
Produced from materials originally authored by Scott Bader Company.
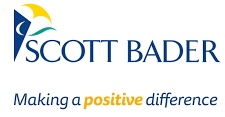
This information has been sourced, reviewed and adapted from materials provided by Scott Bader Company Ltd.
For more information on this source, please visit Scott Bader Company Ltd.