In this interview, McKinnon Ray, Senior Project Engineer at Jenike & Johanson, talks to AZoM about innovative feeder and hopper design solutions.
Can you briefly introduce yourself and explain how your background in chemical engineering and experience across different industries have shaped your expertise in solids handling operations?
My name is McKinnon Ray, and I am a senior project engineer with Jenike & Johanson. Before joining Jenike, I worked at Anheuser-Busch in its packaging and logistics departments. One could say I traded in "flow of liquids" for "flow of solids". I have a degree in chemical engineering from Mississippi State University. Like most new engineers, I had minimal experience in powder and solids handling design before joining Jenike.
At Jenike, I've had the opportunity to work on many solids handling projects, including the design of bins, silos, feeders, transfer chutes, and pneumatic conveying systems. Industries i've had the opportunity to work on projects include agriculture, food & beverage, nuclear waste, environmental, plastics, and cement. All of these industries have one thing in common: tricky powders and bulk solids.
During your presentation, you discussed the differences between feeders and conveyors. Could you elaborate on these two components' critical design distinctions and operational implications?
Feeders and conveyors are often very different from a design perspective. Feeders are used to control the discharge rate from a storage vessel (i.e, bin, hopper, silo, etc.) and are flood fed. Conveyors are intended only to transport material between locations and operate only partially fully. Often feeders operate at variable speeds to allow for changes in flow rate out of the storage vessel above.Typically, conveyors operate at a single fixed speed.
You mentioned funnel flow and mass flow patterns in hoppers. How do these flow patterns influence the design and performance of feeders in industrial applications?
A funnel flow pattern occurs when material funnels through itself rather than slide against the internal sidewalls of a hopper. This results in a first-in, last-out flow sequence. There are several negative consequences that can result in a funnel flow pattern including ratholing, flooding of fine powders, higher loads acting downward on the feeder, inconsistent discharge of material, and caking (due to material stagnation).
On the other hand, a mass flow hopper ensures all material flows along the walls, promoting first-in, first-out discharge. By discharing in mass flow, stagnant zones of material are eliminated and ratholing cannot occur. Additionally, material discharing through the feeder has more time to deaerate, resulting in less chance of flooding of fine powders.
In the webinar, you highlighted the limitations of constant pitch screw feeders and the advantages of variable pitch and tapered shaft designs. Could you provide an example of an industry scenario where these designs have significantly improved operations?
In most industrial cases, a constant pitch screw feeder will lead to a funnel flow design. Because of this, the capacity of storage vessels with constant pitch screw feeders can be limited significantly. A simple change to a variable pitch or tapered shaft screw feeder can have positive impacts on the flowability of the bulk solids or powders above. Often, this change can be enough to convert a storage vessel from funnel flow to mass flow.
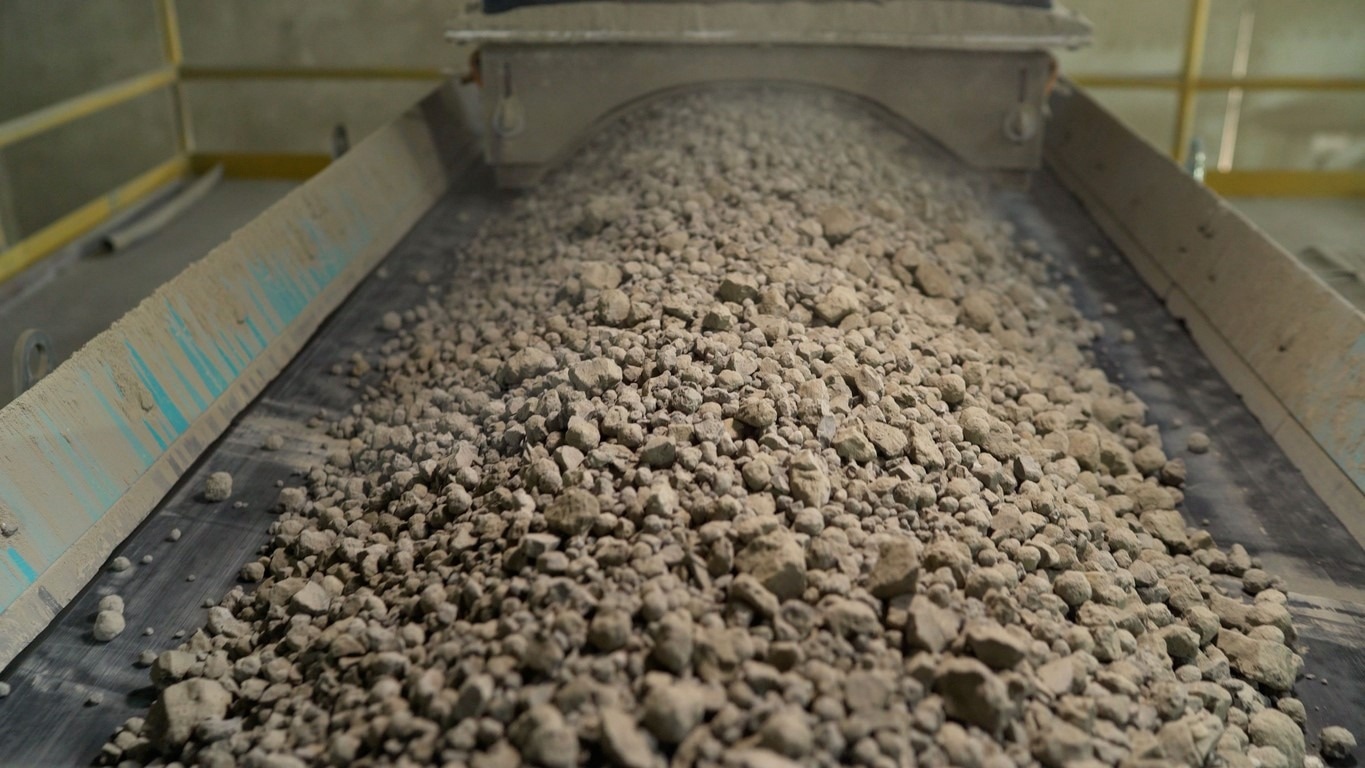
Image Credit:Jenike & Johanson
With feeders like rotary valves, belt feeders, and screw feeders available, how do you approach selecting the most appropriate design for materials with varying properties, such as cohesiveness or particle size distribution?
There are many factors that can come into play when deciding on the best feeder to use. Common process factors include throughput requirements, feeder fitup to the storage vessel, and downstream equipment. Additionally, there are several material properties that can have a large impact on how to decide which feeder to use. As an example, cohesive strength can play a pivotal role in deciding between screw feeders, belt feeders, and rotary valves. In most cases, cohesive materials are unsuitable for rotary valves given the small opening size of rotary valves, which can lead to bridging. Particle size also has an impact on the selection of the feeder. For example, belt/apron feeders are not the best choice when dealing with fine powders, as these can flood right off the belt.
You emphasized the role of flow property testing, such as bulk density, cohesive strength, and wall friction. Could you explain how these tests directly influence the choice and design of feeders?
Flow property testing is critical for the selection and design of feeders. Without testing, the design of any feeder would be incomplete. Bulk density data is critical in determining the throughput of the feeder, loads acting down on the feeder, and ultimately the speed at which the feeder must operate to hit a target throughput. Wall friction testing is required to determine the hopper angles needed for mass flow above the feeder, as well as selection of the materials of construction for the screw feeder. Cohesive strength testing is required to determine the outlet size above the screw to prevent bridging and ratholing.
Are there any emerging technologies or methodologies in the design of feeders and hoppers that you find particularly promising for addressing industry challenges?
Emerging technologies like discrete element method (DEM) modeling are promising for analyzing tricky powders and solids, as DEM allows for simulation of material behavior to optimize designs. DEM is classcially used in the evaluation of transfer chutes, but in some cases, can be very useful in the design or root-cause analysis of feeders.
About McKinnon Ray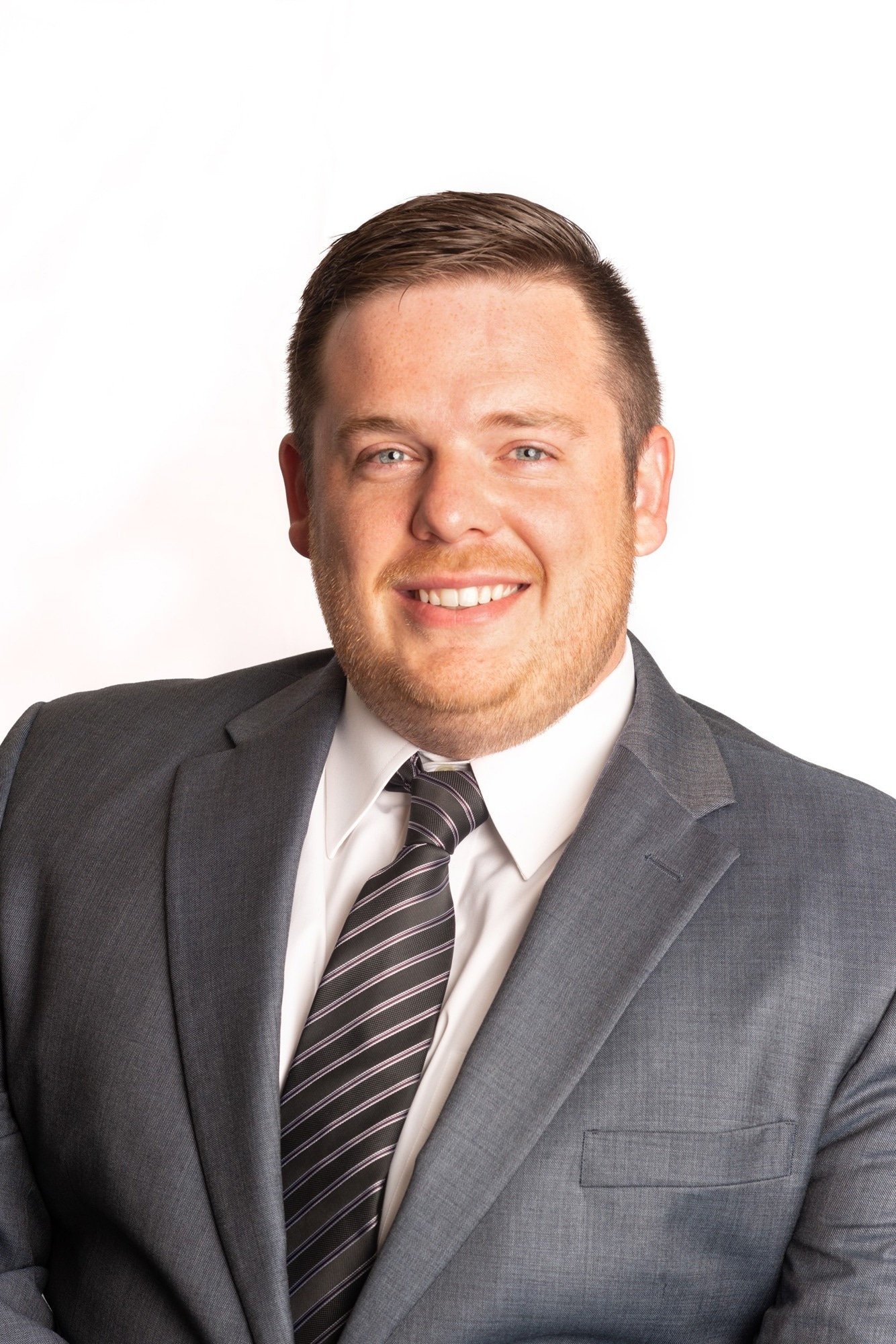
McKinnon Ray is a Senior Project Engineer with Jenike & Johanson for 5 years designing bins, silos, feeders, and transfer chutes for tricky powders and bulk solids. He has worked on projects across several industries including cement, mining, food & beverage, agriculture, and more. Before Jenike & Johanson, he worked at Anheuser-Busch as a shift supervisor in packaging and logistics departments. McKinnon has a Chemical Engineering degree from Mississippi State University.
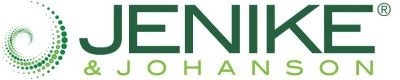
This information has been sourced, reviewed and adapted from materials provided by Jenike & Johanson.
For more information on this source, please visit Jenike & Johanson.
Disclaimer: The views expressed here are those of the interviewee and do not necessarily represent the views of AZoM.com Limited (T/A) AZoNetwork, the owner and operator of this website. This disclaimer forms part of the Terms and Conditions of use of this website.