Surface roughness refers to the fine texture of a part’s surface. Every manufactured part’s surface has three main components—form, waviness, and roughness—that influence how well a part performs. The characteristics of these components are linked to the manufacturing processes used to form the part, such as polishing, grinding, cutting, or edging, among others.
Surface roughness significantly impacts the functionality and durability of precision components. A rough surface increases friction between parts, resulting in greater wear over time. This roughness can also reduce lubrication effectiveness, potentially leading to accelerated component degradation and diminished efficiency.
Additionally, rough surfaces have a greater likelihood of trapping dirt or debris, which further accelerates wear and tear.
In certain applications, surface roughness can directly affect the longevity and reliability of the part. For instance, rougher surfaces can compromise the sealing effectiveness in components that are designed to retain fluids or gases, such as valves or seals, potentially causing leaks. Roughness also concentrates stress in certain areas, which increases the likelihood of fatigue failure under repeated use.
Apart from functionality, surface roughness influences other factors as well. Rougher surfaces expose more area to corrosive elements, which can accelerate the corrosion process. This is especially crucial in environments where parts are exposed to chemicals or moisture. Excessive roughness in consumer-facing products can also detract from the look and feel of the product, lowering both its aesthetic appeal and perceived quality.
By understanding and controlling surface roughness, manufacturers can ensure that components achieve optimal performance, maintain durability, and satisfy design requirements for both functional and aesthetic purposes.
The form describes the shape of the surface. In other words, is the part flat, spherical, conical, or a combination of these? Waviness could be thought of as the bridge between form and roughness, as it identifies features with longer spacing between them. Roughness represents the set of features with the smallest scale and shortest spacing between them.
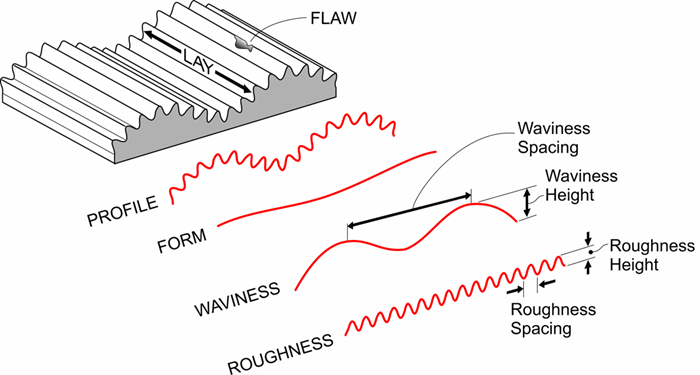
Image Credit: Zygo Corporation
At first glance, it might appear beneficial to make a measurement that includes all three components. However, in reality, this approach can be somewhat misleading. To properly analyze surface roughness, the form must first be removed, followed by the waviness.
How Do You Measure Just the Roughness?
Non-contact 3D optical profilers equipped with powerful data gathering and data analysis software simplify and accelerate this type of measurement compared to other roughness inspection methods.
A profiler utilizing Coherence Scanning Interferometry (CSI) facilitates sufficient data collection for most samples while maintaining high vertical precision. The hardware and software streamline the process of isolating roughness data by removing the form and waviness data, enabling scientists to concentrate on the finer details of roughness.
1. Start with the Correct Objective
The correct objective functions similarly to the proper stylus probe on a contact measurement device. When selecting an objective, three key factors must be considered: field-of-view (FOV), working distance, and lateral resolution. These elements are essential for achieving accurate and reliable measurements.
FOV refers to the area captured by the device in a single image. A larger FOV (lower magnification) provides a broader view of the surface, which is ideal for general observation. Conversely, a smaller FOV (higher magnification) captures finer details for in-depth roughness analysis.
The working distance is the space between the lens and the part being measured. It plays a crucial role in maintaining a clear focus, especially when the part has protrusions or indentations. This distance prevents damage to both the lens and the part.
Lateral resolution refers to the device's ability to distinguish fine details on a surface. High lateral resolution is crucial for capturing small height variations accurately, allowing individual roughness features to be identified without merging them together. This level of resolution is essential for precise measurement of surface roughness, as it ensures that finer surface details and height variations are accurately recorded.
2. Continue with a Few Part Setup Considerations
Once the correct objective is installed, the next step is to set up the test part. Profilers such as the ZeGage, NewView, and Nexview include a Z-Stop which can be configured to prevent a costly crash to the objective, test part, and possibly staging.
These Zygo products are also equipped with a unique ‘crash prevention’ feature, which minimizes or prevents damage to the instrument and samples. However, best practices still recommend setting the Z-stop before measuring.
With the Z-Stop set, it is time to focus. This can be a manual, two-part process encompassing a visual and interferometric focus. Alternatively, users can utilize Zygo Mx software, which includes a convenient Part Finder tool to quickly locate and focus on the test part. The goal is to achieve a sharp and clear image on the monitor, accompanied by the presence of fringes. If there are no fringes, there will be no data.
Even the most carefully positioned test parts will have some degree of tip and tilt present. Minimizing or eliminating tip and tilt where possible is essential. This process, commonly referred to as “leveling the surface” or “nulling the fringes,” is crucial for obtaining adequate roughness measurements.
At this point, the amount of light may require adjustment. Excessive light will cause the image to be saturated, while insufficient light will produce a dark image. In either case, data will be missing from the final map, which may affect measurement repeatability.
As mentioned previously, many of these setup procedures can be streamlined by using the Part Finder feature available on all Zygo Optical Profilers. Depending on the objective in use, the user can manually position the objective close to the test part and activate Part Finder.
Another feature, Smart Setup, automatically detects the best focus for the part, adjusts the light level, and configures the optimal measurement length over the FOV.
3. Set the Software Controls
Zygo’s range of 3D Optical Profilers operates using Mx Software, offering a set of acquisition controls that are easy to configure. These intuitive controls ensure that the necessary data is collected to meet the required precision and throughput standards for the part being measured.
One important factor that affects results is the scan length, which varies depending on the surface being measured. This control refers to the vertical envelope, carefully adjusted to capture all the details of the part along the Z-Axis.
While choosing a longer scan length may be required to ensure thorough measurement, it also increases the measurement time. To mitigate this, part tilt can be minimized, helping to reduce acquisition times. As noted previously, when Smart Setup is enabled, the system automatically determines and sets the optimal scan length.
4. Processing the Measured Data to Isolate Roughness
After the test part data is acquired, data processing is necessary to calculate the final roughness parameters. First, a Form Remove is applied to the data to remove the part’s overall shape (sphere, cylinder, etc.).
Next, the data is filtered to remove the part’s waviness from its roughness. This is achieved by carefully selecting a wavelength, known as the cut-off wavelength (λc), which distinguishes waviness from roughness. It should be noted that these filters operate based on the spacing of the features, not their height.
The surface roughness (Ra) call-out on a print should specify the filtering parameters. However, if filtering parameters are unspecified and the drawing conforms to one of the National Standards formats, such as ISO and ASME/ANSI, then these parameters can be inferred by the call-out.
The chart below illustrates an example of a filter cutoff selection chart according to DIN EN ISO 4288, ASME B46.1.
To use the chart, it is necessary to first identify which result the specification on the drawing is calling for and then select the corresponding λc in which range the result limit falls.
For instance, if a part drawing specifies a Ra value of 0.5 µm, a cutoff of 0.8 mm (800 µm) would be used. The data should be filtered to remove form and waviness, leaving only the roughness data.
Source: Zygo Corporation
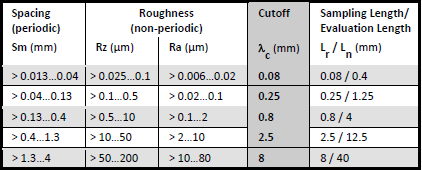
A Roughness Measurement Example
The following example involves a metal sealing surface, which can be crucial for retaining fluid within a pressure cavity. To capture the roughness and quantify its functional effects, a sequence of processing steps must be followed.
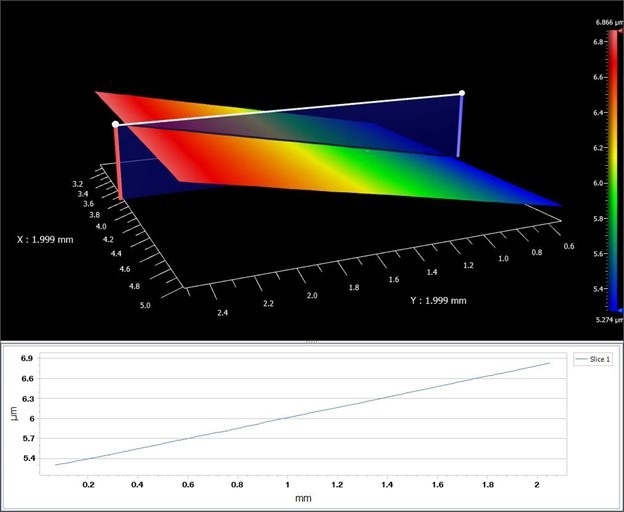
Figure 1. Metal Sealing Surface with Tilt. Image Credit: Zygo Corporation
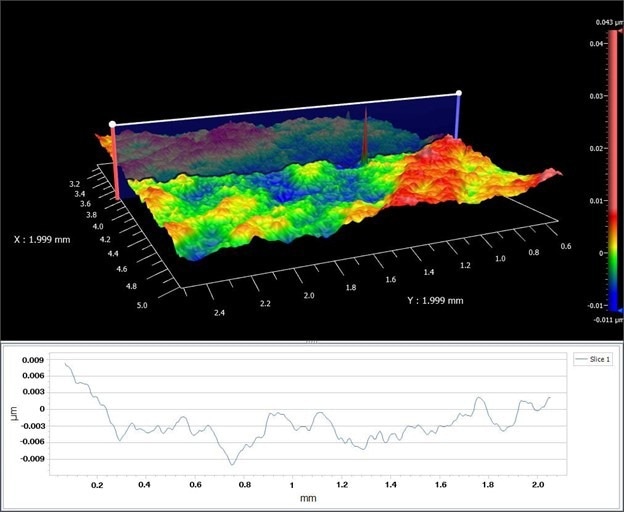
Figure 2. Removing Tilt from the Data. Image Credit: Zygo Corporation
Utilizing the Data Processing Fit/Remove function in Mx and choosing Plane as the Surface Type eliminates tilt and fits a plane to the raw data, essentially removing any shape data.
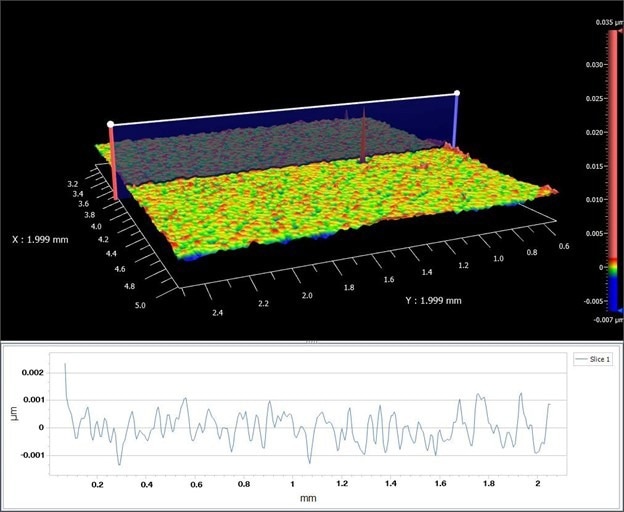
Figure 3. Applying a High Pass Filter. Image Credit: Zygo Corporation
At this point, the data is in a "plane" state. As shown above, the surface roughness is revealed by applying a high-pass filter in accordance with ISO standards. The filter removes the waviness, leaving only the roughness components visible. Although ISO standards offer general guidelines, it may be necessary to customize the filters to meet the specific functional requirements of each part.
Conclusion
Accurate measurement of surface roughness requires a careful approach that distinguishes between form, waviness, and roughness. This separation allows for a more precise evaluation of each part’s surface, ensuring it aligns with both performance standards and design specifications.
Advanced 3D optical profilers equipped with CSI and intelligent software solutions make this process both efficient and reliable. By utilizing these tools, manufacturers can effectively monitor surface quality, ensuring optimal product performance.
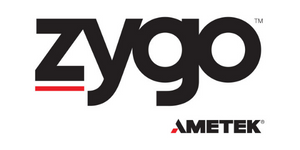
This information has been sourced, reviewed and adapted from materials provided by Zygo Corporation.
For more information on this source, please visit Zygo Corporation.