Established industrial systems have historically been designed to function as linear frameworks, transforming raw materials—including fossil and renewable resources—into products that become waste with little or no value at their end of life. These products also tend to incur disposal or landfill management costs.
Despite a more widespread shift toward product recyclability, these types of linear systems are still especially prevalent in the plastics industry. Typical product life cycles range from short-lived, single-use items to long-lasting pipes. Many plastic products become non-recycled waste destined for landfill disposal or energy recovery.
Recent years have seen several evolutions in the polymer industry; however, waste recycling and the creation of renewable materials like bio-based and biodegradable plastics (known as bioplastics) are forming key pathways toward sustainability.
The European Bioplastics Association reports that bioplastics production capacity increased to 2.18 million tons in 2023 and is anticipated to grow to 7.43 million tons by 2028.
Enhancement and expansion of biotechnological processes are required to achieve this capacity, with key processes like fermentation and purification key to producing essential biochemical monomers and molecules for the synthesis and polymerization processes employed in bioplastic production.
Biotechnology contributes to this aspect of the plastics industry while providing end-of-life waste management solutions via enzymatic recycling, facilitating monomer recovery under milder conditions without using solvents.
Biotechnology also plays an important role in recovering critical raw materials (CRMs) from electronic waste and accelerating and enhancing plastic biodegradation in different environmental conditions via bioaugmentation and other techniques.
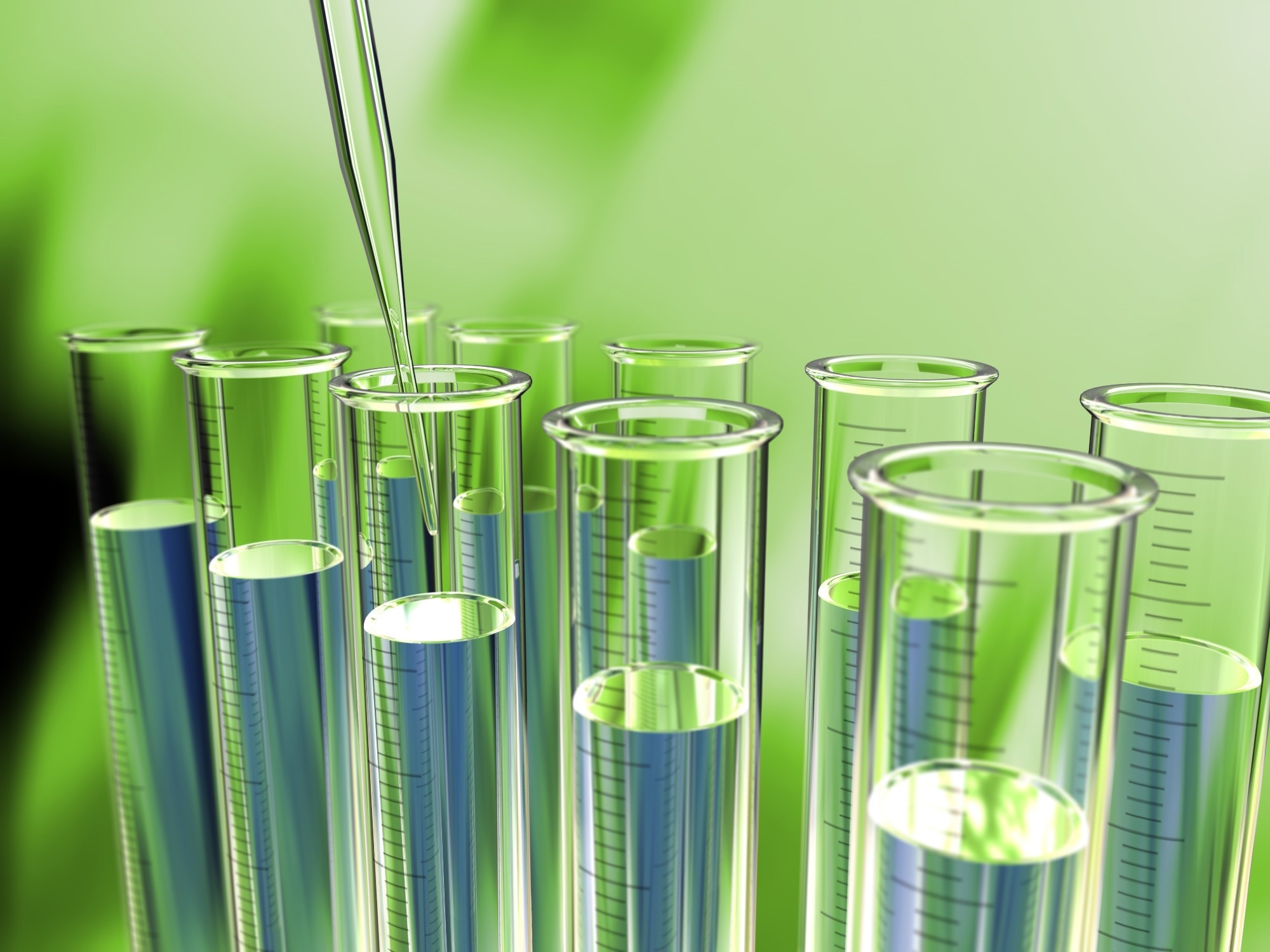
Image Credit: Paolo Toscani/Shutterstock.com
Bioplastic Production and Fermentation
The anaerobic biological process of fermentation involves sugars and other substrates undergoing incomplete oxidation, converting them into secondary metabolites such as alcohols and acids.
Fermentation is commonplace in the food industry, typically used to produce fermented foods. It is also widely used in the biochemical industry to create high-value-added products.
These value-added compounds/products are referred to as ‘platforms’ within the context of industrial biotechnology, serving as building blocks and precursors for other products. The primary platforms used in the bio-based plastics industry include:
- Ethanol platform: Using yeast as the inoculum, ethanol can be produced via fermentation. This platform can also be used to synthesize ethylene, a precursor for polyethylene.
- Lactic acid platform: Lactic acid bacteria can be used to generate lactic acid by fermenting sugars. This is the primary monomer of polylactic acid (PLA), the most commonly employed biodegradable bioplastic.
- Succinic acid platform: This platform is produced by bacteria able to metabolize sugars to produce succinic acid, which is, in turn, used to create PBS and other biodegradable polyesters.
Sugars required for fermentation can be sourced from a range of organic waste and by-products from different industries, most notably the food industry.
This process effectively repurposes these waste products, converting them into environmentally friendly, high-value bioplastics through polymerization and other chemical processes.
Enzymatic Recycling
The enzymatic recycling process leverages specific enzymes—biological protein molecules that function as catalysts—to break down plastic polymers into their respective monomers and oligomers.
PETases can cleave PET chains into their fundamental components, such as terephthalic acid and ethylene glycol. Enzymes enable polymer decomposition under mild pH and temperature conditions. Enzymatic recycling also employs specialized enzymes modified or designed to target specific polymer bonds, such as ester groups in polyesters.
Unlike natural biodegradation, enzymatic recycling is performed under controlled conditions to ensure optimized enzyme activity. This is normally done at thermophilic temperatures between 50 °C and 70 °C and controlled pH, typically adding a base to neutralize acidic reaction products.
While this process tends to be used for polyesters that include PET, it has also proven effective for bioplastics like PHA and PLA, enabling effective monomer recovery while avoiding the value loss typically linked to composting biodegradation processes.
This process also boasts low-temperature requirements, making it more energy-efficient than chemical recycling, which typically necessitates higher pressures and temperatures.
This technology still faces challenges in terms of scalability, the costs of enzyme production, and the chemical structure of some plastics, which prevents their enzymatic recycling. Despite these issues, it remains a viable option for improving global plastic recycling.
Critical Raw Material Recovery Through Biotechnology
Critical raw materials are key to the European region’s economic and technological development, but these materials face significant supply risks due to material scarcity, limited suppliers, and challenges associated with extraction and processing.
The importance of these materials for strategic industries like electronics and renewable energy means that they must be recovered wherever possible to help mitigate these supply risks.
Electronic waste remains a key source of critical raw materials, with biotechnological leaching representing a sustainable and environmentally friendly approach to recovering CRMs from PCBs and other electronic waste.
Biotechnological leaching is a natural process involving the solubilization of insoluble metals via microbial activity. A range of microorganisms are used in these processes, typically including Acidithiobacillus ferrooxidans and Acidithiobacillus thiooxidans. Aspergillus niger is also a viable option, producing organic acids able to promote metal solubilization.
Once solubilized, these metals can be recovered using traditional recovery techniques, including electrodeposition and chemical precipitation.
The primary advantage of biotechnological leaching is its environmental sustainability. This solubilization method achieves high metal recovery efficiency while avoiding using chemicals and acids and boasting low energy requirements and operational costs. However, the process has its downsides, including long processing times, reduced efficiency, and high pulp densities.
Accelerating Plastic Biodegradation
Biodegradation is a natural process, with microorganisms such as fungi and bacteria decomposing polymers and other materials into simpler compounds. These compounds include CO2, water, and salts, which can be safely returned to natural ecological cycles.
Various factors, including environmental conditions and temperature can impact plastic biodegradation. For example, higher temperatures typically improve materials’ biodegradation by increasing the flexibility of polymer chains. They also better facilitate materials’ enzymatic hydrolysis into their basic constituents and monomers, which microorganisms can employ as carbon and energy sources.
Plastic biodegradation is also affected by microorganism concentration, with higher concentrations of microorganisms accelerating the process due to their ability to function as biocatalysts. Hydrolytic enzymes are synthesized initially before hydrolysis products are broken down into CO2 or CH4, depending on whether the process is aerobic or anaerobic.
Very few identified and classified microorganisms can degrade plastics, prompting the emergence of bioaugmentation as a potential solution to this issue.
Bioaugmentation involves specialized microorganisms' growth and external addition to degrade certain plastics in the biodegradation environment.
Using bacteria isolated from various environments has enabled AIMPLAS to successfully reduce biodegradation times. These bacteria have demonstrated the capacity to biodegrade different types of plastics, offering viable solutions for contaminated soil remediation and biodegradation testing.
Acknowledgments
Produced from materials originally authored by Pablo Ferrero, a leading biotechnology researcher at AIMPLAS.
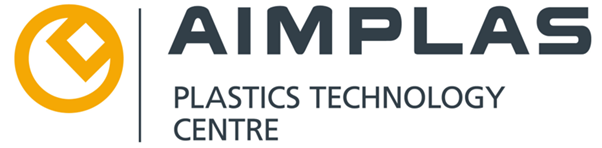
This information has been sourced, reviewed and adapted from materials provided by AIMPLAS.
For more information on this source, please visit AIMPLAS.