The Thermo Scientific™ LInspector™ Edge in-line mass profilometer represents the next generation of electrode loading analysis. This instrument is set to become a key tool throughout the battery industry, particularly for those facing intense pressures in terms of both economics and performance.
This article introduces the LInspector Edge system, exploring its impact on electrode coating process control and its advantages when utilized by battery manufacturers.
The Thermo Scientific LInspector Edge In-line Mass Profilometer
The LInspector Edge is a cutting-edge process analyzer that uses a linear detector array to enable real-time measurement of the full strip width of electrode coating uniformity, from ‘edge-to-edge’, offering exceptional cross-strip resolution.
Thermo Scientific has developed this innovative new instrument based on its decades of metals gauging expertise in flat sheet production, where maintaining uniform thickness is essential for an array of rolling and stamping operations.
The LInspector™ Edge brings groundbreaking measurement capabilities to the battery manufacturing industry, allowing electrode manufacturers to investigate coating uniformity with levels of detail that were previously inaccessible.
It has the ability to precisely measure electrode coating material’s edges in order to identify unwanted defects such as sliding edges or ‘bunny ears.’ These measurements are achievable across the entire width of the line, enabling simultaneous analysis and monitoring of multiple stripes or lanes.

Image Credit: Thermo Fisher Scientific – Production Process & Analytics
The Importance of Accurately Measuring Electrode Loading
Poorly controlled electrode coating uniformity is widely recognized as a key contributor to various performance and safety issues in battery cells. One of the industry's primary concerns is the N/P ratio—the mass-specific capacity ratio between the negative (anode) and positive (cathode) electrodes—due to its critical impact on battery performance and longevity.
A low N/P ratio indicates excessive cathode loading, and this is typically linked to poor battery cycling performance. A high N/P ratio, in contrast, indicates excessive anode loading, reducing battery energy density.
A sub-optimal N/P ratio can also result in internal short circuits, thermal runaways, and hot spots, all of which represent major safety concerns for battery manufacturers.
It is, therefore, necessary to consistently maintain an optimal N/P ratio via carefully controlled electrode coating uniformity in order to ensure balanced electrochemical reactions within the battery. This improved control allows cell designers to achieve improved safety and more consistent performance for specific applications.
Achieving the necessary level of control requires precise, comprehensive measurements of coating uniformity for both the anode and cathode. Detecting loading variations across the entire surface is essential for identifying defects that could compromise electrochemical performance and overall battery reliability.
These defects can be especially troubling when a high spot on the cathode material aligns with a low spot on the anode or vice versa. Cell designers require balanced mass loading on both sides to help prevent performance and safety issues when batteries are utilized in their final applications.
Mass Profilometry’s Impact on Electrode Loading Analysis
The LInspector Edge represents a significant advancement over conventional single-point scanning gauges, offering improvements in three key areas:
- Coverage
- Speed of profile update
- Cross-strip resolution
A typical scanning gauge moves back and forth across the electrode every 3-5 seconds, covering less than 5 % of the electrode surface. The LInspector Edge features a fixed detector array able to cover 100 % of the electrode surface, measuring the full electrode width every 1 millisecond.
These powerful measurement capabilities result in considerably enhanced coverage and a speed of profile update that is approximately 3000 to 5000 times faster than its conventional counterparts.
The LInspector Edge also employs individual pixels that measure every 1mm. This is a notable improvement over the measurement spot size of single-point scanning systems, which is generally no smaller than 3mm. This equates to a three-fold increase in cross-strip resolution.
Mass profilometry allows its users to rapidly monitor the complete electrode coating in significant detail, offering major improvements over conventional technology.
In terms of its use in N/P ratio control, the LInspector Edge offers its users a real-time ‘heat map’ of mass loading, highlighting peaks and valleys in the coating with a precision of +/- 1 gsm over a spot size of +/- 1 mm across the whole electrode surface.

Figure 1. Traversing single point sensors only measure 2% to 4% of the electrode material (note red trace of measurement spot). Image Credit: Thermo Fisher Scientific – Production Process & Analytics

Figure 2. Mass profilometry measurement. Image Credit: Thermo Fisher Scientific – Production Process & Analytics
Benefits for Battery Manufacturers
Its capacity to revolutionize capabilities in these three core areas allows the LInspector Edge to instantly visualize the entire mass loading profile in unparalleled detail. For battery manufacturers, this represents a vast improvement over the less-detailed, infrequent snapshots offered by conventional systems.
Detecting defects and irregularities as small as 1mm × 1mm early in the battery cell manufacturing process allows for the consistent and timely segregation of non-conforming materials. By taking a proactive approach to this critical task, manufacturers can identify and address suboptimal electrode coating uniformity before cell completion.
This early intervention improves yield in downstream processes such as slitting, calendaring, and cell assembly while reducing reliance on final cell inspection. Additionally, by synchronizing communication between the LInspector Edge and manufacturing and inventory control systems, manufacturers can trace every square millimeter of electrode material to its final placement within a cell.
Such a high level of traceability is particularly valuable as individual cells are assembled into modules and packs and ultimately integrated into their final applications.

Image Credit: Thermo Fisher Scientific – Production Process & Analytics
Impact on Process Economics and Return on Investment
Production managers are often focused on maximizing capital investment efficiency, which, on the electrode coating line, means maintaining the highest possible line speed without sacrificing quality.
The LInspector Edge provides operators with real-time, comprehensive data to optimize production speed while ensuring consistent performance.
Automatic control systems typically require stable data from 10 consecutive profiles to implement a control adjustment. With its rapid update speed, the LInspector Edge significantly improves responsiveness compared to conventional scanning systems, allowing for faster, more precise process control.
While high-speed production is crucial for return on investment (ROI), product quality is equally important. The LInspector Edge excels in this area, offering exceptional speed, long-term stability, reproducibility, and measurement resolution.
By enabling precise alignment of anode and cathode sheets using accurate, high-resolution data, it supports the production of batteries with balanced loadings, ensuring optimal performance throughout their lifespan. Additionally, minimizing defects and inconsistencies helps reduce material waste and improve overall manufacturing efficiency.
Summary
The LInspector Edge is laying the foundation for the cost-efficient production of better-performing batteries. Its significant, quantifiable benefits are particularly crucial given the steep financial and reputational risks associated with releasing substandard batteries.
Although a relatively new tool, the LInspector Edge is expected to become integral to key battery manufacturing processes, consistently providing a strong return on investment while enhancing quality and efficiency.
Acknowledgments
Produced from materials originally authored by Palani Shanmugam from Thermo Scientific.
This information has been sourced, reviewed and adapted from materials provided by Thermo Fisher Scientific – Production Process & Analytics.
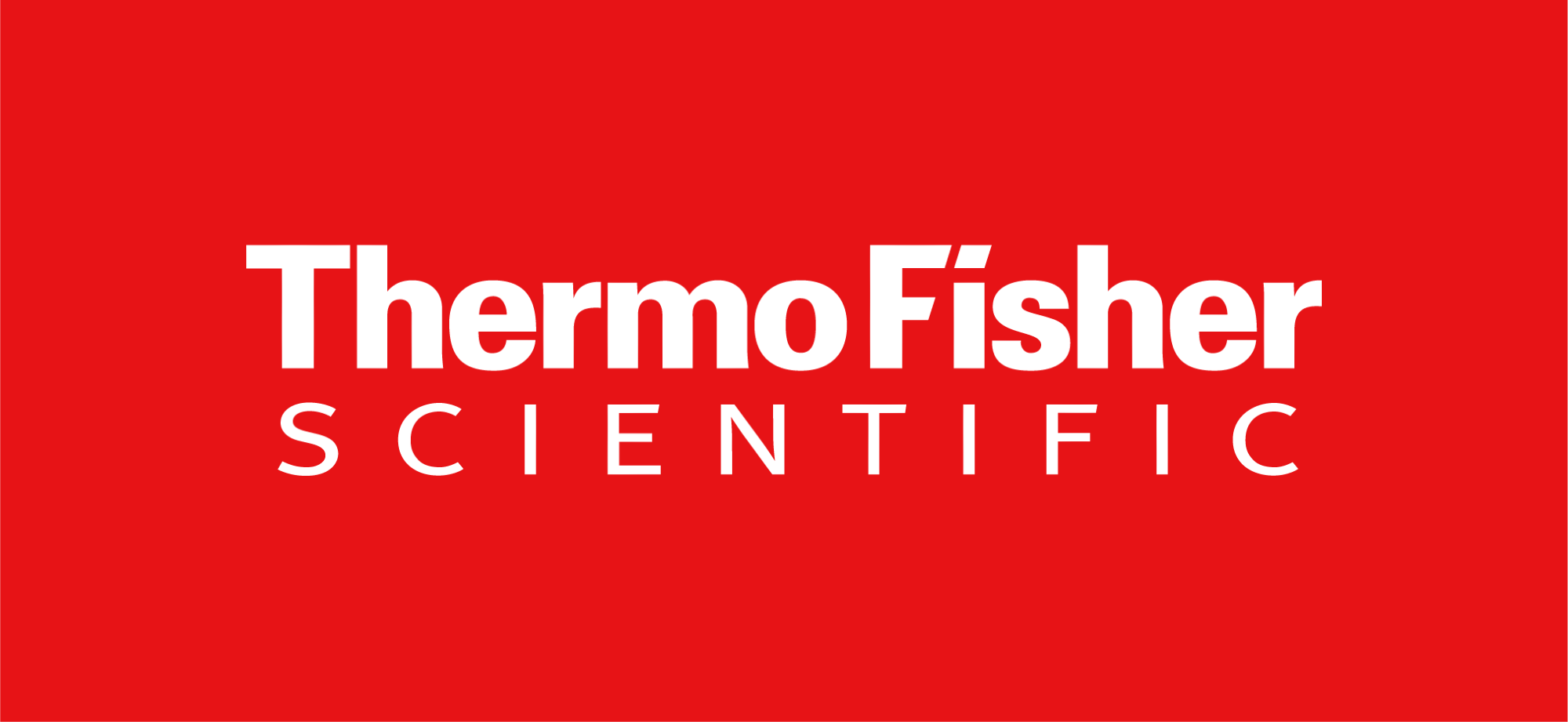
For more information on this source, please visit Thermo Fisher Scientific – Production Process & Analytics.