Makrolon® is an amorphous, thermoplastic molding compound. It is noted for its high light transmission, high heat resistance, high toughness, high creep modulus, high dimensional stability and good electrical insulation properties. Glass fiber reinforced Makrolon® has a particularly high rigidity, coupled with very good dimensional stability. The production plants for Makrolon® have been certificated to DIN ISO by the competent certification companies.
Product Characteristics
- Inherent color - Clear and transparent, like glass
- Toughness - Without notching, no failure; high notched impact strength
- Dimensional accuracy and stability - Exceptionally high, since no change in dimensions due to water absorption and post shrinkage, high creep modulus, high heat deflection temperature, isotropic behavior
- Heat resistance - Glass transition temperature up to 148 °C
- Resistance to ignition sources - Fire classification up to UL 94V-0/1.5 mm and UL 94-5VA/3.0 mm; maximum temperature in glow wire test up to 960 °C
- Electrical insulation - Volume resistivity 1014 Ohm x m; dielectric strength up to 36 kV/mm (1 mm wall thickness)
Miscellaneous - Makrolon® grades for food contact and medical engineering applications
Medical and Laboratory Uses
Human lives depend on the reliable operation of a large number of medical appliances.
Covestro is aware of the special responsibility that goes with ensuring the non-toxicity of products that are in direct contact with body fluids and tissues.
Items of equipment such as oxygenators, dialyzers and infusion units require visual monitoring in order to check for air bubbles, and only a transparent material will permit this.
The non-toxicity of the material employed is a further criterion for use in many medical and laboratory applications.
In addition to this, an increasing number of drugs are being administered intravenously in liposome solutions. Covestro supplies the first lipid-resistant polycarbonate for infusion technology applications.
Makrolon® LQ (Lens Quality) is a product class specially developed for correction lenses, and is noted for its outstanding cleanliness and light transmission.
Properties and Reasons For Using Makrolon® in Medicine
Biological compatibility - All applications that involve direct or indirect contact with blood or tissue must comply with the appropriate provisions of the relevant authorities.
In the case of medical products within the validity area of ISO 10 993-1, only Makrolon® grades that comply with the test criteria specified in this standard may be employed. The biocompatibility tests conducted by Covestro on the basis of this standard, however, do not cover the following areas of use:
- Long-term use over 30 days, particularly when used as an implant
- Long-term contact over 30 days with endogenous substances (blood, tissue, dentine and other body fluids)
- Multiple use in medical applications
- Sterilizability - It is essential for medical equipment to be capable of absolutely reliable sterilization.
Makrolon's® high dimensional stability in heat, up to a temperature of 135 °C, permits steam sterilization at 121 °C. The range of special medical grades is rounded off by Makrolon® grades for gamma radiation sterilization. All Makrolon® grades can additionally be sterilized through exposure to ethylene oxide gas (ETO).
Where even higher temperatures are required, use can be made of Apec®, Covestro's high-temperature polycarbonate. Apec® is suitable for hot-steam sterilization and for treatment in autoclaves at temperatures of up to 134 °C.
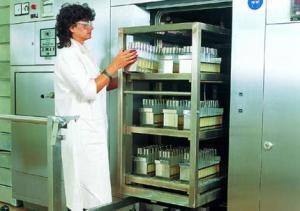
- High heat resistance and dimensional stability.
- Light transmission - Makrolon® LQ (Lens Quality) is noted for its outstanding cleanliness and light transmission. This high light transmission, together with a favorable refractive index, fulfils the requirements of the optical industry.
- A grade with a special UV absorber ensures 100% UV protection.
- Outstanding break resistance - Makrolon's® high impact strength means that, providing the material is correctly processed, virtually unbreakable spectacle lenses can be achieved with Makrolon®. It does not matter whether the stress acts at a temperature of - 40 or + 40 °C.
- Tolerances - The quality of spectacle and other lenses is primarily determined by the production tolerances. The focal length of a lens is determined by the shape of the lens and is subject to particularly tight tolerances.
- Production tolerances of up to ± 0.1 % can be achieved with Makrolon® on state-of-the-art injection molding machines.
Special Requirements For Medical Appliances
Makrolon® is used for the production of high-grade medical appliances. The main reasons for the choice of Makrolon® include its glass-like transparency, toughness, resistance to fracture, reliable sterilizability and good compatibility with body fluids and tissues for contact times of up to 30 days.
|