For many years the manufacture of precision castings in titanium has relied on the vacuum arc remelting (VAR) process. This slow and costly technique severely limits development of the advanced casting capabilities that modern end users demand. In particular the aerospace industry has been extremely aggressive in its technical design requirements for components both large and small, some in flight critical applications on programmes such as the Eurofighter, the Airbus A340 and A3XX, and the US's Joint Strike Fighter. To date, success on these programmes has been impressive in terms of increased size capability but there has been a lack of metallurgical integrity and improvements in dimensional tolerances. Consequently, there is a vital need for a step improvement in the moulding, melting and pouring of titanium precision castings, work towards which has typically employed an induction melting process usually referred to as inductive skull remelting (ISR). The Taramm Process In Europe, the need is being met by a small company called Taramm (Tirane et Alliages Rares MicroMoules) which is providing a viable production capability using a unique combination of cold crucible induction melting and centrifugally assisted pouring. At the heart of the process is a special vacuum melting and pouring furnace designed by Taramm. The furnace structure accommodates the melting and pouring equipment and uses conventional vacuum pumping systems. In a conventional one piece copper crucible the magnetic field generated by the field current in the heating coil is cancelled out by the magnetic field associated with the induced current in the crucible. The magnetic flux that would be necessary to heat and melt a conductive metal charge thus does not exist. In contrast the Taramm copper crucible, figure 1, is segmented, each segment being water cooled and insulated from each adjacent segment. Under power, this design causes the induced current to loop around each segment as shown by the arrows A, B, C, and D, and allows the generation of an induced current, creating the required magnetic field in the metallic charge.  | Figure 1. A section of the segmented cold crucible and the induction coil | The metal is heated quickly, begins to melt and initially fills the base of the crucible, where a small volume resolidifies and forms a local, thin `skull' of metal. As melting nears completion, the electromagnetic (Laplace) force in the molten metal concentrates it in the centre of the crucible, reducing metal mould contact, figure 2. 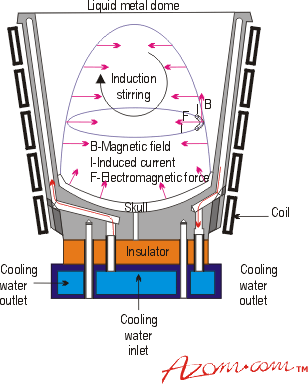 | Figure 2. Schematic cross-section after melting | Once melting is complete the charge is partially levitated and, due to the minimal heat exchange between the metal and the crucible, the metal becomes superheated. This can be controlled for charge weights up to 5kg. The Taramm technique therefore provides significant advantages in terms of the `filling' of thin sections in the mould, and the overall length of flow of the molten metal, compared with the VAR process, which is incapable of superheating. The constant and vigorous stirring of the titanium by the induced electromagnetic forces also gives the benefit of optimum chemical and thermal homogeneity in the metal. When the requisite molten metal temperature is achieved, the crucible is tilted and the titanium poured into a ceramic mould rotating at high speed. In order to maintain the temperature of the melt the electrical power is applied throughout the pouring operation. Advantages of the Taramm Process On entering the mould the molten titanium is immediately subjected to centrifugal forces. The filling of the mould cavities is accelerated by the continually increasing pressure exerted on the molten metal and directed towards the outer diameter of the mould. This centrifuge effect, combined with the superheated nature of the titanium, promotes the filling of section cavities as thin as 0.5mm, with attendant fine detail and form. Centrifugation is maintained until the titanium solidifies. Satisfactory centrifugal casting demands a symmetrical mould which is balanced radially within a prescribed annulus. An additional advantage of centrifugation is a more efficient use of metal due to the parabolic free surface of the liquid metal in the mould. The metal charge weight is carefully adjusted for each mould configuration to ensure the filling of each casting cavity and its `feeder', while leaving a significant portion of the central downsprue devoid of metal. This technology has further benefits. While the conventional VAR process demands the use of a custom made electrode, sized to fit the crucible, the Taramm process is able to use forged or rolled premium quality off cut, material which is a fraction of the cost of the VAR electrode. Also, in VAR a `stub' of the electrode is left as a remnant of the electrical circuit after melting and, considered with the `skull' material covering the interior surface of the crucible, a significant proportion of the original electrode is left unused After the Taramm process the only unused metal is contained in the minimal skull in the base of the crucible amounting to a large material saving. So far the cold crucible induction process has been used mainly to produce Ti6Al4V commercially pure titanium and titanium aluminide eutectic alloys. However, nickel base alloys, such as IN 718, are compatible with the process and there is therefore no need to use different types of melting furnace for these metals. The metal flow and filling performance produced by the combined effect of superheating and centrifugal pouring in the Taramm casting process enables the pre heat temperature of the recipient mould to be significantly reduced, compared with the VAR process. Preheat costs are therefore lower but, most importantly, the formation of alpha case, due to the oxide-forming metal-mould reaction, is significantly reduced. As a result, `chemical milling,' which has now become the mandatory surface cleaning operation for alpha case removal is used much more sparingly. This allows for the retention of much more of the cast surface layer and means cast tolerances and physical dimensions are better maintained. This process is effective for castings from a few grams to 2kg in weight, and wall section thicknesses as low as 0.5mm are routinely achieved. Form and detail are extremely well defined. Due to the pressures applied by the centrifuge and subsequent densification by hot isostatic pressing (HIP), castings show little or no evidence of porosity and micro-shrinkage even on a microscopic scale. The use of premium quality melt stock and the robust nature of the `face coat' the Taramm developed shell moulding system combine to give good metallurgical integrity when assessed for casting defects such as non-metallic inclusion Electromagnetic stirring eliminates any propensity for segregation, and the casting technique yields consistently uniform grain size and structure. Figure 3 shows a nozzle casting for a missile application. This technology also lends itself to other industries such as the medical and leisure industries. 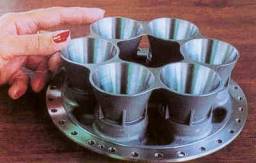 | Figure 3. A rocket exhaust nozzle with reduced weight and increased strength. | Taramm's new furnace and centrifugal pouring technology mean that customers in these industries can expect complex `near net' shapes with very thin sections, precise dimensional control, metallurgical properties comparable with forgings and very competitive costs. Small quantities or prototypes can be made using rapid prototyping techniques, and aluminium pattern tooling facilitates the repetitive and consistent production of larger quantities. The desirable properties of titanium have caused precision castings to be used in many diverse applications, for example missile guidance components requiring a coefficient of expansion very similar to glass, low inertia titanium shuttles for weaving machines, high strength cryogenic parts for space exploration, and fatigue resistant and tissue compatible surgical implants. Some examples of the types of applications that can be serviced by this technology are given in table 1 Table 1. Uses of Taramm titanium castings. | Airframe structural parts | Junction plates, fans and compressor wheels, door slides, stiffeners. | Aero engine components | Air intake housings, pump bodies, supports. | Medical implants | Knee, hip, vertebrae, shoulder. | Missile industry | Nozzle plates. | Leisure industry | Bicycle parts, jet ski propellers, climbing equipment, automotive. | Jewellery | Rings, earrings. | Chemical and marine industry | Valves, housings, fittings. | Optical components | Low co-efficient of expansion. | Textile industry | Shuttles with reduced inertia. | Space exploration | High performance at cryogenic temperatures. | In 2000, Taramm is introducing a second generation of its furnace, increasing casting yield from 2.5 to 5kg per mould. The new furnace has two vacuum interlock chambers, allowing the loading of a preheated mould while the one just cast is cooling under vacuum, providing a further increase in throughput. A new crucible, redesigned to generate full levitation of the charge and with an innovative `pour' capability, has been developed and is awaiting a patent. This new furnace combination will enable the use of 100% of the charge metal and the increased mould diameter, giving an increased centrifuge effect, will maintain `feed and fill' capability for Taramm's bigger size capability. |