A material's surface is treated in order to provide a number of properties, such as low friction, hardness, or corrosion resistance. The rule in the past has been that one treatment gives one property. The coat is either slippery, hard or provides corrosion resistance. Armoloy, a new treatment that bends these rules and provides all three at once. Surface Treatments Surface treatments have evolved dramatically over the past 20 to 30 years, and their impact on the engineering world has been significant. There is a mindboggling array of techniques available today for a variety of applications, both high and low tech, but they generally impart just one property listed above. Armoloy strikes a balance between the high and low tech extremes, using a process viewed as relatively low tech to apply an advanced coating. Being a three in one coating opens up a huge range of possible applications. Industries such as aerospace, nuclear, military, and bearings, as well as food and pharmaceutical, pump and valve, machine tool, plastic moulding, tooling, sea exploration and pressing industries are all existing applications. What is Armoloy? Armoloy is a low temperature, multistate process of electrocoating based upon chrome plating technology. Rather than the usual chrome plating solutions it uses a proprietary chemical solution, developed to provide unique characteristics, as well as a special pre-cleaning stage and a proprietary technique for removing the matrix on the surface of the base metal. By using a modified electrocoating process that affords tighter control of deposition than conventional electroplating techniques, the metallic elements of the Armoloy solution permeate into the pores of the base material, integrating the coating with the metal itself. The result is a hard, slippery, corrosion resistant, nonporous and crack free surface. The coating is applied at low temperature and at finished tolerance, and adheres absolutely to the base material. How thick are Armoloy Coatings? Armoloy deposits can be from 1 to 10µm thick, but are usually between 3 and 5µm depending on the application. Deposits of less than 5µm can be controlled within +/- 0.5µm, providing a very even deposit, figure 1. The process can be used on existing components generally, with little or no design changes. 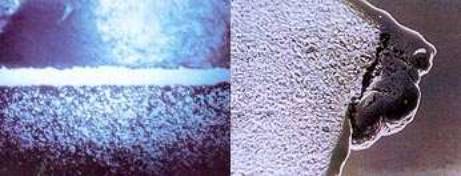 | Figure 1. (a) Cross section showing intimate contact, lack of porosity and even coating across substrate surface and (b) showing how the coating can follow the contours of the substrate. | Surface and Morphology Effects A further feature of Armoloy is that it will faithfully reproduce the shape of the base material. Figure 1 shows an example of the coating following the contours of a burr. The ability to follow a sharp edge is a great advantage when applying the coating to cutting blades. Such blades often operate in damp and humid environments, for example in the food, textile or paper industry, where a sharp edge needs to be maintained. In these applications wear resistance, corrosion resistance and non-stick characteristics, food sticking to the blade can cause quality problems, are all necessary qualities, and the adhesion of the coating is of paramount importance. Foreign matter cannot get under the Armoloy' coating and strip it away along the cutting edge, which means a sharper edge is maintained for longer. Thin section blades benefit from the low temperatures (below 75°C) employed during processing, eliminating any risk of distortion or exceeding previous temper temperatures. One of the key features of the coating is its controlled, dense micro-nodular finish, similar to the skin of an orange. This `ball bearing' surface means the contact area is relatively low, reducing friction, and the same nodularity provides certain self-lubricating characteristics by retaining available lubrication between the nodules. The surface is very dense and extremely durable with a surface hardness is 72R, due in large part to the absolute adhesion of the coating to the base material. It is also nonporous, so applying the coating effectively seals the substrate. The distinct characteristics of added density and controlled micro nodularity are the principal differences between Armoloy and `traditional' surface coatings. In applications where lubrication is not available Armoloy can be effectively operated against itself, but with lubrication static or sliding coefficients of friction can be reduced to around 0.14 to 0.12 (figure 2). This makes the coating a very attractive option for the bearing industry, which requires a very tight tolerance coating that reduces friction and provides corrosion resistance. 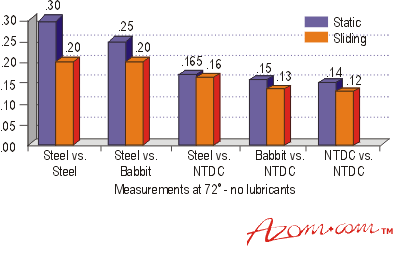 | Figure 2. Comparison of static and sliding coefficients of friction for various systems. | Applications Armoloy in a Car Plant In one particular application, a new overhead conveyor was being fitted into a car plant. The conveyor ran through a wash down facility, so lubrication, fretting, wear and corrosion were all an issue, as was minimising the risk of the conveyor seizing. Keeping productivity high and down time low were primary concerns, and so stopping the conveyor for maintenance, repairs and lubricating was out of the question. Since the inner and outer races, circlips, pins and sleeves were all coated in Armoloy the conveyor has not stopped for over 3 years, even for routine maintenance. The corrosion resistance of the Armoloy coating is an important attribute. Tests have shown that it provides corrosive resistance exceeding 440C stainless, and the Armoloy coating of 440C components to improve both corrosion and wear resistance is a proven application. Coating of 300 series stainless steels for anti gall and fretting applications has also been of benefit to the aerospace, nuclear and food industries. Armoloy in Paper Manufacturing The coating has also been used successfully to provide corrosion resistance for bearings in paper and pulp production, packaging machinery, printing, and food and beverage uses. In America a well known manufacturer of alcoholic drinks had been changing the bearings on its bottling lines every 3 months due to corrosion, creating problems with down time and lost production. After competitive tests Armoloy-coated bearings were installed and these had, when last reported, exceeded two years service on the bottling line without replacement. Armoloy in Marine and Aerospace Applications The effectiveness of the coating's combination of wear and corrosion resistance with low friction is most impressively demonstrated in industrial applications such as these, where down time is the principal enemy. Armoloy-coated bearings have also been in service on naval vessels and aircraft for a number of years, and there has been a great deal of interest in using the process as a replacement for cadmium in these applications, figure 3. 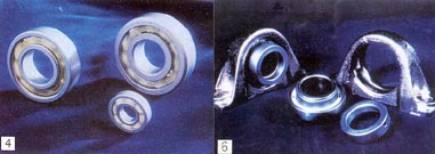 | Figure 3. Armoloy bearings from (a) navy vessels and aircraft (still in service) and (b) from the food industry. | Armoloy in the Food Industry Armoloy-coated thin section blades have been used successfully in the automated slicing of dog food treats, where a low friction coating had previously been used to prevent residue building up on the blade and causing quality rejections. Due to the content o the product (cereals, rice etc) it was a fairly abrasive process and, while the coating was preventing any build up, it was only a short time before it was worn away. A sample set of Armoloy-coated blades was produced and after six months use still looked and performed as new. Summary By using a specialised surface preparation technique and modifying existing electrocoating technology Armoloy has been able to produce a versatile, big tech surface treatment that provides a combination corrosion resistance, wear resistance and low friction in an eminently controllable process. |