Introduction Hard-metals based on tungsten carbide (WC) with Co or Ni as a sintering additive have been utilized widely for cutting tools and wear-resistant machine parts. The main element of hard-metals is tungsten, which is very expensive. However, a small amount of their scraps are recycled; less than 20% in Japan [1]. Recently, the zinc process has been applied to recycle scraps of WC hard-metals [2]. In this process, scraps of hard-metals are sucked into fused zinc and eutectic reaction between fused zinc and Co or Ni occurs. As a result, the scraps are powdered into WC grains, which stick on the bottom of the zinc bath. After that, WC powder is obtained by evaporating zinc at high temperatures in the inert gas atmosphere. Since commercial WC hard-metals include many additives such as TiC and VC, strict selection of scraps is required to supply high-quality hard-metal powder with suitable additives for their applications. Because there are many smaller enterprises in the Japanese machine industry, collecting the scraps from them is very difficult. A recycling process for hard-metal scraps is proposed in this paper. Tungsten trioxide, WO3, shows high partial pressure of gaseous tungsten oxides at elevated temperatures. Figure 1 shows the equilibrium partial gas pressure of gaseous tungsten oxides from pure WO3 in air as a basis of the thermodynamic data reported by Barin [3]. Gaseous (WO3)3 shows the highest partial pressure and reaches to 10-4 atm at 1300°C. The maximum evaporation rate per the unit area, J, can be estimated by using the Langmuir equation: (1) where P, m, k and T are partial gas pressure, molar mass of molecular, the Boltzmann constant and temperature, respectively. When the constant, α, is assumed to be unity as the maximum value, WO3 of 170 g (include 135 g of W) can be obtained from one chip with 1 cm2 of surface area for 1 h. By oxidizing the hard-metal scrap at elevated temperatures in air, high purity WO3 can be obtained without contamination of Co, Ni and TiC, which have negligible gaseous phases with remarkably low partial pressures. With reduction processes of WO3 to form W [4-7] and direct carbonation processes of WO3 to form WC [8-14], pure W and WC can be produced from the hard-metal scrap by high-temperature oxidation in air. In this paper, the evaporation of tungsten oxide from commercial hard-metal tools by oxidizing at high temperatures in air is reported for applying the recycle process using high-temperature oxidation. 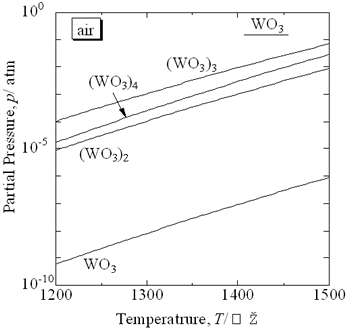 | Figure 1. Partial gas pressure of tungsten oxides of WO3 in air at high temperatures. | Experimental Procedure Figure 2 shows the commercial hard-metal cutting tool used in this work. A half of the hard-metal chip was used as a specimen for the oxidation experiment. Figure 3 shows the schematic illustration of the apparatus for the oxidation experiment. The specimen was put in an alumina or mullite container, which was suspended in an electric furnace. A mullite tube was set above the specimen to introduce a stream of dried air. The specimen was oxidized at temperature raging from 1200 to 1300°C. 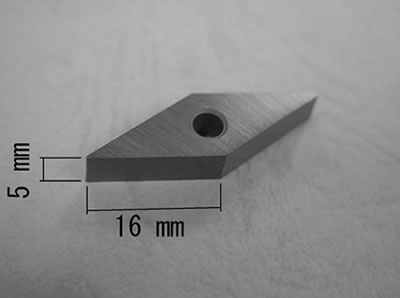 | Figure 2. Sample of a WC hard-metal chip. | 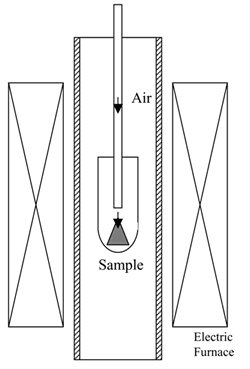 | Figure 3. Schematic illustration of the experimental equipment. | Phase identification of an oxidized specimen was carried out by X-ray diffraction (XRD). Microstructure of an oxidized sample was observed by scanning electron microscope (SEM) and electron probe microanalysis (EPMA). White powder, which appeared on the inside of furnace tube after oxidation experiments, was collected carefully and was identified by XRD. Results Figure 4 shows the specimen oxidized at 1300°C for 3 h. Liquid phase forms and covers the surface of specimen during oxidation in air. Figure 5 shows the microstructure of oxidized layer on the specimen. The oxidized layer consists of two regions. Oxide products were identified as WO3 and CoWO4 by XRD. Since the top layer, which is the molten phase, includes Co and W, it can be identified as CoWO4. Molten CoWO4 covered the specimen during oxidation at high temperatures in air. 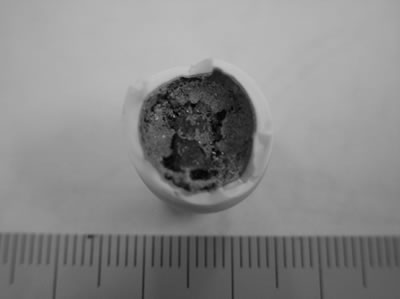 | Figure 4. Surface of the specimen oxidized at 1300°C for 3 h in air. | 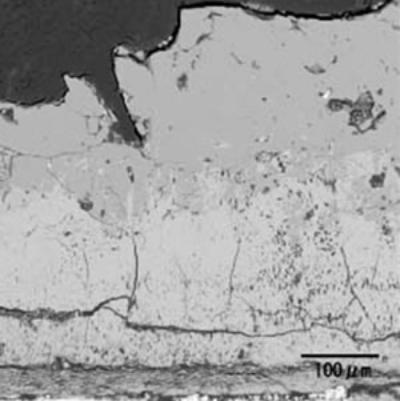 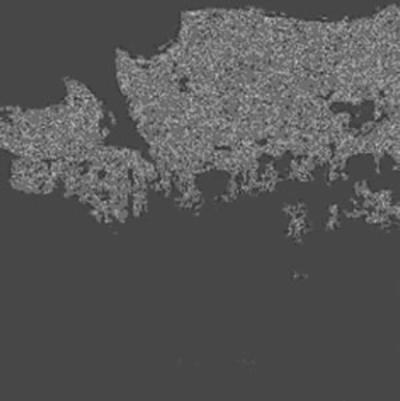 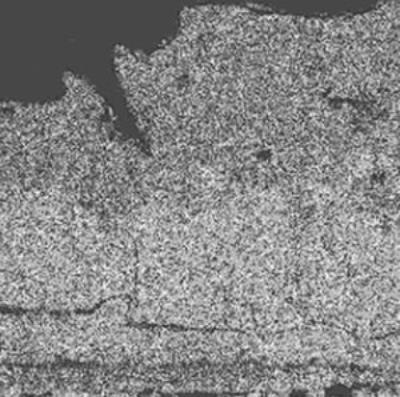 | Figure 5. Microstructure of oxidized layer of WC hard-metal chip at 1300°C. (a) SEM image, (b) Co X ray-map and (c) W X-ray map. | Figure 6 shows the collected powder after oxidation process at 1300°C for 3 h in air. This white powder was collected mainly on the inside wall of the furnace tube as shown in Fig. 6 (b). The collected powder was identified as WO3 by XRD. Figure 7 shows amount of collected WO3 as a function of oxidation temperature with different rates of airflow. With increasing oxidation temperature, the amount of WO3 powder increases. The amount of WO3 collected was, however, very small under each experimental conditions. 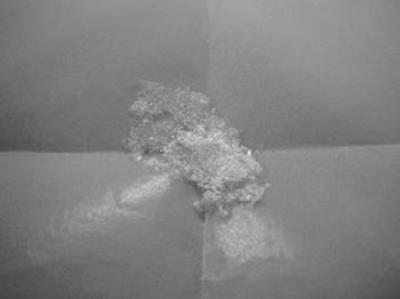 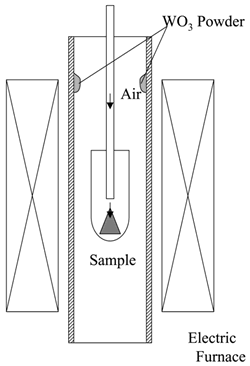 | Figure 6. Collected powder after oxidation of WC hard-metal chip at 1300°C in air. (a) the collected WO3 powder and (b) the position which the WO3 powder deposited during high-temperature oxidation of the WC hard-metal chip. | 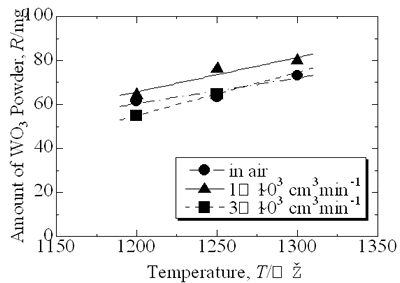 | Figure 7. Amount of collected WO3 powder as a function of oxidation temperature. | Discussion The amount of WO3 powder collected was very small in comparison with the value calculated by using the Langmuir equation. This is caused by existence of molten CoWO4 on the surface of the hard-metal chip during oxidation. Partial pressure of tungsten oxides of CoWO4 can be expressed as follows: (2) That is, (3) where aCoO, ΔG°(2), and R are activity of CoO, the standard Gibbs energy change of reaction (2) and the gas constant, respectively. Because tungsten oxides are evaporated from molten CoWO4, the activity of CoO would be high on the surface, i.e., the activity of WO3 would be low. Here, the activity of CoO is assumed to be unity, the partial pressure of tungsten oxides can be calculated by using the thermodynamic data reported by Barin [3]. Figure 8 shows the equilibrium partial pressure of tungsten oxides from CoWO4 under unity in activity of CoO. At 1300°C, the highest gas pressure is 10-8 atm of (WO3)2 from CoWO4 and is 4 decades lower than the value of (WO3)3 from pure WO3. Since the evaporation flux assuming the Langmuir theory is proportional to the gas pressure, the amount of collected WO3 is in agreement with the order of magnitude of the theoretical value. In order to increase the evaporation rate of WO3, further research is necessary. Conclusions A recycling process for WC hard-metals by applying high-temperature oxidation was proposed. In order to establish the proposed recycle process of the WC hard-metals, evaporation of WO3 from a WC-Co chip was investigated at temperatures ranging from 1200 to 1300°C. Although pure WO3 was obtained by high-temperature oxidation of commercial WC-Co hard-metal chip in air, the evaporation of WO3 was very slow. A molten CoWO4 covered the surface of the hard-metal chip. Decrease in activity of WO3 due to the formation of CoWO4 on the sample reduced partial pressure of gaseous tungsten oxides, and resulted in evaporation rate of WO3. Further investigation to increase evaporation rate of gaseous tungsten oxides is required. Acknowledgement The authors wish to express their gratitude to Niigata prefecture for partially supporting this work though Shinanogawa Technoporis development organization. Reference 1. Report of the Rare Metal Brach, Mining Council in Ministry of Economy, Trade and Industry of Japan, “Going Steady Supply of Rare Metals Supporting Frontier”, p21 (2000). 2. B. F. Kieffer and E. F. Baroch, “Recycle of Tungsten Carbide and Mill Scrap”, Extr. Metall. Refract. Met., Proc. Symp. Ed. by Sohn, H. Y.; Carlson, O. Norman; Smith, J. Thomas, (Publisher: Metall. Soc. AIME, Warrendale, PA, 1981), pp. 273-94. 3. I. Barin, Thermochemical Data of Pure Substances, 3rd Edition, (VCH, Weinheim, 1995). 4. N. E. Fouad, K. M. E. Attyia and M. I. Zaki, “Thermogravimetry of WO3 Reduction in Hydrogen: Kinetic Characterization of Autocatalytic Effects”, Powder Tech., 74 [1] (1993) 31-37. 5. D. S. Venables and M. E. Brown, “Reduction of Tungsten Oxides with Carbon. Part 1. Thermal Analysis”, Therm. Acta, 282-283 [10] (1996) 251-264. 6. D. S. Venables and M. E. Brown, “Reduction of Tungsten Oxides with Carbon. Part 2. Tube Furnace Experiments”, Therm. Acta, 282-283 [10] (1996) 265-276. 7. D. S. Venables and M. E. Brown, “Reduction of Tungsten Oxides with Hydrogen and Carbon”, Therm. Acta, 285 [2] (1996) 361-382. 8. A. Hara, M. Miyake, T. Yamamoto, “Studies on Direct Carburization of WC from the Mixture of WO3 and Carbon”, J Powder Powder Metall Jpn., 22 [1] (1975) 82-86. 9. M. Miyake and A. Hara, “On the Carbothermic Reduction of WO3 Powder”, J Powder Powder Metall Jpn., 26 [1] (1975) 92-97. 10. M. Miyake and A. Hara, “On the Carbon Reductions and Carburization of WO3 with Trial Rotary Carburization Furnace”, J Powder Powder Metall Jpn., 26 [2] (1975) 98-103. 11. M. Miyake, A. Hara and T. Sho, “The Direct Production of WC From WO3 by Using Two Rotary Cauburization Furnaces”, J Powder Powder Metall Jpn., 26 [3] (1975) 104-109. 12. F. C. Nava Alonso, M. L. Zambrano Morales, A. Uribe Salas and J. E. Bedolla Becerril, “Tungsten Trioxide Reduction-Carburization with Carbon Monoxide-Carbon Dioxide Mixtures: Kinetics and Thermodynamics”, Intl. J. Mine. Proc., 20 [1-2] (1987) 137-151. 13. D. S. Venables and M. E. Brown, “Reduction of Tungsten Oxides with Carbon Monooxide”, Thermochimica Acta, 291 [1-2] (1997) 131-140. 14. J. M. Giraudon, P. Devassine, J. F. Lamonier, L. Delannoy, L. Leclercq and G. Leclercq, “Synthesis of Tungsten Carbides by Temperature-Programmed Reaction with CH4-H2 Mixture. Influence of the CH4 and Hydrogen Content in the Carburizing Mixture”, J. Solid State Chem., 154 (2000) 412-426 Contact Details |