Introduction The quantity of the heavy oil fly ash which is generated recently in 2002 at ESP (electrostatic precipitator) of power plants in Korea is approximately 10,000 tons and most of it is being incinerated or re-utilized as a desulfurizing agent. However, for economical efficiency, the power plants are planning to use heavy oil containing high sulfur; therefore, they will generate more than 20,000 tons of the heavy oil fly ash annually and it is predicted to be difficult to reutilize the heavy oil fly ash as a desulfurizing agent due to the large quantity of sulfur in the heavy oil fly ash. As dust gathers at the electronic dust-gathering machine in a power plant which is fueled with heavy oil, heavy oil fly ash consists of inorganic substances such as SiO2, Fe2O3, and Al2O3 with 70~80% of unburned carbon. The heavy oil fly ash also contains heavy metals (e.g. vanadium and nickel) which existed in the crude petroleum at the outset and they are increased during the process of incineration [1]. Several studies to recover the heavy metals in the heavy oil fly ash have been conducted as ways of reutilizing the heavy oil fly ash [2, 3], but they are not in common use because the content of heavy metals in the heavy oil fly ash varies and there are problems of treatment of sludge after the extraction. This study investigated physical and the chemical properties of heavy oil fly ash in order to find out the ways of efficient reutilization of the heavy oil fly ash. Experimental results were carried out to determine the content of unburned carbon, color, X-ray diffraction (XRD) data, Scanning electron microscope (SEM), particle size, and the variation experimental result as applied to cement mortars. Experimental Procedure The heavy oil fly ash gathered at electrostatic precipitator (ESP) of Pyeong Taek Thermoelectric Power Station has been used as a sample for the experimental work and it has been compared to carbon black used as a black pigment for secondary cementious materials. Its moisture content has been calculated by measuring the weight in the oven at 105˚C after drying. It’s true density and bulk density have been measured by Korea industrial standard KS L 5110(testing method for specific gravity of hydraulic cement). Porosity of the sample was measured using a porosimeter (Micromeritics DR, NORCROSS, GA 30093, USA). Chemical analysis was measured by the chemical element analyzer. Eltra Gmbh CS-2000 instrument (Germany) was used for carbon and sulfur analysis and Eltra Gmbh ON-900 instrument (Germany) was used for oxygen and nitrogen analysis. NETZSCH Simultaneous Thermal Analyzer (Netzsch, STA 409 C/3/F Germany) was used for DT-DSC analysis under atmospheric condition. The temperature was increased 10℃/min up to 1,000˚C. Its color has been measured with a color measuring instrument of Hunter Corp (Gretag Macbeth Color-eye 3100). Particle size distribution of heavy oil fly ash was measured with Malverion particle size analyzer (Mastersizer S Ver. 2.15, England). The phase analysis of heavy oil fly ash were carried out using a X-ray powder diffractrometer (MAC Science Co., Ltd.). In order to show the change of physical property when it is added to cementious materials, the change of compressive strength has been measured by Korea industrial standard KS L 5105( testing method for compressive strength of hydraulic cement mortar). Results and Discussion The content of moisture, density and porosity of the heavy oil fly ash are listed in Table 1. The bulk density of the heavy oil fly ash was 0.52 g cm-3 and its true density was 2.15 g cm-3; they differ for carbon black. Its porosity was 10.31%; it is lower than carbon black which is being used as a black pigment. Table 1. Physical properties of the heavy oil fly ash. | Heavy Oil Fly Ash | 11.54 | 0.52 | 2.15 | 10.31 | Carbon Black | 14.77 | 1.28 | 1.98 | 18.52 | Table 2 lists chemical analysis data for composition of heavy oil fly ash and carbon black samples. As seen in the table, heavy oil fly ash is mainly composed of carbon, sulfur and residue ash, whereas carbon is dominant content of carbon black. Comparing with carbon black sample, heavy oil fly ash contains lower carbon content and higher amount of sulfur and residue ash. Lower carbon content in heavy oil fly ash attributed to higher combustion rate of heavy oil. Table 2. Chemical analysis data and residue ash content. (wt %) | Heavy Oil Fly Ash | 3.26 | 76.13 | 1.92 | 1.24 | 19.85 | Carbon Black | 0.79 | 97.87 | 1.25 | 0.92 | 0.8 | The result of color measurement is listed in Table 3. The “L” value shows lightness, “a” and “b” value shows red and yellow respectively. According to the result, Lightness value of heavy oil fly ash is 46.493 which is close to the Carbon Black. The color measurement of heavy oil fly ash is decreased a little as a and b value are -0.111 and 0.066, compared to carbon black which is used as a black pigment. Table 3. The result of color measurement. | Heavy Oil Fly Ash | 46.493 | -0.111 | 0.066 | L | Lightness | Carbon Black | 44.385 | -0.170 | -0.335 | a | (+) red, (-) green | b | (+) yellow, (-) blue | The DT-DSC analysis of the heavy oil fly ash and carbon black is shown in Figure 1. According to the DT-DSC analysis of the heavy oil fly ash, the weight begins to decrease at around 400˚C and the decreasing rate is about 73%; DSC data shows an exothermic peak as the weight decreases and the weight decreasing and the heat generation is mostly because unburned carbon in the heavy oil fly ash burns. In case of carbon black, the weight decreasing rate and heat generation peak are larger than those of the heavy oil fly ash and this is assumed that the amount of carbon in carbon black is higher than that of the heavy oil fly ash. 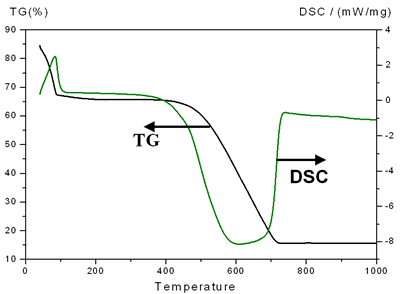 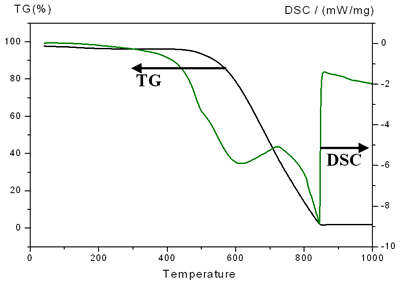 | Figure 1. DT-DSC Analysis of heavy oil fly ash and carbon black. | The XRD patterns of the heavy oil fly ash and carbon black are similar to each other and they are both amorphous to X-ray. Generally the crystal structure of the heavy oil fly ash is known that it consists of carbon in amorphous state and metallic sulfate (Mx(SO4)y) or metallic oxidized material (MxOy). The SEM micrographs are shown in Figure 2, and they confirm that the particle size of heavy oil fly ash ranges from 10 to 120 μm, which is larger than that of carbon black, and contains small pores few μm in sizes. Small pores may have formed during the combustion process of heavy oil fly ash. 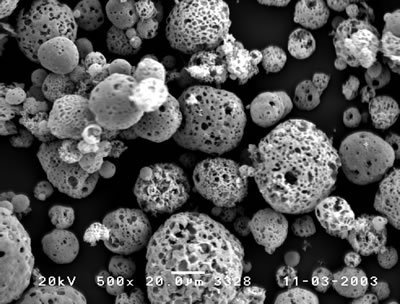 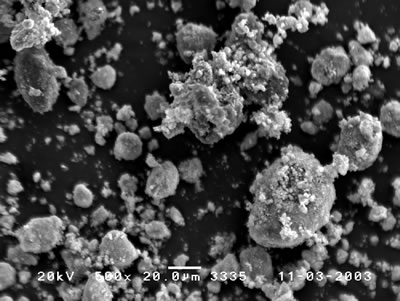 | Figure 2. The SEM micrograph data. | The particle size distributions of the heavy oil fly ash and carbon black are shown in Figure 3. The average particle size of the heavy oil fly ash is about 45 μm and it is ranged from 0.06 μm in the form of the ultra fine to 120 μm. Most of particles of carbon black are smaller than those of heavy oil fly ash. Particle size distribution of carbon black exhibits bimodal shape as shown in Figure 3 (b). 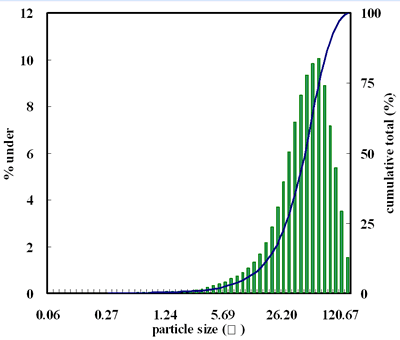 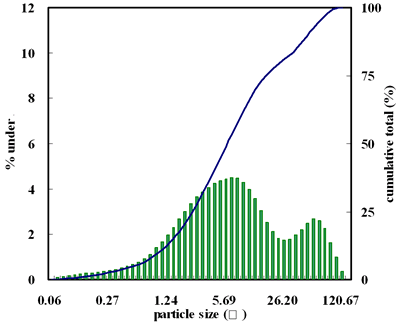 | Figure 3. The measurement result of particle size. | When we consider to re-utilize as a black pigment or admixture for secondary cementious material, it is required that the cementious material products should possess suitable properties. To investigate the possibility of replacing carbon black with heavy oil fly ash, the change of compressive strength has been measured by KS L 5105. Figure 4 shows the change of strength in cement mortar for each quantity of the added heavy oil fly ash. As the quantity of addition is 2% or 4%, it is rather stronger than the reference; but it shows decrease of strength at 6% or 8%. It shows the result of the test processed with domestic pigment (carbon black) under the identical situation in order to compare it to the heavy oil fly ash. The domestic pigment shows remarkable decrease of strength as the quantity of addition increases. 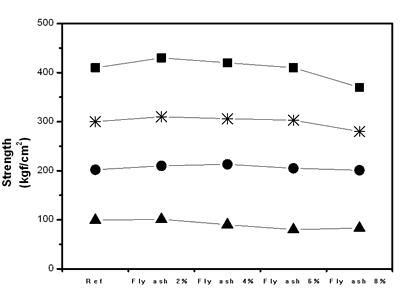 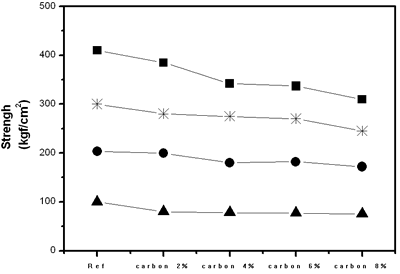  | Figure 4. Change of strength in cement mortar. | Compressive strength of the carbon black in mortar test is rapidly decreased with increasing addition. In contrast, compressive strength of the heavy oil fly ash is insensitive to increase of addition since the residue ash such as SiO2 and CaO in glass state contributes to the formation of hydrate cementious materials. Conclusion In this study the physical and chemical properties of fly ash generated from heavy oil are analyzed and compared to those of carbon black to investigate the possibility of reutilization of it as a black pigment for secondary cementious material. Heavy oil fly ash is mainly composed of carbon, sulfur and residue ash, whereas carbon is dominant content of carbon black. Comparing with carbon black sample, heavy oil fly ash contains lower carbon content and higher amount of sulfur and residue ash. Lower carbon content in heavy oil fly ash attributed to higher combustion rate of heavy oil. The particle size ranged from 10 to 120 μm, and XRD data confirms that it is composed of amorphous carbon. Characteristic color property of fly ash was similar to carbon black. According to the SEM result, heavy oil fly ash has spherical shape. The result of mortar test shows stable compressive strength (Figure 4) with increasing heavy oil fly ash additions. It is attributed that glass state inorganic substances such as SiO2, Fe2O3, Al2O3 and CaO in heavy oil fly ash contribute to the formation of hydrate cementious material to enhance compressive strength. According to the results achieved for this study, heavy oil fly ash has good physical and chemical properties. There is a possibility of finding ways to substitute carbon black for the heavy oil fly ash for secondary cementious materials through several additional experiments. Acknowledgements This work was supported by the financial support of “Electric Power Industry Technology Research” of the Ministry of commerce, industry and energy, Korea. References 1. S.K. Hwang, J.H. Park, S.U. Hong, J.H. Jung, M.Y. Jung, Y.U. Son and K.J. Cho, "Engineering Development and Operation for Heavy Oil Fly Ash Incineration Plant”, KEPRI-93C-T04. Korea Electric Power Research Institute (January 1996). 2. Y.T. Riu, B.G. Kim, Y.Y. Choi, S.Y. Hong, S.K. Hwang and J.H. Park, " Properties and combustion charateristics of heavy oil fly ash", J. Korea Solid Wastes Engineering Society, 13 (1996) 236-246. 3. Sandra Vitolo, Maurizia Seggiani and Francesco Falaschi, "Recovery of Vanadium from a Previously Burned Heavy Oil Fly Ash”, Hydrometallurgy, 62 (December 2001) 145-150. Contact Details |