Introduction In 2002, sewage sludge of 5,689 tons per day was discharged from a sewage disposal plant in Korea. And it is expected that the discharge will increase to about 9,000 ton per day in 2005. At present, most of sewage sludge is thrown away into the sea, reclaimed into the land or incinerated. But the prohibition act of the reclamation into the land in Korea has been taken into effect since July 2003, and London agreement for the prohibition of marine pollution by dumping of wastes and other matters will come into effect in 2004. Recently, re-utilization of sewage sludge in the cement kiln process has drawn much attention to recycling of wastes and reducing environmental pollution [1]. The use of sewage sludge as a raw material for the production of cement is an effective method, since the organic components may serve as fuel while the inorganic components such as SiO2, Al2O3, Fe2O3 components offer as the raw material for the clinker. However one of the obstacles to this application to cement kilns is the relatively high P2O5 and Cl content in sewage sludge. Many investigators have dealt with the influence of P2O5 and sewage sludge on cement qualities [2, 3]. In this study, the effect of P2O5 and chloride on clinkering reaction is investigated for the purpose of reutilization of sewage sludge from a sewage disposal plant during cement clinkering process. Sewage sludge’s analysis showed it’s chloride content from 300 ppm to 10,000 ppm varying in different localities (coast or urban). We expected the chloride contents in the cement raw mix would be maximum 400 ppm, by applying sewage sludge as a raw materials. However, the chloride contents in the kiln process expected to be 15,000 ppm by volatilized chloride component. To examine clinkering reaction in a real kiln, we experimented with increased chloride component to 20,000 ppm in the raw mix. Cement industries are using many wastes which have high P2O5 contents [4, 5], we experimented by increasing the P2O5 contents to 2,000 ppm in the raw mix to examine the effect of P2O5 on clinkering reaction. Experimental Procedure A composite sample was prepared by mixing with 99.3 wt% kiln feed raw material and 0.7 wt% bituminous coal ash. Chemical composition of kiln feed raw material is SiO2 (13.75 wt%), Al2O3 (3.39 wt%), Fe2O3 (2.15 wt%) and CaO (42.12 wt%). Bituminous coal ash is composed of SiO2 (51.77 wt%), Al2O3 (24.02 wt%), Fe2O3 (8.59 wt%) and CaO (7.81 wt%). To investigate the effect of P2O5 and chloride on clinkering reaction, P2O5 and Cl were added to the composite sample about 0 ~ 2.0 wt% using P2O5 and NH4Cl. The modules of composite samples were prepared and fired separately in platinum dishes in an electronic furnace at a heating rate of 10°C/min and retained at a final temperature of at 1450°C for 20 min. The resulting clinker was allowed to cool initially within the furnace up to 1350°C and then rapidly quenched. The level of the free lime was determined by the ethylene glycol extraction method. Also, Cl component of the clinker was determined by a Potentiograph. A RigakuD/max-RINT 2500 diffractor with Cu Kα radiation was used for X-ray diffraction (XRD) analysis of clinker mineral. Theoretical amount of clinker mineral sintered at different temperatures was calculated using a TOPAS software developed by Bruker Co. Results and Discussion Chemical analysis data of composite sample prepared by mixing kiln feed raw material (99.3 wt%) and bituminous coal ash (0.7 wt%) and theoretical amounts of clinker mineral calculated from the chemical analysis data of composite sample are shown in Table 1. Table 1. Chemical analysis data of composite sample and calculated amount of clinker mineral. (Units wt%) Chemical analysis of composite sample | Calculated amount of clinker mineral | SiO2 | Al2O3 | Fe2O3 | CaO | MgO | C3S | C2S | C3A | C4AF | 14.02 | 3.53 | 2.17 | 41.88 | 1.90 | 56.95 | 18.73 | 8.74 | 10.12 | 0.5 wt% ~ 2.0 wt% of P2O5 and Cl were added to the composite sample using a P2O5 and NH4Cl and sintered at 1450°C for 20 min to form a clinker mineral. The level of the free lime was determined by the ethylene glycol extraction method. Results of free lime and Cl content of the clinker samples with varying P2O5 and Cl contents are summarized in Figure 1. It is seen that the addition of ranging from 0.5 wt% to 2.0 wt% P2O5 to the composite sample increases the free lime content of the clinker sample from 0.51 wt% to 5.07 wt%. The results are in agreement with the previous result in the literature [6]. 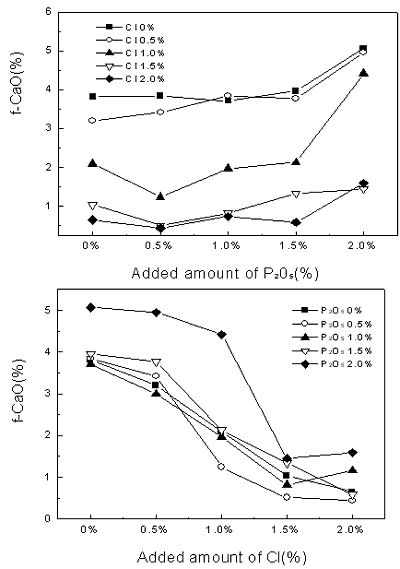 | Figure 1. Changes of free-CaO amount in clinker mineral with variation of P2O5 and Cl contents. | As seen in Figure 1, for even up to 0.5 wt% of P2O5 addition, free lime content of the clinker is constant, while the addition of P2O5 from 0.5 wt % to 2.0 wt% to the composite sample increases rapidly the free lime content. Also, free lime content of the clinker decreases with increasing addition of Cl. It is attributed to the fact that Cl compound plays a role as an accelerator for the liquid-solid reaction of clinkering reaction since Cl compound turns into liquid phase at low temperature. The XRD results of clinker samples with varying P2O5 and Cl contents are shown in Figure 2. From the XRD results, it is evident that clinker produced at 1450°C for 20 min form all major cement mineralogical phases like alite(C3S), belite(C2S), ferrite (C4AF) and aluminate (C3A). The clinker made from the addition of P2O5 to the composite sample in Figure 2, is found to have a slightly decreased C3S peak and an increased C2S, f-CaO peak. 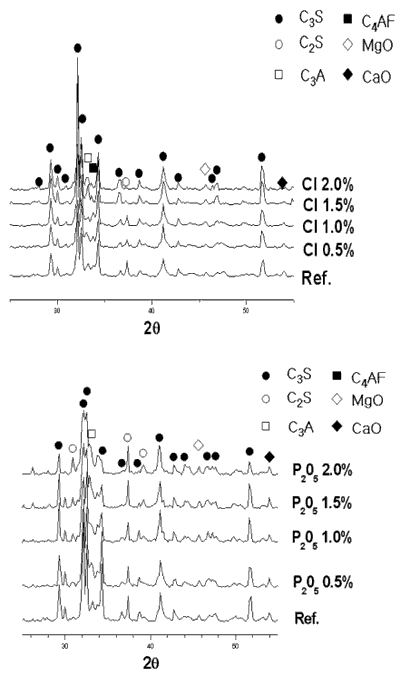 | Figure 2. X-ray powder diffraction data with variation of P2O5 and Cl contents. | Theoretical amounts of clinker mineral with various P2O5 and Cl contents were calculated using a TOPAS software and the data are shown in Figures 3 and 4. Although calculated values of alite mineral content and belite mineral content in clinker were 56.95% and 18.73%, respectively, actual alite mineral content and belite mineral content in clinker were 45.50% and 29.80%. As seen in Figure 3, content of alite decreases and belite content increases gradually. This result is in agreement with the previous results [2, 6, 7]. This is because it was reported that P2O5 forms a solid solution with C2S thus stabilizing it, and cause a reduction in the concentration of C3S with a corresponding increase in the free lime content [7, 8]. The alite content decreases from 45% to 15% by the addition of up to 2% P2O5, and belite content increases from 30% to 55%. This result indicates that the effect of P2O5 has to be controlled to obtain good quality clinker. According to addition of chloride, content of alite(C3S) is decreased from 46% to 15% and content of belite is increased from 30% to 50%. The influence of chloride on clinker reaction has to be clarified prior to applying the cement kiln process since Cl compounds are known to affect more in the kiln process than the quality of clinker. In general, the production of free lime is proportional to the differential between contents of alite and belite. As shown in Figures 1 and 2, however, addition of P2O5 of up to 2% generates only 3.6% increase of free lime decreasing amount of alite by 30%, which implies that there exists difference in mass balance of alite and free lime. The mismatch of mass balance of clinker mineral in the experiment is attributed to the new clinker minerals were formed with increasing of P2O5 contents in the raw mix. The contents of ferrite mineral and aluminate mineral increased with the addition of P2O5 and decreased with Cl addition. 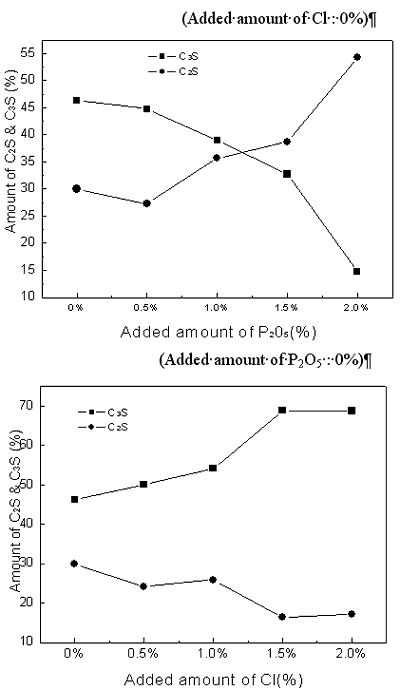 | Figure 3. Changes of Alite(C3S) and Belite(C2S) contents in clinker mineral with variation of P2O5 and Cl contents. | 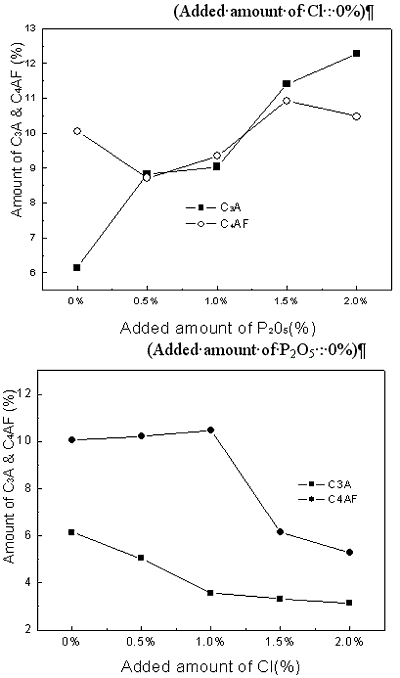 | Figure 4. Change of Ferrite(C4AF) and Aluminate(C3A) contents in clinker mineral with variation of P2O5 and Cl contents. | Conclusion To explore the possibility of effective reutilization of sewage sludge into cement kiln process, characterization of clinkering reaction was carried out with various amounts of P2O5 and Cl addition. These results indicate that the amount of free CaO is increased and amounts of alite, ferrite and aluminate minerals are decreased with P2O5 addition. The Cl addition exhibits opposite properties to P2O5 addition. However, the chloride influence on clinker reaction are clarified prior to applying the cement kiln process since Cl compounds are known to affect more in the kiln process than the quality of clinker. From this experiment, we knew the influence of P2O5 and chloride components on clinkering reaction. Therefore, this experiment provided the basis of reutilization in the cement industries which has high P2O5 and chloride components wastes. References 1. H. Uchikawa, “Cement and Concrete Industry Orienting Toward Environmental Load Reduction and Waste Recycling”, Chichibu Onoda Cement Research report, 133 (1997) 1-33. 2. T. Shirasaka, D. Sawaki and H. Uchikawa, “Influence of Phosphorus on Clinker Constituent Phase and Hydration of Cement”, Japan Cement Association Proceedings Of Cement & Concrete, 50 (1996) 8-13. 3. K. Akatsu, K. Maeda and I. Ikeda, “The Effect of Cr2O3 and P2O5 on the Strength and Color of Portland Cement Clinker”, The Cement Association of Japan Review of the 24th General meetings, (1970) 20-23. 4. T. Tanosaki, K. Nozaki, M. Matsumoto, K. Usukura and K. Miyashige, “Domestic Water Treatment and Properties of Sludge in Japan”, Chichiba Onoda Cement Research report, 32 (1997) 55-74. 5. Lee Jong Ryul, Cha Chun Su and Woo-Teck Kwon, “Sewage sludges application to cement kiln process”, Construction Materials, (2002) 84-103. 6. M. Kanaya, N. Ozawa, K. Honma and M. Ichikawa, “Influence of Phosphorus on the Quality of Clinker” Cement Science and Concrete Technology, 53 (1999) 10-15. 7. L. Halicz, Y. Nathan and L. Ben-Dor, “The influence of P2O5 on clinker reactions” Cement and concrete research, 14 (1983) 11-18. 8. J. Hakoshima and M. Kume, “The Influence of Phosphorus and Magnesium on the Characteristics of Clinker Minerals”, Cement Science and Concrete Technology, 53 (1999) 16-22. Contact Details Woo-Teck Kwon, Young-Hee Kim, Yong-Sik Chu, Jong-Kyu Lee, In-Seob Kim and Soo-Ryong Kim Department of Ceramics Building Materials Korea Institute of Ceramic Engineering and Technology 233-5, Gasan-Dong, Guemcheon-Gu Seoul, 153-801 Korea E-mail: [email protected] This paper was also published in print form in “Advances in Technology of Materials and Materials Processing”, 7, [1] (2005), 63-66. |