Introduction The Yttrium Aluminum Garnet is used in the production of laser systems in solid state, for coating electronic devices, as well as for tubes of cathodic rays, and lately it has been considered as a suitable material for structural applications at high temperatures [1, 2]. These applications are intimately related with its optical properties, chemical stability at high temperatures, good corrosion resistance and mechanical properties [2-4]. The first method that was used for the synthesis of the YAG phase was the conventional method of powders [3], but the problem with this route was that it requires a high temperature and a long time of calcination for the formation of the YAG phase. This causes grain growth and therefore a decrease of mechanical properties of the final products. Due to this, a series of wet methods have been developed [4-9], with the purpose of reducing the formation temperature and the impurities of this compound. Liu et al. [4] synthesized the YAG phase, starting from three-ethanolamine, nitric acid, yttrium nitrate and aluminum. By means of thermal treatments they produced a precursor that later was calcined at various temperatures, and observed the formation of the YAG phase and YAlO3 (YAP) at 850°C. The metastable YAlO3 phase disappeared after 950°C. Lu et al. [5] obtained YAG starting from the same salts as Liu et al., except that they added pure aluminum in the form of pellets and substituted the nitric acid for citric acid. The precursor was a sol, and by calcination obtained the YAG phase at 900°C, without the presence of intermediate phases. Han [6] synthesized YAG by dissolving powder of Y2O3 in an alumina sol and the crystallization route presented the metastable hexagonal phase of YAlO3, which disappeared completely as the powders were calcined at temperatures higher than 950°C. The presence of intermediate phases has also been observed in the precipitation method with urea [7], where other phases like Y4Al2O9 (YAM), Y2O3 and Y2O2SO4 were observed. The method of the precursory citrate [8] diminished the crystallization temperature considerably until 700°C, but, it requires long thermal treatments. However, the method of homogeneous precipitation [9] has yielded the pure YAG phase at 850°C, but it requires calcining at 1400°C to achieve a complete crystallization. This work reports the use of a modified route of the citrate precursor to obtain totally pure YAG phase, without the observation of intermediate phases, reducing the stages of thermal treatments and milling with respect to the route of the citrate precursor. Experimental The starting materials used in the present work were ethylene glycol (99.9% purity, J. T. Baker, Phillipsburg USA), monohydrated citric acid (99.9%, J. T. Baker), monohydrated aluminum nitride (99.9%, J. T. Baker), hexahydrated yttrium nitride (99.9%, Aldrich Chem. Com., Milwaukee USA), and deionized water. Initially aluminum nitride and yttrium nitride were dissolved separately in deionized water in the stoichiometric amounts and mixed in order to obtain a final solution with a molar yttrium/aluminum relationship of 3:5. Then, citric acid previously dissolved in deionized water and ethylene glycol were added to the solution. The resulting solution was stirred for 15 min to assure homogeneous mixing of components. This solution was fed to a spray dryer where the solvent was pulverized into small drops and evaporated in fraction of seconds giving a homogenous wet powder. Finally, the precursor powders were calcined at various temperatures. The thermal behavior of YAG phase transformation was followed by means of X-ray diffraction (XRD: SIEMENS D5000 Diffractometer), simultaneous thermal analysis (TA Instruments SDT Q600), and thermodilatometric analysis (THETA Instruments Thermodilatometer). The morphology was observed by scanning electron microscopy (SEM: JEOL JSM 6400). The experimental route is shown in Figure 1. 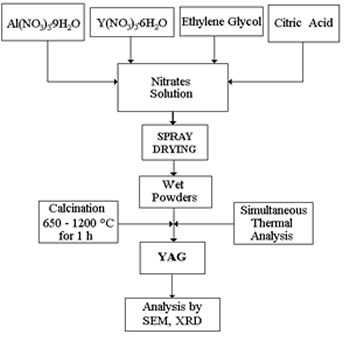 | Figure 1. Schematic diagram of experimental route. | Results and Discussion Simultaneous thermal analysis results are shown in Figure 2. Figure 2(a) corresponds to the thermogravimetric curve where a steep slope is observed between 100 and 600°C due to loss of water and nitrides from the system. The subsequent behavior indicates no weight change. Crystallization, as indicated by the DTA curve (Figure 2(b)), occurs at <900°C with no weight change but only an atomic re-arrangement to form the characteristic crystalline structure. At 1000°C it is observed a significant weight loss in the material (~ 6%) that might be due to the presence of residual carbon from the initial addition of citric acid and its oxidation at this temperature [8]. Figure 2(b) shows the DTA curve and its derivative. About 100°C a small endothermic peak is observed corresponding to the removal of water and ethylene glycol; in the range of 350-600 °C, small changes in the derivative curve indicate the removal of nitrates. At 800°C it can be noticed a major exothermic peak in the derivative curve corresponding to the crystallization of YAG phase and was confirmed by XRD analysis. Finally, in the range of 1025-1075°C two exothermic peaks appear due to the oxidation of residual carbon. 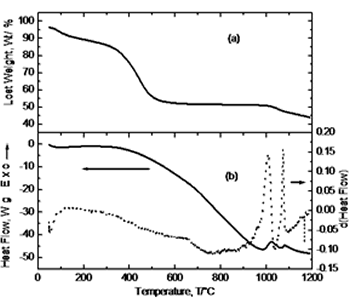 | Figure 2. Simultaneous thermal analysis: (a) thermogravimetric curve (TGA), and (b) differential thermal analysis curve (DTA). | Figure 3 exhibits the thermodilatometric analysis curve of processed powders. In this figure it can be observed that in the range of 25-780°C the sample undergoes a contraction associated with the approaching of the components due to the loss of organic compounds and around 825°C initiates an expansion because of the atomic re-arrangement to reach the equilibrium positions in the crystalline structure of YAG phase. With the derivative curve, the maximum peak was determined which corresponds to the maximum rate of phase transformation in according with the thermal analysis and XRD (Figure 4). From the above, it can be concluded that the crystallization takes place at this temperature. Above 850°C, the sample undergoes a shrinkage because of grain growth and sintering. 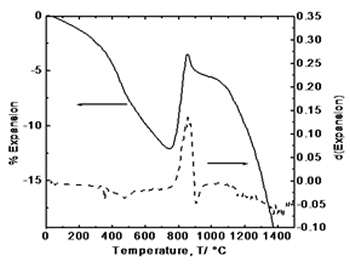 | Figure 3. Thermodilatometric analysis curve. | Figure 4 displays the X-ray diffraction patterns for the calcined powders at 750, 800, 825, 850, 900, and 1200°C, respectively. XRD patterns corresponding at 750 and 800°C show an amorphous phase while in XRD patterns at higher temperatures appears a single crystalline phase of cubic YAG with no intermediate phases, where the most intense reflection belongs to the plane (420) which appears about at 2θ angle of 33 degrees. As the temperature increases, the intensity of the YAG reflections increases and peak-broadening decreases which indicates the crystallinity of the material. 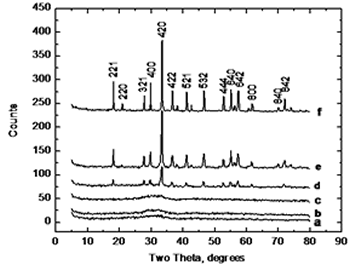 | Figure 4. XRD patterns of samples calcined for 1 hour at various temperatures, a) 750, b) 800, c) 825, d) 850, e) 900 and f) 1200°C. |
XRD analysis suggests a direct crystallization of YAG phase below 900°C without the appearance of intermediate phases such as YAP (Yttrium Aluminum Perovskite) which has been reported that occurs by using other methods [2, 4, 6, 7], and the disappearance of this phase requires temperatures as high as 1200 to 1300°C. This is in agreement with the thermal analysis where the transformation is observed at 825°C. Figure 5 shows a SEM image of a sample calcined at 900°C. It can be observed that powders consist of spherical particles agglomerates below 2 microns in size; this morphology was observed in all samples and is distinctive of powders processed by using spray drying. 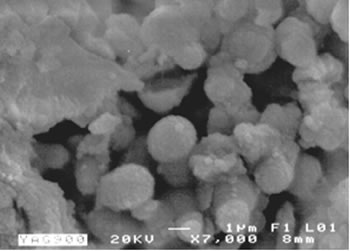 | Figure 5. SEM image of powders calcined at 900ºC for 1 hour. | This technique has some advantages for obtaining single YAG phase where comparing with other techniques. The most important parameters in the YAG formation are the enhanced distribution of aluminum and yttrium ions and the shortening of the effective diffusion distances. It is possible to reach this distribution at atomic level because of the dissolution of salts and organic compounds that after spray drying maintain the high degree of dispersion due to the active groups that fix the cations. Once the organic compound is eliminated, the diffusion distance and the ion distribution remain high [8]. All these factors contribute to decrease the formation temperature of YAG phase below temperatures reported in other work [4, 7, 9]. Conclusions The employment of spray drying diminishes the processing time (approximately 16 hours) with regard to other methods and maintain the high degree of components mixing, moreover it has an important energy saving. Powders consist of spherical particle agglomerates of < 2 microns that results in materials with good fluidity characteristics. By this route YAG phase was synthesized with a formation temperature as low as 825°C according to thermal analysis results which also confirms the high degree of homogenization and short diffusion distances that were obtained by this route. Acknowledgements The authors thank to Ing. F. Solorio and Mrs. V. Luque for assistance with SEM and XRD analysis. References 1. D. R. Messier and George E. Gazza, “Synthesis of MgAl2O4 and Y3Al5O12 by Thermal Descomposition of Hydrated Nitrate Mixtures”, Ceramic Bulletin, 51, 9 (1972) 692-694, 697. 2. J. G. Li, T. Ikegami, J. H. Lee and T. Mori, “Low-Temperature Fabrication of Transparent Yttrium Aluminum Garnet (YAG) Ceramics without Additives”, J. Am. Ceram. Soc., 83, 4 (2000) 961-963. 3. Viechniki, D. and Caslavsky, J.L., “Solid state formation of Nd:Y3Al5O12(Nd:YAG)”, Amer. Ceram. Bull., 58, 8 (1979) 790-791. 4. Y. Liu and Lian Gao, “Low-Temperature Synthesis of Nanocrystalline Yttrium Aluminum Garnet Powder Using Triethanolamine”, J. Am. Ceram. Soc., 86, 10 (2003) 1651-1653. 5. Q. Lu, W. Dong, H. Wang and X. Wang, “A novel Way to Synthesize Yttrium Aluminum Garnet from Metal-Inorganic Precursors”, J. Am. Ceram. Soc., 85, 2 (2002) 490-492. 6. K. R. Han, H. Jin Koo and C. Sup Lim, “A Simple Way to Synthesize Yttrium Aluminum Garnet by Dissolving Yttria Powder in Alumina Sol”, J. Am. Ceram. Soc., 82, 6 (1999) 1598-1600. 7. N. Matsushita, N. Tsuchiya and K. Nakatsuka, “Precipitation and Calcination Processes for Yttrium Aluminum Garnet Precursors Synthesized by the Urea Method”, J. Am. Ceram. Soc., 82, 8 (1999) 1977-1984. 8. M. Cinibulk, “Synthesis of Yttrium Aluminum Garnet from a Mixed-Metal Citrate Precursor”, J. Am. Ceram. Soc., 83, 5 (2000) 1276-1278. 9. D. J. Sordelet, M. Akinc, M. L. Panchula and Y. Han, “Synthesis of Yttrium Aluminum Garnet Precursor Powders by Hmogeneus Precipitacion”, J. of the Europ. Ceram. Soc., 14 (1994) 123-130. Contact Details |