It is a paradox that elastomers whose unique property is high elasticity are rarely used in tension. Elastomeric products are used in areas such as vibration isolation, bridge bearings, suspension bearings, earthquake protection, flexible joints, seals, electrical insulators, energy absorption, hoses, belts, tyres, and many other areas. Virtually all industrial applications utilise rubbers in shear, compression or a combination of these whilst taking advantage of other properties. Typical applications are bridge bearings, suspension bearings for rail vehicles and anti vibration mountings. To be useful most rubber components have to be properly fixed in the appropriate location. Therefore most articles comprise an appropriate rubber shape permanently bonded to suitable rigid mounts, usually steel, for bolting to the structures concerned. Good quality natural rubber compounds can be strongly bonded to properly prepared steel surfaces by standardised one or two coat bonding systems obtained from various trade suppliers. Excellent, reliable bonds can be obtained on a production line basis provided proper attention is given to cleanliness and procedures. Non-bonded components can be used, relying on the high coefficient of friction of rubber to keep the component in position, but are generally much less satisfactory than bonded components, which have more consistent deformation characteristics and can be located much more positively. Also, bonded components can tolerate the load going through a zero or even negative force during unusual situations such as a resonant vibration. Bridge and Suspension Bearings A typical bridge bearing, which generally is a solid square or cylindrical piece of rubber, is sandwiched between steel plates as in figure 1a. Substantial height changes can be avoided when intermediate metal plates are inserted, and bonded into the structure. These contribute to non-linear behaviour by steadily incurring shear and surface tensile forces within the block, which inhibit the large sideways bulge (figure 1b). 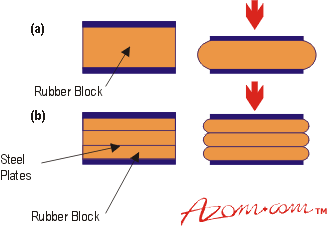 | Figure 1. Behaviour of a typical bridge bearing consisting of (a) a single rubber block and (b) multiple rubber blocks separated by steel plates. | Figure 2 further shows that the insertion of steel plates into a bearing can radically increase the load bearing capacity. Note that inserted plates are completely encapsulated by the rubber to prevent delamination by rusting, bond failure, or water ingress. 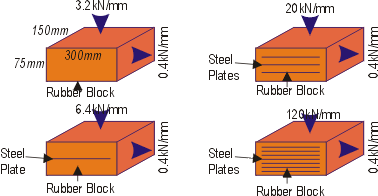 | Figure 2. By increasing the number of steel plates, the load bearing capacity can be increased. | This type of bearing can accommodate vertical deflection (compression), horizontal deflection due to 'spread' or lateral movement (shear) in any direction and tilt (notation) due to flexure. All this is achieved with one solid, maintenance free bearing involving no moving parts: typical sizes would be up to 250mm square and 100 to 150mm thick, with a design life in excess of 50 years, thus replacing complex conventional bearings which require routine maintenance and inspection. An example of a bearing designed for a range of stiffness’s in different directions is shown in figure 3. This type can be used, for example, as suspension units for rail cars. The main weight of the car is carried on the top face and down into the 'V' area, putting the rubber into combined shear and compression, with different load bearing capabilities vertically (up and down the page), in the direction of travel (left to right or right to left across the page) and along the axle (perpendicular to the page). 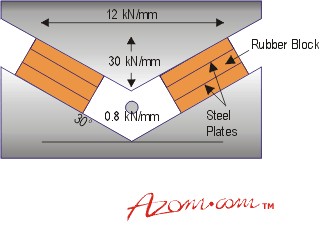 | Figure 3. Bearing design for a range of stiffness’s. | Vibration Isolation All moving or vibrating masses, such as a car engine, have a resonant frequency at which any applied deflection is greatly amplified (figure 4). The bearing design is devised so that the natural frequency of the assembly is some one third of the applied frequency. At this level any applied deflection is suppressed, (figure 4). This is fine in steady state service but of course the mass has to pass through the resonant frequency during starting and stopping. It is therefore essential that the mass be damped to minimise movement, for example the engine compartment is not a large space and excessive movement could damage both engine and body shell. 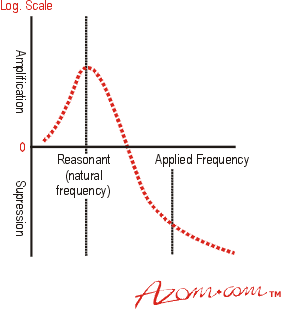 | Figure 4. Frequency of rubber vibration damper compared to the applied frequency. | Steel coiled springs with separate mechanical dampers would be adequate but relatively complex, whereas solid rubber mounts of appropriate design are simpler and superior, using the natural damping qualities (hysteresis) of the elastomer to achieve the performance. Energy Absorption A major application for rubbery materials is in energy absorption, for example absorbing the large amounts of energy from the ‘way’ of a large ship coming in to dock is important to avoid damage to both ship and dockside. Simple dock fenders are often a thick wall tube, wall thickness around 75mm and overall diameter 300mm, giving a collapsing distance of about 150mm before a steep rise in transmitted load becomes apparent. For a typical fender, a load of about 12 tonnes/metre would be required to compress the fender flat. Larger fenders with a range of geometries can provide a collapsing distance of about 1 metre. Lighter construction pneumatic fenders, built similarly to a tyre, are also, available and give very good load deflection characteristics. Other uses for rubber in energy absorption include transportation of delicate or expensive machinery, which can be mounted on collapsible supports for transport. The supports are designed to buckle to extend the load/deflection plot for extra energy absorption. They can also damp the harmonic frequency and suppress excessive movement. |