An initial step in failure analysis is verifying the chemical structure of the material used to fabricate the part. Fourier transform infrared spectroscopy (FTIR) confirmed that the failed material was either a polypropylene homopolymer or copolymer, without any obvious gross differences from the known control sample.
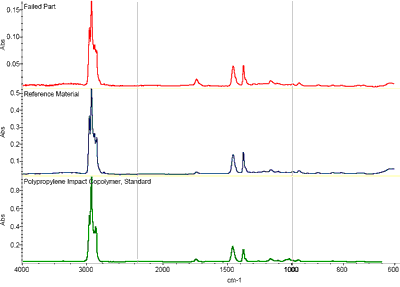
Figure 1. The FTIR results obtained on the failed part material were consistent with a polypropylene homopolymer or copolymer resin.
The next step in material characterization was a melting point determination using differential scanning calorimetry (DSC). The results of this test method confirmed the presence of the correct polypropylene copolymer resin, but also revealed two additional types of polypropylene homopolymers.
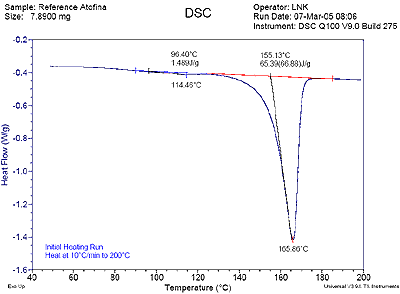
Figure 2. The DSC results obtained on the control sample.
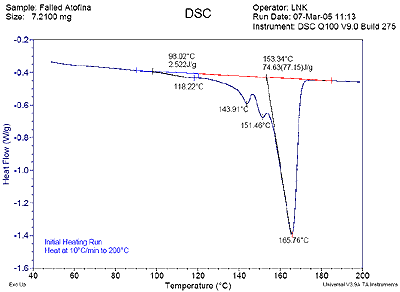
Figure 3. The DSC results obtained on the failed sample showed additional transitions associated with contamination.
Conclusion
The plastic molder was contacted, and denied the use of any regrind in the safety device. After several discussions, it was determined that the colorant supplier had decided to use a lower grade pigment dispersant containing polypropylene homopolymer regrind. While the correct material was also a polypropylene-based resin, the mechanical properties of homopolymers and copolymers are different.
Element Materials Technology determined that the relatively low level of contamination in the safety device changed the overall behavior of the material, enough to cause failures.
Fatigue and Fracture In Environment - Extended Version
Video Credit: Element Materials Technology
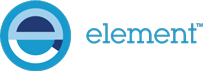
This information has been sourced, reviewed and adapted from materials provided by Element Materials Technology.
For more information on this source, please visit Element Materials Technology.