Introduction Refractory materials can be considered how resistant products to the generation of high temperatures of the process at the furnaces and reactors [1, 2]. The reliability of a refractory for specific applications is determined for his chemical attack resistance to the molten slags and molten products, as soon as his mechanic and thermal resistance in use [3]. By other hand, it knows that all refractory materials are destroyed when they are exposed to the characteristic conditions of each application and a common factor in the destruction is the temperature [4]. For this reason, new refractory materials with high temperature resistance and very high resistance in contact with aggressive environments are required [5, 6]. The glass industry has serious problems of contamination [7, 8] because during the initial melting glass, the refractory brick can be attacked in the most vulnerable points as in the matrix that surrounds the gross particles. The dissolution process of the matrix frees the gross particles and they remain floating in the glass, passing subsequently to the final product [9, 10]. The principal interest of this work is the development of refractory bricks with good mechanical properties and good corrosion resistance [11, 12], taking like departure point the commercial product composition (AZS = alumina-zirconia-silica). Experimental Procedure Raw Materials Selection and Characterization The raw materials selected for the production of AZS compositions were alumina, zirconia and silica, proceeding of two sources: silica sand and silica fume. The difference between raw materials is their particle size, the silica sand presents an approximate particle size of 150 μm while the silica fume is lower than 45 μm, the change was carried out with the objective to obtain homogeneity in the particle sizes of the raw materials with the formulations be prepared. According to it found in the literature [13-15], the AZS refractory materials with alumina-zirconia-silica are used for the glass melting furnaces, and the other side, the presence of carbides provides refractories with better properties such as greater corrosion resistance by molten materials. With the purpose of knowing the characteristics of each raw material, the following analysis techniques were used: x-ray diffraction, scanning electron microscopy and differential thermal analysis. These analysis were carried out taking a representative quantity of each composite of them. Manufacture of AZS Formulations AZS refractories were produced at the laboratory with Al2O3 (43%), ZrO2 (20 and 37%) and SiO2 (20 and 37%), at the same time, AZS refractories with small contents of silicon carbide and magnesium oxide were manufactured with the purpose of obtaining a product with better properties. See Table 1. Table 1. AZS compositions (weight percent of each raw materials) | 1* | 43 | 37 | 20 | -- | -- | 2** | 43 | 20 | 37 | -- | -- | 3*** | 39 | 33 | 18 | 10 | -- | 4*** | 39 | 33 | 18 | -- | 10 | * commercial composition ** low amount of ZrO2 *** AZS with SiC and MgO respectively All raw materials were dried at a temperature of about 110°C during 18 h, three grams of each one of the compositions presented in the Table 1, were mixed, homogenized and pressed to form specimens of 2.5 x 0.5 x 0.5 cm with 13350 N of load, sufficient to compact the dust and to obtain the samples. The burning was carried out at a temperature of 1450°C during 12, 18, 24 and 48 h. The results obtained from RXD and SEM characterization of the AZS prepared indicate the need to change some experimental conditions because the adequate refractory phases formation was not obtained, due to that direct bond among the grains is absent and the material remains without reacting, which can produce problems when the product is in use [16]. New AZS compositions were prepared with the addition of an organic compound (methocel) and silicoaluminate (clay) like bonding materials in the composition 1 (AZS= 43-37-20) with the objective of improving the bond among the grains at the moment of the compaction and press [17]; the similar alumina, zirconia and silica particle sizes (<45 μm) were obtained with the change of the silica sand (150 μm) by silica fume (<45 μm). These formulations were sintered to 1450°C during 12, 18, 24 and 48 h (Table 2). By another side, the pressed load was increased from 13350 to 44500 N to improve the specimen compaction. With the results obtained from characterization of these products with bonding materials, we can see that the addition of these compounds was not necessary for an adequate phases formation, however, the use of silica fume provides homogeneity at the particle sizes and better mullite formation. By other hand, the comparative analysis between commercial AZS and the AZS compositions produced at the laboratory (composition 1: AZS= 43-37-20 and composition 2: AZS= 43-20-37) was obtained with a commercial brick characterized by x-ray diffraction, scanning electron microscopy, differential thermal analysis and the static test of penetration and attack with molten glass. The static test was carried out for 4 h at a temperature of 1450ºC in a gas-air furnace [18]. Table 2. AZS modify compositions. | 1 | 43 | 37 | 20 | -- | -- | -- | 2 | 42.1 | 36.3 | 19.6 | -- | 2 | -- | 3 | 42.1 | 36.3 | 19.6 | -- | -- | 2 | 4 | 43 | 37 | -- | 20 | -- | -- | 5 | 42.1 | 36.3 | -- | 19.6 | 2 | -- | 6 | 42.1 | 36.3 | -- | 19.6 | -- | 2 | These compositions were compacted with two loads 13350 y 44500 N to compare them. Results and Discussion Figures 1 and 2 present the X-Ray diffraction patterns of two compositions with high and low percentage of zirconium oxide, respectively. Although in all cases badeleyite, quartz and corundum (from raw materials) without refractory properties were obtained, also the presence of zircon and mullite is detected. These are highly refractory phases and they can provide excellent properties to the final product, as it knows that the refractory phase formation with low amount of ZrO2 is feasible at similar time and temperature. This observation indicates that the refractory phases formation is independent of the amount of ZrO2 [19]. 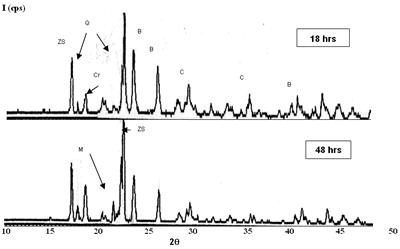 | Figure 1. Composition 1 sintered to 1450°C, load of 13350 N. (B-badeleyite,Q-quartz, Cr-cristobalite, C-corundum, ZS-zircon, M-mullite). | 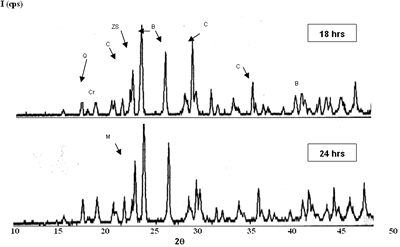 | Figure 2. Composition 2 sintered to 1450C. (B-badeleyite, ZS-zircon, C-corundum, Q-quartz, Cr-cristoballite and M-mullite). | On the other hand, the formulations with carbides and magnesium oxide additions did not present an adequate behavior, because they are not consolidate a refractory matrix and the low melting point phases formation is present, respectively. The XRD patterns of the composition with magnesium oxide addition is detected the cordierite formation, this product has a low melting point (about 1390ºC), which represents a critical problem when the refractory material is in use because the mechanical properties, such as refractariety and mechanical resistant will be decrease. Microscopic characterization of the sintered compositions indicates the presence of large grains of SiO2 (Figure 3). The presence of zircon around the grains is detected by EDS (Figure 4), however, a good bond in the microstructure is not observed, due to the separation between grain and grain, and the presence of the characteristic “needles” of mullite is not detected [20]. Although, with these sinter conditions, temperature and times, we can find refractory phases, it does not mean that product obtained had very good physical properties. The presence of a weak bond between the grains due to a bad compaction of the product because the particle size distribution is not adequate; it can observed to low sinter temperatures. 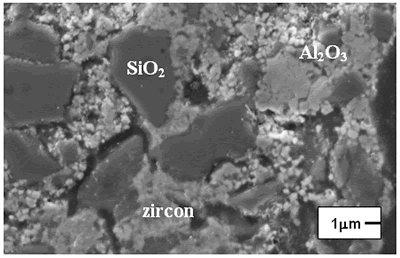 | Figure 3. Composition 1 (1450°C) 18 hours, the microstructure presents separation between grains of SiO2. | Due to the original raw materials (alumina, zirconia and silica sand) can not produce a good product due to the different particle sizes. The particle size of the silica sand is larger than the particle sizes of alumina and zirconia and then some modifications were considered [17]: • Bonding materials: clay or methocel (2%) • Replace of silica sand by silica fume (from 150 to 45 µm respectively). • Change of pressed pressure from 13350 to 44500 N The phases found in this case are the same that in the previous compositions but in this case the quartz combines easily with the badeleyite to produce zircon, and the free quartz tends to be transformed completely in cristobalite. The addition of bonding materials, such as methocel or clay, does not alter the formation of phases, because these materials only contribute to the compaction of the product (Figures 5 and 6). They can help to form a better bond between particles and improve the sintering. 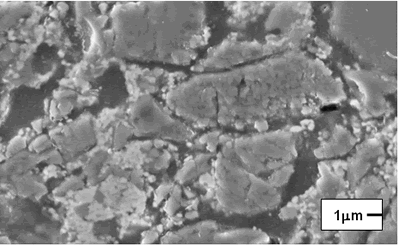 | Figure 4. Composition 4 (1450°C) 18 h, the separation of the grains of SiO2 (dark) and zircon formation (clear). | 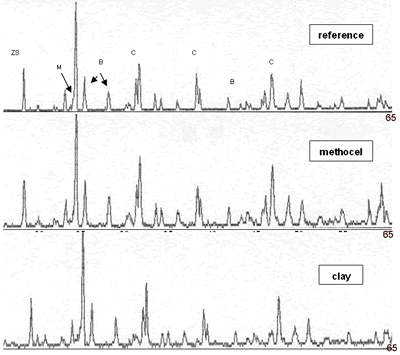 | Figure 5. Composition 1 sintered to 1450°C during 18 h with addition of methocel and clay, load 13350 N, (B-badeleyite, C-corundum, Q-quartz, ZS-zircon, M-mullite). | 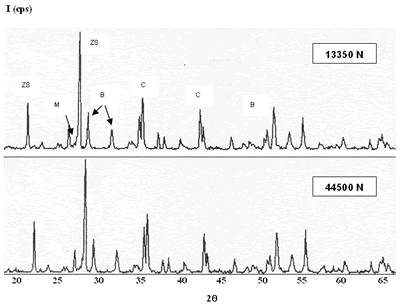 | Figure 6. Composition 1 (43-37-20): 1450°C during 18 hours without addition of methocel and clay, load 13350 and 44500 N. (B-badeleyite, C-corundum, ZS-zircon, M-mullite). | Figure 7 represents a model of sintering process, the starting point is consisting of contacting particles, the initial bonds range from point contacts to highly deformed interfaces. With sintering the contacts grow in size, and in the initial stage there is extensive loss of surface area. As the pore structure becomes rounded the discrete particles are less evident and the intermediate stage of sintering occurs. This is characterized by a tubular, rounded pore structure that is open to the compact surface; gas can permeate through the open pore space. Consequently, many sintered structures are sintered to this stage only to preserve desirably pore structures [21]. 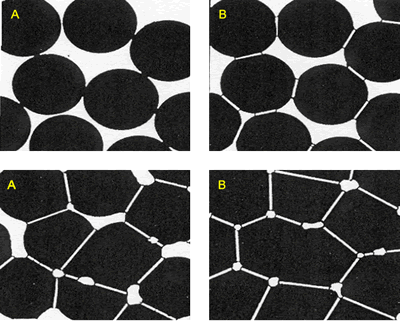 | Figure 7. Model of the interparticle bond as the ceramic microstructure is transformed during the sintering process. (a) Loose powder (start of bond growth). (b) Initial stage (the pore volume shrinks). (c) Intermediate stage (grain boundaries form at the contacts). (d) Final stage (pores become smoother). | After evaluating the microstructure of the modified compositions, the best results were found for the addition of silica fume and pressed pressure of 44500 N, independently of the addition of bonding product (Figures 8 and 9). 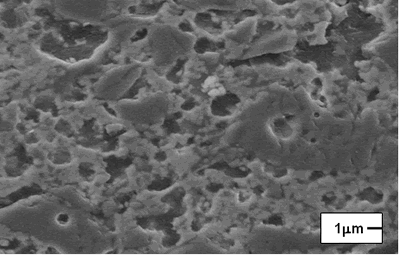 | Figure 8. Composition 1: 18 h, the use of silica fume can provide a good bond between grains of Al2O3 (dark grains). | 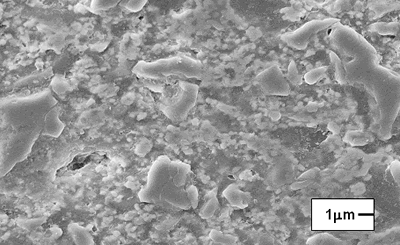 | Figure 9. Composition 1, 18 h, the microstructure presents some pores. | The particle size of the raw materials is very significant since it contributes to the phases formation owing to provide a good bond between grains of the same size, and then a final product with better physical properties is obtained [22, 23]. This fact can be seen with a static test of the refractory in contact with molten glass for the compositions 1, 2 and the commercial product; in the Figure 10 we can see the three compositions after the static test and they indicate the penetration of the molten glass. The microscopic analysis of three compositions indicates a good behavior of the composition 2 with low content of ZrO2 because the molten glass penetration is about 1.5 cm of the hot face (region in contact with the glass), for this reason the penetration is absent at the cold face (the other region of the sample), which indicates that this composition can present good corrosion resistance. 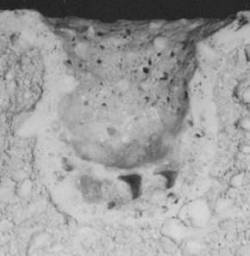 (a) 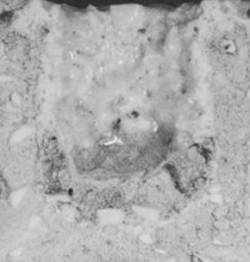 (b) 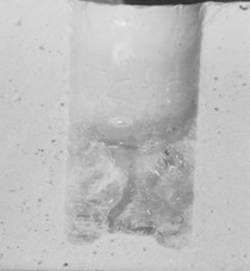 (c) | Figure 10. Static test to 1450°C during 4 h, (a) composition 1:43-37-20, (b) composition 4:43-37-20, (c) commercial product | We can see the microstructure without pores and homogeneous phases distribution conducting to good properties and characteristics of the refractory phases. The development of new Al2O3-ZrO2-SiO2 (AZS) product with low ZrO2 allows to have refractory materials with good mechanical and thermal properties; therefore the AZS with 20% of ZrO2 has economic advantages since the ZrO2 is very expensive and the contain in the commercial product is about 37%. In agreement to these results and discussion we propose the next conclusions. Conclusions • The AZS refractories manufactured at the laboratory, with low amount of ZrO2, can stand aggressive conditions in contact with molten glass. • The use of bonding materials (methocel and clay) and the adequate compaction of the raw materials are recommendable for the refractory phases formation. • The particle size of the components of the raw materials contributes to the phases formation and it can help to obtain a refractory matrix, this characteristic is very important for the refractory ceramic materials. • Therefore the AZS refractories manufactured with low content of ZrO2 can be used in the melting furnaces with a satisfactory economy. Acknowledgement The authors thank to Harbison Walker Refractories, S.A. de C.V. for providing access to the facilities for experimental data. References 1. H. W. Hennicke, “Refractories:Traditional Or Advanced Ceramics”, Interceram, 41, [4] (1992) 252-257. 2. W. D. Kingery, H. K. Bowen and D. R. Uhlmann, “Introduction To Ceramics”, John Wiley&Sons, Usa (1976) Pp. 540-549. 3. A. M. Alper, “High Temperature Oxides. Magnesia, Lime and Chrome Refractories” Academic Press. (1970) P. 143-148. 4. J. I. Duffy, “Refractory Materials”, Noyes Data Corporation, Usa (1980) Pp. 180-181. 5. H. Leupold and K. Santowski, Et. Al. “Improvement of Resistance to Alkali Attack of Refractory Materials of the Sio2-Al2o3 System for Temperature Up To 1300°C In Rotary Cement Kilns”, Interceram, (1984) 29-34. 6. N. Santander, “Refractarios En Altos Hornos”, Siderurgia Latinoamericana, 361 (1990) 2-15. 7. K. Lang, “High-Duty Silica Refractories for Glass Melting Furnaces”, Glass, July (1995) 254. 8. K. J. Konsztowicz, “Study of Porosity In Corroded Refractories”, J. Am. Ceram. Soc., 76 [5] (1993) 1169-1176. 9. P. Robyn, J. Moreau, “Selection of Zircon Bricks for Superstructure of Container Glass Furnaces by Laboratory Simulative Testing”, Glass, July (1995) 408. 10. J. C. Tribollet, H. Lagneaux, “Stresses In AZS Fused Cast Blocks During Heat-Up”, Glass, July (1995) 251252. 11. G. Duvierre, B. Copet And M.A. Nelson, “Use of Fused-Cast AZS Products And Their Monolithic Derivatives In Applications for the Ceramic Industry”, American Ceramic Society, Corrosion of Materials By Molten Glass, P. 105-129. 12. J. Tirlocq And R. Dramais, “Reaction Sintering of Mixed Oxides And Their Applications In Glass Industry”, Xxviii International Colloquium On Refractories, Aachen (1986) 426-435. 13. C. Mcgarry And T. Wehrenberg, “Refractories for Glassfibre Melting Furnaces”, Glass, November (1989) 459. 14. G. Duvierre And Y. Boussant-Roux, “Fused Zirconia Or Fused AZS: Which Is the Best Choice?, Ceram. Eng. Sci. Proc., 20, [1] (1999) 65-80. 15. S. Endo, K. Hamaoka and A. Ito, “Zirconia Fused Cast Refractories”, Glass, March (1990) 109-113. 16. D. W. Richerson, “Modern Ceramic Engineering. Properties, Processing And Use In Design”, Marcel Dekker, Inc. N.Y. (1982). 17. I. Knizek, “Los Parámetros De Refractarios Moldeables Y Prefabricados”, Barro Mex, S.A. De C.V., México (1989) 7-12. 18. Norma Alemana D.I.N. 1069, (1931). 19. T. Katoh, K. Ichikawa, “Developments of Dense Bricks for Glass Fiber Furnace”, Xxviii International Colloquium On Refractories, Aachen (1986) 388-407. 20. S. Sugita, C.A. Contreras, “Fine Pure Mullite Powder By Homogeneus Precipitation”, Journal of European Ceramic Society, 18, (1998) 1145-1152. 21. R. German, “Fundamentals of Particle Packing Theory”, John Wiley&Sons, Inc., New York (1996) 1-13. 22. E. A. Thomas, D.G. Patel and W.T. Brandt, “Bonded AZS Refractories for the Glass Processing”, Journal of the Canadian Ceramic Society, 53, (1984) 51. 23. J. H. Chesters, “Refractories. Production and Properties”, The Iron And Steel Institute. London (1973) P. 363-364. Contact Details A. M. Guzmán Facultad de Ingeniería Mecánica y Eléctrica, Doctorado en Ingeniería de Materiales Universidad Autónoma de Nuevo León Email: [email protected] | P. Rodríguez Facultad de Ingeniería Mecánica y Eléctrica, Doctorado en Ingeniería de Materiales Universidad Autónoma de Nuevo León | E. Sereno Harbison Walker Refractories, S.A. de C.V. | | |