Introduction Chemical properties of diamond surfaces can be intentionally modified if functional groups are introduced in a controllable way on the diamond surface. New types of organic-inorganic hybrid materials could be developed and the properties of diamond structural materials like grinding wheels controlled. Modifications by hydrogenation [1], oxidation by gases at high temperatures [2-3], silanation [4], and organic-chemical reactions [5-6] of diamond powder surface have been reported. Recently, surface modification of diamond powders by sonochemical reactions has been proposed by Uchida et al. [7]. Ultrasonic cavitation is known to produce sonochemically-activated reactions in water resulting in the formation of hydroxyl radicals, which are strong and nonselective highly effective oxidants, i.e., for organic pollutants in wastewater [8-9]. Ultrasonic irradiation of liquid-powders slurries or suspensions of metals creates cavitation and shockwaves that can accelerate solid particles to high velocities and interparticle collisions capable of inducing striking changes in surface morphology, composition and reactivity [10]. Ultrasonic systems are extremely sensitive and vulnerable to operational parameters [11]. It has been reported that the different stages of acoustic cavitation of liquids are affected by the irradiation conditions (frequency, external pressure, temperature, etc.) [12]. Chivate and Pandit studied the effects of vapour pressure, temperature, salinity and degassing on the pressure intensity of the fluid bulk [13]. Terahara et al., investigated the effects of parameters, such as distance of the horn to the sample, ultrasound intensity and frequency in sonophoresis [14]. According to our knowledge only Uchida et al. focused on studying the effects of operational parameters on sonochemical diamond powder surface modification. These authors studied the effect of horn material and horn-tip shape on the modification of diamond powder [7]. In order to modify diamond powder surfaces efficiently by this technique, the ultrasonic treatment parameters need to be well analyzed as mentioned before. The objective of this work is to study how pretreatment of the powder by acid washing and differences in sonochemical treatment conditions including horn immersion depth, bubbling gas and power affect the quality and quantity of oxygen surface groups produced on diamond powder. Experimental The diamond used in this study was a commercial synthetic powder of 5-12 µm grain size from Matsumoto yushi-seiyaku Co., Ltd. High power ultrasonic treatment was achieved with a SONOPET 250 B (Seidensha Electronics Co., Ltd., Japan) at 28 kHz. Following the recommendations of Uchida et al. [7] a concave titanium horn with a 3.5 curvature radius was employed. All samples were ultrasonically treated in distilled water with a 0.2 mass% concentration, at 40°C in a beaker of 3 cm diameter and 6 cm depth for a period of 360 s. A schematic representation of the experimental setup is shown in Figure 1. 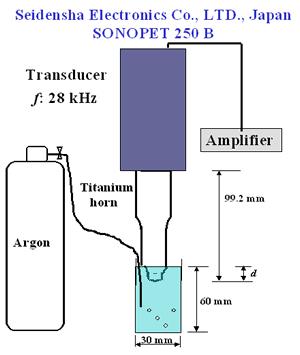 | Figure 1. Schematic diagram of the experimental set up | Acid-washed diamond (AWD) was prepared inserting the raw diamond (RD) powder in a 1:1 mixture of HF and HNO3 acids at room temperature for 4 h under constant stirring conditions, subsequently rinsed with distilled water until the pH reached a value of 7 and dried at 120°C for 20 h. In order to study the effect of acid washing the powder surface, RD and AWD powders were ultrasonically treated bubbling argon into the suspension with a flow rate of 0.5 l min-1 , a power of 120 W and a horn immersion depth (d) of 13 mm. To analyze the effect of the horn immersion depth, seven different depths (0, 5, 10, 13, 18, 25 and 50 mm) were selected. Suspensions of AWD powder with the horn immersed at the established depths were ultrasonically treated with a power of 120 W. To study the effect of bubbling argon, suspensions of AWD powder without and with a 0.5 l min-1 flow rate of bubbling argon were ultrasonically treated with a horn immersion depth of 13 mm and 120 W of power. Three different applied powers according to the capacity of the equipment were evaluated: 40, 80 and 120 W. These samples were treated bubbling argon into the suspension with a flow rate of 0.5 l min-1 and a horn immersion depth of 13 mm. For each experimental condition, 3 samples were prepared. Diffused reflectance infrared Fourier transform (DRIFT) spectroscopy was used to analyze and quantify the oxygen surface groups produced on the diamond surface after each treatment. DRIFT spectra were obtained using a Shimadzu FT-IR 8300 spectrometer equipped with a Spectra-Tech diffuse reflectance accessory, a Triglycine Sulfate (TGS) detector and data processing software. For each measurement three different portions of each sample in the region of 4000-400 cm-1 were taken. For each spectrum, 256 scans were accumulated at a resolution of 4 cm-1. The reported spectrum for each condition is the average of nine spectra in the case of treated powders and of three for the raw powder. The spectral bands were deconvoluted and quantified using a Jandel peak separation and analysis software in log (1/R) units. The details of the spectral qualitative and quantitative analysis have been presented elsewhere [15]. Results and Discussion Pretreatment of the Powder by Acid Washing The common scale DRIFT spectra in the 4000 – 400 cm-1 region of RD, AWD and of those powders after ultrasonic treatment (US) are shown in Figure 2 (a). The IR spectrum shape of the RD powder agrees well with that of the reported IR spectrum of diamond [16]. The IR spectrum shape of the AWD powder is similar to that of the RD. After the ultrasonic treatment, several additional peaks are observed for both powders, but the intensity of the peaks is higher for the AWD/US than that for RD/US. The area of the deconvoluted peaks normalized to the area of the diamond peaks from 2250 cm-1 to 2100 cm-1 are shown in Figure 2 (b). The samples pretreated with acid show the highest normalized intensities for all the oxygen surface groups. The dashed lines in Figure 2 (b) show the total normalized peak area of oxygen related species. For the sample ultrasonically treated after acid washing the amount of oxygen related species increases by a factor of 2.3. Probably, after acid pretreatment (HF + HNO3), surface impurities are removed and the surface becomes more active to react with the species formed by ultrasound. 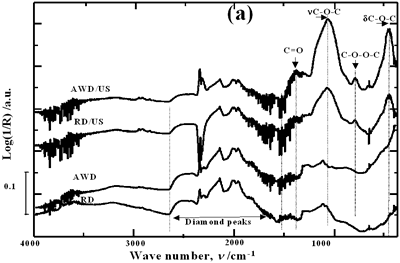 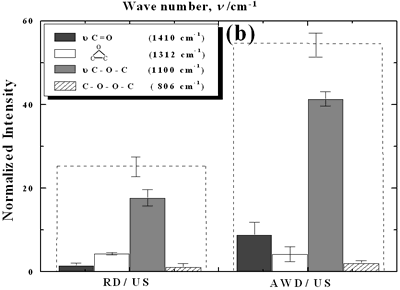 | Figure 2. Effect of pretreatment of the powder by acid washing (a) Common scale DRIFT spectra, (b) Normalized peak area of the deconvoluted bands. Dashed line: total normalized peak area. After acid washing, diamond becomes more reactive with the species formed in ultrasound | Horn Immersion Depth The common scale DRIFT spectra in the 4000 – 400 cm-1 region of AWD after ultrasonic treatment (AWD/US) at different horn immersion depths are shown in Figure 3 (a). It can be observed that the horn immersion depth into the liquid has an influence on the intensity of the species formed. The area of the deconvoluted peaks normalized to the area of the diamond peaks from 2250 cm-1 to 2100 cm-1 are shown in Figure 3 (b) for all conditions. The same oxygen surface groups are observed for all the samples. The highest normalized intensities correspond to ν C-O-C for all depths. Figure 3 (c) shows the total normalized peak area of oxygen related species after ultrasonic treatment at different horn immersion depths. The quantity of oxygen surface groups varies with the horn immersion depth. The samples treated at 0, 5, 25 and 50 mm show the lowest amount of oxygen related species produced and higher relative error values. The samples treated at a horn immersion depth of 13 mm show the highest normalized intensities for all the oxygen surface groups. This can be explained by observing the wave distribution in the horn as shown in Figure 4. 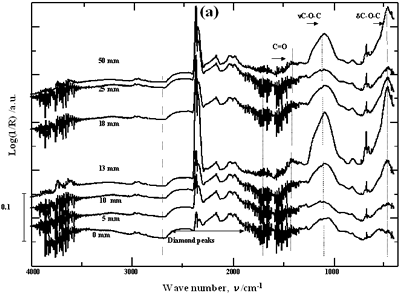 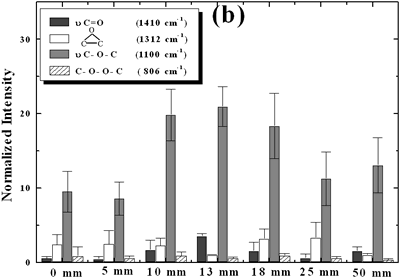 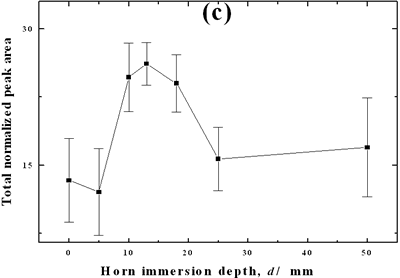 | Figure 3. Effect of horn immersion depth on modification of diamond powder by ultrasound (a) Common scale DRIFT spectra, (b) Normalized peak area of the deconvoluted bands, (c) Total normalized peak area. A horn immersion depth of 13 mm, that corresponds with the node of the horn, gives the highest intensity of oxygen related species. | 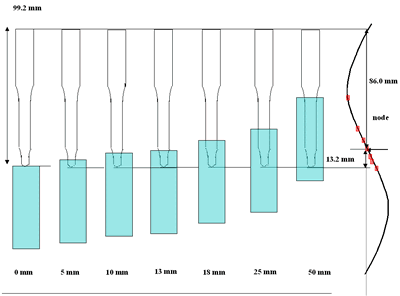 | Figure 4. Horn ultrasound wave distribution. Observe that the node is located at 13 mm | This wave distribution was calculated considering that the horn is a resonant element in the longitudinal mode and its function is to magnify or amplify the vibrating motion generated by the transducer. The sound wave travels with a specified velocity for each material [17]. The ultrasound velocity c is 4.9 x 105 cm s-1 for a titanium rod [18] and the frequency of the transducer; f = 28.5 kHz, then, the wavelength λ=172 mm. Therefore, the node distance of the wave from the top of the horn is: λ / 2 = 86.0 mm and the node of acoustic pressure is located at 13.2 mm from the base of the horn, corresponding approximately with the immersion depth that produces more oxygen species on the diamond surface. Bubbling Gas Into the Liquid The common scale DRIFT spectra in the 4000 – 400 cm-1 region of AWD after ultrasonic treatment with no bubbling gas and bubbling argon are shown in Figure 5 (a). It can be observed that the DRIFT spectrum of the sample treated bubbling argon into the liquid is similar to the spectrum treated with no bubbling gas but the peaks are sharper and the areas larger. The area of the deconvoluted peaks normalized to the area of the diamond peaks from 2250 cm-1 to 2100 cm-1 are shown in Figure 5 (b). The samples treated using bubbling gas into the liquid show the highest normalized intensities for all the oxygen surface groups. The dashed line in Figure 5 (b) shows the total normalized peak area of oxygen related species. By introducing a bubbling was the amount of oxygen surface groups produced doubles. As bubbles appear in the liquid more potentially active sites for cavitation are produced. As probability increases, the formation of oxygen active species increases. 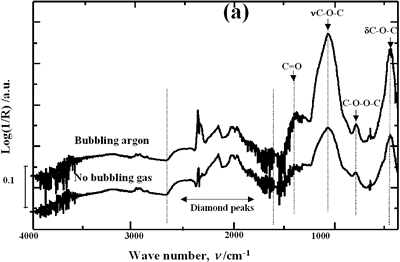 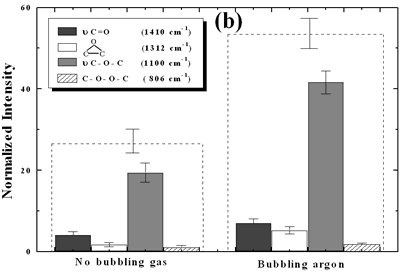 | Figure 5. Effect of introduction of bubbling gas on modification of diamond powder by ultrasound: (a) Common scale DRIFT spectra, (b) Normalized peak area of the deconvoluted bands. Dashed line: total normalized peak area. Bubbling gas in the liquid enhances the formation of oxygen related species on the diamond powder surface | Power The common scale DRIFT spectra in the 4000 – 400 cm-1 region of AWD after ultrasonic treatment at different ultrasound power are shown in Figure 6 (a). It can be observed that for the three power intensities evaluated the same peaks are observed and increasing the power the area of these peaks slightly increases and becomes sharper. The area of the deconvoluted peaks normalized to the area of the diamond peaks from 2250 cm-1 to 2100 cm-1 is shown in Figure 6 (b). The samples treated at 120 W show higher normalized intensities for all the oxygen surface groups. The dashed lines in Figure 6 (b) show the total normalized peak area of oxygen related species. Increasing the power, the amount of oxygen related species on diamond surface increases. The larger the power [W] the greater the value of acoustic pressure PA, the greater is the displacement of the molecules [12, 19] in the liquid and easier the formation of bubbles. 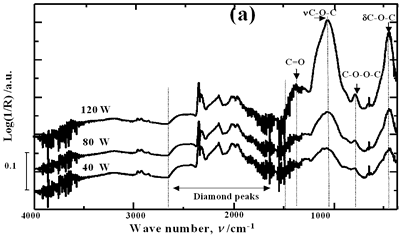 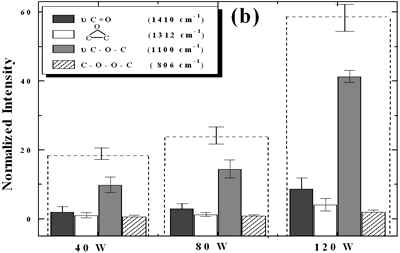 | Figure 6. Effect of applied power intensity on modification of diamond powder by ultrasound: (a) Common scale DRIFT spectra, (b) Normalized peak area of the deconvoluted bands. Dashed line: total normalized peak area. Increasing power increases the amount of oxygen related species formed. | At sufficiently high acoustic intensities ultrasound produces cavitation. Cavitation is the process in which micro bubbles, formed within a liquid during the rarefaction cycle of the acoustic wave, undergo violent collapse during the compression cycle of the wave. Cavity growth depends on the intensity of sound, for high intensity ultrasound, the cavity can expand rapidly [11, 20], then, the liquid rushes and the cavity implodes. The higher the cavitation the higher will be the formation of oxygen species on the diamond surface. Therefore increasing the power the formation of these species increases as well. Conclusions The largest absorbance intensity fraction for all the conditions evaluated corresponds to ether stretching (ν C-O-C) surface groups. By monitoring the quantity of oxygen groups formed the following is concluded: • A horn immersion depth where the ultrasound wave node is just at the liquid surface gives the largest oxygen surface content. • Acid washing makes the diamond surface to be more reactive to ultrasonic treatment, increasing by approximately a factor of 2.3, compared to the raw diamond, the total intensity of oxygen surface groups. • Bubbling argon into the diamond suspension enhances the production of oxygen surface groups approximately by a factor of 2. • As expected, by increasing the applied ultrasound power, the amount of oxygen surface groups is increased. Acknowledgments The authors are indebt to the Japanese government for financial support to Heidy Visbal through the scholarship as well as the partial support to the research through the 21st century Centers of Excellence (COE) program of the Ministry of Education, Culture, Sports, Science and Technology References 1. T. Ando, M. Ishii, M. Kamo and Y. Sato, “Thermal Hydrogenation of Diamond Surfaces Studied by Diffuse Reflectance Fourier-transform Infrared, Temperature-programmed Desorption and Laser Raman Spectroscopy”, Journal Chemical Society Faraday Transations, 89 [11] (1993) 1783-1789 2. T. Ando, K. Yamamoto, M. Ishii, M. Kamo and Y. Sato, “Vapour-phase Oxidation of Diamond Surfaces in O2 studied by Diffuse Reflectance Fourier-transform Infrared and Temperature-programmed Desorption Spectroscopy”, Journal Chemical Society Faraday Transactions, 89 [19] (1993) 3635-3640 3. S. Ji, T. Jiang, K. Xu and Shuben Li, “FTIR study of the Adsorption of Water on Ultradispersed Diamond Powder Surface”, Applied Surface Science, 133 (1998) 231-238 4. T. Tsubota, S. Iida, O. Hibarashi, S. Nagaoka, S. Nagayama, M. Nagata and Y. Matsumoto, “Surface Reforming of the Oxidized Diamond Surface with Silane Coupling Reagents”, Journal of the Ceramic Society of Japan, 110 [10] (2002) 904-910 5. T. Tsubota, S. Tanii, S. Iida, M. Nagata and Y. Matsumoto, “Chemical Modification of Diamond Surface with CH3(CH2)nCOOH Using Benzoyl Peroxide”, Physical Chemistry Chemical Physics, 5 (2003) 1474-1480 6. T. Nakamura, M. Ishihara, T. Ohana and Y. Koga, “Chemical Modification of Diamond Powder Photolysis of Perfluoroazooctane”, Chemical Communications, (2003) 900-901 7. T. Uchida, T. Takatera, T. Sato and S. Takeuchi, “Surface Modification of Diamond Powders by Sonochemical Reaction”, Proceedings of the IEEE Ultrasonics Symposium, 1 (2001) 431-434 8. R. H. de Lima, P. Cognet, A.-M. Wilhem and H. Delmas, “Anodic Oxidation of 2,4-dihydroxybenzoic Acid for Wastewater Treatment: Study of Ultrasound Activation”, Chemical Engineering Science, 57 (2002) 767-778 9. M. Kenneth and G. L. Chahine, “The Use of Cavitating Jets to Oxidixe Organic Compounds in Water”, Proceeding of FEDSM’98, ASME Fluids Engineering Division Summer Meeting, Washington, June 21-25 (1998) 1-8 10. S. Kenneth and J. Gareth, “Applications of Ultrasound to Materials Chemistry”, Annu. Rev. Mater. Sci., 29 (1999) 295-326 11. N. H. Ince, G. Tezcanli, R. K. Belen and I. G. Apikyan, “Ultrasound as a Catalyzer of Aqueous Reaction Systems: The State of the Art and Environmental Applications”, Applied Catalysis B: Environmental, 29 (2001) 167-176 12. J. P. Lorimer and T. J. Mason, "Sonochemistry. Part 1 - The Physical Aspects", Chemical Society Review, 16 (1987) 239-274 13. M. M. Chivate and A. B. Pandit, “Quantification of a Cavitation Intensity in Fluid Bulk”, Ultrasonics Sonochemistry, 2 (1995) S19-S25 14. T. Terahara, S. Mitragori, J. Kost and R. Langer, “Dependence of Low-frequency Sonophoresis on Ultrasound Parameters; Distance of the Horn and Intensity”, International Journal of Pharmaceutics, 235 (2002) 35-42 15. H. Visbal, C. Ishizaki and K. Ishizaki, “DRIFT Evaluation of Ultrasonically Modified Diamond Powder”, The 42nd Symposium on Basic Science of Ceramics, sponsored by The Basic Science Division, Ceramic Society of Japan, Japan, (2004) 16. J. Wilks and E. Wilks, “Properties and Applications of Diamond”, Butterworth-Heinemann, Oxford, (1991) pp.70-89 17. R. Goldman, “Ultrasonic Technology”, Chapman & Hall, Ltd., London, (1962) pp. 14-35 18. E. A. Neppiras, “Very High Energy Ultrasonics”, British Journal of Applied Physics, 11 (1960) 143-150 19. 19. T. J. Mason, “A General Introduction to Sonochemistry”, in Sonochemistry: The Uses of Ultrasound in Chemistry, (Ed. T. J. Mason), Royal Society of Chemistry, Cambridge, (1989) pp. 4-8 20. K. S. Suslick, “The Chemical Effects of Ultrasound”, Scientific American, (1989) 80-86 Contact Details Heidy Visbal Nagaoka Gijutsu-Kagaku Daigaku (Nagaoka University of Technology) School of Mechanical Engineering Nagaoka, Niigata 940-2188, Japan | Satoshi Sugita Centro de Investigaciones en Quimica Inorganica Universidad de Guanajuato Noria Alta S/N Noria Alta, Guanajuato, GTO. C.P 36050 Mexico | Chanel Ishizaki Nano-TEM Co., Ltd. Shimogejo 1-485 Nagaoka, Niigata, 940-0012 Japan | Kozo Ishizaki Nagaoka Gijutsu-Kagaku Daigaku (Nagaoka University of Technology) School of Mechanical Engineering Nagaoka, Niigata 940-2188, Japan Email: [email protected] | |