Introduction We are faced with serious global environmental issues of shortage of natural resources and an increase in waste disposal. For establishing a sustainable society, it is urgently necessary to develop innovative re-circulation technology reducing the impact on the Earth. One of the serious problems in Japan is the disposition of garbage and wastes because of the shortage of waste disposal sites. In the year 2000, the amount of discharged industrial waste was 406 million tons in Japan [1]. Among the nineteen categories of industrial wastes, sludge accounted for the largest ratio of 47% (189 million tons). Furthermore, the recycle ratio of sludge was the lowest value of 8%. Therefore, novel recirculation technology using sludge comes to play an important role for the sustainable society. The hydrothermal reaction as one of the effective low energy consumption wastes conversion methods have been investigated using low-SiO2 and high-Al2O3 starting materials with lime [2-5]. Although many work has been published for the hydrothermal reaction in the CaO - SiO2 system, little has been reported on the influence of high Al2O3 content in a starting waste on the strength development during hydrothermal solidification. It has been stated that the formation of hydrogarnet (Ca3Al2(SiO4)(OH)8) leads to lowering strength [6]. It is suggested that the problem is avoided by controlling the crystal size of hydrothermally formed aluminous phases such as hydrogarnet and zeolite [5]. The sludge, containing very fine particles of quartz and clay minerals, is usually treated with coagulant agent of poly aluminum chloride (PAC) for the disposition, resulting in the higher content of reactive amorphous Al(OH)3 in the sludge. Thus, the hydrothermal reaction is possibly applied to the re-circulation technology for sludge waste. The objective of the present work was to investigate the influence of added Ca(OH)2 on the strength development and its relation to the microstructure in the hydrothermal reaction system of water purification sludge - calcium hydroxide. Experimental Sample Preparation The sludge from a water purification plant in central Japan and calcium hydroxide (Ca(OH)2, UBE Industries, Ltd., Japan) were used as starting materials. Table 1 shows the chemical composition of the sludge. The SiO2 and Al2O3 content were 33% and 25%, respectively. The Al/(Al+Si) atomic ratio was 0.47. X-ray diffraction pattern (XRD) of the sludge indicated that quartz, muscovite, albite, clinochlore, and kaolinite were the main constituent minerals (Figure 1). Aluminum hydroxide derived from PAC seemed to be amorphous. The sludge was calcined at 600°C for 5 h to remove organic compounds, followed by wet-ball milling. 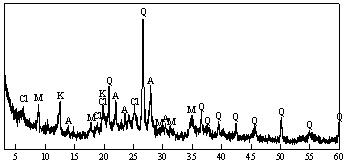 | Figure 1. XRD pattern of the sludge from a water purification plant (Q; quartz (SiO2), M; muscovite (KAl2(Si3Al)O10(OH,F)2), A; albite (NaAlSi3O8), Cl; clinochlore ((Mg,Al)6(Si,Al)4O10(OH)8), K; kaolinite (Al2Si2O5(OH)4)). | Table 1. Chemical composition of sludge from water purification plant (mass%). | 33 | 25 | 6.3 | 1.1 | 1.2 | 1.1 | 0.5 | 0.6 | 0.6 | 0.2 | 0.3 | 1.3 | 1.7 | 26.5 | *L.O.I means loss on ignition. The calcined sludge and calcium hydroxide were weighed to obtain mixtures with calcium hydroxide/(calcium hydroxide + calcined sludge) mass% of 0, 2, 5, 10, 15, and 20, which were equivalent to the bulk Ca/(Al+Si) atomic ratio of 0.02, 0.04, 0.07, 0.12, 0.18, and 0.25, respectively. After weighing, an additional amount of distilled water was added for mixing and forming (30 mass% of the powder mix). Rectangular test specimens with the size of 15(W)×10(H)×40(D) mm were formed by uniaxial pressing at 30 MPa and hydrothermal treatment under saturated steam pressure at 220°C for 10 h. The bulk density of the green body was about 1100 kg·m-3. Analytical Methods After hydrothermal treatment, the test specimens were dried at 80°C for 2 days. The dried specimens were tested for three point flexural strength (Tensilon RTM-500, A&D, Japan; support distance 30 mm, cross head speed 0.5 mm·min-1) and their bulk density was calculated from the mass and dimensions. The phases that constitute the specimens were identified by XRD analysis (RAD-B, Rigaku, Japan). The microstructures observation of the specimens was carried out using field emission scanning electron microscope (FE-SEM: JSNM-5400, JEOL, Japan). The atomic ratio of formed phases was determined with analytical transformation electron microscope (TEM: JEM-2010F, JEOL, Japan). The specific surface area and pore distribution were measured by the N2 gas adsorption BET and BJH method (Macsorb HM, model-1201, Mountech, Japan), and mercury intrusion pore distribution was determined by mercury intrusion porosimetry (PoreMaster-33P, Quantachrome, USA). The self humidity controlling property was evaluated by the released moisture amount from specimens (55 mm in width, 5 mm in height, 55 mm in depth) between 90%RH and 50%RH at 25ºC in the chamber (PR-3KP, Espec Co., Japan). The heat resistance was evaluated by thermomechanical analysis (TMA: TMA8310, Rigaku, Japan) and thermogravimetry - differential thermal analysis (TG-DTA: TAS-300, Rigaku, Japan). Results and Discussion Reaction Products XRD Results Figure 2 shows XRD patterns of the specimens with various amount of added Ca(OH)2 autoclaved at 220°C for 10 h. The XRD patterns after the autoclaving were similar in spite of various amount of added Ca(OH)2. The typical binding compound such as tobermorite or calcium aluminate silicate hydrates could not be observed, suggesting that the reaction products had near amorphous nature. 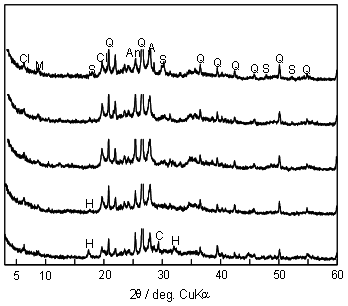 | Figure 2. XRD patterns of specimens with various amount of added Ca(OH)2 autoclaved at 220°C for 10 h (Q; :quartz (SiO2), M; muscovite (KAl2(Si3Al)O10(OH,F)2), A; albite (NaAlSi3O8), Cl; clinochlore ((Mg,Al)6(Si,Al)4O10(OH)8), S; 3Al2O3·4SO3·8H2O, An; anhydrite (CaSO4), H; hydrogarnet (Ca3Al2(SiO4)(OH)8), C, calcite (CaCO3)). | Anhydrite (CaSO4) was observed for all specimens. The specimen using only sludge (Ca(OH)2=0 mass%) gave 3Al2O3·4SO3·8H2O. The hydrogarnet was formed for the specimen added 10 mass% of Ca(OH)2 and higher. As for the starting material, quartz, muscovite, albite, clinochlore remained. SEM Observation and Chemical Composition of Reaction Products Figure 3 shows SEM photographs of specimens with various amounts of added Ca(OH)2 autoclaved at 220°C for 10 h. Except for the specimen with 5 mass% of Ca(OH)2, the hydrothermally formed platy phase was observed. With the increase of Ca(OH)2 addition, the thickness of the platy phase increased. For the specimens with 5 mass% of Ca(OH)2, the granular particles in a few tens nm size were mainly observed as the hydrothermally formed phase.  (a) 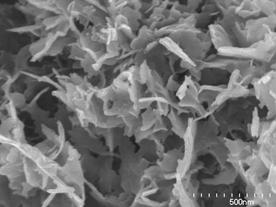 (b) 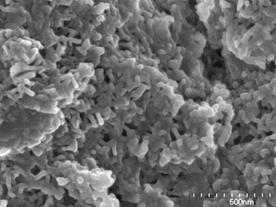 (c) 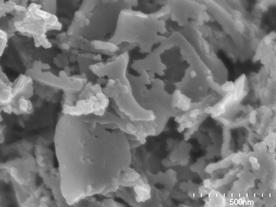 (d) | Figure 3. SEM photographs of the specimens added (a) 0, (b) 2, (c) 5 and (d) 20 mass% of Ca(OH)2 after autoclaved at 220°C for 10 h. | Table 2 lists the major element ratios of the granular phase in the specimen with 5 mass% of Ca(OH)2 measured by analytical TEM. The major elements in phases formed were Al and Si, having the average Al/(Al+Si) ratio of 0.57 and Ca/(Al+Si) ratio of 0.02. However, it was not possible to identify the formed phase. Table 2. Analytical TEM results of hydrothermally formed phase in the specimen added 5 mass% of Ca(OH)2 autoclaved at 220°C for 10 h (atomic ratio). | | 0.371 | 0.590 | 0.020 | | 0.431 | 0.757 | 0.015 | | 0.490 | 0.960 | 0.019 | | 0.603 | 1.520 | 0.034 | | 0.608 | 1.551 | 0.028 | | 0.653 | 1.882 | 0.019 | | 0.705 | 2.386 | 0.015 | | 0.731 | 2.719 | 0.015 | Average | 0.574 | 1.546 | 0.021 | Standard deviation | 0.130 | 0.763 | 0.007 | Flexural Strength The bulk density did not change through out the hydrothermal treatment and it was almost constant at ~ 1100 kg·m-3 after hydrothermal treatment. Figure 4 shows the flexural strength of hydrothermally treated body at 220°C for 10 h as a function of the amount of added Ca(OH)2. It is noteworthy that no addition of Ca(OH)2 yielded the flexural strength of 8.5MPa, which was about 8 times higher than that of green body. This suggests that the calcined sludge is a suitable waste for the hydrothermal solidification. The flexural strength gave maximum strength of 13 MPa at Ca(OH)2=5 mass%. With the increase in Ca(OH)2 addition, the strength decreased to 1 MPa at Ca(OH)2=15 mass%, which is comparable with that of green body. It is believed that the variation of flexural strength with Ca(OH)2 addition is affected by difference of microstructure observed by SEM. 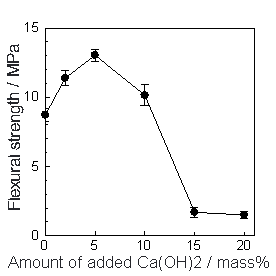 | Figure 4. Variation of flexural strength with amount of added Ca(OH)2. The specimens were autoclaved at 220°C for 10 h. | Although the binding materials was not clear, XRD results and analytical TEM results show the possibility of the near amorphous aluminate silicate hydrate having Al/(Al+Si) ratio of 0.57 and Ca/(Al+Si) ratio of 0.02. As anhydrite was formed even in the lowest strength specimen, it could not be the binding material. Microstructure Mercury Intrusion Porosimetry Figure 5 shows micropore distribution measured by mercury intrusion porosimetry. The hydrothermal treatment yielded the modal pore diameter shift from 1 µm to 0.01 - 0.02 µm. With the increase of Ca(OH)2 addition, the modal pore diameter after autoclaving increased: 0.02 µm (Ca(OH)2=0 mass%), 0.01 µm (Ca(OH)2=2, 5 mass%), 0.02 µm (Ca(OH)2=10 mass%) and 0.05µm (Ca(OH) 2=20 mass%). Since the flexural strength increased with the decrease of modal pore diameter, it is suggested that the formation of finer pore affects the strength development. 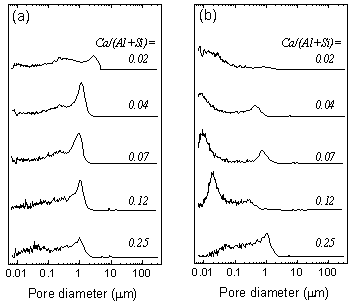 | Figure 5. Mercury intrusion pore size distribution of the specimens (a) before autoclaving and (b) after autoclaved at 220°C for 10 h. | N2 Adsorption Porosimetry The specific surface area of the specimen was increased by the hydrothermal treatment. For the specimen with 5 mass% of Ca(OH)2, the specific surface area increased from 30.2 m2·g-1 to 157.6 m2·g-1 by hydrothermal treatment. This is attributed to the formation of nano sized reaction product (Figure 3(c)). The specific surface area was 5 times higher than that of autoclaved aerated concrete, a hydrothermally solidified porous material [7, 8]. Figure 6 shows the pore distribution of the specimen with 5 mass% of Ca(OH)2 after autoclaving. The sharp peak at 4 nm and broad peak at around 7 nm were observed. 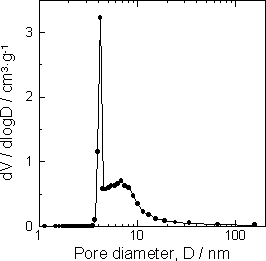 | Figure 6. N2 absorption pore size distribution of the specimen added 5 mass% of Ca(OH)2 autoclaved at 220°C for 10 h. | Application for Building Materials The high specific surface area and the pore distribution of the mesoporous materials from water purification sludge are suited for self humidity controlling material. The mesoporous materials with a 3 to 7 nm pore diameter are able to keep humidity in the range of 40 to 70% according to Kelvin’s equation [9,10]. Table 3 shows humidity controlling property of various materials. The specimen added 5 mass% of Ca(OH)2 had higher humidity controlling property (460 g·m-2) than that of cedar (65 g·m-2) and hydrothermally solidified waste soil (76 g·m-2) [11]. Table 3. Humidity controlling property of hydrothermally solidified sludge from water purification plant and waste soil, and cedar | Hydrothermally solidified sludge from water purification plant added 5 mass% of Ca(OH)2 | 460 | Hydrothermally solidified waste soil | 76 | Cedar | 65 | From TMA and TG-DTA results (Figures 7, 8), it was clarified that the mesoporous materials from water purification sludge has high heat resistance. In the TMA result, the dimension change was scarcely observed under 800°C. This suggests that the mesoporous materials from water purification sludge have high heat resistance as that of general autoclaved insulation material having tobermorite as a binding material [12]. 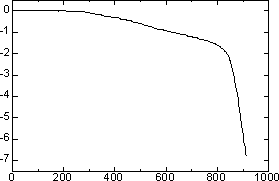 | Figure 7. TMA curve of the specimen added 5 mass% of Ca(OH)2 autoclaved at 220°C for 10 h. | 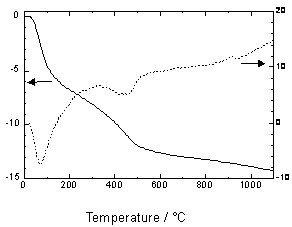 | Figure 8. TG-DTA curve of the specimen added 5 mass% of Ca(OH)2 autoclaved at 220°C for 10 h. | The higher amount of moisture absorption and heat resistance suggests application to building materials such as self humidity controlling tile or board. Conclusions The recycling technology of sludge from water purification plant was investigated using hydrothermal reaction. The solidified specimen using the mixture of the sludge with 5 mass% of calcium hydroxide yielded the highest flexural strength of 13 MPa with a bulk density of 1090 kg·m-3, resulting from the formation of about few tens nm size hydrate. The high specific surface area of 157 m2·g-1, the higher amount of moisture absorption and the high heat resistance suggest an application to building materials such as self humidity controlling material. References 1. “White Paper on the Recycle-Based Society in Japan 2003”, Ministry of the Environment, Gyosei Corp., Tokyo, (2003) pp.47-51. 2. H. Maenami, O. Watanabe, H. Ishida and T. Mitsuda, “Hydrothermal Solidification of Kaolonite-Quartz-Lime Mixtures”, J. Amer. Ceram. Soc., 83 [7] (2000) 1739-1744. 3. H. Maenami, H. Shin, H. Ishida and T. Mitsuda, “Hydrothermal Solidification of Waste with Formation of Zeolite”, J. Mater. Civil Eng., 12 [4] (2000) 302-306. 4. O. Watanabe, K. Kitamura, H. Maenami and H. Ishida, “Hydrothermal Treatment of a Silica Sand Complex with Lime”, J. Amer. Ceram. Soc., 84 [10] (2001) 2318-2322. 5. H. Maenami, N. Isu and E. H. Ishida, “Solidification of Al-rich Inorganic Waste Materials Using Hydrothermal Technology”, J. Ceram. Soc. Japan, in press. 6. I. Stebnicka-Kalicka, “Application of Thermal Analysis to the Investigation of Phase Composition of Autoclaved Cement Pastes and Mortars”, Therm. Anal., 1 (1980) 369-374. 7. N. Isu, S. Teramura and T. Mitsuda, “Fracture Toughness of Autoclaved Aerated Concrete Products”, in Ceramic Transactions, 37, Cement-Based Materials: Present, Future and Environmental Aspects (Ed. M. Moukwa, S. L. Sarker, K. Luke and M. Grutzeck), Amer. Ceram. Soc., Westerville (1992) pp. 129-137. 8. N. Isu, S. Teramura, H. Ishida and T. Mitsuda, “Mechanical Property Evolution during Autoclaving Process of Aerated Concrete Using slag: II Fracture Toughness and Microstructure”, J. Amer. Ceram. Soc., 77 [8] (1994) 2093-2096. 9. S. Tomura, M. Maeda, K. Inukai, F. Ohashi, M. Suzuki, Y. Shibasaki and S. Suzuki, “Water Vapor Adsprption Property of various Clays and Related Materials for Applications to Humidity Self-Control Materials”, Clay Sci., 10 [3] (1997) 195-203. 10. S. Tomura, “Research on Synthesis of Kaolinite Clay and Humidity Conditioning Materials”, J. Ceram. Soc. Japan, 110 (2002) 71-77. 11. H. Maenami, H. Shin, E. H. Ishida and T. Mitsuda, “Hydrothermally Solidified Waste Soil”, Trans. Mater. Res. Soc. Japan, 25 [2] (2000) 649-652. 12. “Hand Book of Hydrothermal Science”, Gihodo Shuppan Co.,Ltd., Tokyo, (1997) pp. 310-320. Contact Details Hiroki Maenami Basic Research Center, INAX Corporation 3-77, Minato-cho Tokoname-shi, Aichi, 479-8588 Japan Email: [email protected] | Hideaki Tanaka Basic Research Center, INAX Corporation 3-77, Minato-cho Tokoname-shi, Aichi, 479-8588 Japan | Norifumi Isu Basic Research Center, INAX Corporation 3-77, Minato-cho Tokoname-shi, Aichi, 479-8588 Japan | Emile H. Ishida Research plus Development Center INAX Corporation 3-77, Minato-cho Tokoname-shi, Aichi, 479-8588 Japan | |